1. 引言
镁及其合金具有化学活性高、易降解、力学相容性及生物相容性好等优点,在生物医用材料领域具有广阔的应用前景 [1] [2] 。但是,从目前的实验结果来看,镁合金在生物体环境中存在降解速度过快、力学性能降低的问题 [3] [4] 。因此,提高镁合金在生物体环境中的耐腐蚀性能是当前研究的重点,实现途径主要有两个:一是通过合金化改善镁合金本身的耐腐蚀性能,降低其降解速度;另一条途径是通过表面处理,改善合金的耐腐蚀性能。在合金化研究方面,除了考虑添加元素对合金耐腐蚀性能的影响外,还须考虑添加元素在生物体内的毒性反应。Al元素是镁合金中最常用的合金化元素,不仅可有效提高合金的力学性能,且可保持较高的塑性,是结构件用镁合金中广泛添加的元素之一 [5] - [9] 。但是,研究表明 [10] [11] ,Al元素不是人体必需的元素,且具有神经毒性,可能危害人类健康,尽管也有部分研究人员的实验表明Mg-Al系合金具有较好的生物相容性,理由是其在模拟体液中的腐蚀产物是人体的必需物质 [12] 。总之,Mg-Al系合金作为生物医用材料使用尚存争议,还须进一步验证 [13] 。为避免Al元素的影响,近年来,又开发了Mg-Ca系 [14] - [16] 和Mg-Zn [17] [18] 系等生物医用镁合金,Ca元素是骨骼中含有的重要元素,Zn也是人体必需的元素,故在含量适当的情况下,可保证合金的生物相容性且无生物毒性,属于较合适的添加元素;此外,研究还表明,添加少量的稀土元素可在一定程度上提高合金的力学性能及耐腐蚀性能 [19] ,由此开发了Mg-Zn-Ca-RE合金,但在添加稀土元素时,需排除Pr、Ce、Lu等对人体有害的元素 [20] [21] 。本文即以应用前景较好的Mg-Zn-Ca-Gd合金为研究对象,研究了合金的固溶工艺及其对耐蚀性能的影响,研究结果可为该合金的制备奠定基础。
2. 实验
本文所制备试验合金的名义成分为Mg-4.0Zn-0.2Ca-1.0Gd (wt.%)。合金的原材料为纯锌锭(>99.9 wt.%)、Mg-10 wt.% Ca中间合金及Mg-30 wt.% Gd中间合金。金相腐蚀液的化学成分为2.5 g苦味酸、35 ml无水乙醇、5 ml乙酸和5 ml水。电化学测试所用溶液为浓度3.5% NaCl溶液(模拟海水)和市购Hank’s模拟体液(生产厂家:Beijing Solarbio Science & Technology Co.Ltd)。合金经熔炼、精炼后用铁模浇注,熔炼过程中采用氩气保护以减少氧化。采用电火花线切割机将铸锭切成15 × 15 × 3 mm样品进行固溶处理研究,为减少氧化,固溶处理过程中同样采用氩气进行保护,固溶结束后将样品快速水冷,转移时间小于3 s。用于金相观察及扫描电镜观察的试样首先在水磨砂纸上进行预磨,然后采用抛光液进行机械抛光,最后采用腐蚀液进行腐蚀,腐蚀方式为浸蚀,腐蚀时间大约为15~20 s。金相观察在上海伦捷机电仪表有限公司生产的4XC-MS型金相显微镜上进行,扫描电镜观察在Quanta 200型扫描电镜上进行,并采用配备的能谱仪对第二相进行成分分析。用于硬度测试的样品首先在砂纸上打磨光亮,然后在莱州华银试验仪器有限公司生产的200HV-5型小负荷维氏硬度计上进行,文中数据为5个测试点的平均值。用于X射线衍射的样品尺寸为18 × 15 × 3 mm,运用Rigaku D/Max 2500型18KW转靶X射线衍射仪和Jade 5.0软件进行物相分析,测试时的扫描速度为7˚/min,入射束为CuKα射线,扫描角度范围为10˚~80˚。电化学测试在上海辰华仪器有限公司生产的CHI760E型电化学工作站上进行。
3. 结果与讨论
3.1. 铸态显微组织
图1所示为合金铸态的金相显微组织。从图中可以看出,铸态合金的晶粒组织较为粗大,且尺寸不均匀。如图所示,A箭头对应晶粒的尺寸明显大于B箭头对应晶粒,经截线法进行统计,铸态合金的平均晶粒尺寸为106 μm。除晶粒粗大外,在晶内及晶界还可观察到不同形状的第二相颗粒,如图中箭头C所示。这类第二相颗粒在扫描电镜下呈白色(图2)。从A区域的能谱分析结果可知,在铸态合金中,镁基体内Ca和Gd元素的含量非常低,仅Zn元素具有一定的溶解量。由此说明,由于铸造过程中合金凝固速度较快,先凝固出的固相中溶质原子没有足够的时间进行扩散。从颗粒B所示的能谱分析结果可以看出,主要元素为Mg、Zn和Gd,且Mg原子与(Zn + Gd)原子之比接近1:1,Ca的含量较少;从分布的位置来看,这种颗粒主要存在于晶界上。对另一种颗粒C的能谱分析结果则表明,其主要含有合金元素Gd,Ca和Zn的含量则较少,从原子含量的比例来看,Mg原子与Gd原子的比例接近5:1。颗粒D的形状及尺寸与颗粒C的相似,均为不规则的小颗粒,但从能谱分析结果来看,则存在较大差异,该颗粒中Ca的含量为10.05 at.%,Zn的含量为35.69 at.%,Mg的含量为52.61 at.%,Gd元素的含量很低,仅为1.65 at.%。
为探明合金中第二相的化学成分,本文采用X射线衍射仪对铸态合金进行了分析,结果如图3所示。由图可知,除α-Mg基体的衍射峰外,在其它位置也出现了一些小的衍射峰,经过与PDF卡片进行比对,可知这些衍射峰分别对应Mg2Ca、Mg5.05Gd、MgZn及Ca2Mg6Zn3。结合前述在扫描电镜下对第二相的能谱分析结果,可知晶界上的条状第二相颗粒为MgZn相,但部分Gd原子取代了Zn原子的位置。形状不规则的小尺寸颗粒则分别为Mg5.05Gd相和Ca2Mg6Zn3相。这些第二相颗粒尺寸达到微米级,且与基体不共格,在受拉力变形时可能成为裂纹源,应通过随后的热处理将其溶入基体。
3.2. 微观组织与力学性能演变
根据文献,非平衡共晶α-Mg/MgZn在
341 ℃
左右将发生溶解,α-Mg/Mg2Ca、α-Mg/Ca2Mg6Zn3及α-Mg/Mg5.05Gd的溶解温度则分别约为
517 ℃
、
400 ℃
和
548 ℃
。因此,为使上述不同种类的第二相颗粒充分溶入基体,本文采用分级固溶的方式,各级固溶温度确定为
320 ℃
、
400 ℃
和
500 ℃
。
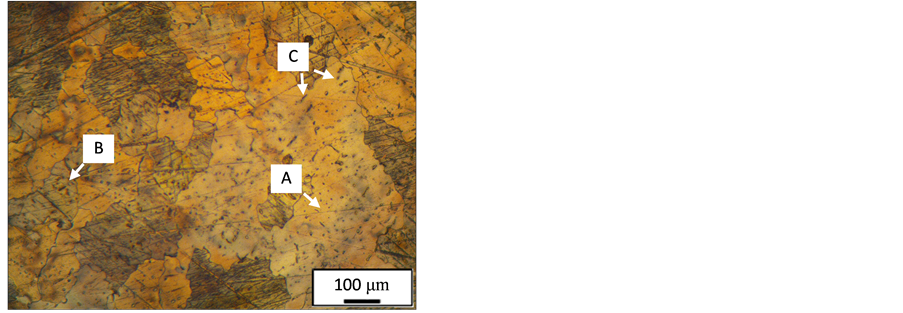
Figure 1. Optical microstructure of the experimental alloy with as-cast state
图1. 试验合金的铸态金相显微组织
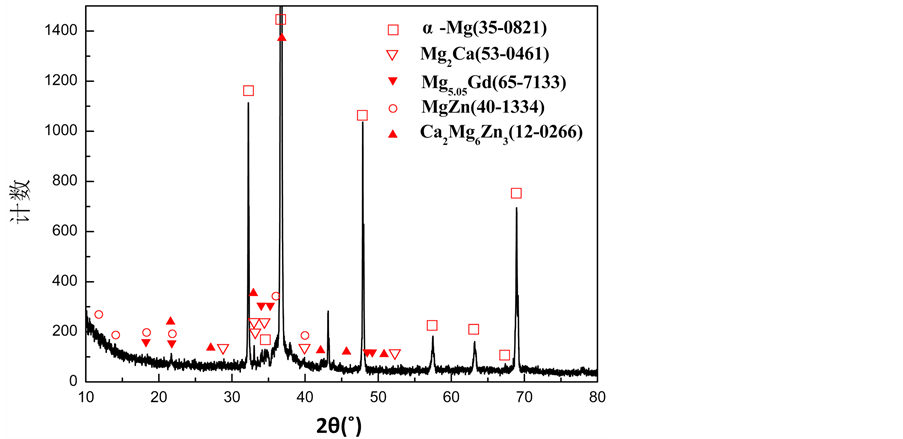
Figure 3. XRD results of the experimental alloy with as-cast state (the PDF card numbers are shown in brackets)
图3. 试验合金铸态的X射线衍射结果(括号内为PDF卡片编号)
图4(a)示出了合金在
320 ℃
条件下固溶不同时间后的硬度曲线。由图可知,合金铸态的硬度值大约为50,随着固溶时间的延长,合金的硬度先降低后保持稳定。从前述对合金铸态微观组织的分析可知,在铸态中存在较多因非平衡凝固而产生的第二相颗粒,这些颗粒虽然尺寸较大,均为微米级,与基体也不共格,但仍对位错运动有一定的阻碍作用,导致合金的硬度较高。在固溶过程中,随着这些第二相颗粒溶入基体,强化作用降低,尽管固溶进入基体的原子也能产生一定的固溶强化效果,但同时晶粒的长大也将使合金的硬度有一定程度的降低。因此,随固溶时间的延长,合金硬度降低是由上述三种因素综合
(a)(b) (c)
Figure 4. Ageing curves of alloys with different solution treatments: (a) 320˚C/xh; (b) 320˚C/6h + 400˚C/xh; (c) 320˚C/6h + 400˚C/6h + 500˚C/xh
图4. 不同制度固溶处理后的硬度曲线:(a) 320℃/xh;(b) 320℃/6h +
400 ℃
/xh;(c) 320℃/6h +
400 ℃
/6h +
500 ℃
/xh
竞争作用的结果,最终使合金软化的因素强于使合金硬化的因素,导致合金的硬度降低。为避免晶粒过分长大,同时又达到较好的固溶效果,本文选择硬度刚好到谷底的6 h作为第一级固溶的时间。从金相显微组织来看(图5(a)),晶界及晶内的第二相颗粒的数量有一定程度降低,达到了较好的固溶效果。
经第一级固溶处理后,将温度升高到
400 ℃
继续进行固溶以消除熔点较高的第二相颗粒。在
400 ℃
进行第二级固溶时,合金的硬度出现小幅度波动(图4(b)),但均基本维持在40左右。在固溶6 h后,合金中第二相颗粒明显减少,晶界变得更加清晰,晶粒也变得较粗大,如图5(b)所示。根据前述扫描电镜结果,残留的粗大相应为Mg元素与Gd元素形成的Mg5.05Gd相,为消除这些粗大第二相颗粒,本文将固溶温度升高至
500 ℃
,进行第三级固溶。合金硬度随第三级固溶时间的变化情况如图4(c)所示,随固溶时间的延长,合金的硬度逐渐降低,并在4~8 h时呈现出低硬度值平台,硬度的降低可能与合金固溶后晶粒长大有关。图5(c)示出了合金经
500 ℃
固溶6 h后的金相显微照片,从图中可以看出,合金的晶粒已明显长大,但与双级固溶后的样品(图5(b))相比,合金中第二相颗粒的数量明显较少,颗粒的尺寸也显著降低,达到了良好的固溶效果。因此,
320 ℃
/6h +
400 ℃
/6h +
500 ℃
/6h是较优的固溶处理工艺。
3.3. 耐腐蚀性能
为探明合金在生物体内的耐腐蚀性能,本文研究了其在模拟体液中的腐蚀行为,作为对比,同时研究了其在模拟海水中的腐蚀行为。图6示出了合金在模拟体液和模拟海水中的极化曲线。由图可知,合金在两种介质中的自腐蚀电位分别为−1.578 V和−1.656 V。一般而言,自腐蚀电位越高,合金的耐腐蚀性能越好。因此,合金在模拟体液中的耐蚀性能优于模拟海水中的耐蚀性能。通过与其它镁合金的自腐蚀电位进行对比 [22] ,可知该合金具有较为优异的耐蚀性能。
4. 结论
通过研究固溶处理对Mg-4.0Zn-0.2Ca-1.0Gd合金的微观组织与性能的影响规律,得到了如下结论:
1) 合金铸态的由α-Mg基体及非平衡共晶组成,非平衡共晶主要为Mg2Ca、Mg5.05Gd、MgZn及Ca2Mg6Zn3。
2) 合金较优的固溶处理工艺为:
320 ℃
/6h +
400 ℃
/6h +
500 ℃
/6h,经该工艺处理后,非平衡共晶可基本溶入基体,达到了较好的固溶效果。
3) 合金在模拟体液及模拟海水中均具有相对较优的耐蚀性能,其自腐蚀电位分别为−1.578 V和−1.656 V。
(a) (b) (c)
Figure 5. Optical microstructure of alloys with different solution treatments: (a) 320˚C/6h; (b) 320˚C/6h + 400˚C/6h; (c) 320˚C/6h + 400˚C/6h + 500˚C/6h
图5. 不同制度固溶处理后的金相显微照片:(a) 320℃/6h;(b) 320℃/6h +
400 ℃
/6h;(c) 320℃/6h +
400 ℃
/6h +
500 ℃
/6h
(a) (b)
Figure 6. Potentiodynamic polarization curves of the solution treated alloy in different environments (a) Simulated body fluid (b) Simulated sea water
图6. 固溶态合金在不同环境中的极化曲线 (a) 模拟体液;(b) 模拟海水
基金项目
湖南省自然科学基金(2016JJ5042)。