1. 引言
工程上,螺栓若承受较大横向载荷,常常会选择铰制孔螺栓,其螺杆部分与孔之间过渡配合,依靠螺栓本身的抗剪作用防止被连接件的相对滑动。但是由于铰制孔螺栓具有强定位功能,配好后连接件位置不可调,对于夹具类等拆装反复性高的零件,或者在某些特殊的使用工况下,铰制孔螺栓并不适用,只能选择普通螺栓或螺钉,此时横向载荷主要靠预紧力带来的摩擦力承受。
机械设计过程中对螺钉连接强度进行校核是必不可少的环节。一般情况下,螺钉按照《机械设计手册》中的要求选型,使用通用或经验公式进行校核。螺钉正常的安装形式当如图1(a)所示,要求螺钉拧紧后,两零件不会发生相对滑动。
在实际情况下,由于打孔误差、装配误差,或者设备在使用中受到冲击或其它复杂载荷,可能会产生如图1(b)所示的螺接形式。此时,螺钉受到径向载荷作用,除了自身的预紧拉力,还可能受到剪力和弯矩。在这种情况下,螺钉不再是单向受拉。在多个螺钉共同作用时,由于“群体折减效应”,一旦发生破坏往往会在短时间内依次破坏。对于受力较大的承剪螺钉,必须考虑出现这种非正常情况下的安全性。
(a) (b)
Figure 1. Curve: screw connection mode: (a) Normal; (b) Abnormal
图1. 螺接形式:(a) 正常;(b) 非正常
2. 螺钉受力分析 [1]
非正常受力状况下的螺钉可以统一简化为如图2的计算模型。A端以下是被拧入螺孔的部分,B端代表螺钉头。AB段在被连接件的通孔内,长度为L。如此可视该螺钉为悬臂梁结构,在B端产生挠度ω和转角θ。螺钉头受到一个摩擦力F1和力矩M,力矩由螺钉头和连接件表面的机械位置约束产生。螺钉杆存在初始的拧紧力P0,同时螺钉杆上会受到零件滑移产生的剪力F2。螺钉弯矩图见图2(c)。A点弯矩最大,同时还受到剪切和挤压应力,是上述状态中的薄弱点。
(a) (b) (c)
Figure 2. Curve: screw stress analysis
图2. 螺钉受力分析
螺钉头的挠度和转角由摩擦力F1和力矩M引起:
(1)
其中:
由图1,螺钉头的挠度和转角一般被机械结构约束,可以通过几何结构确定其最大值。F1和M分别为:
(2)
其中,E是螺钉材料的弹性模量,I为螺钉截面的惯性矩,
,d1为螺钉的最小截面直径。
螺钉受到的弯矩见图2(c),最大弯矩发生在A端,最大弯矩为:
(3)
则螺钉受到的弯曲正应力为:
(4)
螺钉受到的预紧拉应力为:
(5)
其中P0为螺钉预紧力,A为螺钉公称应力截面积。
则螺钉受到的轴向应力为:
(6)
螺钉受到的剪切应力为:
(7)
螺钉杆受到的挤压应力:螺钉杆受到的挤压应力与挤压接触面积有关。理论上,接触面是一条无宽度的切线。但是由于材料一方面会产生弹性变形,另一方面表面粗糙度会导致“弱接触”情况下的接触刚度较小。而圣维南原理指出,荷载的具体分布只影响荷载作用区附近的应力分布。根据有限元计算中常用的边界设置方法,认为螺钉杆受剪后的接触面积如图3所示。螺杆径向的接触长度为1/3d1,螺杆轴
向的接触长度为3倍螺距,即3P。接触面积
。
则螺钉受到的挤压应力为:
(8)
结合公式(6) (7) (8),可以作出螺钉薄弱点的三向应力摩尔圆(图4):
可以解得主应力为:
(9)
螺钉薄弱点的最大正应力与最大切应力分别为:
(10)
可以通过以上公式校核承受径向载荷螺钉的静强度。
3. 实例计算
3.1. 离心场下静压轴承的螺钉连接方式
在某离心机上安装有四个全密封静压轴承,共同对某零件导向。这要求四个轴承运动轴线的平行度很高。而离心机由于体型较大,在不同温度和不同离心加速度情况下都会有比较明显的变形,从而破坏了轴承运动轴线的平行度。在工作中需要经常对轴承的位置进行微调,故轴承与离心机直接不能使用铰孔,只能用普通螺钉进行连接,从而留出调节余量,这就导致普通螺钉可能有受剪的风险。
图5所示为全密封静压轴承的外形图,底面有14个宽17 mm的马蹄槽,安装时,穿入14个M16的圆柱头内六角螺钉将轴承固定在基座上。底面的螺钉编号从1到14号。离心加速度的大小为100 g。
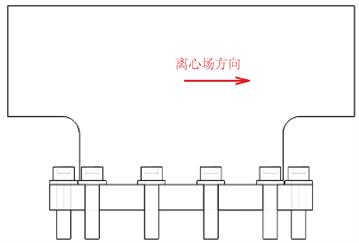
Figure 5. Curve: screw connection mode of fully sealed bearing
图5. 全密封轴承的螺接方式
在离心场下,轴承所受的离心力需要由底面摩擦力平衡。轴承被螺钉压紧在基座上,要求在离心场下轴承和基座不得有相对滑动。基于此,螺钉理论上仅受预紧力提供的拉力。
考虑到由于存在以下因素,给螺钉足够预紧力后,轴承仍可能发生滑动,导致螺钉受力:
1) 全密封轴承是精密的导向零件,对基座的平面度要求较高,精加工以后基座的粗糙度较小;
2) 安装调试轴承时,会在轴承底部垫铜箔,从而减小其摩擦系数。
因存在以上不确定因素,轴承的安装螺钉的选择要满足以下两个保证点:
1) 为满足轴承的正常使用条件,要求螺钉能提供足够预紧力,保证底面有足够摩擦力平衡轴承的离心力;
2) 为保证使用的安全性,要求一旦轴承发生侧滑,螺钉能承受由此引起的剪力,不会被剪断。
3.2. 螺钉预紧力计算
轴承被14个螺钉压紧在基座上,轴承的质量为45 kg,离心场下,产生Q = 45 kN的横向离心力。各螺栓预紧力P0需要至少为:
(11)
其中:
Q为轴承受到的离心力,大小为45 kN;
Kn为可靠性系数,这里取1.1;
m为摩擦面数量,这里为1;
z为螺钉数量,这里为14;
f为摩擦系数,这里取为0.15 [2]。
为保证安全,选择12.9级的螺钉,该型螺钉的保证载荷为452 kN。初始拧紧力达到所需的5倍,设定为:
(12)
3.3. 螺钉受力计算
假设轴承由于某些特殊情况,摩擦系数f下降到0.02,产生的摩擦力不足以克服离心力,产生了滑移,对螺钉产生横向力。
每个螺钉头下的摩擦力大小变为:
(13)
螺钉穿过的通孔直径为17 mm,螺钉上端直径为16 mm。考虑到打孔以及安装精度,各螺钉中心和孔中心会存在一个间距h,hmax = 0.5 mm;受到机械约束,螺钉帽与基座保持平行,其转角θ = 0。
根据公式(6),可计算得出该离心场下螺钉的轴向应力,见公式(14),位置在图1中的A点处:
(14)
在连接交界面上,螺钉存在剪力。对于该全密封轴承,由于每个螺钉与孔的初始中心距h是不同的,故h最大的两个螺钉将最先与孔接触,接触点受到最大的集中力F2。
(15)
根据公式(7),螺钉受到的剪应力为:
(16)
根据公式(8),螺钉在接触面受到的挤压应力:
(17)
其中M16的螺距P = 2。
画出接触点的应力状态,作出其对应的摩尔圆(见图6),根据公式(10),得到螺钉的最大正应力与最大切应力为:
说明螺钉满足受力条件,即便轴承发生滑动,系统仍是安全的。
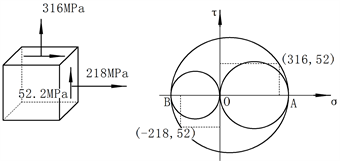
Figure 6. Curve: screw stress and Moore circle of maximum stress point
图6. 螺钉受力简图及最大受力点的摩尔圆
3.4. 有限元法验证
在一些复杂装配体的有限元仿真中,对于螺接关系的处理有时会直接用节点之间的耦合或者约束来代替,这样做通常不能够反映螺钉本身的受力特性。文献 [3] [4] 对螺钉的有限元建模及分析进行了研究,通过对螺钉及被连接件进行接触的定义、对螺钉施加预紧力等方式,可以得到较为准确的仿真结果。本文采用相似的方法,对静压轴承的螺钉进行有限元分析。模型的网格划分如图7所示,对螺钉、垫片以及底座连接面的网格划分较细,对非关注区域的网格划分较粗。
网格采用C3D8R (8节点六面体单元),共89,358个单元,该单元克服了在线性完全积分单元中的剪切与自锁问题,在单元扭曲比较小的情况下,得到的位移和应力结果更精确;同时在弯曲问题中,厚度方向只需要很少的单元,就可以得到与二次单元相当的结果,而计算成本可以明显降低。
3.4.1. 边界条件与载荷设置
共设置两个分析步:第一个分析步仅施加40,000 N的螺钉预紧力,第二个分析步给轴承施加100 g的离心加速度。
螺钉头与垫片、垫片与轴承底座表面设置接触边界,摩擦系数与上文一样设置为0.02。约束轴承底座在垂直方向的自由度,约束螺钉下部拧入基座部分的水平自由度,如图8所示。
垫片选用型号:钢结构用高强度垫圈 [5]。厚3 mm,其中
。
3.4.2. 仿真分析结果
仿真分析结果见图9:
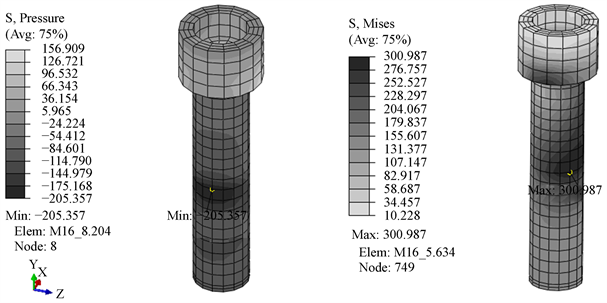
Figure 9. Surface pressure (left) and stress cloud map (right)
图9. 螺钉受到的表面压强(左)与螺钉应力云图(右)
将仿真分析计算结果与公式法计算结果进行比较,如表1所示:
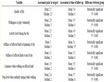
Table 1. Comparison of formula calculation results and finite element calculation results
表1. 公式法和有限元法计算结果对比
4. 结束语
1) 公式法和有限元法的计算结果差别很小,其中公式法得到的结果比有限元法的结果略大,在实际应用中则更加安全,证明了公式法的正确性。螺钉的最大应力点出现在连接交界面位置。
2) 螺钉受到横向载荷,最好使用铰制孔螺栓;但如果只能使用普通螺钉时,须考虑螺钉在非正常工作状态下不被破坏。这种情况可以采用文中给出的计算方法进行校核,以便设计人员进行选型。
3) 如果螺钉还受到交变载荷的作用下,需要额外进行疲劳校核。