1. 引言
随着能源和环境形势的日益严峻,环保、高效、经济的蒸发冷却空调技术在节能减排中发挥着重要的作用,随着蒸发冷却空调技术的发展,其性能测试技术也在不断地更新迭代,本文所涉及的机房空调测试实验室,是基于空气焓差法原理建造,可测试大型蒸发冷却空调及直通风产品的综合性能测试实验室 [1]。基于空气焓差法建造的环境实验室,其房间内部气流组织的均匀性会对测试结果的稳定性和准确性造成严重影响。由于房间内部测试区域的速度场、温度场以及气流流动方向难以预测,而在实验室建成后通过现场实测结果调整送风结构使测试区域气流组织满足测试要求的方法将耗费大量的人力和物力。CFD仿真技术可以在实验室设计阶段,对房间内的气流分布进行模拟仿真,预测气流方向,避免气流短路,因此CFD仿真技术在送风结构的设计过程中具有重要的实用价值 [2]。
2. 数据中心空调实验室室外侧气流组织
本文所涉及的焓差实验室送风结构是基于国标GB/T 17758-2010和GB/T 19413-2010的要求以及相关技术协议进行设计 [3] [4],本实验室室外侧房间外形尺寸为18 × 15 × 10 m (长 × 宽 × 高)测试区域尺寸为18 × 8 × 8.5 m (长 × 宽 × 高),室外侧测试工况范围为干球温度−40℃~60℃,温度波动范围±1℃,风速小于2.5 m/s,单层孔板送风结构见图1。
1) 由于该实验室测试区域空间层高较高,因此房间内的送风方式选择下送上回,以使气流充满整个测试区域,避免出现气流短路,在测试区域送风口处布置全面孔板,孔板尺寸选择为12 × 3 m (长 × 宽)。
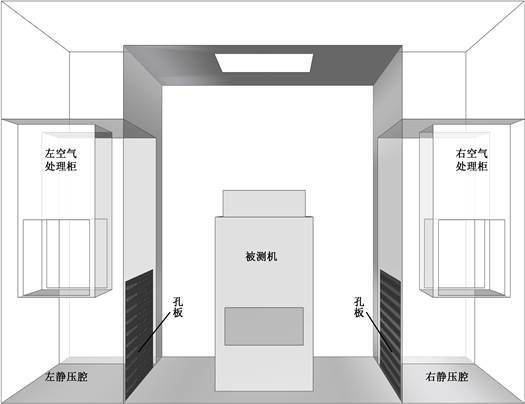
Figure 1. Single-layer orifice plate air supply structure
图1. 单层孔板送风结构
2) 焓差实验室室外侧房间内最大循环风量的选择取决于以下几个因素:① 房间内最大循环风量应不小于被测机的最大循环风量,由相关技术要求可知该实验室室外侧被测机最大循环风量为200,000 m3/h;② 按国标要求,房间内最大循环风量应满足不小于房间内每分钟一次的换气量(取富余量0.5),计算可得房间内循环风量为240,000 m3/h。因此该实验室最大循环风量为240,000 m3/h,由于该实验室室外侧循环风机数量众多,其安装受现场尺寸限制,因此该实验室采用左右两侧送风的方式,其中左右两侧空气处理柜的送风风量均为120,000 m3/h。
3) 参照《实用供热手册》中全面孔板送风的设计计算方法 [5],进行孔板的设计计算,其中总循环风量选取为240,000 m3/h,孔板选择6 mm孔径,计算过程如下:
(1)
式中va——孔口射流风速,m/s;
d——孔口直径,mm;
——空气运动粘度,取15.06 × 10−6 m2/s。
根据射流风速和送风量可计算开孔总面积Sk和孔隙率
:
(2)
式中F——送风量,m3/h;
——孔口流量系数,本实验室采用1 mm厚铝制孔板,故取0.78。
(3)
式中S为单侧孔板总面积,计算得36 m2。
检验校核工作区最大风速,其风速值应小于测试区域允许最大风速,即2.5 m/s由于全面孔板,孔口射流扩散角等于0,因此工作区域最大风速可按照下式计算:
(4)
式中Vb为测试区域最大风速,m/s。
孔板送风结构的静压腔厚度,将直接影响静压腔内部的静压分布规律(参考文献),进而影响孔口射流的方向和大小,以及孔板出风的均匀性。静压腔的厚度可由下式进行计算:
(5)
(6)
式中H为静压腔厚度,m;
L为气流在静压腔内的最大流程,m;
Fd为单位面积孔板的送风量,m3/m2·h。
代入上式计算可得,在循环风量为240,000 m3/h时,可以得到孔板孔隙率为26%,静压腔厚度为2.434 m。综合以下因素:① 最大测试机宽度为5.5 m;② 国标要求被测机非进风面与房间墙板间距离应不小于0.9 m。因此送风静压腔厚度取3.5 m,如图1所示。
3. 物理建模和仿真分析
3.1. 建立实验室室外侧房间物理模型
根据上述实验室室外侧房间几何尺寸,建立物理模型,忽略墙板厚度,空柜送回风口尺寸,以及房间内风道板开口尺寸均按照上述计算尺寸进行设置。由上述孔板的设计计算可知,单块孔板的开孔数目极多(单块孔板孔口数目可达334,707个),在ICEM软件中无法进行每个圆孔面的创建以及网格的划分,因此在物理模型的创建过程中,本文将整块孔板理想化为风道板开口,并在该开口上创建一个无厚度的面,作为孔板透风面 [6]。实验室室外侧房间物理模型如图2所示。
3.2. 数学模型基本假设与边界条件选择
如图2所示,房间内的气流流向可描述为,气流在经空气处理柜的降温、除湿、加热、加湿等处理后,由空气处理柜侧面流出,进入静压腔,在静压作用下由静压腔一侧孔板流入测试区域,在测试区域上部与被测机出风相混合,经风道板顶部出口离开测试区域,并经顶部回风腔回到空柜中。
对建立好的物理模型做如下假设:
1) 本文所研究的室外侧房间内气流为不可压缩的稳态湍流;2) 实验室室外侧围护结构与风道板均为150 mm厚聚氨酯保温库板,在物理模型中围护结构及风道板均简化为没有厚度的绝热壁面;3) 被测机视为内热源;4) 使用Boussinesq密度假设,考虑重力加速度影响,即需考虑垂直方向上由于温度梯度的变化进而对浮升力产生的影响,动量方程中其他项的密度均视为常数;5) 湍流流动过程中的粘性耗散忽略不计 [7]。
本文中物理模型边界条件设置如下:空柜出风口设置为速度入口,速度入口边界条件可准确控制测试区域循环风量;空柜回风口处设置为压力出口,静压设置为0 Pa;风道板顶部回风口设置为通透面,即interior;由前文所述,该模型中孔口数目众多,无法在ICEM中准确描述每一个孔口面,因此本文借助ANSYS中现有的多孔阶跃模型(porous-jump)来描述气流流经多孔板前后的压降,由前人研究可知,该模型广泛适用于多孔板在不同介质条件下的数值计算,其中多孔阶跃模型的计算公式如下 [8]:
(7)
式中μ——介质动力粘度,Pa·s;
α——粘性阻力系数,/m2;
ρ——介质密度,kg/m3;
C2——惯性阻力系数,m−1;
v——介质流速,m/s;
Δn——多孔板厚度,m。
有关多孔介质的参数推导,常用方法有如下几种:1) 在已知压损和速度的条件下,拟合阻力损失与速度的函数关系,进而求得C2与α;2) 基于欧拉公式可推导填充床的粘性阻力系数和惯性阻力系数;3) 对于湍流状态下的多孔板和滤网,常使用Van Winkle [9] 等公式推导得出多孔介质的相关参数。本文所使用的多孔板可理想化为气压均布板,故该多孔板的α = 1,C2的计算公式使用上述方法推导得出 [10]:
(8)
式中C为多孔板孔系数,C取0.78;
Δn为多孔板厚度。
室外侧房间空气处理柜选用20台变频调速风机,分左右两侧布置,风机静压可满足风道内局部阻力损失和沿程阻力损失要求 [11]。被测机进出风方式为侧进顶出。室外侧工况为干球温度40℃,风量选择80,000 m3/h。多孔板选用2 mm厚铝制孔板 [12],孔板开孔率选择26%,12%,6%,三种不同孔板,旨在探究,孔板开孔率对测试区域气流组织的影响。
3.3. 单孔板送风模拟结果分析
为了方便比较不同开孔率下,测试区域的速度和温度分布,本文在测试区域垂直方向,被测机入口附近选取了三个截面,进行比较分析,三个截面高度为1.5 m、2 m、2.5 m,如图3所示。
不同孔隙率下测试区域的速度分布如图4所示:
由速度云图可知,随着孔隙率的降低,测试区域水平截面的平均风速有所减小,最高风速均小于2.5 m/s,现有三种孔隙率下的单孔板送风方式,均可满足国标要求。由图4(e)可知,在孔板孔隙率为26%时,被测机侧面入口处出现了的局部风速偏高的区域,最大风速可达2 m/s,被测机入口风速超过了设计值,而在远离孔板送风区域的位置,风速偏低,最大风速和最小风速差值为1.9 m/,因此孔隙率为26%时的送风方式虽然在风速大小上满足国标要求,但在被测机迎风面风速过高,因此,此种布置方式不满足测试要求。为改善房间内的速度场分布,降低被测机迎风面风速,本文设计减小孔板开孔率,增加射流衰减的速度。比较图4(a)、图4(d)和图4(e)可知,随着孔板孔隙率的降低,房间内最大风速降低至1.8 m/s,最大风速与最小风速差值为1.7 m/s,被测机迎风面风速分布得到了有效改善,风速偏小的区域面积有明显的减小。在开孔率为12%时,虽然速度大小有所衰减,但被测机迎风面速度分布仍不均匀,受送风口射流的影响仍十分明显。因此,降低孔板孔隙率,可有效改善房间内的速度场分布,当孔隙率降低至6%时,测试区域内速度分布较为均匀。
观察图4(a)、图4(b)、图4(c)可知,随着截面高度的增加,气流逐步混合,风速较低的区域面积逐渐减小,速度场分布不均的现象逐渐改善。
由图5可知,测试区域内上端温度较高且温度波动大,下端温度较低,且温度波动较小,观察图5(f)可知,房间内温度分布主要受被测机出风影响,由于测试区域上端靠近被测机出口,因此该区域温度波动较大,而测试区域下端远离被测机顶部出口,因此温度受其影响较小。观察图5(a)、图5(d)和图5(e)可知,孔隙率的变化对房间内温度分布影响较小,当孔隙率为6%时,z = 1.5 m平面最高温度为313.9 k,该截面最大温差为1.3 k,孔隙率为12%时截面最高温度为314.2 k,最大温差为1.6 k,孔隙率为26%时,截面最该温度为314 k,最大温差为1.4 k,由前文可知,测试工况为313 k,因此在三种孔隙率下,房间内温度波动均为超过±1 k。由此可知,在送风量以及送风结构确定的情况下,送风孔板孔隙率的改变对测试区域温度分布的影响十分有限。
为了更加直观的观察被测机周围的速度分布情况,如图6所示,在送风孔板孔隙率为6%时,在被测机三面入风口处设置观测点,获取速度分布曲线。速度取样区域,如图6所示。
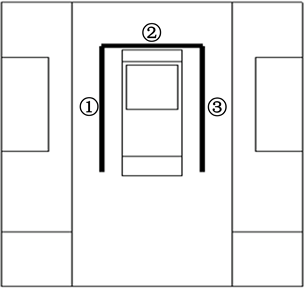
Figure 6. Distribution of measuring points of air supply velocity field of single orifice plate
图6. 单孔板送风速度场测点分布图
由图7可知,被测机两侧迎风面风速呈对称分布,在Y向4 m到13 m处,存在风速偏高区域,且在
(a) 监测点①速度分布
(b) 监测点②速度分布
(c) 监测点③速度分布
Figure 7. Velocity distribution line graph
图7. 速度分布折线图
Y = 10.8 m处风速达到最高,说明孔板送风口与被测机侧面入口处气流受到孔板出风和被测机回风两方面的影响,气流流速存在较大波动。由图7(b)可知,被测机端部回风口处气流状态十分稳定,由该折线图可以很直观的看出,气流由两侧孔板送入测试区域,并迅速衰减,直到被测机端部入风口处,气流受被测机进风影响,风速有小幅提升。顶出风被测机端部入风口处气流组织才是最理想的状态,而被测机迎风面入口的气流组织状态并不理想,因此由上述分析可知,单孔板送风,孔隙率为6%时,测试区域的速度场指标满足测试要求,但被测机迎风面的速度场分布并不均匀,因此该结构的送风方式还需进一步改善。
3.4. 双孔板送风模拟结果与分析
为了进一步改善被测机迎风面气流流速波动较大这一状况,本文提出了双层孔板节流的送风方式,其结构图如图8所示:
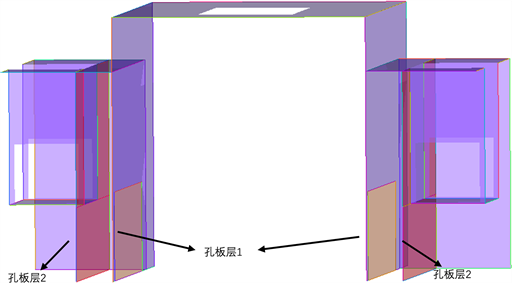
Figure 8. Double-hole plate air supply structure diagram
图8. 双孔板送风结构图
双孔板送风方式,是在原有单孔板送风结构的基础上,在孔板风口与空气处理柜中间增加一层2 mm厚铝制孔板。由上述可知,单孔板送风结构下,当孔板开孔率为6%时,房间内气流组织较为均匀,因此双孔板送风结构下,两层孔板的开孔率均选择6%。其测试区域内1.5 m、2 m、2.5 m截面速度场与温度场分布,如图9所示:
图4与图9中等截面速度分布图相比,可以很清晰的发现,双孔板送风结构,有效消除了孔口射流对被测机迎风面气流组织的影响。在双孔板送风结构下,测试区域内气流平均流速维持在0.8 m/s。被测机进风口处均未受到孔口射流影响,其附近速度梯度变化均匀,测试区域内风速较小的区域面积大幅减小。在测试区域垂直方向上,速度分布区域均匀,整体变化趋势与单孔板送风方式相同。双孔板送风方式下,测试区域内温度分布也存在明显改善,在1.5 m截面上,高温区域面积有大幅减小,且仅出现在远离被测机的房间边角处,被测机出口侧测试区域内,温度有明显降低,测试区域内最大温差为1.8 K,面平均温度为312.85 K,面平均温差控制在,0.15 K。因此双孔板送风方式可有效改善测试区域内速度与温度分布,消除孔口射流对测试区域内速度场的影响,削弱被测机出风对房间内温度场的影响。
4. 结论
1) 根据数据中心空调的测试需要,设计了侧面孔板送风顶部出风的送风结构,探究了孔板孔隙率,对高大空间孔板送风的影响,研究发现,在单孔板送风结构下,孔板孔隙率由26%变化为12%最后变化为6%,对测试区域内的温度场的影响十分微弱,对测试区域内速度场的分布略有影响,降低孔板孔隙率可以减小测试区域面平均风速,并使速度场分布更加均匀。但降低孔隙率并不能改善被测机迎风面上的速度分布,在孔板孔隙率为6%时,被测机迎风面依然存在较大的风速波动。
2) 双孔板送风结构,很好地改善了被测机迎风面的速度分布状况,并进一步减小了测试区域的面平均风速,使房间内速度场分布更加均匀,在一定程度上,双孔板节流的送风形式,也改善了测试区域内原有的温度场分布,使原本的高温区域面积大幅减小,并集中在测试区域边角处,被测机周围的温度分布更加均匀,温度波动变小,因此双孔板节流的送风形式更加适用于大风量、高大空间实验室的气流组织。