1. 引言
航空发动机被称为飞机的心脏,是飞机的动力装置,同时航空发动机内部结构复杂,使用要求高,因而一直有“工业皇冠”的美誉,它的制造水平也是一个国家制造业发展水平的重要体现。现代航空发动机以燃气涡轮发动机为主,它的主要结构包括进气道、压气机、燃烧室、涡轮和尾喷管。其工作原理是:气流通过进气道进入发动机,在压气机进行压缩和减速,从而方便气体在燃烧室与雾化的燃料进行充分的燃烧,燃烧产生的高温高压气体推动涡轮做功,之后通过尾喷管喷出,通过与外界气体的相互作用力,为飞机提供推力 [1] [2] [3]。
因此,涡轮的主要作用便是将高温高压气体的能量转化为涡轮转动的机械能,进而为飞机提供所需要的能量,它的主要工作部件便是涡轮叶片。涡轮叶片的工作环境极其恶劣,它不仅要在较高的转速下运行,同时还要承受高温高压气体的冲击,相当于它同时工作在高温、高压、高转速的环境中。这样的工作环境导致对于涡轮叶片的制造要求非常严苛,目前国内在涡轮叶片制造方面与国际先进水平相比仍有很大的差距,这也成为国产发动机技术发展的一个重要瓶颈。
因此本文进行有关涡轮叶片在实际工作环境中应力分布的分析计算,得到涡轮叶片在实际工作中应力分布的数据信息。在现代民航客机的维护工作中,航空发动机的维护是非常重要的环节,航空发动机一旦在工作中出现故障,那么便会对飞行安全产生极大的威胁,比如民航客机在飞行中出现发动机空中停车的危急情况。而不管是航空发动机维护中的检查、保养还是修理工作,涡轮叶片都是这些工作要针对的重点对象,为了能够圆满的完成相关的工作,就需要我们能够清晰地认识和分析涡轮叶片内部的应力状况以及可能产生的损耗,进而根据这些情况制定出合理的维护方案,从而在保证飞行安全性的同时也满足有关经济性的要求。
2. 涡轮叶片的结构分析与建模
本文通过CATIA进行相关的建模过程,得到模型以及有关的几何参数,为下一步进行涡轮叶片的应力分析提供基础。
CATIA建模过程中,先建立单个涡轮叶片三维模型,包括为叶身、叶冠、叶根部分。建好的单个涡轮叶片如图1所示。
进行整体涡轮叶片的建模,先建立涡轮盘部分,再组装上图1的单个涡轮叶片模型,然后利用阵列命令得到整个涡轮叶片三维模型如图2所示。
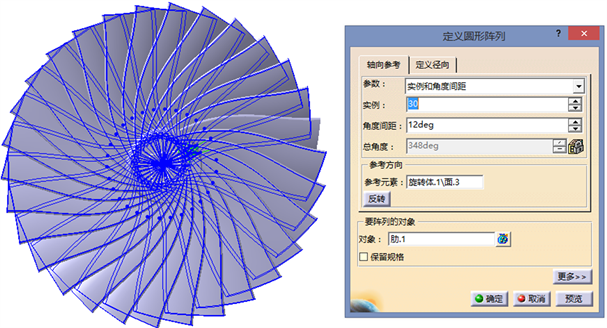
Figure 2. All turbine blades of integral turbine
图2. 整体涡轮的所有涡轮叶片
三维模型建好以后,根据CATIA提供的相关命令就可以得到其几何特性,比如体积,表面积,质量等等,也可以改变相应的参数,比如材料等得到不同的结果。
3. 涡轮叶片应力与疲劳分析仿真
本文采用ANSYS软件进行涡轮叶片的应力与疲劳分析仿真 [4] [5] [6]。
3.1. 单个涡轮叶片应力分析的仿真
进行单个涡轮叶片的应力分析主要包括以下步骤:将三维模型导入ANSYS软件;选用GH4033合金材料;进行划分网格操作,本文中单个涡轮叶片划分的网格中,节点数为3759,网格数为1895;确定涡轮叶片固定约束部分,选择叶根部分的几个面,即确定叶根部分是固定的;接着给涡轮叶片施加重力和离心力载荷,并确定环境温度;最后给涡轮叶片施加气体冲击力;根据之前施加的相关载荷,对单个涡轮叶片产生的变形、应力、应变情况进行分析。可添加涡轮叶片在载荷作用下的整体变形、正应力和正应变即可进行相关的分析,如图3所示。
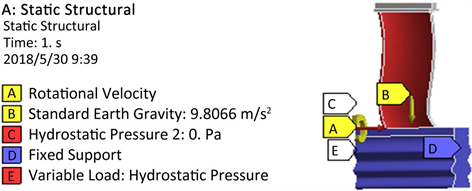
Figure 3. Total load of single turbine blade
图3. 单个涡轮叶片的载荷总况
单个涡轮叶片在上述载荷作用下的整体形变情况如图4所示。由整体变形的分析图可得到以下信息:① 叶根部分的变形几乎为0,虽然在之前的理论计算部分中,叶根部分承受的重力最大,但由于重力的作用效果并不大。而且叶根处属于固定部分,所以冲击力和离心力造成的力矩无法使其产生变形。② 叶身部分的整体变形则是基本随叶身高度的增加而不断增加的趋势,这说明随着旋转半径的增大,离心力造成的变形也越大,同时值得注意的是,涡轮叶片左侧面的气体冲击力是远大于涡轮叶片叶盆曲面和叶背曲面的,但在整体变形中却未体现出来,这说明气体冲击力大小是远小于离心力的,以至于无法在整体变形中显示出其作用效果。③ 叶冠部分的整体变形最大,达到了0.0023832,这主要是由于叶冠部分所受到的离心力最大,而且由于其尺寸较小,所以虽然不同高度上的离心力有差距,但产生的整体形变的差距并不大,所以在图上没有体现出来。
单个涡轮叶片在上述载荷作用时产生的正应力和正应变如图5所示。由正应力和正应变的分析图可以得到以下信息:① 与整体变形时不同,在涡轮叶片的正应力和正应变的分析图中可以发现,叶根部分的应力应变是比较大的,主要是由于在实际中叶身部分所受到气体冲击力和离心载力产生的力矩会加载在固定的叶根处,这也是为什么叶根与叶身接合处容易出现损伤的原因。② 就叶身部分而言,应力应变并未沿叶身高度而发生较大的变化,同时由于几何特性的区别,叶盆曲面和叶背曲面的应力分布存在较大的不同。③ 就叶冠部分而言,应力应变较为稳定,但应力在顶部的分布有一些不均匀。如图4所示。
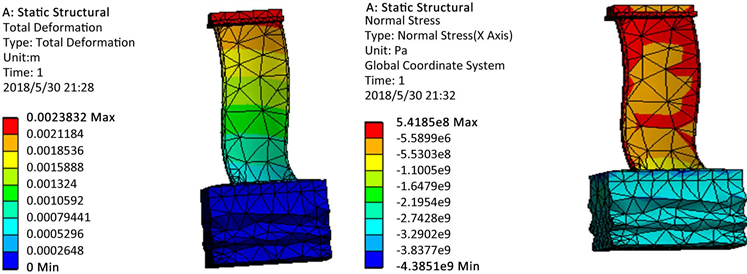
Figure 4. Deformation and stress distribution of single turbine blade
图4. 单个涡轮叶片的变形情况和应力分布情况
3.2. 整体涡轮应力分析的仿真
进行整体涡轮的应力分析,包括以下步骤:
1) 与单个涡轮叶片的分析相同,将三维模型导入ANSYS软件;选用GH4033合金材料;进行划分网格操作。
2) 进入分析界面之后,与分析单个涡轮叶片相比,施加的载荷有所不同。首先在分析整体涡轮时没有必要施加重力,同时在固定约束部分和气动载荷上也有不同。固定约束部分选择整体涡轮的装配孔部分。整体涡轮在工作时承受的也是两种大小不同的气体冲击力,所以也是添加两个流体压力选项。在第一个流体压力选项中选择流体密度为0.36 kgm−3,加速度则选为在x方向上存在,大小为1400 ms−2,但承受部位为涡轮盘的左侧面和叶身30个左侧面;在第二个流体压力选项中选择流体密度为0.36 kgm−3,加速度则同时在两个方向存在,x方向的加速为936 ms−2,y方向的加速度为664 ms−2,承受部位为30个涡轮叶片的内型面和外型面。整体涡轮承受的相关载荷如图5所示。
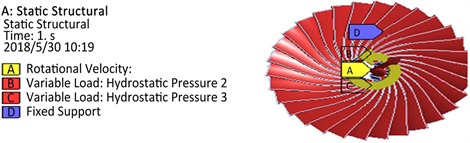
Figure 5. Total load condition of integral turbine
图5. 整体涡轮的载荷总况
3) 进行整体涡轮在上述载荷作用下的整体变形、正应力和正应变的分析。执行之前类似的操作,得到整体涡轮的变形和应力应变图。整体涡轮的变形情况、应力情况、应变情况等见图8。
4) 由整体涡轮的变形图,可以得到相关信息:① 很明显可以看出,整体涡轮的变形情况与其和旋转轴线的距离有关,这说明整体涡轮的变形主要是由离心载荷造成的,而与气体冲击力的关系并不密切。② 涡轮叶片承受气体冲击力部分和未承受气体冲击力部分的变形情况基本相同,且涡轮叶片的最大变形产生在叶尖附近,这主要是由于此处的离心力最大,最大变形为0.00012691。这与之前有关的理论计算是吻合的。③ 在涡轮盘装配孔处,由于需要与轴进行装配,因而此处属于固定部分。即便此处可能存在较大应力,变形量也是最小的。
5) 由整体涡轮的应力和应变分析中,可得到以下结论:① 就涡轮盘而言,应力最大的部分位于装配孔附近。主要是由于在整体涡轮中,装配孔部分是处于固定的,因而无论是离心力所带来的偏心力矩,还是气体冲击力所施加的力矩,都主要由装配孔附近的部分来承担,所以此处的应力最大,最大值为279 MPa。② 就涡轮叶片而言,应力最大的部分位于叶根处。这主要是由于涡轮叶片形状是不规则的,因而在其旋转时,离心力部分会和轴线有偏差,从而产生力矩,其应力值大概为62 MPa。
4. 涡轮疲劳分析的仿真
在实际工作中,整体涡轮除了承受较大的载荷之外,还会受到疲劳损伤的困扰。因此,为了更好的了解涡轮叶片的工作环境,需要对整体涡轮进行相关的疲劳分析。
进行疲劳分析仍然利用ANSYS来完成。首先就是要定义材料的疲劳性能,常用S-N曲线来表达材料疲劳性能。在ANSYS中,通过编辑材料属性来实现将S-N曲线导入到ANSYS中,从而方便进行下一步的分析。有关材料的疲劳性能如图6所示。
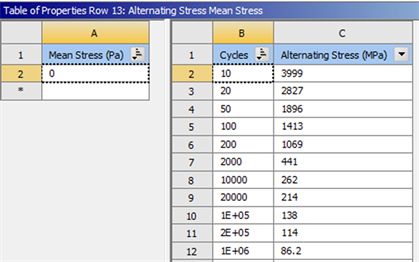
Figure 6. GH4033 material fatigue properties
图6. GH4033材料疲劳性能
定义完材料的疲劳性能之后,然后便要进行整体涡轮盘的疲劳分析。通过在整体涡轮应力的工作界面处添加疲劳工具来进行,在下方的面板中定义疲劳的详细情况。加载方式采用“Zero-Based”,即在加载周期内最小应力为0。平均应力采用Gerber模型,其他则采用默认设置。如图7所示。
最后进行疲劳分析,需要分析的内容为在疲劳状况工作下整体涡轮的交变应力。在疲劳工具中添加相关分析项目后进行分析。分析结果见图8所示。根据交变应力分析图可知,整体涡轮交变应力较大的部分主要分布在涡轮盘附近。其中涡轮叶片的最大的交变应力位于其叶根附近,其大小为27.966 MPa。而涡轮盘最大的交变应力位于装配孔附近,其大小为125.82 MPa。
5. 总结
在进行涡轮叶片的结构与应力分析之后,可以得出以下结论:① 涡轮叶片在实际工作环境中的变形主要是由离心力造成的,因此,涡轮的转速对涡轮叶片的使用性能具有非常大的影响。② 在涡轮叶片工作时,由于其固定端承担很大的力矩,所以固定端部分的应力最大。③ 综合分析实际环境对涡轮叶片的影响之后,可知涡轮叶片的叶根和叶尖部分最易发生失效,在实际维护工作中需要特别注意。
本文的分析局限性主要体现在以下几个方面:① 在进行涡轮叶片的建模时,缺乏较为准确的数据信息,因此在一些方面只能进行合理的推测,从而导致模型与实际涡轮叶片有一定的差距。② 在进行涡轮
(a) 变形(b) 应力分布
(c) 应变 (d) 交变应力
Figure 8. Fatigue analysis results
图8. 疲劳分析结果
叶片应力分布的理论计算时,对涡轮叶片不规则的形状进行了一定的理想化处理,造成了计算结果和实际情况有偏差。③ 在进行涡轮叶片应力分析的仿真时,由于缺乏热耦合相关的知识,未对涡轮叶片中存在的热应力进行分析,而热应力对分析的结果具有一定的影响。
总之,本文对某型发动机涡轮叶片的结构与应力分析进行仿真,对机务维护人员掌握发动机涡轮叶片的工作原理及失效过程提供帮助,具有一定指导意义。
基金项目
2019年中央高校教育教学改革专项资金项目:教学质量国家标准背景下飞行器制造工程专业建设(E2019016);四川省教育厅重点项目:基于方法融合的通航飞机机电设备故障预测技术研究(16ZA0020)。