1. 引言
Al-Mg-Si合金由于其优异的成形性能和较低的生产成本,广泛应用于与国民经济高度相关的众多领域。在Al-Mg-Si合金挤压材生产中,不仅需要使挤压材达到较高的尺寸精度,而且还需要采用合适的工艺以保证挤压材所需综合性能 [1] [2] [3] [4] 。
目前,在保证挤压材尺寸精度方面,生产中取得了丰富的实践经验。例如在挤压材在线淬火过程中,采用冷却速率相对较小的风冷或水雾冷却,可显著减少合金淬火应力引起的变形。在挤压材性能调控方面,除主合金元素外,优化微合金化元素以调控综合性能的基本理论已较为完善。例如,大量文献表明 [5] [6] [7] ,在Al-Mg-Si合金中添加适量Mn元素 [5] [6] ,可显著细化晶粒尺寸和结晶相尺寸 [7] ,同时改善其强度与韧性。然而,Mn元素添加对Al-Mg-Si合金性能的限制作用鲜见文献报道。
前期在实际生产过程中发现,当采用冷却速率较低的淬火工艺处理Al-Mg-Si合金挤压材时,发现添加Mn元素的合金其强度反而不如未添加Mn元素的合金。本文针对这一问题,设计了不同Mn元素添加量和不同淬火工艺试验,采用光学金相、扫描电镜及透射电镜研究了Mn元素对不同淬火工艺下Al-Mg-Si合金组织性能的影响,揭示了Mn元素不影响同淬火工艺下对Al-Mg-Si合金性能的作用机理。本文的研究结果可为Al-Mg-Si合金挤压材成分与工艺的适配调控提供有益参考。
2. 试验材料与方法
本文所用试验合金分别为2种不同成分的Al-Mg-Si合金,其中一种不添加Mn元素,另一种添加约0.31%wt Mn。其化学成分如表1所示。均匀化后的试验铸锭加热至510℃后,上机以5 m/min的速度进行挤压,挤压比约为23,挤压出口温度控制在530℃~535℃范围内。挤压成4 mm厚的型材后,在线分别进行风冷(Air quenching, AQ)和水冷(Water quenching, WQ)淬火冷却到室温,其冷却速度分别相当于6℃/s、200℃/s。2种材料均以风冷和水冷淬火2种方式进行淬火,获得4种不同淬火工艺和不同Mn元素添加量的挤压型材,相应工艺如表2所示。淬火后,将所有挤压材置于时效炉内进行人工时效,时效温度为182℃,保温时间0~16 h。
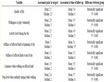
Table 1. Chemical compositions of the experimental alloys
表1. 试验材料的化学成分
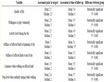
Table 2. Process of the experimental alloys
表2. 试验材料的处理工艺
时效硬化曲线在时效过程中按一定时间间隔取样,测试硬度后绘制相应的时效硬化曲线。硬度测试在华银HV-3硬度计上进行,加载力约为30 kgf,保荷时间约为15 s;根据时效硬化曲线的结果,分别在各合金的时效峰值处取样进行力学性能和微观组织检测分析。
拉伸力学性能在万能电子试验机上进行,试样标距为50 mm,拉伸试验速率约为2 mm/min,试验过程中采用引伸计测定材料在0.2%塑性变形时的拉伸应力,作为材料的屈服强度,试样拉断后,测定材料的断后伸长率。所有试验结果均取3个试样的平均值。
金相试样经打磨抛光后,采用氟硼酸溶液进行阳极覆膜,其电压为20 V,处理时间约为45 s。随后置于Olymbas光学显微镜下采用偏光模式分别观察试样的金相显微组织。扫描电镜显微组织试样在Zesis M10扫描电镜上观察,其加速电压约为12 KV;透射电镜显微组织在FEINICAL F20透射电镜上进行,加速电压约为120 KV,其试样为经电解双喷减薄后的薄膜试样,双喷电解液为体积比3:7的硝酸甲醇溶液。
3. 研究结果
3.1. 时效硬化现象
图1为不同试样在182℃下保温0~16 h的人工时效硬化曲线。从图中可见,所有试样均表现出显著的时效硬化现象,但其硬化速率、峰值硬度等方面可见明显差异。从淬火态试样(0 h)来看,风冷淬火试样硬度较水冷试样高,其中0.3 Mn/AQ试样硬度最高,而采用水冷的0.3 Mn/WQ试样硬度最低;随着时效的进行,所有试样均表现出较高的硬化速率,其中0.3 Mn/WQ试样硬化速率显著高于其他试样,其硬度峰值最高,约为101 HV;值得注意的是,虽然添加Mn元素的0.3 Mn/AQ,其淬火态试样硬度较高,但其峰值硬度反而较未添加Mn元素的0 Mn/AQ试样低。此外,添加Mn元素的试样时效峰值时间稍短于未添加Mn元素的试样。
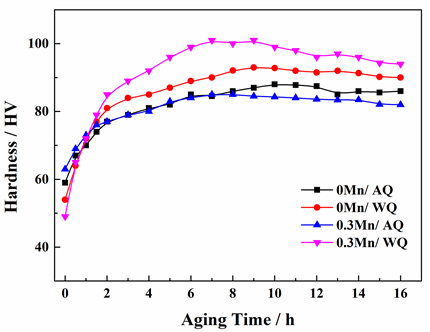
Figure 1. Aging hardening curves of the different experimental alloys
图1. 不同试样的时效硬化曲线
3.2. 拉伸性能
在不同试样的时效峰值处取样,进行拉伸性能检测,所得结果如图2所示。从图中可见,水冷淬火的试样均比风冷淬火的试样强度高,其中0.3 Mn/WQ试样强度最高,其屈服强度约为284 MPa。然而,在AQ组试样中,0.3 Mn试样的屈服强度反而比0 Mn试样低,这与时效硬化的结果一致。此外,断后伸长率的结果表明,添加Mn元素后,断后伸长率显著提高。
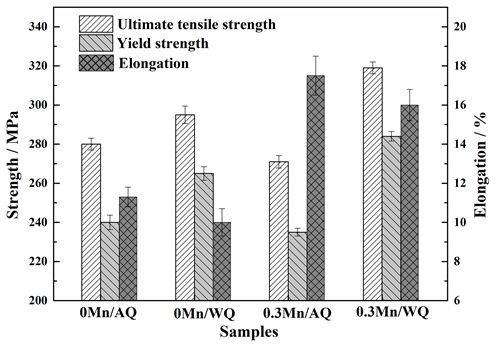
Figure 2. Mechanical properties of the experimental alloys
图2. 试验合金的拉伸力学性能
3.3. 光学金相组织
图3为不同试样的金相显微组织。从图中可见,0 Mn试样的金相组织为等轴状的粗大再结晶组织,其晶粒尺寸约为100 μm,而0.3 Mn试样除表层可见约200 μm厚的粗晶层外,次表层以内保留着纤维组织形态;而从淬火工艺上来看,AQ试样与WQ试样的金相组织未见明显差异。此结果表明,添加Mn元素的添加,抑制了材料的再结晶与晶粒长大过程,使得0.3 Mn合金形成挤压纤维组织,同时这种挤压纤维组织结构与淬火冷却速率相关性较低。
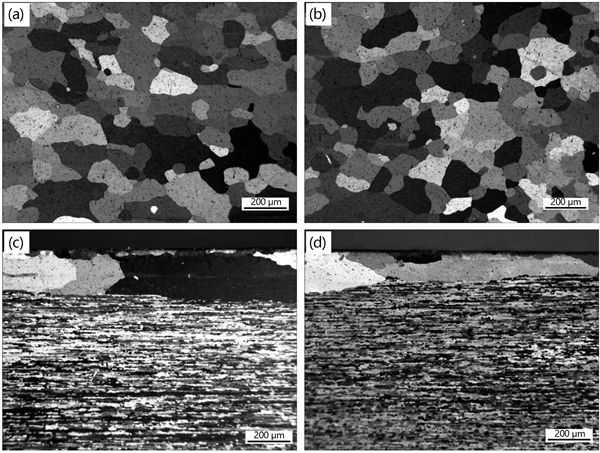
Figure 3. Optical micrograph of the experimental alloys: (a) 0 Mn/AQ, (b) 0 Mn/WQ, (c) 0.3 Mn/AQ, (d) 0.3 Mn/WQ
图3. 试验合金的光学金相组织:(a) 0 Mn/AQ,(b) 0 Mn/WQ,(c) 0.3 Mn/AQ,(d) 0.3 Mn/WQ
3.4. 扫描电镜显微组织
图4为不同试样的扫描电镜显微组织,从图中可见,所有试样中均弥散分布着大量的第二相粒子,但0.3 Mn组试样和0 Mn试样存在显著差异。0.3 Mn组试样的第二相粒子大多呈颗粒状,其最大尺寸约为8 μm,能谱定性分析结果表明,这些粒子主要为Al(FeMn)Si相 [3] ,而A、B组试样的粒子在视场中大多呈杆状,其最大尺寸达15 μm,能谱分析表明,这些粒子主要为AlFeSi相 [3] 。从淬火工艺上来看,风冷和水冷的第二相粒子在形貌、尺寸和分布上均未见明显差别。此结果表明,Mn元素的添加,显著细化了合金中的第二相粒子,同时在线淬火过程与第二相尺寸无显著相关性。
Al-Mg-Si合金中,一般存在Al(FeMn)Si、AlFeSi、MnAl6等主要弥散第二相粒子,这些第二相粒子作用于Al基体组织,使得合金中形成不同尺度下的多相微观组织。前期的研究结果表明 [3] ,Mn元素促进了Al-Mg-Si合金在均匀化过程中的β→α的相转变过程,显著细化和球化了第二相粒子。因此,在本文的试验条件下,0.3 Mn组试样中的第二相粒子尺寸较0 Mn组试样小(如图4所示);同时0.3 Mn试样中还存在大量亚微米级的Al(FeMn)Si粒子,这些亚微米级粒子在合金挤压过程中能显著抑制合金中的再结晶和晶粒长大过程,使得试样保留了明显的挤压纤维组织,相应地,未添加Mn元素的0Mn组合金其晶粒为粗大的等轴状再结晶组织(如图3所示)。此外,从图3和图4的结果来看,相同合金成分但不同淬火工艺试样的基体和第二相粒子无显著差异,这表明,由Mn元素添加引起的基体和弥散结晶相组织变化与淬火工艺无显著相关性。
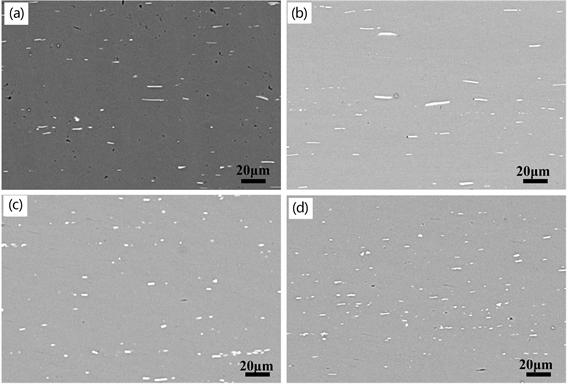
Figure 4. SEM micrographs of the experimental alloys: (a) 0 Mn/AQ, (b) 0 Mn/WQ, (c) 0.3 Mn/AQ, (d) 0.3 Mn/WQ
图4. 试验合金的扫描电镜显微组织:(a) 0 Mn/AQ,(b) 0 Mn/WQ,(c) 0.3 Mn/AQ,(d) 0.3 Mn/WQ
3.5. 透射电镜显微组织
图5为不同试样的峰值时效样品从[001] Al晶带轴方向观察到的透射电镜显微组织照片。从图中可见,所有试样中均可观察到大量呈针状的析出相,这些析出相均为β相,但不同试样中析出相的尺寸和分布可见明显差异。从尺寸上来看,WQ组的试样析出相总体尺寸较AQ组试样更细小,其中0.3 Mn/WQ试样中析出相尺寸最小。从数量分布上来看,虽然添加了Mn元素,在0.3 Mn/AQ试样中,析出相分布在所有试样中反而最为稀疏。此结果表明,Mn元素对析出相尺寸和分布的影响与冷却速率显著相关。一般认为 [8] [9] [10] [11] ,位错、亚晶界及晶界等微结构均为析出相形核的优先位置,在相同成分和工艺下,这些微结构含量越多,时效后析出相的尺寸越细小;本文中,由于Mn元素的添加,0.3 Mn组试样均保留着明显的纤维组织,其内部析出相形核位置较0 Mn试样多,因此,从透射电镜组织来看,其晶内析出相尺寸显著小于0 Mn试样,同时其分布也较0 Mn试样密集。
图6为不同试样在淬火后晶粒内部弥散粒子的明场像。从图中可见,0.3 Mn组试样中可见较多亚微米级的弥散粒子,而0 Mn试样中亚微米级粒子较少。此外,在0.3 Mn/AQ试样中弥散粒子周围可观察到呈杆状的粒子,如图,这些杆状粒子应为平衡态的Mg2Si相 [11] ,而0.3 Mn/WQ试样中,未见明显的Mg2Si相衬度。此结果表明,在冷却速度较低的情形下,Mn元素形成的弥散粒子能作为Mg2Si相形核位置,在淬火过程中使得平衡态的Mg2Si粒子析出。
值得注意的是,在风冷淬火试验条件下,0.3 MnAQ试样析出相分布反而较0 MnAQ试样稀疏,如图5(a)、图5(c)所示;同时力学性能的结果也表明,0.3 MnAQ试样强度较低。这主要是由于在冷却速度较低的情形下,Mn元素形成的亚微米级Al(FeMn)Si粒子与Al基体之间的相界是一种高能界面 [4] [5] [12] ,在较高温度下,能作为Mg2Si相形核位置从而使其优先析出,在淬火过程中形成了无明显强化作用的平衡态Mg2Si相,使得合金中的Mg、Si溶质原子大量消耗,显著降低了合金过饱和度,图6(c)中观察到的弥散粒子周边可见析出相衬度的现象与上述分析相吻合。
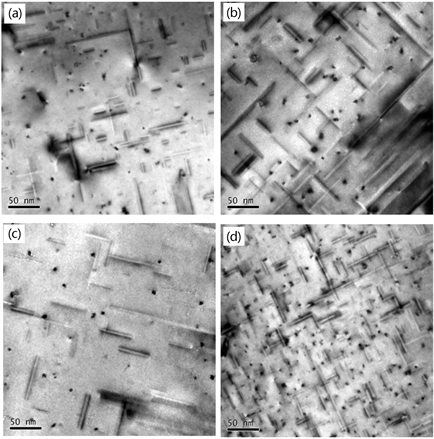
Figure 5. TEM micrographs of the peak aging alloys: (a) 0 Mn/AQ, (b) 0 Mn/WQ, (c) 0.3 Mn/AQ, (d) 0.3 Mn/WQ
图5. 峰值时效态试验合金的透射电镜显微组织:(a) 0 Mn/AQ,(b) 0 Mn/WQ,(c) 0.3 Mn/AQ,(d) 0.3 Mn/WQ
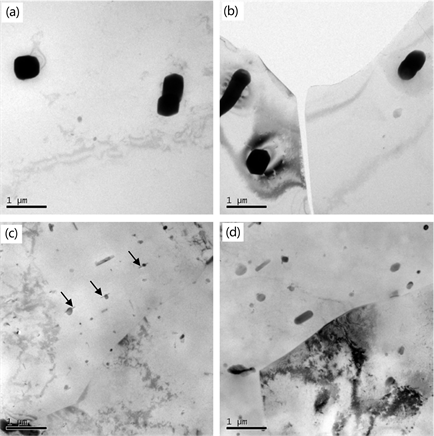
Figure 6. TEM micrographs of the as-quenched alloys: (a) 0 Mn/AQ, (b) 0 Mn/WQ, (c) 0.3 Mn/AQ, (d) 0.3 Mn/WQ
图6. 淬火态试验合金的透射电镜显微组织:(a) 0 Mn/AQ,(b) 0 Mn/WQ,(c) 0.3 Mn/AQ,(d) 0.3 Mn/WQ
综合上述分析可知,Mn元素的添加抑制了再结晶和晶粒长大,同时显著细化了第二相粒子,因此0.3 Mn试样的断后伸长率显著高于0 Mn试样;添加Mn元素后,试样的强度对淬火冷却速率较为敏感,主要表现为,在水冷条件下,0.3 MnWQ试样强度最高,而在风冷条件下,0.3 MnAQ试样强度反而最低,即Mn元素显著提高了合金的淬火敏感性。
4. 结论
本文采用硬度、拉伸试验、光学金相、扫描电镜和透射电镜研究了Mn元素对不同淬火工艺下Al-Mg-Si合金组织和性能的影响,得到如下结论:
1) Mn元素的添加显著细化了合金中的第二相粒子,其参与形成的亚微米级Al(FeMn)Si具有抑制再结晶和晶粒长大作用;晶粒和第二相粒子细化使得添加Mn元素的试样断后伸长率显著提高;
2) Mn元素的添加,使得淬火冷却速率对合金性能的影响更为显著。在水冷淬火条件下,0.3% Mn合金屈服强度较0 Mn合金强度提高约17%,而在风冷条件下反而比0 Mn合金低。
3) 在风冷淬火的试验条件下,Mn元素添加形成的亚微米级Al(FeMn)Si相与铝基体之间的界面在淬火过程中促进了Mg2Si平衡相的析出,降低了合金过饱和度,从而使得0.3% Mn试样硬度和强度反而低于未添加Mn元素的试样。
NOTES
*通讯作者。