1. 前言
出钢口是转炉终点钢水流出的必经通道,一般由出钢口座砖和袖砖组成,是转炉耐火材料的关键部件之一。由于出钢口通钢量大,受到高温溶液(钢水和炉渣)的溶解、冲刷及氧化熔损等,因此出钢口在使用过程中经受侵蚀,导致其使用寿命低 [1]。马鞍山钢铁股份有限公司第一钢轧总厂通过采取改善出钢口套砖材质、扩大出钢口内径、出钢里口定期喷补、在出钢口使用后期下套管等措施,将出钢套砖使用寿命由138炉提高到182炉 [2]。山西金烨钢铁公司炼钢厂通过采用改善出钢口材质和填料质量、优化日常维护等措施,使出钢口平均寿命由130次提高到491次 [3]。山东石横特钢公司通过改进出钢口组装工艺,优化出钢口更换工艺,调整挡渣工艺等措施对出钢口进行优化改进,出钢口使用寿命由实施前的200~300炉提高至700~800炉 [4]。在借鉴同行生产经验的基础上 [1] - [8],本研究团队通过分析山钢股份莱芜分公司(以下简称莱钢)炼钢厂转炉出钢口存在问题并进行针对性改造,提高了出钢口的使用寿命和使用效率。
2. 转炉出钢口存在问题
原有出钢口在使用过程存在四个方面的风险。第一,使用寿命低。出钢口平均寿命200炉左右,每座转炉平均6天完成一次更换出钢口作业。第二,穿钢风险高。因出钢口首砖与滑板内水口采用耐火泥涂抹的方式连接,在出钢过程中,钢水易从耐火泥涂抹缝隙间渗出,导致内水口穿钢事故的发生。第三,作业时间长。更换一次出钢口作业,平均需要90分钟,若因内水口渗钢被迫更换出钢口,由于要清理冷钢,更换时间则需要再延长60分钟左右,严重影响产量。第四,劳动强度大。受现场环境影响,更换出钢口作业时,职工劳动强度较大,若出现内水口渗钢,则需要烧冷钢作业,进一步增大现场工作人员的劳动强度,且危险性增大。
3. 转炉出钢口寿命短的原因分析
3.1. 炉气的氧化
从转炉装入铁水到吹炼过程中,出钢口都处于高温氧化气氛下,吹炼过程中产生的炉气中含有大量的CO,从出钢口排出时发生C-O反应,在出钢口内壁表面生成脱碳层,直接造成出钢口的损毁。
3.2. 钢水、炉渣的摩擦损毁及机械冲刷破坏
出钢时,出钢口要承受转炉内钢水的巨大压力,同时钢水、炉渣在流出出钢口时,与出钢口内壁产生摩擦、冲刷,直接对出钢口内壁造成机械破坏。
3.3. 钢水、炉渣的高温熔解
出钢温度一般为1640℃,高温钢水的作用下,出钢口的材料会软化,强度显著降低,甚至会熔解,造成出钢口的损毁。
3.4. 钢水、炉渣的化学侵蚀
出钢口的理化指标见表1。
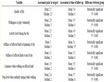
Table 1. Physical and chemical indexes of tapping hole
表1. 出钢口理化指标
转炉冶炼达到终点出钢时,钢水一般都具有较强的氧化性,尤其是炉渣氧化性更高,在高温、高氧化性条件下,会发生以下化学反应。
在化学反应过程中,钢水或炉渣中的氧会从镁质出钢口材料中夺取碳,从而使耐火材料结构疏松,强度变差。另外,如果炉渣碱度太低或渣中MgO含量较低,产生以下化学反应。
同样会加剧出钢口的化学侵蚀。
4. 解决转炉出钢口寿命短的措施
4.1. 出钢口改造优化
在理论分析基础上,通过对更换下线的出钢口进行检查,发现出钢口侵蚀严重的部位主要为首砖部位,首砖部位侵蚀严重是导致出钢口更换的主要原因,如图1所示。内水口砖与出钢口首砖采用人工涂抹耐火泥的方式连接,造成内水口与出钢口首砖之间不可避免的会存在一些缝隙,出钢过程中由于钢水静压力的作用,内水口与出钢口首砖之间缝隙容易穿钢,是导致首砖侵蚀严重的主要原因。由于首砖部位与出钢口是一个整体式,首砖部位侵蚀严重后,必须更换整支出钢口。

Figure 1. Influencing factors of tap hole life
图1. 影响出钢口寿命的因素分析
对出钢口首砖进行分体式改造,在首砖和内水口之间加一个碗状台阶,避免内水口与出钢口首砖直接接触,如图2所示。当出钢口使用到一定次数以后,碗砖内壁受到侵蚀,此时可以直接更换碗砖。
(a) 改造前
(b) 改造后
Figure 2. Split transformation of tapping hole
图2. 出钢口分体式改造
4.2. 转炉降低终渣∑FeO%含量,减少对出钢口的侵蚀冲刷
由于测量TSC时机不合适、不使用自动炼钢模型而手动干预,不同废钢比使用相同操作模型等因素,导致终点压枪时间不够,过程枪位过高,导致出现终点渣泡情况。制定新的枪位模型,保证终点压枪时间,减少人为干预,保证自动炼钢的使用率。
目前氧枪使用喉口直径为35.2 mm,设计工作氧压使用范围0.85~0.95 MPa。在低废钢比冶炼炉次过程控制中,为保证充分化渣和兼顾抑制喷溅,通常采用较低氧压低枪位操作模式,正常工作氧压控制在0.85~0.90 MPa范围,在大废钢比冶炼中,低枪位不利于转炉化渣,低氧压不利于转炉熔池提温。提高转炉供氧压力至0.90 MPa以上,通过高供氧强度冶炼提高转炉熔池温度,能确保将炉内废钢快速熔化。大废钢比冶炼延长前期高枪位至5分钟左右,通过高枪位冶炼增加渣中氧化亚铁含量,保证炉渣化透,提高前期炉渣脱磷率。大废钢量导致转炉开渣时间由原来吹炼4 min延长到6~7 min,转炉开渣后逐渐氧枪至正常枪位直到终点。保证终点压枪时间大于1.5 min。
通过一系列举措渣中∑FeO%含量由20%降至16%,炉渣氧化性降低,一方面可减少对出钢口的侵蚀,增加出钢口寿命;而且可降低铁损降低钢铁料消耗,给转炉带来双向效益。
5. 效果分析
5.1. 出钢口寿命提高
项目实施后,出钢口平均使用寿命由平均200炉提高至平均370炉左右,减少了出钢口更换次数。表2为出钢口改造后每个月各炉座月平均出钢口寿命。
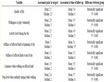
Table 2. Monthly average tap hole life of single furnace from June to December, 2021
表2. 2021年6~12月份各炉座月平均出钢口寿命
出钢口寿命为每一个出钢口能够生产的炉数,即从出钢口上线到下线生产的炉数。
5.2. 缩短出钢口设备更换时间,降低生产周期
对出钢口首砖进行分体式改造并降低炉渣氧化铁含量后,平均使用寿命提高170炉以上,在国内同类型转炉出钢口寿命提高50炉以上,同时大幅度减少了出钢口更换次数,提高了生产作业率。具体而言,改善前出钢口每200炉更换一次,改善后每370炉更换一次,每座转炉计算按10,000炉/年,则每年可减少更换出钢口23支/炉座,更换一支出钢口需要平均时间约90 min,可节约一年一个炉座生产时间缩短2070 min。
5.3. 缩短出钢时间,降低生产周期
在出钢口全寿命周期内,使用更换后的出钢口,出钢时间由平均4分40秒降至平均4分钟(表3)。
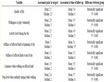
Table 3. Monthly average tapping time of single furnace from June to December, 2021
表3. 2021年6~12月份各炉座月平均出钢时间
出钢时间为钢水由转炉全部倒入钢包所需时间。
5.4. 降低过程温降,降低精炼电耗
出钢时间由平均4分40秒降至平均4分钟后,过程温降(转炉出钢到精炼进站过程温降)由平均95.6℃降低至平均82.3℃,从而使得精炼电耗降低。
以1号精炼各月实际电耗作为计算依据(数据来源为我厂机动设备室工序电耗统计表),2021年1号精炼各月电耗对比如表4。在表4中,1至3月为出钢口改造前数据,4至12月为出钢口改造后数据。项目实施后精炼电耗实际降低值为:34.48 − 29.37 = 5.11 kwh/(t∙钢)。
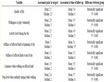
Table 4. Monthly Electricity Consumption Statistics of No. 1 Refining in 2021
表4. 2021年1号精炼月度电耗统计表
综上所述,出钢口首砖分体化改造技术,有效解决了在使用过程中出现的诸多问题,通过首砖分体式设计改造的研究与应用,出钢口侵蚀严重时可以单独更换首砖,作业率大力提升,劳动强度大幅降低,同时保证了职工的人身安全,在同类型转炉出钢口中具有广阔的推广价值和应用前景。
6. 结论
1) 对转炉出钢口首砖进行分体式改造,在首砖和内水口之间加一个碗状台阶;
2) 为减少炉渣对出钢口的侵蚀,通过优化冶炼工艺,渣中∑FeO%含量由20%降至16%;
3) 出钢口使用寿命由原来平均200炉提高到平均370炉,更换碗转只需要3~5 min,每年可节约2070 min/炉座;出钢过程温降(转炉出钢–精炼进站)由平均95.6℃降低至平均82.3℃,精炼炉电耗降低5.11 kwh/(t∙钢)。