1. 引言
装药在半无限介质中爆炸,装药与临空面之间的一部分土岩将被破碎、抛掷形成爆破漏斗 [1],这种爆破方式称为抛掷爆破。抛掷爆破充分利用炸药能量抛掷土岩、减小清渣工程量,因其高效、经济的优点在覆盖层剥离、硐室爆破、隧道掏槽爆破等工程中被广泛使用。
采用钻孔内分层装药研究抛掷爆破效应,靠近孔口的装药起爆后会形成倒圆锥型或V型漏斗坑,并为后续装药创造新的临空面 [2],后续装药爆炸加大开挖深度,这种通过扩大钻孔直径、采取分层装药、逐层延时起爆、逐层破碎抛掷的方式可有效地增大岩土成坑深度和抛掷效果,提高施工效率。而分层装药参数、延期起爆时间间隔等条件都直接影响了最后成坑效果。为研究上述因素对爆破成坑的影响,基于分层爆破理论设计爆破实验参数,并开展石灰岩上层、下层两阶段爆破模拟实验,研究不同装药组合条件下的爆破效果,利用ANSYS/LS-DYNA有限元程序,结合SPH-FEM算法模拟了分层延时起爆条件下的爆破过程,重点分析了岩体受力及质点运动特征。
2. 分层装药爆破参数设计
在水平地形条件下,利用柱状装药爆破创造一个V型漏斗坑,再在V型地形条件下爆破加深。这里需要解决两个问题,一是V型地形的形成,所使用装药称为上层装药,二是V型地形下的二次破碎抛掷,所使用装药称为下层装药。
2.1. 上层装药参数
为了形成岩体破碎效果并将岩块尽量多的抛掷出漏斗坑为后续抛掷提供更好条件,需要根据爆坑开口水平尺寸 [3]、装药直径等合理确定装药在孔口的留长,以及装药长度等关键参数。
集团装药量与爆坑直径D、最小抵抗线h、介质材料等因素的关系为:
(1)
式中:Q——中级炸药装药量(kg);
K——与介质材料相关的抗力系数,
,
为炸药密度,
为岩石临界破坏速度,
为装药爆炸后周围岩石速度;
η——爆炸作用指数的系数,爆炸作用指数
,
;
h——最小抵抗线(m)。
爆坑可见深度P与最小抵抗线h、爆炸作用指数n的关系为:
(2)
将爆破参数与爆坑尺寸整理后,发现爆坑半径和深度随比例埋深
的增大开始增长,随后开始下降。具体见图1所示。对于短圆柱装药可以简化为集团装药计算,对于长圆柱装药需要进行叠加处理。

Figure 1. Size of medium internal explosive pit
图1. 介质内部爆坑尺寸
2.2. 下层装药参数
根据V型地形条件下爆破计算模型,装药量可按下式计算:
式中:a——下层装药距离倒圆锥底部的距离(m);
α——倒圆锥或V型地形的夹角度数(˚)。
由于V型地形两侧岩石夹制作用,夹角越小夹制越明显,需要的药量也越大。随着夹角增大,夹制作用减弱,当α为180˚时变成了水平地形的爆破形式。变化规律见图2。
在介质密度2285 kg/m3石灰岩中钻孔,孔径70 mm,装药采用聚黑2炸药(密度1.7 g/cm3,直径60 mm)进行爆破,考虑介质内部爆破当量换算后,根据不同最小抵抗线计算得出漏斗半径和可见深度等参数见表1。
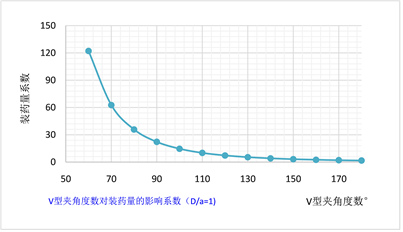
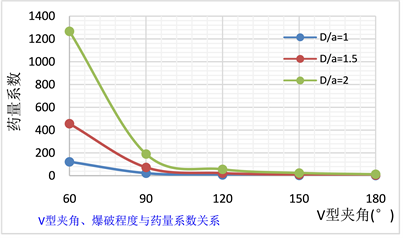
Figure 2. Effect of Angle and blasting degree on drug volume under type V terrain
图2. V型地形条件下角度和爆破程度对药量的影响
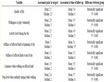
Table 1. Parameter calculation of rock blasting
表1. 岩石抛掷爆破参数计算
3. 爆破装药参数试验研究
为研究上层装药对孔口爆破漏斗和抛掷效果、上下装药之间间距、时间间隔、孔口留长、装药长度等参数合理性,共开展7组爆破试验,其中,上层装药试验5组,下层装药试验2组。爆破试验在南京汤山石灰岩介质中实施,装药采用圆柱状聚黑2 (8701炸药),直径60 mm。使用高速摄像机和普通摄像机记录爆破过程。
3.1. 上层装药爆破试验
试验中钻孔孔径为70 mm,孔深60至130 cm,装药上表面距离地面距离30至50 cm,装药长度15至90 cm,试验中孔口留空段无填塞。装药参数具体如表2所示。
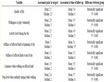
Table 2. Pharmaceutical blasting test condition of the upper layer
表2. 上层装药爆破试验工况
由爆破试验可以看出,上层装药在岩石中爆炸后大致可分为,爆炸气体膨胀、岩石鼓包脱离、岩块飞散运动以及岩块回落四个阶段 [4] [5]。对爆破后可见漏斗进行测量记录,之后采用人工开挖破碎岩石形成实际破碎轮廓,针对不同工况下的爆破可见深度和实际破碎轮廓见图3。其中,紫色线段代表落石回落后实际轮廓线,玫红色线段代表实际爆破漏斗。爆破试验结果表明,孔口留长取35 cm时,可见漏斗深度最大约为45 cm,最大岩石破裂半径约100 cm。当孔口留长增大时可见深度减小,破碎半径也减小;当孔口留长减小时可见深度也会减小,破碎半径也呈现减小趋势。装药长度25 cm为宜,当装药长度增加时不会增加可见深度,破碎半径有缓慢增大趋势。当装药长度继续增加时实际破碎体积变化不大,当超过临界深度时只能对装药周围岩石进行破碎,由于破碎范围较小且不易人工开挖。当装药长度减小时可见深度也会减小,见图3。
通过对比工况(1)、(4)、(6)及工况(3)、(8)可以看出,当钻孔深度一定时,随着装药量的增大,形成的漏斗坑直径增大,整体形状趋于扁平,且坑底出现平台区间,而随着装药量进一步增大时,漏斗坑直径变小,当孔口留长与装药深度比值较小时,爆破坑截面呈上宽,下窄的多段形状(见工况(7)、(9)),爆后端部不生成漏斗孔。这是因为垂直柱状装药上表面离孔口地表接近时,一定范围内的装药对岩石作用形成破碎并抛掷,超出这个范围的装药能量对漏斗基本没有贡献。一定范围内又有一部分装药能量大部分形成空气冲击波,对岩石破碎抛掷范围也不大。

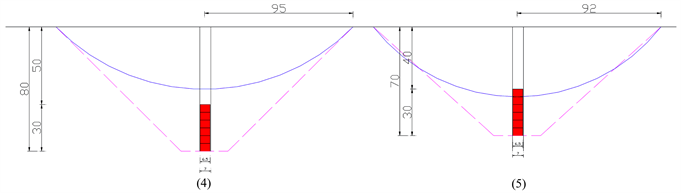
Figure 3. Diagram of upper layer charge blasting effect
图3. 上层装药爆破效果示意图
3.2. 下层装药爆破试验
为了取得直观数据,将分层装药延时起爆分解为上层装药起爆和下层装药起爆,其中,下层装药起爆是在上层装药起爆后开挖碎块再钻孔。根据上层装药试验结果,钻孔孔径为70 mm,孔深60 cm,装药长度25 cm,装药上表面距离地面距离35 cm。装药采用直径60 mm的聚黑2炸药,试验中孔口留空段无填塞,爆炸形成漏斗坑。将上层装药爆破形成的V型坑内的碎块清理干净后在V型坑内钻孔、装药,保留装药上表面与漏斗坑底部距离,点火爆破,而后,观察下层装药爆破抛掷情况,并进一步清理坑内碎块,观察破碎范围及深度。根据采用不同装药长度、装药上表面与V型地形底部距离爆破比较后,效果相对较为理想的试验参数如图4。爆破效果具体见图5。


Figure 4. Design of pharmaceutical blasting parameters of the lower layer
图4. 下层装药爆破参数设计
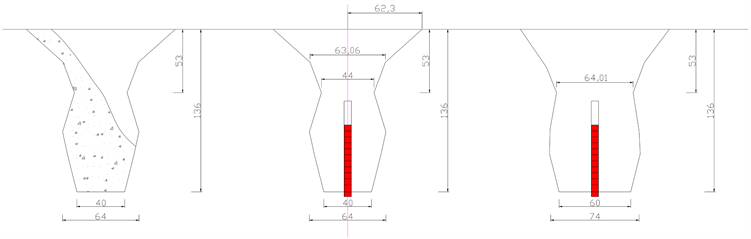
Figure 5. Diagcharge blasting effect of lower layer
图5. 下层装药爆破效果示意图
根据实际爆破效果,下层装药上顶面距离V型坑底25至30 cm时,抛掷效果和开口长度可以满足需要,清理工作量相对较少。当下层装药上顶面与V型坑底距离加大,水平开口长度和抛掷量都会下降,证明了多级装药逐级起爆、逐层破碎抛掷、逐步加大开挖深度的方法是有效的,可以控制地表岩石破碎半径,得到深度不小于孔径的深坑,V型地形下装药爆破可以形成有效抛掷,下层装药量确定方法基本正确,能达到预期效果。
4. 分层爆破数值模拟研究
研究分段装药延时起爆在岩土爆破为后段装药生成自由面的爆炸作用过程。钻孔直径70 mm,延期时间为12 ms,隔爆介质采用湿土材料,起爆点位于上部装药顶端。
4.1. 数值模型
构建如图所示全三维数值模型,模型包含土体,上层装药、下层装药两部分,上层装药长30 cm、间隔40 cm、填塞40 cm,下层装药长40 cm。对爆炸核心区采用SPH粒子划分,其余采用拉格朗日网格进行划分,单元总数为161,385,粒子总数为210,586,见图6。
(1) 三维几何
(2) 网格剖面
(3) SPH粒子与网格视图
Figure 6. Finite element model
图6. 分层装药起爆作用有限元模型
炸药、填塞及炮孔近区岩体采用LS-PREPOST将FEM网格转化为SPH粒子,模型边界处岩体采用FEM网格建模,便于边界条件时施加,SPH岩体与FEM岩体之间通过*CONTACT_TIED_NODES_TO_SURFACE关键字设置固结耦合。由于建立的是全三维模型,所以在模型无需增加位移及旋转约束。岩石域周边定义为非反射边界,模拟半无限岩体域,见图7。
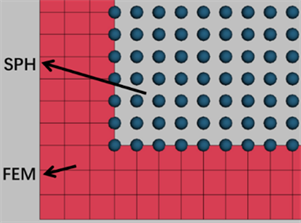
Figure 7. FEM-SPH solid connection coupling
图7. FEM-SPH固连耦合
4.2. 材料本构模型及参数
岩石乳化炸药的材料工况采用LS-DYNA材料库中提供的炸药工况*MAT_HIGH_EXPLOSIVE_BURN,状态方程采用适合表征炸药材料的*EOS_JWL,炸药材料参数如表3所示。
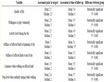
Table 3. Parameters of explosive materials and equation of stat
表3. 炸药材料和状态方程参数
空气材料采用空材料工况*MAT_NULL,状态方程采用适合表征空气的*EOS_JWL,空气密度为1.29 kg/m3。
按照ALE算法的设置,将岩石材料设置为普通拉格朗日网格;炸药和空气单元建立共节点,采用多材料ALE单元(*ALE_MULTI-MATERIAL_GROUP)设置,采用cm-g-us单位制。岩石材料采用适合表征高应变率作用下的岩石混凝土等结构的HJC本构工况,材料参数设置如表4所示。
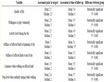
Table 4. Setting Table of HJC operating condition parameters of rock materials
表4. 岩石材料的HJC工况参数设置表
采用一般矿石的抗压强度,为岩石材料添加失效准则,即达到静态抗压强度114 Mpa、静态抗拉强度9 Mpa时,岩石单元破坏,不再提供承载能力,删除单元。
4.3. 数值模拟结果及分析
4.3.1. 爆炸作用过程
为直观反映分层装药延时起爆在岩土爆破为后段装药生成自由面的爆炸作用过程,图8给出不同时刻,SPH粒子结构材料的爆破飞散过程。
从图8中可以看出,炸药首先在起爆点发生爆炸反应并产生爆轰波,爆轰波由起爆点向四周传播。然后爆轰产物开始作用于岩壁。岩壁在爆轰波作用下首先发生塑形变形。500 us时刻爆轰波到达掌子面,爆轰产物作用于孔壁而使其承受较高的压力;对于非自由面方向(包括空孔) [6],岩壁会产生的较强约束作用使得爆轰产物粒子向外膨胀受阻,且在爆轰产物与岩壁界面发生应力波的反射与透射。在爆轰产物的推动下,前段装药的预爆岩石向掌子面运动由图可以看出,各段药柱起爆后,产物粒子向岩壁轰击,形成一股很强的爆轰产物粒子流,爆轰产物粒子膨胀轰击作用于孔壁,炮孔壁承受载荷开始产生损伤破坏。随着孔内爆轰产物的继续膨胀,内部粒子作为产物粒子流的后续补充继续拉断向前运动,自由面方向岩体进一步受到破坏。从空间形成历程图上看,采用SPH‑FEM耦合法模拟岩土爆破中岩体大变形具有独特优势。
4.3.2. 岩体受力及运动特性分析
沿装药轴线,从自由面到装药端面的中点20 cm处选取3个特征位置的岩石SPH粒子,跟踪粒子的位移和速度信息,并绘制时程曲线如图9所示。t = 3750 μs时刻岩石粒子挤压至掌子面,位移增量随后变缓;在9900 us时位移增量出现大幅增长。岩石粒子在收到爆轰作用后的速度最大值为93.90 m/s,随后3个特征位置的抛掷的速度出现了明显的下降区,在3900 us后回弹进入一个平台区,速度约为15.10 m/s;t = 10,000 μs之后粒子运动速度陡升至峰值75.4 m/s,故临空面岩体完全脱离主岩体的时间为10 ms。
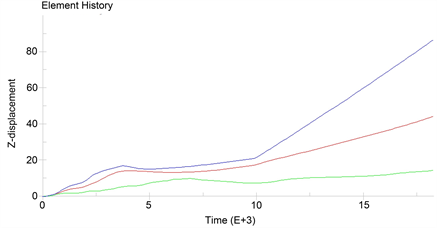

Figure 9. Time range curve of rock particle displacement and velocity change
图9. 岩石粒子位移和速度变化时程曲线
图10为岩石粒子3个特征位置等效应力和Z方向应力(压应力为负值)时程曲线,岩体主要发生Z方向的压缩抛掷,所以其等效应力和Y方向应力的变化规律基本相同。岩体在爆炸载荷作用下迅速被压密实,最大等效应力出现在297 us,其值为52.1 Mpa。
等效应力
Y方向应力
Figure 10. Equal effect force and Y direction stress time range curve
图10. 等效应力和Y方向应力时程曲线
在岩体裂纹出现的位置处选取2个相邻的SPH粒子,提取z方向上的位移数据,并绘制位移时程曲线如图11所示。观测岩石材料SPH粒子在z方向上的位移曲线可以看到,炸药起爆后,爆腔开始膨胀,
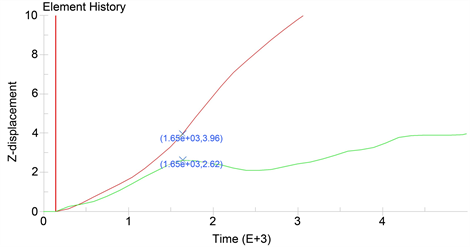
Figure 11. Time curve of rock particles near the crack
图11. 裂纹附近岩石粒子位移时程曲线
靠近临空面一侧的岩体开始向外运动,在临空面最外层和堵塞段斜向拉裂,随着爆腔继续膨胀,临空面岩体和堵塞段出现被拉断,将裂纹大于1 cm时视为拉断时,拉断时间为1650 us。图12为下端炸药近自由面端面的SPH粒子等效应力。由等效应力曲线可以发现,t = 149 μs时材料的应力达到峰值38.20 MPa。

Figure 12. Time curve of rock particles near the crack
图12. 下端炸药自由面等效应力
4.3.3. 爆破漏斗形状与尺寸
数值模拟结果,在t = 8.8 ms时,上层装药爆破后的倒圆锥漏斗已形成,至t = 18.0 ms下层装药爆炸破碎抛掷完成,最终形成葫芦状漏斗坑,形状与实验类似,口部直径173 cm、腰部30 cm、下部52 cm,如图13所示。
5. 结语
针对上、下两层分段岩土爆破,采用柱形装药岩土爆破理论设计爆破参数,通过开展模型试验,研究了不同装药长度、孔深及孔口留空下的上层V型爆坑,以及最终爆炸成坑,并利用ANSYS/LS-DYNA有限元程序结合SPH-FEM算法开展了口部填塞时分层爆破过程数值模拟,模型试验及数值结果表明,下层装药上顶面距离V型坑底25至30 cm时,整体抛掷及爆炸成坑较好;当下层装药上顶面与V型坑底距离加大时,水平开口长度和抛掷量都会下降;爆腔膨胀后,靠近临空面一侧岩体向外运动,在临空面最外层和堵塞段产生斜向明显拉裂。