1. 背景
毋庸置疑,无论国内外煤炭都是一种极为重要的能源,而我国又是多煤少油的国家,占据着已经探明煤炭能源储存的15%,而我国的石油、天然气、储备仅仅占有2.7%和0.9%,因此这就注定了我国是煤炭使用大国。
因为煤炭的储量丰富、价格便宜,上至企业化工材料、下至农村取暖使用的都是煤炭。但煤化工产生的污水极难处理,其中所含较多复杂的有机物,这就限制了煤化工行业的进一步发展。“十四五”规划指出将继续保持“创新、协调、绿色、开放、共享”的发展理念,“十四五”规划我国石化和化工行业进入高质量发展阶段,要以“去产能、补短板”为核心,以“调结构、促升级”为主线,大力实施创新驱动和绿色持续发展战略,积极培育战略新型产业,按照“重质轻量”的原则,着力提升产业的国际竞争力和可持续发展 [1]。
煤化工是以煤炭为原料生产其他化学产品,例如煤制醇、煤制油、煤制烯烃等等,在生产过程中会产生大量的污水,这些污水普遍含有大量的酚类、氰化物、苯等有毒有害物质、具有极高的CODcr、色度、氨氮且极难处理 [2],煤化工废水的处理是一个极大的难题。
2. 不同工艺产生的废水(图1)
2.1. 煤焦化产生的废水
煤焦化废水的来源:炼焦、净化过程、产品精制,主要来源于蒸氨过程中产生的氨水,剩余氨水主要由装炉煤表面的湿存水、装炉煤产生的化合水、吸煤气管道和集气管循环氧水泵内的含油废水。
特点:有毒有害、焦油含量大、氨氮的浓度较高、生物处理此废水具有很大的难度。所含污染物有酚类、多环芳香族化合物、氟、吡啶、联苯等等,因为其组成负责处理难度较大。
2.2. 煤气化产生的废水
煤气化就是将固态的煤在高温下转化成小分子气体。在煤气洗涤、冷凝、分馏的过程中,煤气化产物以及副产物溶于水,就形成了难处理的煤气化废水。在气化的过程中,煤炭中含有的氨、硫、氯、金属部分转化为氨氮、氰化物、金属化合物,这些污染物大部分溶解于气化过程中的洗涤水、洗气水、蒸汽分流后的分离水和储罐排水中以及一部分设备管道清扫过程中放空等,处理起来极为困难。
2.3. 煤制油产生的废水
煤制油时分为直接液化和间接液化两种。直接液化就是在高温下将煤浆加氢裂解成液态烃的过程,最早是由德国引进。而间接液化则是将煤的产物作为原料进行生产。
特点:煤制油废水乳化程度高、色度大、含有大量的氨氮、氰化物、苯系物、硫的杂环类有毒物质,成分复杂处理难度大。
2.4. 煤化工废水的处理
煤化工处理一般分为三部,分别为预处理、生物处理、深度处理。这三部分包含许多的处理方式,不同的厂区采用不同的处理方式。
3. 预处理
首先煤化工废水的预处理时必须存在的,煤化工废水中含有的油脂、酚、氨、有毒有机物存在生物毒性,不进行预处理会严重影响后面的生物处理。
3.1. 隔油法和气浮法
煤化工废水中的油类物质可以粘附在菌胶团的表面,严重的影响后面生物处理。生物进行废水处理时废水中的含油量一般要求小于50 mg/L,最好可以控制低于20 mg/在,减小后续处理压力。Zhang等 [3] 在毒性机制基础上建立了煤化工特征难降解有机物的生物毒性评估,认为含氮杂环及酚类化合物的积累性毒性严重抑制了生化系统的微生物活性。
隔油法:隔油法利用的是油和水的密度差异性,通过自然沉淀或者上浮达到分离的目的,轻油浮于水面由刮油设计送至储油罐;重油则下沉至池底由排泥管定期排出。
气浮法:气浮法分类较多,常用的有:加压气浮法、曝气气浮法、电解气浮法等等,气浮法是依靠表面张力作用吸附分散在水中的小油滴,气泡的浮力不断地增大上浮从而达到分离的目的。主要去除的是水中的油类物质和悬浮物。但是使用该方法对COD的去除效果较差,因此常使用气浮法和其他方法混用,保证更好的处理效果 [4]。
3.2. 脱酚
脱酚的方法又可以分为吸附脱酚、萃取脱酚、水蒸气脱酚。
吸附脱酚是利用比面积较大的材料产生的表面张力进行去除,当吸附材料饱和无法再吸附时,可以使用有机溶剂,蒸汽对吸附剂解脱再生,重复利用 [5]。常用的吸附剂有改性膨润土、活性炭、吸附树脂等。
萃取脱酚利用酚在煤化工废水中和萃取剂中的溶解度不同达到脱酚效果,影响萃取脱酚的主要因素为萃取剂的种类和萃取工艺参数。对于萃取剂的要求:不易乳化、效率高、油水易分离、不会造成二次污染等特点。
水蒸气脱酚即通过蒸汽带走废水中挥发的酚,此法常用于挥发性酚占比较大的废水处理中。水蒸气脱酚流程简单、处理成本低,但去除不了不会发性酚,因此实际运行中仍然以萃取法为主,但可以结合实际适当运用水蒸气脱酚法。
3.3. 脱氮
煤化工废水中的氨,主要以高浓度的氨氮以及微量氰化物的形式存在,脱氮主要使用的是蒸汽法,在碱性环境下,氨氮以游离的形式存在,因此为了有效地降低煤化工废水中的氨氮,可以通过高温水蒸气的吹脱后,再通过蒸馏或者分离等多种方式处理后,煤化工废水还可以达到回收再次利用的效果 [6]。
4. 生物处理
4.1. 活性污泥法
煤化工废水中存在的高浓度氨氮、氰化物等有机物会危害污泥中的微生物,以至于去除效果相对来说较差,通过一系列改进:提高生物耐毒性、提高溶解氧等,虽然这样会得到一些改善,但氨氮的去除较低还是需要其他工艺配合使用。
4.2. 生物脱氮
生物脱氮法可以去除大部分的CODcr、BOD以及氨氮。生物处理就是在污泥之中接入生物,通过生物的新陈代谢可以将废水中的污染物进行分解去除,生物处理是废水处理的核心,也是煤化工废水进一步处理的必要过程,可以在很大的成度上降低有机物的浓度。生物处理就是硝化反应和反硝化反应相结合。
具体硝化反应和反硝化反应如下
首先由亚硝酸菌将氨氮(
和
)转化成亚硝酸盐(
):
然后再由硝酸菌将亚硝酸盐(
)氧化成硝酸盐(
):
反硝化则是异养兼性厌氧菌将硝态氮转化成氮气:
4.3. A2O工艺
A2O是国内外较为常用的工艺即厌氧–缺氧–好氧,通过严格控制溶解氧营造细菌所需环境,硝化与反硝化反应紧密结合(通过内外回流比的控制)。Zhou [7] 等比较了A2O与AO处理焦化废水的效果,在相同的停留时间下,A2O与AO的COD和氨氮的去除率基本相同,但氮的去除率A2O要比AO效果好,因为产酸时可以有机氮化合物讲解成易降解的中间产物,因此效果要优异一些。影响降解效率的因素有很多主要的是温度、溶解氧、碳源投加量等等这些都影响这工艺的降解效率。庆华某煤制气、赤峰某煤化肥等多个项目工程,废水水质复杂,均使用多级A/O工艺,其出水水质COD和氨氮分别可以控制在200 mg/L以下和80 mg/L以下 [8];王晓伟 [9] 等实践A/O + MBR工艺,其对于COD的去除率可达85%,出水COD均值 ≤ 21 mg/L;对氨氮的去除率可达98%,出水氨氮均值 < 2 mg/L,总氮平均去除率在61.2%,而且工艺运行稳定。
4.4. SBR工艺
首先SBR工艺和A2O不同的地方为A2O是持续不停的进水出水,而SBR则是分为5个周期,分别为进水时期、反应时期、下沉时期、出水时期、闲置时期间。SBR歇性进水,5个周期反复进行从而达到厌氧–好氧–厌氧循环。SBR工艺是一个间歇反应器,和其他工艺相比SBR没有二次沉淀池、污泥回流设施,而且通常不设立调节池。SBR工艺的优点在于耐冲击负荷、工艺简单,费用较低、沉淀性能也相对较好。例如王鑫 [10] 对SBR阶段进行了试验,结果表明曝气时间和水中有机物的降解存在着密切相关的关系,曝气时间、曝气量不足时有机物降低程度低,而过长的曝气时间和曝气量会引起类似效果,因此对曝气量和时间需要严格的控制。
4.5. 其他工艺
现在存在许多工艺,例如MSBR工艺是A2O和SBR工艺的有机融合而来,废水和除氮后的活性污泥一起流到厌氧区,污泥混合液进而流进缺氧去、SBR和好氧池,最后由空气堰排出。
如果此期间使用单个处理工艺无法达到处理效果,就可以充分的考虑运用多种工艺进行联合,可以使用多种处理方式进行互补,在煤化工废水处理过程中回取得更好得效果 [11]。
4.6. 二级处理后煤化工废水的出水水质
从表1中我们可看出经过二级处理后的煤化工废水仍然含有较多的污染物,因此后面仍需要进行深度处理,以达到国家的排放标准。
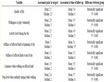
Table 1. Contents of various components of coal chemical wastewater after secondary treatment [12]
表1. 煤化工废水经过二级处理后各类成分含量表 [12]
5. 深度处理
5.1. 沉淀混凝法
就现在而言,常用的混凝胶有聚合硫酸铁(PAF)、聚合氯化铝铁(PAFC)、聚丙烯酰胺(PAM),煤化工废水中的胶状体和悬浮状的污染物凝聚成大絮体或颗粒沉淀后得到分离,沉淀混凝法普遍用于预处理和深度处理中,但存在的缺点是对出水的pH要求较高。
5.2. 吸附法
吸附法是通过吸附煤化工废水中的污染物沉淀分离,被广泛的应用于预处理和深度处理,原理是物理(范德华力)、化学(化学键力)、交换(静电力)来完成吸附去除。最为常见的就是活性炭。该法具有很好的去除效果,价格也较为便宜,但用量较大。
5.3. 高级氧化法
5.3.1. Fenton试剂法
Fenton试剂铁盐和双氧水的结合体,Fe3+在酸性条件下作为催化剂,加速双氧水分解产生具有高氧化活性物的自由基(·OH),而·OH能够使大多数的有机物降解和矿化。因为Fenton具有较强的去色和氧化能力,因此被广泛的应用于染料废水、含酚废水、煤化工废水的处理中。Fenton试剂法在原有的基础上不断发展,衍生了许多机理类似的Fenton体系,像配体-Fenton、电-Fenton等等。而影响Fenton试剂法的因素也有很多,比如温度、pH催化剂的种类、双氧水和铁盐的投加比等都对其有一定的影响。例如王维明 [13] 等制备了Al2O3/TiO2载体,负载铁氧化物作为催化剂,对4-氯酚的降解能力,结果表明其效果明显比普通芬顿法要好。Zhuang等 [14] [15] 将新型催化剂氧化铁和污泥活性炭用于非均相催化臭氧氧化和Fenton氧化工艺处理煤气废水,结果表明出水COD、总酚、BOD5均达到国内排放标准。
5.3.2. 臭氧氧化法
臭氧是氧化性极高的气体,但是臭氧不稳定必须现制现用。臭氧氧化可以明显地降低COD、降低色度,而且反应迅速,对pH的要求较低,而且出水后臭氧可以在短时间内分解掉且没有毒害,影响小,可以很好的应用于煤化工废水的处理之中,而且随着发展,臭氧的制造成本也在不断的下降,是一个不错的选择。臭氧氧化可以分为两种:直接氧化和间接氧化。间接氧化是由自由基进行氧化(·OH);直接氧化则是对有机物直接氧化,直接氧化反应速率比较慢、具有选择性、反应速率常数在1.0~103 M−1S−1之间。例如张志伟 [16] 试验臭氧的影响因素表明,臭氧浓度仅仅影响氧化速率,对于COD的去除率没有太大的影响,而臭氧的浓度影响较大,浓度过低会使反应时间增长,而浓度过高则会造成浪费,因此需要选择合适的臭氧浓度达到最高的利用率;煤化工废水的pH对臭氧的去除效果影响较大,在酸性和中性的条件下对COD的去除率仅为30%,而pH为9.06时对COD的去除率可以达到45%,而pH再升高达到11.49时,去除率反而会有所降低,因此在使用臭氧氧化时需要调节合适的pH。Zhu等 [17] 认为臭氧催化氧化(AOPs)技术可以有效去除煤化工废水中的含氮杂环有机物,吡啶和吲哚的去除率分别可达90%、95%以上。
5.3.3. 临界水氧化法(SCWO)
临界水氧化法(SCWO)又可以称为“内燃烧”。因为它是在水中氧氧气在水的超临界状态(22 MPa, 400℃)下氧化水中的有机物,此过程我们可以近似的看作是燃烧,有机物被氧化成水和二氧化碳;氮被氧化成氮气;氯、硫被氧化成无机盐,然后通过沉淀分离达到污染物的去除,燃烧相对来说比较彻底,因此该方法的氧化率较高可以达到99.9%以上。SCWO在煤化工废水中占有一定的地位,无论高浓度有机废水、吡啶废水、喹啉废水,皆有很好的去除效果,而且SCWO可以分为连续和间歇操作两种可以满足任意流量,无论是大流量还是小流量,但连续操作对于设备的要求就会高许多,较为复杂。
6. 结语
就我国的能源储存来看,煤化工一定是重中之重,而从目前来看,主要还是预处理、生物处理等等,但仍然存在许多问题,例如治理成本相对较高,处理效果有时不太理想不稳定,工艺也相对落后,因此这就需要我们不断地探索、试验,引进新的技术或者结合各种工艺来扬长避短,发挥各自的优势,实现废水处理的效益最大化,只有把处理成本以及存在的各种问题解决掉,我国的煤化工才可以进入“高速路”,我国的能源储存形势改变不了,因此煤化工的工业废水处理必然是发展和研究的重点。