1. 引言
随着现代工业的迅速发展,在石油的开采、储存与运输过程中,由于操作不当等原因,漏油事故频发,海洋浮油污染越来越严重,油水分离已经成为举世关注的问题。一方面,原油泄漏带来的大面积水域污染,严重影响到全球生态系统的健康;另一方面,生产生活中油水混合物的肆意排放也威胁到了内陆水系的清洁和安全 [1] [2] [3]。因此,如何进行简单高效、操作方便、利用率高的油水分离成为近些年研究的重点。
工业中常用的油水分离方法主要有重力式分离、离心式分离、电分离、吸附分离、气浮分离、凝聚和絮凝等方法,但这些方法通常成本较高,分离效率低,不能够反复利用,甚至会造成二次污染,不适用于大规模海洋浮油的清理,其应用往往大幅度受限 [4] [5] [6] [7]。因此,如何选择一种清洁、高效又能够大规模重复利用的油水分离方法成为研究的重点。近年来,仿生学的迅速发展引发了对界面材料的研究热潮。通过对荷叶表面超疏水现象的研究,发现表面的微纳复合形貌和低表面能的化学组成是其超疏水的原因。受此启发,科研人员致力于超疏水材料的仿生制备,并且成功应用于油水分离领域 [8] [9] [10] [11] [12]。此外,金属网状材料因为机械强度高、表面易加工处理,在分离和收集含油废水实践中得到广泛的应用。
研究以铜网材料为基体,通过化学镀的方法,在铜网表面沉积纳米银层;经正十八硫醇修饰后,铜网材料浸润性发生变化,制备出超疏水亲油的网状材料。选择不同表面张力的油性介质(正己烷、石油醚)与不同含盐量的水样(去离子水、10%盐水、15%盐水)配制成油水混合液,进行油水分离测试,测量并计算不同表面张力油水混合物的分离效率,并分析讨论微观结构和表面组成调控对浸润性及油水分离效率的影响。
2. 实验过程
2.1. 实验材料
实验所使用的材料和化学试剂如表1所示:
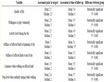
Table 1. Reagents and their materials involved in the work
表1. 实验所使用的材料和化学试剂
2.2. 实验步骤
1) 配置0.15 M的硝酸银乙醇溶液,将清洗后的铜网放置进硝酸银乙醇溶液中浸泡时间为20 s。取出,去离子水清洗表面后吹干待用。
2) 配置0.01 M的十八硫醇的乙醇溶液,将化学镀后的铜网放入1~2 h,取出清洗后60℃下干燥即可得到超疏水亲油的铜网材料。
3) 分别以正己烷、石油醚为油样,以去离子水、10%盐水、15%盐水为水样(水样经亚甲基蓝染色)制备油水混合物。利用制备的超疏水亲油铜网作为分离装置进行油水混合物,并记录分离效率。
2.3. 实验仪器
采用JSM-6701F型场发射扫描电子显微镜表征表面微观结构,适用光电子能谱(XPS):VG ESCALAB 210,英国VG Scitntific公司;使用Smart APEX II型X射线衍射仪对表面成分进行分析;采用DSA100接触角测量仪测定表面接触角,测试液体体积5 μL,五点测量取平均值。
3. 结果与分析
3.1. 铜网浸润性分析
疏水化处理完成后,铜网表面由原先的金黄色改变为黑色如图1所示,这是由于表面化学沉积的纳米银层所导致。沉积的纳米银层较薄,对铜网孔径影响不大。测量表面接触角列于表2,从结果可以看出,处理前,铜网表面接触角在70˚~91˚间,并随着铜网孔径降低增大,这是由于铜网本身由于网孔造成的毛细管力使得与水的接触角较大。经疏水化处理,铜网表面接触角增大,铜网孔径380 μm时最大为167˚,表面呈现超疏水状态。
图2是孔径380 μm超疏水铜网试样的FESEM照片,如图2(a),图2(b)所示,铜网处理前,表面光滑,粗糙度较低。疏水化处理后,被还原的银颗粒附着于铜网表面形成团簇凸起,导致表面粗糙度增加;将处理后的样品放大6000倍后,可见纳米银粒子的排列形成类珊瑚状的枝晶,在枝晶间形成较大孔隙,如图2(c);继续放大至11,000后,可看到类珊瑚状枝晶是由无数几百个纳米的小颗粒组成的,枝晶间存在大量微米级的孔隙,如图2(d)。化学镀后,铜表面的微米孔洞和纳米银颗粒构建出微纳相间的复合结构,这是铜网表面超疏水化的结构因素。
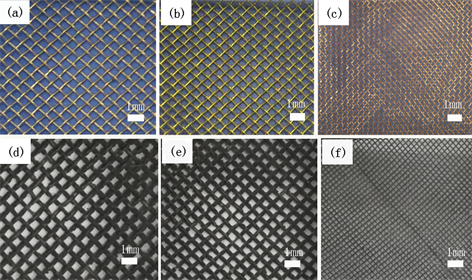
Figure 1. The photo of copper mesh before (a) 1180 μm, (b) 830 μm, (c) 380 μm and after superhydrophobic treatment with different mesh size (d) 1180 μm, (e) 830 μm, (f) 380 μm
图1. 铜网疏水化处理前后照片。处理前(a) 1180 μm,(b) 830 μm,(c) 380 μm处理后:(d) 1180 μm,(e) 830 μm,(f) 380 μm
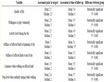
Table 2. The contact angle of copper mesh before after superhydrophobic treatment with different mesh size
表2. 疏水化处理前后不同孔径铜网表面接触角
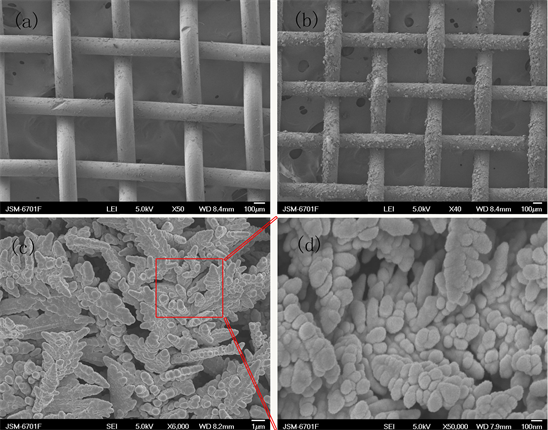
Figure 2. FESEM of the surface of superhydrophobic copper mesh (380 μm), (a) original mesh, (b) superhydrophobic mesh, (c) surface structures (d) larger view of c
图2. 超疏水铜网(380 μm)表面的FESEM电镜照片,(a) 原始铜网,(b) 超疏水铜网,(c) 表面形貌,(d) 表面形貌高倍照片
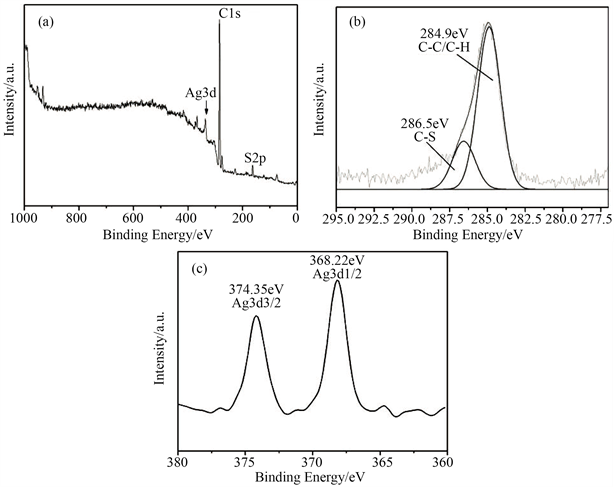
Figure 3. XPS spectra of the surface of superhydrophobic copper mesh, (a) survey scan, (b) C 1 s, (c) Ag3/2p
图3. 超疏水铜网表面的XPS图谱,(a) 全谱,(b) 碳分谱,(c) 银分谱
为了对铜网表面进行化学成分的分析,图3给出了超疏水亲油铜网表面的XPS图谱。从图3(a)全谱中可以明显看到银、碳和硫元素的三个峰。图3(b)、图3(c)分别给出了碳和银的分谱。通过吉布斯拟合,碳元素可拟合为两种:碳碳/碳氢键(C-C/C-H)和碳硫键(C-S)。在368.1 eV和374.1 eV处的两个峰对应于Ag3d3/2和Ag3d1/2,由于在金、银等金属元素(软酸)与巯基硫元素(软碱)之间会遵循软硬酸碱理论 [13] 形成稳定的Au-S和Ag-S键,从成分分析可知铜网表面化学沉积的银粒子与硫醇中的硫优先形成稳定的Ag-S共价键 [13] [14]。既可在银纳米粒子表面通过形成化学键包覆一层硫醇分子,起到降低表面能,达到表面超疏水化的目的。
3.2. 油水分离效率
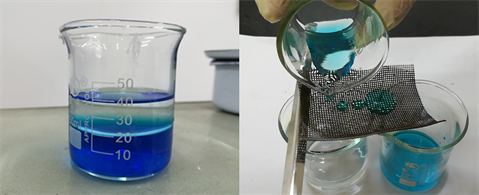
Figure 4. The schematic diagram of Oil-water separation
图4. 油水分离示意图
将正己烷和石油醚分别和水性介质(采用亚甲基蓝染色)混合后,利用超疏水亲油的铜网进行分离,如图4所示。油水分离测试过程中,分别记录分离前水性介质质量m1和分离后水性介质质量m2。采用下列公式计算油水分离效率:
未处理铜网由于表面亲油亲水,油水混合物会通过铜网孔洞流入烧杯,无法进行有效分离,即使孔径380 μm的铜网接触角可达到91˚,但是由于水珠会黏附在铜网表面,之后随水量增加在重力作用下仍会穿过铜网和油性介质混合,没有油水分离能力,认定分离效率为0。
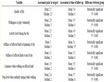
Table 3. The density and surface tension of different liquids
表3. 不同种类液体的密度和表面张力
表3中是几种液体的密度和表面张力 [15],三种水样的表面张力和密度都要比正己烷和石油醚大许多,因此,油水分离时,表面张力低的油性介质石油醚和正己烷在铜网表面迅速润湿铺展并透过,而表面张力大的水性介质在铜网表面呈球状滚落,从而实现油水分离。图5中黑色曲线表示铜网对油性介质/水的分离效率。对正己烷和石油醚这两类油性介质,分离效率分别为97%和98%。实验结果证明,所制得的超疏水亲油铜网可以将表面能有差异的油水混合物进行有效分离,在处理水面浮油污染方面具有较大的应用前景。
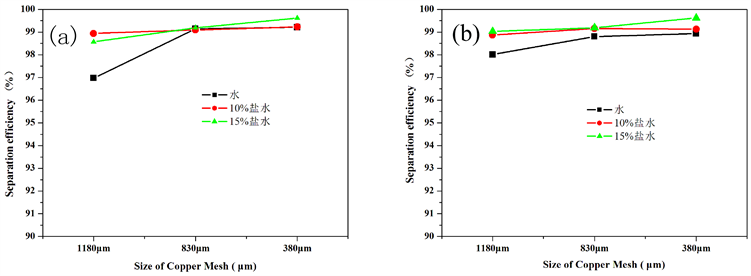
Figure 5. The separation efficiency of superhydrophobic copper mesh with different size in (a) n-hexane/water solution, (b) petroleum ether/water solution
图5. 不同孔径超疏水亲油铜网分离效率(a) 环己烷/水性介质体系 (b) 石油醚/水性介质体系
为了考察实际环境水质中油水分离效果,我们配置不同浓度氯化钠盐水溶液,考察盐度变化对油水分离效率的影响。从图5中可以看出,随含盐量增加,分离效率逐渐增加,所有铜网对油水混合物的分离效率都在96%以上。并且随着铜网孔径降低,铜网表面与水的接触角变大,表面对水的排斥和对油吸附效果差异越大,从而使分离效率提高。同时,我们也发现,含盐量不同的油水混合物分离效率相差不大,两种油性液体与不同水样的最大分离效率分别为99.44% (正己烷与15%盐水混合液)、99.62% (石油醚与15%盐水混合液),表明水中含盐量对本实验所制得的铜网的分离效率影响不大,这也说明采用化学镀方法制备的油水分离铜网材料对海洋浮油的处理具有较强的适应性。
油水分离实验后,铜网经过清洗,表面接触角经测量仍能保持与实验前差别不大,结果如表4所示。表明油水分离过程对超疏水铜网表面浸润性没有影响,铜网可重复循环利用进行油水分离。
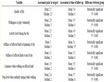
Table 4. The contact angle of copper mesh before after oil-water separation
表4. 油水分离前后不同孔径铜网表面接触角
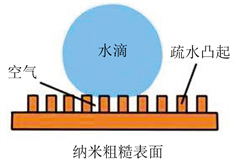
Figure 6. The schematic diagram of superhydrophobic state
图6. 超疏水状态示意图
分析原因,化学镀后铜网表面的粗糙度增加,形成了微纳相间的复合阶层结构;经十八硫醇化学修饰后,铜网从亲水状态变为超疏水状态,水性介质在铜网表面的浸润性得到逆转。如图6所示,当水接触到铜网表面时,由于表面微纳复合结构的存在,大量空气储存在这些微小的凹凸之间,相当于在液体水和铜网之间形成了一层极薄的空气层,此时,水和铜网接触的表面由固–液接触变为固–气接触,固–气–液三相接触线变得不连续,气液接触界面扩大,使液滴保持球状不自动铺展,接触角随之增大,就达到了超疏水状态,阻碍了水在铜网表面铺展穿过。而对于表面张力小的油性介质(环己烷、石油醚等),表面呈现亲油性。当油性介质接触到铜网表面时,迅速润湿铺展并透过铜网孔洞,从而实现油水分离。
4. 结论
本文选用14目、20目、40目三种规格的铜网作为研究材料,通过简单方便的化学镀的方法,实现了铜网表面超疏水并进行油水分离效率研究。研究结论如下:
1) 化学镀后的铜网具有超疏水的特性,其中疏水接触角最大可达到167˚,且重复多次油水分离实验后,仍然能保持良好的超疏水特性。
2) 随着铜网孔径的减小,油水混合物分离效率逐渐增加,最高可达到99.62%。
3) 含盐量对超疏水亲油铜网的分离效率影响不大,铜网可适用于海洋环境浮油的清理分离。
基金项目
本研究由河南省高等学校重点科研项目(18A430019)资助。
NOTES
*通讯作者。