1. 引言
随着环境污染与传统能源的日益匮乏,纯电动汽车的开发与使用已经得到了所有人的重视,纯电动汽车具有排放污染低,能源转化率高等优点。以往纯电动汽车的性能试验往往是在测试道路或台架上进行的,但是随着动力系统的匹配方案和相关部件参数的变化,若都要进行测试,十分耗费精力。故开发早期阶段,合理的动力系统参数匹配以及软件建模与仿真对于电动汽车的动力性能具有至关重要的作用,同时可以极大地缩短汽车的开发周期,降低研发成本。建立符合国家相关标准条件规定的整车模型,又能为纯电动汽车企业试车研究提供理论依据,通过模型的模块运算,直观获取对动力性及经济性评价过程参数,对车辆性能进行范围和性能测试评估。
2. 动力参数的设计匹配
2.1. 整车基本参数与性能指标确定
建立整车模型前,必须先确定车辆的基本参数,包括车辆质量,滚动系数,车轮尺寸,齿轮传动比,机械传动效率等。选用某款纯电动车的整车基本参数,如表1所示 [1] [2] [3]。
该车的性能指标如表2所示。
2.2. 整车动力系统的基本模型(物理模型)
动力传动系统是纯电动汽车的动力源,其性能决定了整车的综合性能。整车动力系统主要包括电机、电池、变速器、主减速器、差速器、车轮等部件,如图1所示。
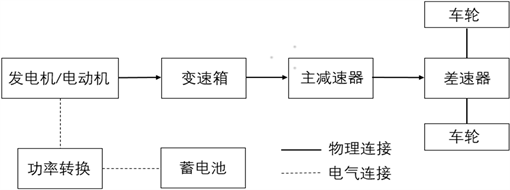
Figure 1. Vehicle power system model of pure electric vehicle
图1. 纯电动汽车整车动力系统模型
2.3. 动力参数的匹配与选型
动力参数主要包括对电动机和电池组参数匹配设计及选型。电动机参数匹配设计及选型应考虑电动机的转速、效率、质量尺寸、成本等因素,本文中选用永磁同步电机。设计电池组参数时,除了满足上述要求,还应综合考虑汽车行驶的实际情况,本文选用锂电池。通过综合分析计算,动力参数最终匹配结果如表3所示。
1) 通过范围测试近似电池容量:
在WLTP周期上进行仿真可以大致估算一个周期上的能耗,评估范围是从充电状态(95%)开始到充电状态(20%)结束,因此估算所需的电池能量如(1)所示。
(1)
式中:电池容量
,单周期能耗
,需求距离
,单周期距离
,最大剩余电量
,最小剩余电量
。
2) 从最大车速估算最大电动机转速:
(2)
式中:车辆最大速度
,齿轮比
和车轮半径
。
电机的基本速度定义为电机最大速度的一半,这是永磁电机的典型值。
(3)
式中:电机基本速度
,电机最大速度
。
3) 近似电动机转矩和功率要求:
以最大允许载荷开始倾斜,(4)式表示以所需的斜率开始的电动机转矩计算。
(4)
式中:电动机最大转矩
,最大允许车辆质量
,重力常数g,倾斜角
,库仑摩擦系数f和静摩擦系数
。
加速测试:
从零速开始加速所需的最大电动机功率可通过式(5)估算,式(5)可以分为三个部分:
惯性部分:它表示加速而无任何损失所需的功率。
滚动部分:它表示在加速过程中由于滚动摩擦而损失的平均功率。
空气动力学部分:它表示由于空气动力学阻力而在加速过程中损失的平均功率。
(5)
式中:车辆整备质量
,一个车轮的惯性
,测试的最大所需车辆速度
,与基本速度旋转的电动机相对应的车辆速度
,空气密度
,空气阻力系数
和车辆前部区域A。
该公式用作评估三个加速测试的动力需求的基础,给出了最大电动机功率,由此可以计算出相应的最大电动机转矩。
4) 通过仿真调整迭代大小:
通过使用Simcenter Amesim中的实验功能加载电机和电池尺寸,调整不同状态,进行迭代来确定电动机和电池的大小。
电机和电池尺寸过小的初始状态可以使用实验来加载。先确定电池的尺寸,因为它会影响车辆的质量。将电动机参数设置为确保车辆正确遵循WLTP周期的值。然后,反复更改电池能量,直到达到所需范围。
然后根据选定的电池参数开始进行电机选型。然后,反复更改电动机的最大转矩,功率和速度,直到满足速度和加速度要求为止。公式(3)和(4)给出了电动机参数的良好的第一近似值 [4] [5] [6] [7]。
电池和达到目标的电机的最终参数设置如下:
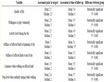
Table 3. Dynamic parameter matching results
表3. 动力参数匹配结果
3. 模型建立与仿真分析
3.1. 整车动力性能仿真模型建立
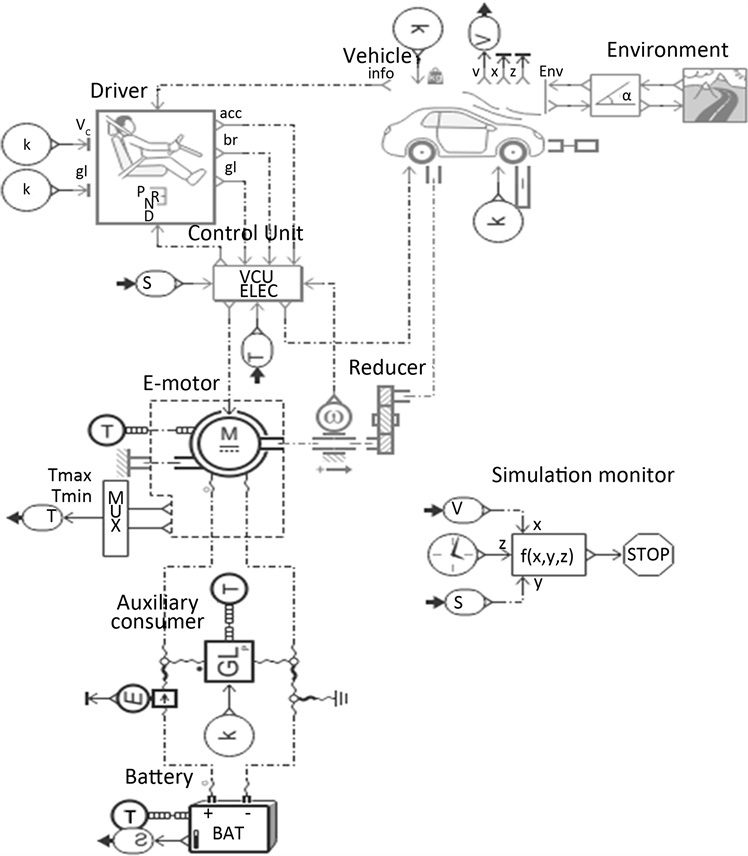
Figure 2. Simulation model of vehicle dynamic performance
图2. 整车动力性能仿真模型
使用Simcenter Amesim搭建的电动整车模型如图2所示。它由纵向车辆模型,驾驶员模型,传动模型,准静态电动机模型和准静态电池模型组成。
通过输入各部件基本尺寸参数和动力参数,经过模块运算,即可对车辆在定义驾驶工况下的动力性及经济性进行仿真分析,对车辆性能进行范围和性能测试评估 [8] [9]。
3.2. 仿真测试工况选择
NEDC标准由四个重复“城市道路循环”以及一个“市郊道路循环”组成。一套完整的测试循环总共持续1180秒,累计行驶里程11.04公里。测试当中车辆的最高时速达到120公里/小时,平均速度约为34公里/小时。
WLTP标准根据功率质量比(简称PWR)将车辆划分为三级,并对应设计了三种测试循环(而NEDC只有一种),考虑了四种道路类型:低速、中速、高速、额外高速等(而NEDC只有两种) [10] [11]。
对比NEDC标准而言,WLTP标准中的车辆最高速度、平均速度、最大加减速度以及加减速度幅度、测试行驶时间等都有了较大提升,整体难度提升不少,更符合实际驾驶工况,故我们这里采用WLTC工况。
3.3. 仿真结果分析

Figure 3. WLTC operating speed simulation results
图3. WLTC工况车速仿真结果
根据图3,我们直观的看到在WLTC工况下车速的仿真结果,仿真车速与工况循环速度随时间变化紧紧跟随,吻合程度极高,说明仿真车辆的动力性能可以满足设计要求,同时也保证了建立模型的合理性。
从图4我们可以看出,仿真车速与工况循环速度的差值始终保持在WLTC工况的最大正负容限内,说明仿真车辆能够正确遵循WLTC工况要求。
图5为该纯电动汽车在一个WLTC工况下电量消耗SOC的变化情况,可以看出SOC曲线整体上呈平缓下降趋势,在部分节点处呈小幅上升,未发生激变现象。
表4为在WLTC工况下对该车辆动力性和经济性的仿真结果与性能指标参数进行对比。
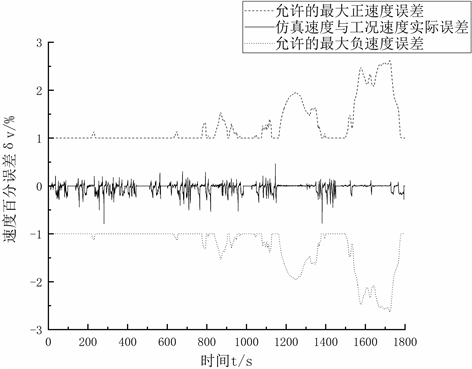
Figure 4. The error between the simulated vehicle speed and working condition cycle speed
图4. 仿真车速与工况循环车速之间的误差
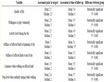
Table 4. Simulation comparison of automobile dynamic performance and economy index
表4. 汽车动力性、经济性指标的仿真对比
通过表4对比该车辆动力性和经济性的仿真结果与性能指标,我们可以看到每项仿真结果都优于性能指标设计参数。百公里加速时间和最大爬坡度满足设计目标,说明电机扭矩匹配合理。最高车速满足设计目标,说明电机功率及传动系统匹配合理。
综上所述,电池和电机匹配均较为合理,整车满足行驶工况要求 [12] [13]。
4. 动力性试验
4.1. 试验方案
采用的仪器为非接触式五轮仪,如图5所示。该仪器包括电源,显示器,光电传感器,信号处理器等部件,在试验车辆的运行过程中,安装在车上的光电路面探测器照射路面,采集路面图像转换成频率信号,频率信号通过信号处理器转换成速度变化,从而对汽车的动力性进行试验。
4.1.1. 最高车速试验
将试验车辆加载到试验质量,增加的载荷应合理分布。按规定对车辆进行准备。在直线跑道或环形跑道上将试验车辆加速,使电动汽车在驶入测量区之前能够达到最高稳定车速,并且保持这个车速持续行驶1 km (测量的长度)。记录车辆持续行驶1 km的时间t1,然后做一次反方向的试验,并记录通过的时间t2。
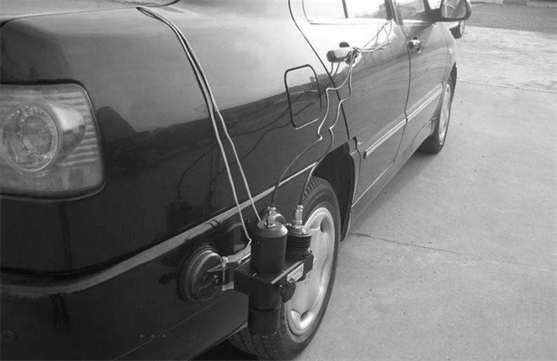
Figure 5. The test vehicle is connected to the five-wheeled instrument
图5. 试验车辆与五轮仪连接
按下式计算试验结果:
(6)
式中,V为实际最高车速,km/h; 为持续行驶1 km两次试验所测时间的算术平均值(t1 + t2)/2 s。
4.1.2. 0~50 km/h加速性能试验
将试验车辆加载到试验质量,增加的载荷应合理分布;将试验车辆停放在试验道路的起始位置,并起动车辆;将加速踏板快速踩到底,使车辆加速到(50 ± 1) km/h;如果装有离合器和变速器,将变速器置入该车的起步档位,迅速起步,将加速踏板快速踩到底,换入适当档位,使车辆加速到(50 ± 1) km/h;记录从踩下加速踏板到车速达到(50 ± 1) km/h的时间;然后以相反方向行驶,再做一次试验。
0~50 km/h加速性能是两次测得时间的算术平均值。
4.2. 试验结果
试验的环境温度为25℃,电动汽车蓄电池达到完全充电状态,相对湿度为60%,风速与试验道路平行方向的风速分量不能超过2 m/s,大气压力为101 kPa。整车空载质量为1598 kg,根据标准将车辆加载到试验质量,半载附加质量为150 kg,增加的载荷均匀分布在乘客座椅上。
最高车速试验结果如表5所示,0~50 km/h加速性能试验结果如表6所示,结果对比如表7所示。
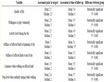
Table 5. Maximum speed test results
表5. 最高车速试验结果
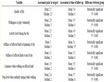
Table 6. 0~50 km/h acceleration performance test result
表6. 0~50 km/h加速性能试验结果
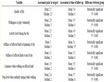
Table 7. Dynamic design index, simulation value and test value comparison
表7. 动力性设计参数,仿真值与测试值的比较
通过分析试验数据,我们得到该车最高车速为127.75 km/h,0~50 km/h的时间为3.1 s,均满足设计要求,且与仿真结果接近,验证了动力参数匹配的正确性与仿真模型的合理性。
5. 模型延伸
随着电动汽车的不断发展普及,电动汽车能量管理系统的设计与开发显得尤为重要,而电动汽车能量管理主要包括动力系统和热管理系统两大部分。
本文对纯电动汽车的动力传动系统进行建模仿真分析,通过输入整车部件相关参数,分析了在某一给定工况下的整车动力性和经济性分析,包括百公里加速时间、最大速度、续驶里程等,并通过实车试验验证了模型的合理性。
整车热管理模型主要实现对电池冷却系统和电机的温度控制,而已建立的整车动力模型可以为整车热管理模型提供热源边界条件,包括电池发热量、电机发热量。通过集成整车动力模型和热管理模型,可以构建整车能量管理仿真分析模型。使用后处理工具,可以直观而高效的分析整车动力传递、能量传递及能量回收情况,计算对象指标用于驾驶性能评价 [14]。
6. 结语
本文根据整车性能指标要求,对电机和电池等动力系统关键部件进行匹配计算,利用Amesim仿真软件,搭建了纯电动汽车整车动力仿真模型,通过输入整车各部件相关参数,验证了该车的动力性(最高车速、爬坡度、加速时间)、经济性(续驶里程),满足设计要求,并通过实车试验,验证了参数匹配与模型的合理性。同时模型还可以进行延伸应用,为后续整车能量管理系统模型的构建提供基础,为实现整车系统优化控制和整车能耗分析提供支持和参考。本文研究内容为纯电动汽车初期各系统间的匹配设计提供了一种有效的参考方法,对车辆性能进行范围和性能测试评估,显著地降低设计成本、缩短开发周期,为纯电动汽车企业试车研究提供理论依据。
基金项目
国家自然科学基金重点项目,51736007;上海理工大学科技发展项目,2018KJFZ179。