1. 引言
气缸作为一种结构简单的多用途产品广泛应用于生产生活的各个领域。随着工艺和材料不断发展,气缸的可靠性越来越高,寿命越来越长,这进行导致气缸寿命试验的成本也越来越高。
自加速寿命试验的概念问世以来,各国对其进行了深入的研究。围绕提高恒定应力试验数据分析精度的问题,Mazzuchi和Hirose分别作了研究[1] [2] 。Watkins,Bugaighis,McLinn和Wang对恒定应力试验的极大似然估计问题进行了研究和改进[3] -[6] 。张志华等则对恒定应力试验的二步估计问题进行了深入的探讨[7] [8] 。1980年Nelson提出的Nelson原理使得产品在不同应力水平下的加速时间可以相互折算[9] ,这使得步进应力加速试验的研究取得突破。此后,Bhattachargga,Tyoskin,Tang和茆诗松等对于Nelson原理进行了拓展和改进[10] -[13] 。葛广平等人的研究使步进应力试验的极大似然估计步骤流程化[14] -[16] 。这些成果大大提高了加速寿命试验的效率和精度。
为了探究气缸寿命试验的方法,Underwood针对厚壁气缸的疲劳寿命进行了仿真分析及实验分析[17] [18] ,Belforte和Raparelli对气缸动密封的磨损进行了寿命试验的研究[19] ,Kang和Kim则选压力、频率和温度作为加速应力提出了一种加速寿命试验的方法,提高了试验的效率[20] 。在国内,付永领,祁晓野,陈娟,马俊功等人对气缸加速寿命试验进行了系统的研究,分析了气缸的失效模式及与之相关的应力类型[21] ,研究并改进了双应力恒定加速寿命试验的试验方法及统计方法[22] [23] ,这些研究使得气缸寿命试验的效率和精度都得到了提升。王德义等研究了适用于机械产品的多应力试验的GLL-Weibull模型[24] 。刘伯红研究了气缸的双应力交叉步进试验,相对于恒定应力试验,试验效率大大提高[25] 。
经过国内外学者的研究,当前针对气缸的加速寿命试验的效率和寿命预测精度都得到了极大的保障,而由于产品寿命的不断提升,对于试验效率的优化依然有着巨大的需求。本文为进一步提升气缸加速寿命试验的试验效率,进行了双应力交叉步降加速寿命试验的研究。
2. 气缸的双应力交叉步降加速寿命试验
2.1. 试验设计过程
多应力的交叉步阶试验的设计思路是选取多个应力进行加速试验,在试验的每一阶段中依次选择其中一种应力升高/降低其应力水平,直至试验结束。这类试验由于每次仅降低一种应力,这使得在试验的总体条件逐步变化的情况也兼顾相邻两阶段的试验条件有关联,可将相邻两阶段的试验理解为局部的单应力步进/步降试验来进行后续的实验分析。考虑到当前试验条件控制成本及统计算法的复杂度,选择双应力进行交叉步阶试验较为可行。
双应力交叉步降试验中,选取两种应力
和
并各设置n个应力水平并满足
(1)
(2)
其中,
和
为产品正常使用下的应力水平
试验过程中每次调整试验条件时,交替降低其中一种应力的水平,以达到在试验过程中逐渐降低应力水平的效果,即试验中各阶段的联合应力水平依次为
(3)
本次研究中使用的气缸为单出杆双作用的活塞气缸,这种气缸经过一段时间的工作后会出现的问题主要为活塞杆、密封圈及缸体内壁相关部位的磨损,导致零部件间隙增大,引起泄漏和气缸的最终失效。研究表明,气缸工作时的环境温度以及气缸的作动频率对于系统的磨损有显著的影响,因此试验中选取这两种应力作为加速应力。
试验中使用了20个气缸作为试验样本,步阶试验中的截尾方式包括定数截尾和定时截尾,试验中每个阶段的样本失效数应尽量相近,不能过多或过少,考虑到本试验过程便于监控,因此采用了定数截尾的试验方法。
综合考虑应力种类和截尾数要求,试验中每种应力选取了四个应力水平,则试验中将使用7组应力,试验截尾数设定为3。具体的加速试验谱如图1所示。
2.2. 试验效率与精度分析
针对同类气缸的双应力恒定应力试验在两种应力各设置4个应力水平的情况下,将会组合出16个应力组合,经过一定的优化可以选择与双应力交叉步阶试验相同的7组应力进行试验,考虑到试验的精度,每组需要至少5个样本,因此双应力恒加试验至少需要35个样本。而交叉步阶试验仅需20个样本,且试验条件可以进行统一控制,大大降低了试验的成本。
对比步进与步降试验,根据失效物理的退化模型以及Nelson的累计失效模型,步阶试验的产品失效是由于各应力试验下所累积的失效概率之和决定的,而与加载顺序及加载方式无关。因此对于应力水平设计相同的步进和步降试验,试验完全进行后所得的样本的累计失效概率是一样的。我们知道,试验样
本累计失效概率是一个漫长的过程,步降试验在试验初期使用高应力进行加速试验,其累计失效概率的速率将大大高于步进试验。根据张春华等人的研究,对于相同的定数截尾的试验方案,在获取等量信息的情况下步降应力试验所用的试验时间比步进应力试验短;而对于定时截尾的试验方案,在相同试验时间的情况下步降应力试验获取的寿命信息比步进应力试验多。因此相对于步进试验,双应力交叉步降试验可进一步提升加速试验的效率。
精度方面,步阶试验所选取的样本数较少,所获得的失效数据也较少,因此在试验结果的精度上将逊于恒定应力试验。而步降试验初始应力较高,失效概率累计很快,从试验结果的记录上来说出现误差的可能性相比于步进试验更高,这就更加增加了试验结果出现误差的可能性。双应力交叉步降加速试验是否能够满足气缸寿命试验的实际精度需求,需要根据试验的结果来评判。
3. 试验结果分析
根据上文的试验应力及加速谱,进行了两组气缸双应力交叉步降加速寿命试验,以其中一组为例进行数据分析。
3.1. 试验结果记录
试验结束后,所得的试件失效数据如表1所示。试件失效时间的不可控,而试验过程中也并不能做到实时监控,因此并非试验的每一阶段的试样失效数都准确为3,而完成第6步试验后所有试样均已失效,因此不再进行第7步试验。这是由于试验本身的特点决定的,而且记录的误差在试验允许的范围内,这一误差不会影响后续的数据处理过程。
拆解失效的试件进行检查,所得出的气缸失效原因包括以下几点:气缸活塞杆磁石磨损严重,出现剥落,甚至出现断裂;密封圈磨损严重,且两侧积累大量磨屑;缸筒内壁和活塞杆都有明显磨痕,尤其是受负载作用力方向的一侧;密封圈变形严重,间隙增大。这些失效机理与常规使用中该类型气缸出现失效的原因保持一致,因此本次试验的结果是有效的。
3.2. 试验数据分析
根据累计效率模型(Cumulative Effect Model),各阶段的失效数据之间可以进行相互的折算,将步阶试验的失效数据转化为等效的恒定应力试验的失效数据,基本的折算公式为
(4)
其中:
为第i阶段的失效数据,
为将第i阶段的失效数据折算至第j阶段的等效数据,
,
分别为产品在i,j阶段的应力条件下的特征寿命。
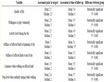
Table 1. Failure number in each period (cpm—cycles per minute)
表1. 各阶段试件失效数(cpm——每分钟的作动次数)
在各阶段应力水平下的产品特征寿命未知的情况下,针对双应力交叉步阶试验,结合广义对数线性模型模型(Generalized Logarithmic Linear Model,简称GLL模型,如式(5)),可将式(4)转化为如式(6)的形式
(5)
(6)
其中
,
,
,
为与试验应力相关的函数,
,
,
为模型参数。通过参数估计及方程组的解算可以得到折算后的各应力水平下的等效试验时间。本试验中所记录的数据折算后的结果如表2所示。
由于气缸的寿命分布服从Weibull分布,经折算的数据可以采用GLL-Weibull作为加速模型。最终经计算推测出气缸在常规工作状态(40℃,100 cpm)下的特征寿命为1992.42万次。
3.3. 结果分析
试验结果的分析包括精度及效率两个方面。
精度方面,常规试验的结果为特征寿命为1656.75万次相比于这一结果,本次双应力交叉步降试验所得的结果中,特征寿命的误差为4.57%。
效率方面,比较的依据是试验所消耗的时间,计算公式为
(7)
其中,
为试验消耗的总时间(试验中检测及变换条件的时间忽略不计),
及
分别为不同试验条件下的作动频率及对应的试验次数。
恒定应力加速寿命试验通常会进行多组,因此会消耗大量的试验件和时间,为此曹春苗对气缸恒定应力加速寿命进行了优化,从两种应力每种四个应力水平所组合成的16个应力水平中选出6个应力水平进行实验分析[26] ,同样达到了2%以内的精度,大大提高了恒加试验的效率。忽略试验中检测的时间,表3给出了常规寿命试验及优化后的恒加试验和双应力交叉步降加速试验的效率成本比较。
相对于双应力恒定加速寿命试验,双应力交叉步降试验的所得的特征寿命存在的误差稍大,但仍处于令人满意的范围。由于双应力交叉步降试验的试验件在试验初期损耗速度很快,难免导致对试验气缸失效数据的记录产生滞后,造成记录的数据偏大。在后续的研究中,可以通过在气缸临近失效时加大检测频率来获得更精确的失效数据。而根据表3的结果,可以看出,常规寿命试验相比,双应力交叉步降试验的在试验件的消耗上增加了一倍,但试验时间仅为常规试验的20%左右。恒加试验通常包括多组样本及试验应力,试验设备数量越多,越有利于提高试验效率,但这需要大量的物力消耗,设备不足时其试验效率十分低下。综合来说,双应力交叉步降试验的人力物力消耗总量远远小于常规寿命试验及恒定应力加速寿命试验。
4. 结论
本文阐述了双应力交叉步降试验方法在气缸寿命试验中对于试验效率提升的作用,并通过具体的试验对这一观点进行了验证。根据试验结果,双应力交叉步降加速寿命试验的效率相对于常规寿命试验及恒定应力加速寿命试验有很大的提升,而试验结果的精度也是令人满意的。后续的研究将进一步这一方法的精度。总体来说,双应力交叉步降加速试验在很多高可靠性产品的寿命测试中有着很大的应用前景。
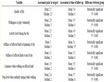
Table 2. Equivalent failure data of each stress combination after conversion (×104)
表2. 折算后各应力组合下的等效失效数据(单位:万次)
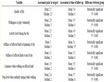
Table 3. Comparison of efficiency and cost between life testing methods of pneumatic cylinder
表3. 各种气缸寿命试验方法的效率及成本对比
致谢
感谢中央高校基本科研业务费专项资金及日本SMC公司对本课题提供的物质帮助,同时感谢本文所参考的文献的作者以及在研究过程中做出贡献的同伴!