1. 引言
塑料制品从设计到成型是一个非常复杂的过程,包括塑料制品的设计、模具结构设计、模具加工制造和模具生产等几个主要方面。需要产品设计师、模具设计师、模具加工工艺师及熟练操作工人协调努力来完成,这是一个设计、修改、再设计的反复迭代、不断优化的过程。目前大多数模具设计人员主要是依据自己的经验来确定模具的设计方案,但由于塑料制品的多样性、复杂性和设计人员经验的局限性,长期以来,工程技术人员很难精确地设计出一套可以减少成本、节省时间、提高产品质量及合格率的最佳工艺方案 [1] [2] 。
目前,CAD/CAM在模具设计与制造中运用比较成熟,而要设计和制造出高质量的模具,仅仅依靠CAD/CAM是不够的,必须运用CAE技术,本文采用Moldflow软件对导轨式电源外壳的充填、冷却和保压过程进行了动态模拟,为模具设计及注塑工艺参数的确定提供了一定的理论依据,改善了塑件的成型质量。
2. 塑件结构及材料分析
2.1. 塑件的结构分析
导轨式电源外壳三维示意图如图1,塑件两侧面均为类似蜂窝状的进、出风口,塑件底部由于是卡勾结构,局部壁厚偏厚,由于与电源上盖装配具有方向性,外壳的口部局部减胶增加防呆缺口、止口功能。其总的外形尺寸为75 mm × 72.5 mm × 90 mm,壁厚最大处为4.0 mm;壁厚最小处为0.5 mm,如图1所示。该塑件为外观件,要求其表面光滑、平整,不能有明显的熔接痕、气泡、银丝、缩孔、翘曲及变形等缺陷。
2.2. 塑件的材料分析
塑件材料为ABS + PC,材料牌号为Bayblend FR1514,材料加工参数如表1所示。
3. 模流分析
塑件整体成对称结构且为外观件,考虑浇口要么位于产品底部外表面的中间位置,要么位于产品底部内表面的中间位置,可以得到完美的外观,但模具的制造成本会增加,且由于模仁的空间有限冷却水路无法布置,只能将浇口位于产品底部外表面的中间位置,Moldflow自动生成的最佳浇口位置也是接近于在产品底部外表面的中间位置,如图2所示,与浇口位置的初步设想基本一致。
塑件底部外表面的浇口位置区域是产品的功能区域,不能有浇口残留,同时考虑到产品的外观要求高,即采用热流道技术,从而还能缩短成型周期,节省塑料原料,且利于生产自动化。模具布局方式一模一腔即可满足产品的年采购需求,创建完成的浇注系统与冷却系统如图3所示。
参考原材料的加工参数表,工艺参数设置如下:模具表面温度为60℃,熔体温度为260℃,开模时
间为5 s,速度/压力切换为97%充填体积,保压压力为注射压力的80%。Moldflow分析序列为冷却 + 填充 + 保压 + 翘曲。
3.1. 充填分析
3.1.1. 充填时间分析
在塑料熔体充填过程中,充填时间较短,如图4可以看出,塑件完全充满需2.428 s。但是通过动画模拟可知塑料熔体不能同时到达两侧型腔的末端,可见产品填充不太平衡。
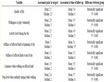
Table 1. Injection parameter of Bayblend FR1514
表1. Bayblend FR1514的加工参数
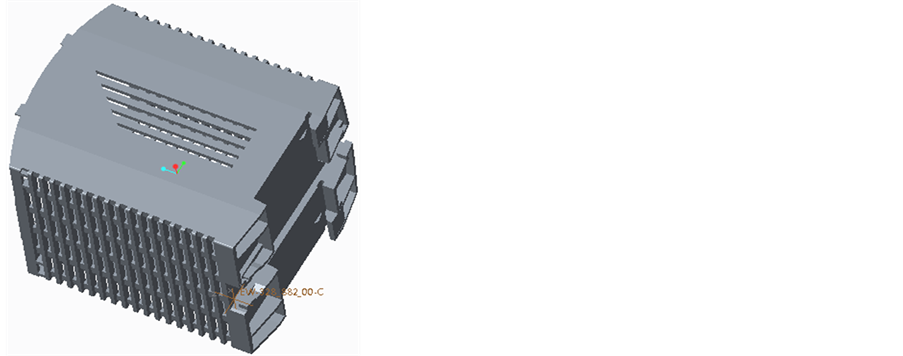
Figure 1. DIN-rail power supply housing 3D
图1. 导轨式电源外壳三维示意图
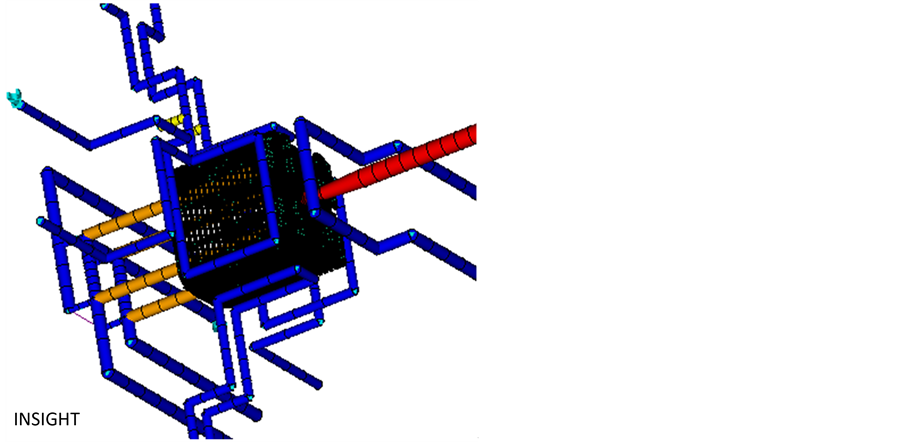
Figure 3. Injection system and cooling system
图3. 浇注系统与冷却系统
3.1.2. 流动前沿温度分析
流动前沿温度是衡量物料充填后塑件质量的重要指标。注塑完成后,合理的温度分布应该大致均匀,模型的温度差一般允许值为20℃ [3] ,流动前沿温度过低,会使塑件外观差,外壁不光滑,严重的时候会充不满塑件,或者有明显的熔接痕。流动前沿温度过高,会导致物料分解,温度过高可能导致塑件内部产生残余应力,而残余应力会导致塑件发生翘曲,严重影响塑件的质量。从图5可以看出,流动前沿温度最高为274℃,符合原材料推荐的成型温度范围250℃~280℃,但是最大温差为34.2℃,熔体的流动前沿温度分布不均匀,格栅区域温度较低。
3.1.3. 熔接痕分析
当两股聚合物熔体的流动前沿汇集到一起,或一股流动前沿分开后又合到一起时,就会产生熔接痕,
熔接痕可以导致塑件表面缺陷,强度降低,应该尽量减少。如图6所示,熔接痕位于格栅区域,若无法避免可能会出现塑件欠注的缺陷。
3.1.4. 气穴分析
气穴的形成是由于模腔内塑料不足,外圈塑料冷却固化,使得内部塑料产生收缩形成真空。气穴可能使塑件没有被完全充填,塑件内部存在气孔;气穴可能导致燃烧,使塑件出现烧焦的现象。气穴应该分布在塑件的边界上,避免在塑件A面上出现气穴,如图7所示,气穴位于出风格栅区域,分布在塑件A面。
3.2. 冷却分析
冷却系统的优劣对成型效率和塑件的质量的影响很大,冷却系统的影响因素主要有模具结构形式、模具大小及成型投影面积的大小,浇口流道的布置等。一般情况下进出流道的水温差不大于5℃。如图8所示回路冷却液的温度分布可知,进出水口的最大温度差为0.56℃,温差值较小符合塑件的冷却要求;
从图9可知经过冷却后制品的最高温度约为86.44℃,低于设置的顶出温度135℃。
3.3. 翘曲分析
翘曲是由收缩变化过大引起的制品缺陷,一般情况下,导致收缩变过大的原因有3种,冷却不均匀、不同区域的收缩不均匀和分子不均匀 [4] 。如图10(c)所示,从分析结果看最大翘曲变形量为0.5170 mm,其中由于冷却引起的变形很小为0.0742 mm (图10(a)),由于收缩产生的变形为0.5356 mm (图10(b)),因
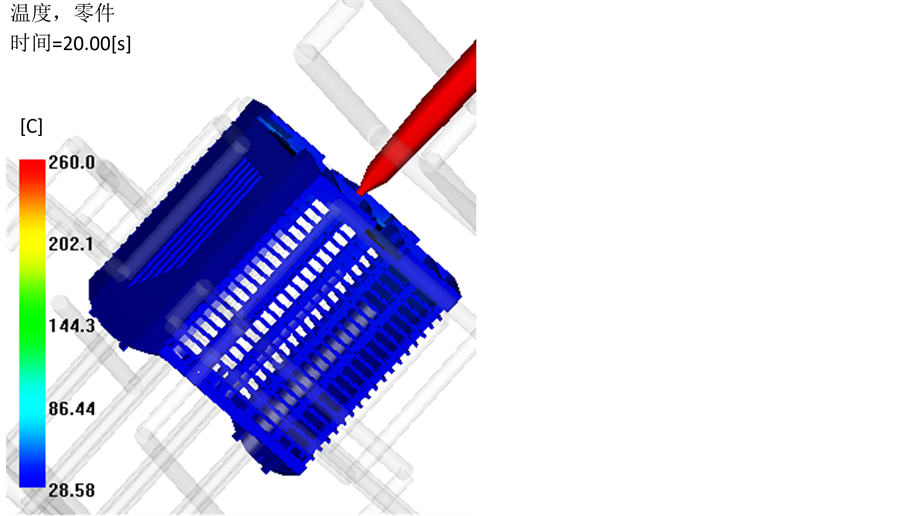
Figure 9. Temperature of part after cooling
图9. 制品冷却后温度
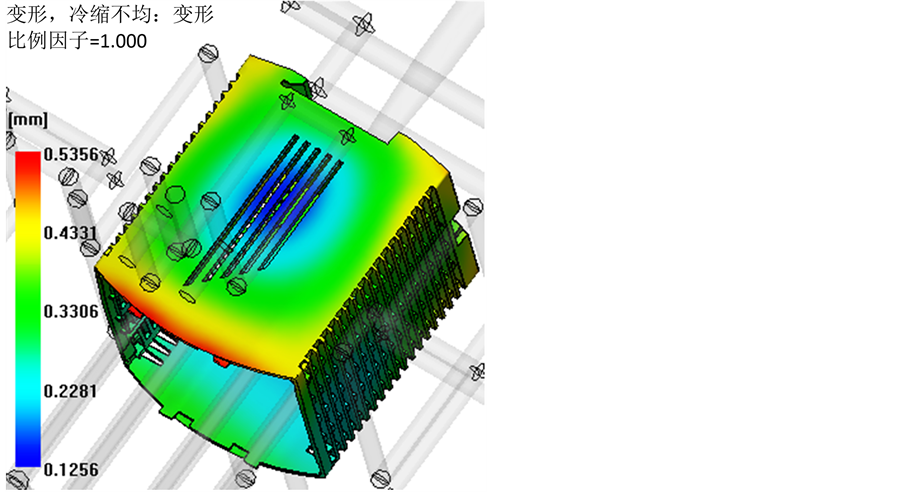
(a) (b)
(c)
Figure 10. (a) Deformation caused by uneven cooling; (b) Deformation caused by uneven shrinkage; (c) Deformation caused by all factors
图10. (a) 冷却不均匀导致的变形量;(b) 收缩不均匀导致的变形量;(c) 所有因素导致的变形量
此收缩是引起的翘曲变形主要原因。
3.3.1. 收缩分析
从模具温度图11可以看出,注塑过程中模具温度分布在26℃~51℃,不满足原材料对模具温度的要求70℃,后续实际生产过程中需要应用模温机。从体积收缩率图12可知,收缩率在−3.660%~1.746%之间,超出了原材料允许的最大收缩率0.7%,收缩率较大的地方集中在制品末端区域和浇口周围。
4. 结论
通过以上的模拟仿真分析,可以得出以下结论:
1) 通过充填分析可知,虽然应用热流道技术提高了塑件填充的平衡性 [5] ,但是由于产品结构的特殊性和局部不对称,塑件还是出现了填充不均匀,格栅区域的熔体温度较低,流动性差,易出现欠注、熔接痕、气穴等缺陷,且由于产品设计的需要无法更改格栅的形状、位置和数量,在模具设计时应重点考虑在相应位置增加排气设计,成型过程中再通过调整和改进注塑工艺来控制熔接痕的大小和位置 [6] ,比如提高注射速度。
2) 通过冷却分析可知塑件的冷却比较均匀,验证了冷却系统的设计、分布是合理的。
3) 通过翘曲变形分析可知,冷却引起的变形很小可以忽略不计,从而又验证了冷却系统的设计是没有问题的,收缩不均才是引起变形的主要原因。塑件的收缩率在很大程度上取决于熔体的补偿能力,而熔体的补偿能力取决于保压压力的大小,以及在该压力下将熔体继续向模内传递的保压时间,这一过程要持续到浇口凝固并封闭为止,保压压力大,保压时间长,则塑件的收缩率就小,因此保压压力和保压时间对塑件的收缩率起着非常重要的作用 [4] 。
如果调整塑件末端区域收缩量,压力如图13(a)所示的变化,延长恒定压力作用时间,塑件末端收缩量减小,反之亦然。
如果调整浇口附近的收缩量,压力如图13(b)所示的变化,压力衰减速度变快,塑件浇口附近收缩量增大,反之亦然。
如果调整塑件中间区域的收缩量,压力如图13(c)所示的变化,把压力衰减过程分为两段,调整压力为图中增加位置,塑件中间区域收缩量减小,反之亦然。
该塑件需要减小塑件末端的收缩量,在实际成型过程中要注意延长保压时间来减小收缩量;同时还需要应用模温机来加热模具并保持模具恒定在工作温度,改善充填流动的平衡性,使成型收缩较充分,后收缩量减小。
5. 结束语
综上所述,针对导轨式电源外壳,运用Moldflow最佳浇口位置的分析结果,得出了初步的设计方案和相应的成型模拟结果,并对模拟的结果进行分析得到了相应的解决方案,对实际生产中设计、修改模具具有很好的参考价值和实践指导意义。