1. 引言
随着经济和社会的发展,能源消耗量激增,能源短缺已成为制约我国长期快速可持续发展的主要瓶颈之一。发展高效能源传递与热功转换技术以提高能源的利用率成为缓解能源短缺问题的重要途径之一。在能源、电力、化工等高耗能领域,换热器作为一种基本的热量传递设备,在金属消耗、动力消耗和投资方面占有重要份额。发展高效强化传热新技术对于高耗能领域的节能具有重要的科学和现实意义。与单相对流换热相比,沸腾传热具有传热温差小、换热系数相对较高等优点,广泛应用于具有小温差的低品位能源热利用领域。强化沸腾换热主要目的包括:1)进一步提高换热设备效率,减少能量传递中的不可逆损失;2)更加合理和有效地利用能源,减小换热面积,降低金属消耗量;3)尽可能的降低换热元件的壁面温度,保证换热设备的安全运行等。传统的强化换热技术可分为有源强化技术和无源被动强化传热技术[1] 。有源强化传热技术[2] [3] 需要额外的泵功等能源消耗,包括增大流速、采用外部电场、磁场、声场等技术强化传热,无源强化传热技术[4] [5] 主要通过改变换热部件的结构来实现,包括采用扩展表面、沟槽管、添加剂、内插物等。已有关于针对管内沸腾传热的强化大都采用基于实验的经验或半经验方法进行研究,这是由于气液可变形相界面的复杂性,使得建立完整的相变传热理论体系较为困难。国内外学者关于管内沸腾传热强化的研究主要通过改变固液/气液界面的性质来实现,如通过人造核化穴降低沸腾起始温度[6] 、通过改变界面的润湿性[7] 提高传热系数以及通过加入添加剂[8] 改变气液界面的张力来改善相变传热等等。沸腾换热传热特性与管道内的气液两相流流型密切相关,如对于流动沸腾,环状流区由于薄液膜蒸发传热使得该类流型对应于管内最高的传热系数。陈宏霞等[9] 在冷态条件下,研究了内嵌金属丝网管对空气/水两相流流型的调控特性,发现内嵌金属丝网管能够改变水平管内的气液两相流型,但他们的研究是在冷态条件下进行的,而在沸腾条件下,沿管长方向的流型是不断发展变化的,内嵌金属网管对竖直蒸发管内流型影响特性与冷态条件完全不同,因此本文搭建了热态试验台,以期获取内嵌金属网管对流动沸腾换热的影响特性,为该技术在沸腾换热领域的应用奠定科学依据。
2. 实验系统及实验方法
为获取内插金属网管对竖直蒸发管内流动沸腾换热的影响规律,分别采用普通的光滑蒸发管及具有内嵌金属网管的蒸发管进行对比实验研究,在保持入口条件相同的情况下,获得传热系数的沿程分布特性。本研究采用的实验台如图1所示,整个实验系统包含两个回路,即主实验回路和冷却水回路。在主
(a) (b)
Figure 1. The experimental setup. 1. fluid pump; 2. Coriolis mass flowmeter; 3. backpressure valve; 4. regenerator; 5. preheater; 6. view section; 7. test section; 8. needle valve 1; 9. needle valve 2; 10. cooler; 11. water storage tank; 12. filter; 13. needle valve 3; 14. ball valve; 15. vacuum pump; 16. high pressure nitrogen; 17. cooling water pump; 18. cooling water box; 19. cooling water tower
图1. 实验系统。1:工质泵;2:科氏力质量流量计;3:背压阀;4:回热器;5:预热器;6:可视段;7:实验段;8:针阀1;9:针阀2;10:冷却器;11:储液罐;12:过滤器;13:针阀3;14:球阀;15:真空泵;16:高压氮气;17:冷却水泵;18:冷却水箱;19:冷却塔
回路中,采用去离子水为工质,工质由齿轮泵从储液罐中抽出并依次流经流量计、背压阀、回热器低温侧、预热器、实验段、回热器高温侧、冷却器,最后回到储液罐完成一个闭式循环;冷却水回路主要有冷却水泵、冷却水箱及冷却塔组成,用于排除主实验回路产生的热量。实验开始前,首先对整个试验回路进行抽真空后再注入去离子水,以排除不凝性气体对沸腾换热的影响。储液罐通过精密调压阀与高压氮气瓶连接,通过该精密调压阀可以控制实验段的运行压力。
实验开始前,首先对整个实验系统进行抽真空注液。储液罐通过高精度调压阀与氮气瓶相连用于控制实验系统的运行压力。齿轮泵用于调节实验管路内的流量,预热器和主实验段分别与两个低压大电流加热器相连。通过调整预热器加热功率,在主实验段进口分别获得泡状流、弹状流、混快状流及混块/环状流等流型,通过数据采集得到主实验段进口压力、进出口压差以及实验段的沿程温度分布,进而得到传热系数的沿程分布特性。
图2给出了实验段(2a)及内插金属网管的装配示意图(2b),图2(c)给出了金属丝网的扫描电镜(SEM)图像,可以看出,金属丝网管的表面为编制的致密网状结构。工质经预热器预热后流经进口可视段进入竖直蒸发管实验段,实验段受热外管为316 L不锈钢管,其内径为14.03 mm,受热外管直接采用大电流通电的方式进行加热。实验段进出口可视段均采用耐热玻璃管,以便于对进出口的流型进行观察。金属丝网管是由目数为200 PPI的不锈钢金属丝网制作,网管外径为10.5 mm, 网面厚度为0.2 mm,网孔孔径为75微米。金属网管作为内插物直接插入不锈钢受热外管,并由支撑卡环支撑使其与外部受热管保持同心,金属网管通过靠近端部的固定卡环固定,防止金属网管与受热外管发生轴向的相对运动。固定卡环用于固定金属网管和受热外管的轴向相对位置。在主实验段受热管外壁沿程焊接了K型热电偶用来测量沿程的温度分布,热电偶为等距分布。
3. 数据处理及参数的不确定度分析
为计算实验段沿程传热系数,必须先进行主加热段内壁温的计算,已知实验段外壁温,并假设在绝
(a) (b) (c)
Figure 2. The schematic diagrams of the test section and mesh cylinder insert. (a) the test section; (b) assembly of the mesh cylinder insert; (c) SEM of the mesh surface
图2. 实验段及内插金属网管示意图.(a)实验段;(b)金属丝网管装配;(c)丝网面SEM图像
热边界条件下,进行一维的有内热源圆筒壁的导热计算。通过计算可推导出主加热段内壁温计算公式:
(1)
式中,
为实验段沿程外壁温度,℃;
:实验段电源加热功率,W;
为实验段校核后的热效率,取90%;D为实验段受热外官的外径,单位:m;d为实验段受热外管的内径,单位:m;L:实验段有效加热长度,单位:m。
对流传热系数计算公式如下所示:
(2)
其中,q为实验段上的热流密度,W/m2;h为传热系数,W/m2k;Twi为实验段内壁温度,℃;Twa为工质温度,℃。
表1定量给出了实验研究参数的不确定度,其中仪表的不确定度由测量仪器厂家给定,对于间接测量,采用误差传递函数计算得出。
4. 结果与讨论
4.1. 入口为泡状流
在质量流速为G = 350.77 ± 2.00 kg/m2,进口压力Pin = 256.99 ± 6.00 kPa,进口过冷度为0.7℃时条件下,对主加热段入口为泡状流时的壁温和传热系数分布特性进行了研究。
图3给出了泡状流条件下普通光管与具有内嵌金属网管的新型蒸发管的碧温随干度的变化特性,其中Tb为普通光滑蒸发管的壁温分布特性,Tm为具有内嵌金属丝网管的新型蒸发管壁温分布特性,可以看出,对于普通光管和具有内嵌金属丝网管的新型蒸发管,壁温均随干度的增大而降低,这是由于在泡状流区,随着干度的增加,蒸发管内的传热由过冷状态泡状流转换为饱和态泡状流,气泡生长和脱离频
(a) (b)
Figure 3. The characteristics of temperature and heat transfer coefficiency distributions for the bubbly flow (q = 29.04 kW/m2). (a) the temperature distribution; (b) the heat transfer coefficiency distribution
图3. 入口泡状流条件下壁温及传热系数分布特性(q = 29.04 kW/m2).(a)壁温分布;(b)传热系数分布
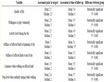
Table 1. Uncertainties of the parameters
表1. 参数的不确定度
率增大,气泡数量增多,气泡核化数量的增加以及核化气泡对流场的扰动使得换热增强和壁温降低。从传热系数沿程分布特性来看,在靠近受热管入口处,具有内嵌不锈钢丝网管的蒸发管具有较高的传热系数,在受热管中间段,两者的传热系数基本持平,而在靠近出口处,具有内嵌金属网管的蒸发管传热系数快速增加,显著大于普通光管的传热系数,这是由于在网管调控区进口处,由于网管端面的阻碍作用,使得上游来流工质的大部分经网管与受热外管的环隙之间流过,增加了进口的对流强度,从而强化传热;对于干度较低的泡状流,其传热机理包含核态沸腾和强制对流两种效应,当干度较小时,强制对流起主导作用,随着干度的增大,核态沸腾的主导作用变得显著。对于具有内插金属网管的新型蒸发管,网管的作用体现在:1)在入口附近,网管增加了上游来流的扰动强化传热;2)在蒸发管中间段,气泡在近壁区的扰动与金属网管对网管内外流体的湍流搅浑作用的阻碍作用相平衡,使得传热系数与普通金属网管相接近;3)在靠近蒸发管出口处,由于气泡的长大受制于环隙的空间尺度限制,气泡变为扁平状,使得气泡与受热壁面之间形成薄液膜传热,从而使得整体传热系数较普通光管增大。
4.2. 入口为弹状流
图4给出了质量流速为G = 353 ± 3.00 kg/m2,进口压力Pin = 256.99 ± 6.00 kPa,受热外管热流密度为37.18 kW/m2条件下,当入口为弹状流时普通光管和具有内插金属网管的新型蒸发管的壁温和传热系数变化特性。由图4(a)可知,对于光滑管和内插金属网管的蒸发管,壁温均随着干度增加而增大,并且新型蒸发管的壁温要显著低于普通光管的壁温2℃ - 4℃。从图4(b)所示的传热系数看,具有内插网管的新型蒸发管沿程传热系数均大于普通光管的传热系数,并且越到下游,传热系数增大的速度越快。通常,弹状流区的传热机理主要包含两方面,即(a)汽弹与受热壁之间存在的薄液膜蒸发换热;(b)汽弹尾流区的尾涡对流增强。当汽弹较短时,由于在整个管道截面上,尾涡区的时均截面占比较大,因此,对流增强作用显著。当汽弹较长时,对于特定的截面,当汽弹和液弹间歇通过时,薄液膜蒸发传热的时间占比较长,此时,薄液膜蒸发传热占主导地位。由于内插金属网管一方面阻碍了网管内外的湍流搅混使得传热弱化,另一方面使得进入网管调控区的汽弹变得更加狭长而增加了薄液膜传热区域,在相对较低的干度下,由于汽弹尾涡的对流效应为主导机理,网管对该尾涡对流效应的阻碍使得传热恶化,如图4(b)前三个截面,插入网管后的传热系数比普通光滑管略低;随着干度增加,伴随着汽弹的长大和变长,薄液膜传热机理变为主导,此时,内插金属网管由于增加了薄液膜传热区域而显著强化传热,靠近出口处的传热系数比普通光管最大强化2.4倍。
4.3. 混块状流
图5给出了质量流速为G = 354.33 ± 2.00 kg/m2;进口压力Pin = 262.25 ± 6.00 kPa,进口干度为Xin = 0.0033141,受热管热流密度为51.76 kW/m2条件下,当入口如混块状流时普通光管和具有内插金属网管的新型蒸发管的壁温和传热系数变化特性。混块状流是由弹状流发展而来的,随着热流密度的增大,汽弹在长大过程中其速度也持续增大,当汽弹周围的下降液膜发生液泛时弹状流便转换为混块状流,当混块状流进入丝网调控区域时,由于网管端面的界面张力作用,气相进入环隙,只有液相进入网管。在沿程的环隙空间内,由于截面含汽率较大,一方面容易发生蒸干造成局部温度升高,另一方面由于蒸发过程导致环隙内蒸汽迅速增多同时压力增大,当蒸汽压力突破网管的界面张力时,蒸汽相经由网管侧壁进入到网管内部,同时网管内的液体进入到环隙空间,这样网管内外变产生了气液的交换,这种气液交换现象的存在可以在受热壁面产生再润湿,壁面受热壁面长期蒸干烧毁,这对于传热是有利的。在靠近网
(a) (b)
Figure 4. The characteristics of temperature and heat transfer coefficiency distributions for the slug flow (q = 37.18 kW/m2). (a) the temperature distribution; (b) the heat transfer coefficiency distribution
图4. 入口弹状流条件下壁温及传热系数分布特性(q = 37.18 kW/m2).(a)壁温分布;(b)传热系数分布
(a) (b)
Figure 5. The characteristics of temperature and heat transfer coefficiency distributions for the churn flow (q = 51.76 kW/m2). (a) the temperature distribution; (b) the heat transfer coefficiency distribution
图5. 入口混块状流条件下壁温及传热系数分布特性(q = 51.76 kW/m2).(a)壁温分布;(b)传热系数分布
管进口区域,如图5(b)所示,插入金属网管后,由于网管对截面湍流交换的阻碍作用,传热系数略降低;在网管下游,由于网管内外强烈的气液交换,使得传热系数得到进一步强化。与弹状流区域相比,混块状流的传热系数强化比最大为3.7倍,显著大于弹状流区,这是由于混块状流区域的湍流对流作用为主要传热机理,普通光管的传热系数相对于弹状流区域要低,这使得强化传热比相对较大。
4.4. 入口为混块/环状流
在本研究中,混块/环状流定义为混块状流到环状流过渡的一种流型结构,其截面含汽率位于混块状流和环状流之间。针对该类流型,如图6(a)所示,普通光管和具有内插金属丝网管的蒸发管壁温沿流动方向呈逐渐降低趋势。从传热系数角度分析,如图6(b)所示,在靠近丝网管调控区入口处,具有内插金属丝网管的蒸发管的传热系数较低,即进口附近出现传热恶化区,这是由两方面的原因造成的:1)在近环状流区,普通光管中的两相流换热系数相对较大;2)插入的金属网管部分抑制了管内气液两相流在径向方向的热质交换。在蒸发管下游,传热系数逐渐增大并且具有内插金属网管的新型蒸发管的传热系数超过普通光管,这是由于在下游,蒸发管内环状流较混块状流占比增大。在环状流未发生蒸干之前,金属网管的作用在于,将整个蒸发管内部分成网管内外两个空间,由于网管侧壁为尺度为75微米的微孔,径向方向的动量交换被部分抑制,环隙区内受热壁面上液膜附近的蒸汽具有更高的流速,从而使得液膜较普通光管变薄更为迅速,越薄液膜对应更高的传热系数。同时,我们也可以推理针对高干度环状流区,内插金属网管将阻碍内部气芯中的液滴重新在受热壁面沉降,这将导致较早的发生蒸干过程,因此,针对高干度环状流,为避免蒸干过早发生,并不推荐采用内嵌金属丝网管来强化传热。
5. 结论
针对竖直管内流动沸腾换热,在已有冷态空气/水两相流流型调控基础上,采用不锈钢金属丝网管作为内插物,研究了泡状流、弹状流、混块状流及混块/环状流的壁温及传热系数沿程分布特性。研究发现,金属丝网管对传热的影响主要表现在两个方面,即1)金属丝网管将整个受热蒸发管内部分为环隙区和网管内部区,网管侧面的微孔对受热管内部径向方向的湍流搅混产生抑制作用,使得强制对流效应为主导的传热发生弱化;2)在相对较低的干度下,由于金属网管侧壁的界面张力作用,环隙内的蒸汽无法进入网管内部而变为被挤压的狭长气泡,增大了薄液膜传热的区域,使得薄液膜蒸发效应增强。实验总体证明,采用金属网管强化竖直管内沸腾换热在泡状流、弹状流和混块状流区域均效果显著,但对于环状流,由于网管将阻碍汽核中携带液滴的再沉降,使得蒸干过早发生,因此,不建议在环状流区采用该技术。
(a) (b)
Figure 6. The characteristics of temperature and heat transfer coefficiency distributions for the churn/annular flow (q = 30.65 kW/m2). (a) the temperature distribution; (b) the heat transfer coefficiency distribution
图6. 入口混块/环状流条件下壁温及传热系数分布特性(q = 30.65 kW/m2).(a)壁温分布;(b)传热系数分布
致谢
本研究得到北京市自然科学基金(3132018)和中央高校基本科研业务费专项资金(JB2015068)资助,在此表示感谢。
基金项目
北京市自然科学基金(3132018)和中央高校基本科研业务费专项资金(JB2015068)资助。