1. 引言
旋振筛是一种广泛应用于颗粒、细粉及粘液等筛分场合的筛分机械,其具有筛面利用率高、筛分效率高及筛分环境清洁等优点,由于其结构封闭,筛分环境清洁,所以目前广泛应用于食品、制药、冶金等领域中。当旋振筛应用于食品生产线上时,就必须要求其具备易清理、部件易更换、筛分效率高、筛分效果好的特点,尤其筛分效率与筛分效果直接决定了食品生产后续工艺的优劣,从而直接决定成品质量的高低。旋振筛在生产线上实际工作时常会出现颗粒梗塞网孔、筛面上物料颗粒聚积等问题,从而大大降低生产效率。针对以上问题需要探索一种新的思考方式,将旋振筛中物料颗粒的运动状态用数据直观的呈现出来,并且对影响其运动状态的因素进行分析,来进一步直观的了解和认识旋振筛的筛分机理。
离散单元法(Discrete element method, DEM)的主要思想是把研究对象划分为一个个互相独立的单元,根据单元之间的相互作用和牛顿运动定律,采用动态松弛法或静态松弛法等迭代方法进行循环迭代计算,确定在每一个时间步长所有单元的受力及位移,并更新所有单元的位置。通过对每个单元的微观运动进行跟踪计算,即可得到整个研究对象的宏观运动规律 [1] [2]。离散单元法作为一种计算散体介质系统力学行为的数值算法,当物料颗粒参数及接触模型设置完毕,并将几何体添加运动状态后,可以很好的模拟物料流中颗粒的运动及颗粒间的相互碰撞情况,适用于旋振筛筛分机理的研究 [3] [4] [5]。
提高旋振筛筛分效率一直是很多国内外学者的研究目标,Hashem等 [6] 采用了离散单元法研究了旋振筛在筛分过程中颗粒的透筛、分层情况,并比较了不同参数、连续筛分与批量筛分旋振筛的筛分效率。杨晋 [7] 设计了一种筛网倾斜式旋振筛,通过反复利用倾斜筛面来提高筛分效率。Sobolev [8] 通过实验研究了物料的含水量不同对旋振筛筛分效率的影响。国内外学者主要通过调整旋振筛几何参数、旋振筛的机械结构来提高旋振筛的筛分效率,并未从物料参数调整的角度进行研究。本文采用控制变量的方法,其中研究对象是三元旋振筛,变量是物料颗粒的形状、物料颗粒的投放速率,并以三维离散软件EDEM为研究工具对物料颗粒在旋振筛内的运动状态进行模拟分析,从而获得相关结论。
2. 旋振筛建模
本文以食品工业中较为常见的三元旋振筛为研究对象,三元旋振筛的三维模型如图1所示。
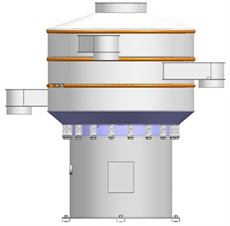
Figure 1. Three dimensional model of three dimensional rotary vibration screen
图1. 三元旋振筛的三维模型
三元旋振筛主要由防尘盖、筛框、多层筛网、紧固带、振动电机、隔振弹簧及底板组成。工作时,安装在旋振筛内部的两个不平衡重锤会将激振源的旋转运动改变,即变为复杂的多种状态叠加的三次元运动,当将这个复杂的三次元运动传递给筛网后,物料颗粒就会在筛网上形成一种螺旋状的由中心向四周的扩散运动,因此在筛网上的物料颗粒会快速的依次完成分层、透筛等过程,粒径大于网孔的颗粒会留在筛网上,而粒径小于网孔的颗粒则会成为筛下物,最终通过出料口落入收集装置中,当旋振筛中的物料全部出筛后,此次旋振筛分工作结束。
由于真实的旋振筛具有很多零部件,为了仿真更加直观高效,所以本次模拟将与仿真无关的部件全部隐藏 [9],简化后的旋振筛仿真模型如图2所示。
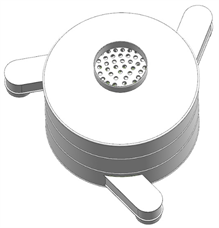
Figure 2. Simplified simulation model of rotary vibration screen
图2. 旋振筛仿真简化模型
3. 初始化模型
本文采用的三维离散软件是EDEM,主要包括前处理器、求解器和后处理工具,前处理器模块用来建立和初始化模型 [10];求解器模块用来进行模拟仿真和计算并可查看仿真的进程;后处理器用于对仿真结果进行提取和分析,如对数据进行保存和提取、用动画显示仿真过程及用图表显示显示仿真结果等 [11]。
第一步向EDEM中导入旋振筛仿真简化模型,然后设置仿真所需物料和旋振筛材料的相关参数,导入的材料具体参数如表1所示。(冷冻颗粒指咖啡浓浆冷冻颗粒,相关参数采用GEMM数据库接触参数标定)形状主要有球形与非球形颗粒,旋振筛的主要运动参数包括圆锥摆角、振动频率等 [12]。在定义基础颗粒时,设置1.5 mm、3 mm、5 mm及6 mm共4种不同粒径的物料颗粒,物料的总质量为0.2 kg。旋振筛的运动设定:以固定点(100.2, 100, 156.3)为中心绕X轴摆动,振动频率14 Hz,摆动幅值0.77 deg,相位0,同时以固定点(100.2, 100, 156.3)为中心绕Y轴摆动,运动参数设置同上,只需将相位改到90,将两个相位相差90˚的垂直摆动进行合成就会达到我们所需的旋振效果 [13]。振动筛分过程的实质是通过筛网与颗粒之间接触、碰撞以及颗粒之间的相互作用来传递能量,从而达到促使不同粒径的颗粒有效分层、顺利透筛的目的。为正确地描述颗粒同筛网以及颗粒同颗粒之间的碰撞过程,本次仿真总时长为8 s,采用弹性–阻尼–摩擦接触力学模型如图3所示 [14]。
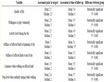
Table 1. Related material property parameters
表1. 相关材料物性参数
注:Fn为法向力;Ft为为切向力;Kn为法向刚度;Kt为切向刚度;Cn为法向阻尼系数;Ct为切向阻尼系数;μ为摩擦系数;1、摩擦器;2、阻尼器;3、颗粒刚度(弹簧)
Figure 3. Elastic damping friction contact mechanics model
图3. 弹性–阻尼–摩擦接触力学模型
为了最大程度模拟旋振筛实际筛分情况,4种粒径的颗粒除6 mm外均采用球形颗粒与非球形颗粒并存的方案,仿真使用的3种非球形颗粒三维模型如图4所示,颗粒填充模型如图5所示。4种不同粒径的颗粒质量占比以及非球形颗粒占对应粒径的比例如表2所示。
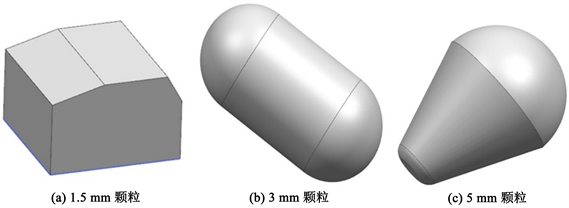
Figure 4. A 3d model of non-spherical particles
图4. 非球形颗粒三维模型
4. 仿真分析
仿真开始时,4个颗粒工厂以设定的速率生成4种不同粒径的颗粒,经物料工厂下落到第一层筛网上,旋振筛做周期性的旋振运动,筛网上的物料颗粒随旋振筛一同作渐开线式扩散运动,粒径大于网孔的颗粒会留在筛网上,而粒径小于网孔的颗粒则会成为筛下物,最终通过出料口落入收集装置中。不同形状、不同粒径的颗粒即使在相同的工况下其运动状态也会有很大差异,本文通过分析颗粒在筛网上的平均速度、不同形状颗粒质量占比及颗粒的投放速度等多种因素,讨论其对于旋振筛筛分效率及筛分质量的影响。
4.1. 颗粒质量占比分析
分析共进行3次模拟仿真,3种不同工况的颗粒质量占比如表3所示,3种不同工况下颗粒的平均速度与平均角速度如表4所示,3种不同工况下颗粒在不同统计区间内的质量分布如表5所示。
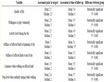
Table 4. The average velocity and angular velocity of particles under three working conditions
表4. 3种工况颗粒的平均速度及角速度
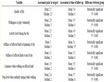
Table 5. Mass distribution of particles in the screen under three working conditions
表5. 3种工况颗粒在筛网的质量分布
分析表4、表5中的数据可以发现,随着非球形颗粒质量占比的增大,物料颗粒的平均速度变化不大,然而物料颗粒的平均角速度却大幅度减小,这说明物料颗粒在旋振筛中的旋转幅度减小,减小了筛分速度。从表5数据中可以发现颗粒在3种不同工况下的质量分布规律:第1、2层筛网统计区间内颗粒质量小幅下降;第3层筛网统计区间内颗粒质量大幅下降;并且随着非球形颗粒质量占比的增大,3层筛网统计区间内的总质量较少较多。由此可见很多小颗粒并没有在设想的筛网统计区间内出筛,从而导致筛分效率的降低。导致此种情况出现的原因是同粒径的非球形颗粒质量要小于球形颗粒,所以在增加非球形颗粒占比的同时,颗粒数量会急剧提升,颗粒间的碰撞加剧,由于不同粒径颗粒质量与动能都相差较大,大量小颗粒会被大颗粒裹挟着提前出筛,从而导致了筛分效率的降低。
4.2. 颗粒投放速率分析
当旋振筛投入实际生产时,一般会选取一个使旋振筛筛分效率最高的物料投放速度作为默认速度。接下来只改变的物料的质量流率,来探索其对旋振筛筛分效率的具体影响。颗粒的平均速度随质量流率变化如图6所示,不同质量流率下物料颗粒在旋振筛三个统计区间内的质量分布如表6所示。
观察图6和表6可以发现,颗粒的平均线速度与平均角速度都随着质量流率的提高而逐渐降低。原因是设定的初始质量流率低,单位时间内落到旋振筛筛网上的物料颗粒相对较少,没有形成物料堆积,物料颗粒与筛网的接触更加充分,从而使得颗粒可以更快速的分层,更充分地完成透筛,完成较高质量的筛分 [15];但伴随着质量流率的不断增大,已经落到旋振筛筛网上的颗粒来不及完成筛分,颗粒料层不断加厚,颗粒的运动空间被压缩,从而导致颗粒无法有效分层,颗粒间相互碰撞愈发剧烈,
(a) 物料颗粒的平均线速度
(b) 物料颗粒的平均角速度
Figure 6. The average velocity of particles at different mass flow rates
图6. 不同质量流率下颗粒的平均速度
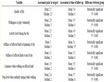
Table 6. Particles mass distribution at different mass flow rates
表6. 不同质量流率下颗粒的质量分布
且因为大颗粒的动能远大于小颗粒,所以部分小颗粒会被大颗粒裹挟着提前出筛,大大降低了筛分效率。其中的主要原因是物料投放速率从一开始逐渐契合旋振筛筛网的处理能力,到后面逐渐超过旋振筛筛网处理能力,旋振筛处理能力与物料投放速率的平衡被破坏,筛分效率因此降低,由此可见物料的质量流率也会很大程度的影响旋振筛筛分效率。
4.3. 颗粒动能变化分析
为进一步加深对旋振筛筛分机理的理解,对旋振筛筛分过程中颗粒的平均转动动能、平均平动动能及平均总动能的变化进行分析,球形颗粒与非球形颗粒在筛分过程中的平均转动动能、平均平动动能的变化如图7所示,球形颗粒与非球形颗粒的平均转动动能、平均平动动能及平均总动能如表7所示,3种粒径的主体颗粒平均动能如表8所示。
从图7中可以观察到筛分初期旋振筛的工作情况不稳定,因此筛分初期颗粒的平均动能有较大波动,球形颗粒更为明显。但当筛分至0.5~1.5 s时,筛分情况逐渐趋于稳定状态,物料颗粒的平均转动动能及平均平动动能曲线也逐步呈现稳定的周期性变化。将球形颗粒与非球形颗粒的平均动能指标进行对比可以看出,在工况完全相同的情况下,球形颗粒的平均转动动能指标约为非球形颗粒的4.8倍,球形颗粒的平均平动动能指标约为非球形颗粒的5.2倍,且球形颗粒的平均总动能也远大于非球形颗粒,这组对比可以从能量的角度说明球形颗粒在旋振筛中的筛分效果要比非球形颗粒更好。
(a) 颗粒平均转动动能
(b) 颗粒平均平动动能1.球形颗粒2.非球形颗粒
Figure 7. The average velocity of particles at different mass flow rates
图7. 不同质量流率下颗粒的平均速度
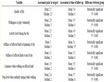
Table 7. Average kinetic energy of spherical and non-spherical particles
表7. 球形颗粒与非球形颗粒平均动能
从表8中可以发现,5 mm颗粒的平均转动动能、平均平动动能及平均总动能均远大于3 mm颗粒,将3 mm颗粒与1.5 mm颗粒进行比较时,结果也是如此,即在相同工况下,较大颗粒的动能指标均远大于较小颗粒。将5 mm和3 mm颗粒的平均动能指标进行对比可以发现,当仅考虑颗粒大小对筛分效果影响时,粒径越大,动能越大,粒径越小则反之,所以当颗粒越小,筛分效率就越低。与此同时当同一批物料中颗粒的粒径相差越大时,小颗粒被大颗粒料流裹挟提前出筛的现象越突出,筛分效果就越差。
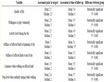
Table 8. Average kinetic energy of main particles
表8. 主体颗粒平均动能
5. 结论
本文以离散单元法为理论指导,以三维离散软件EDEM为研究工具,对物料颗粒在旋振筛上的运动状态进行了多方面分析,得到以下结论:
1) 相同工况下,提高物料中非球形颗粒的质量占比时,会使颗粒数量剧增,急剧颗粒间的碰撞,从而使旋振筛筛分效率下降15%左右,即降低非球形颗粒占比时筛分效率会相应提升。
2) 物料颗粒的质量流率变化会明显影响旋振筛的筛分效率。其在一定范围内的提升可以有效提高筛分效率,并在一定程度上提高筛分质量;但当质量流率提高至某一指标,打破旋振筛处理能力与物料投放速率的平衡时,就会出现大、小颗粒分层不明显、堵塞网孔的现象,导致筛分质量变差,筛分效率也会大大降低。
3) 相同工况下,球形颗粒的平均转动动能、平均平动动能及平均总动能都要远大于非球形颗粒,同时小颗粒的3项平均动能指标均远小于大颗粒,这也就合理解释了当大小颗粒质量占比越复杂、粒径相差越大,筛分效率越低的现象。
本文对旋振筛筛分过程中物料颗粒运动状态进行了模拟分析,获得了影响旋振筛筛分效率的相关参数,对了解旋振筛的筛分机理起到了积极作用,并为旋振筛在实际生产中的应用提供了参考依据。
基金项目
江苏理工学院研究生实践创新计划项目“冻干水果自动化生产线研究”(XSJCX20_43)。
参考文献
NOTES
*通讯作者。