1. 引言
目前国内油田在下油管生产作业时,液压扭矩大钳的旋扣工作主要依靠人工控制旋扣状态来实现的。旋扣工作依靠人工监测,记录旋扣压力值,采取这种方式误差较大。由于人工要准确控制旋扣压力,操作人员必须有一定经验和熟练过程才能胜任,否则误操作的概率就比较大 [1] [2] 。现场情况表明,在油管上卸扣过程中,由于上下两根油管不可能完全处于中心线上,常常会发生黏扣现象。这时液压扭矩大钳上扣的压力会远远大于额定上扣压力,而实际作用于油管上面的扭矩却很少。一般的液压扭矩大钳都是简单的压力转换为扭矩,因此不能真正反映出上扣的实际情况,这样就很容易造成上扣质量不合格,导致事故发生。
由于下油管作业时螺纹连接质量的好坏直接影响着油井寿命 [3] 。现场在下油管中,主要靠经验作业,缺乏监测手段,有时使得旋扣扭矩过大,造成应力集中,螺纹胀裂;有时转矩过小,导致连接强度不够,密封不理想。这些都会造成严重后果,带来巨大经济损失。
目前国内油管螺纹作业质量控制在其专业的领域里没有查新到新的相关技术 [4] ,油管螺纹作业质量控制技术处于空白状态。而现有的套管钳螺纹作业质量控制这项技术也处于起步阶段 [5] [6] ,它仅用于套管的下管作业中。该项技术虽然对套管钳进行简单机械改进,但它只能记录套管作业过程中扭矩–时间曲线,不能及时判别旋扣作业的效果;只能作为下管作业完成后,分析作业效果的参考资料。一旦出现作业事故,可以作为追责依据和数据分析的依据,无法解决已经发生的错误。因为它没有智能评定和分析系统,不能及时发现作业中的错误。
大港油田曾经引进过美国威德福公司的进口套管钳,主要是为了解决套管的螺纹连接质量问题。该套管钳由3块颚板组成,与套管接触面积大,在旋扣过程中对套管本体的损伤小;它体积小、重量轻、操作简单、使用方便,在空间小的钻台灵活好用。但这种套管钳与扭矩仪连接时,需内置磁敏式圈数传感器,国产扭矩仪不能与之配套使用 [7] 。而配套的扭矩仪是针对进口的Mode 16~25型和24~50型2种套管钳量身订做的。该扭矩仪是美国20世纪70年代的产品,体积大而重,自身价格及配件价格昂贵,产品现在已停产;原配操作界面为DOS界面而且全部为英文,操作使用非常复杂,不能自动监测,只能手动操作,延长了施工时间。
目前套管钳和油管液压扭矩大钳分属不同的机械结构,但机械原理相似 [8] [9] 。其扭矩值和压力对应关系分别不同,需要通过大量试验数据和对液压大钳增加辅助检测机构,才能完善油管液压大钳扭矩监测仪的智能评定和分析系统。该项目研究成功后,应用液压扭矩大钳转矩及管长检测技术,有效地监测旋合转矩,并对下管作业过程进行管理,对出现的问题及时进行分析、解决,可杜绝油管螺纹旋紧质量的问题发生。
基于此,笔者应用液压扭矩大钳转矩及管长检测技术 [10] [11] [12] [13] [14] ,有效地监测旋合转矩,并对下管作业过程进行管理,对出现的问题及时进行分析、解决,可杜绝套管螺纹松、紧质量的问题。同时,系统还能够有效地监督厂商提供的油管质量,在旋合过程中可及时发现因螺纹配合公差上的质量问题,作为第一手测量数据,作为凭据与套管厂商交涉,可杜绝套管因出厂时质量问题带来的工程事故隐患。
2. 液压扭矩大钳结构改进设计
对液压扭矩大钳进行结构改进设计,主要是在液压钳侧部加装一个脉冲传感器。当液压钳过桥齿轮旋转运动时,传感器便开始计量齿数。由于过桥齿轮的齿数为一定值Z1,且过桥齿轮i1与大齿轮i2的传动比为恒定值i1/i2 = k,大齿轮旋转1周即套管旋合1圈。利用脉冲传感器,通过测量过桥齿轮的齿数,即可得到套管的旋转圈数,形成扭矩–圈数坐标曲线。
通过液压扭矩大钳转矩溢流阀系统,可有效地监测旋合转矩,解决黏扣带来的压力与实际扭矩不符合的问题,并杜绝旋合螺纹旋紧质量的问题。
3. 液压扭矩大钳转矩及管长测量模型
3.1. 转矩测量模型
液压扭矩大钳在旋合过程中靠尾钳销轴承受反转矩,这样就可以利用安装在上的压力传感器(见图1)测出尾钳销轴所承受的压力F,计算出油管的旋合转矩值M:
式中:M为油管的旋合转矩值,N∙m;F为尾钳压力,N;L为从钳头中心到尾钳压力作用线的垂直距离,m。
在测量过程中,从在安装钳尾销轴上辅助的压力传感器,一路信号进入装在钳体上的压力转矩表,供操作者做参考;另一路进入主控系统。
于是,尾钳销轴压力为:
,
式中:P为传感器内部油压,Pa;r为钳尾销轴半径,m。
最后得:
最终形成扭矩–油压坐标曲线。
3.2. 管长测量模型
由于油管长度一般在10 m左右,长距离下直接测量长度不太方便,因此考虑将其转换为对其它物理量的测量。假设有一个已知的固定长度区间,用一块挡板位移一段距离后,恰好能卡住整个油管。这时,当知道了挡板位移的距离,也就能得到油管的长度。而挡板位移的测量,可以通过电机旋转的齿轮编码器来实现。
按上述方案,研制设计油管长度检测系统。该系统为现场油管长度检测装置,其两端由左右动力组件、左右挡板、左右支架及齿条等构成,如图2所示。左右动力组件分别由电机、减速器、齿轮编码器等构成。该装置置于送管机及排管架之间,且让送管机上的上管摆臂摆动时刚好能勾住油管,便于将检测好的油管送上送管机(如图3所示)。测量时,先核定左右挡板距离L0,再将管架上的油管推入本装置中;按动测量按钮,其两端动力组件带动左右挡板移动,卡住油管,由编码器分别记录左右挡板位移L1和L2,便计算出被测油管长度L,并通过屏幕显示出来。
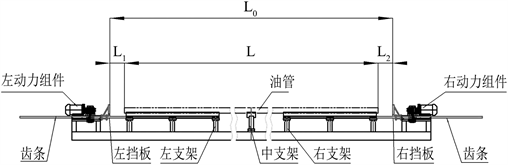
Figure 2. Conception of tubing length detection device
图2. 油管长度检测装置构想图
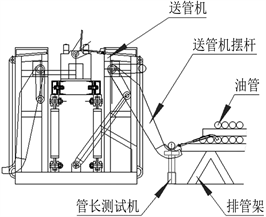
Figure 3. Placement diagram of length measuring device, pipe feeder and pipe rack
图3. 测长装置、送管机及管架放置示意图
4. 检测装置制备
4.1. 油管扭矩检测装置
液压扭矩大钳运转时,位于钳尾座上的高精度扭矩传感器,直接检测主钳旋转上扣时所产生的扭矩值,将产生的扭矩信号传送到下位机扭矩采集卡上,经AD转换后的数字量数据由操作员控制上传的十字操纵杆总成经过通讯电缆传送到电源转换器;由数据转换器转换后的数据传送到上位机便携式电脑,由上位机进行运算并处理。便携式电脑进行参数设置、过程显示、程序控制和相关参数记录。产生实时的扭矩当前值,当达到显示扭矩时,上位机开始作图;当扭矩达到设定的控制扭矩值后,上位机输出控制信号给下位机,控制电磁卸荷阀打开,使液压系统处于溢流状态。此时主钳会自动停止旋转,起到自动控制的效果。如图4所示。
该系统中,液压扭矩大钳由大扭矩摆线油马达驱动,H型手动换向阀与油马达直接匹配,结构紧凑,是目前修井用液压动力钳中较为轻便的一种油管钳。如图5所示。
主钳基本参数:适应范围23/8,27/8,31/2 in油管;额定高档扭矩0.6~1.1 kN∙m;额定低档扭矩1.8~3.0 kN∙m;最大扭矩6.3 kN∙m;额定高档转速100 r/min;额定低档转速30 r/min;开口尺寸95 mm;移运质量105 kg。
背钳基本参数:适应范围23/8,27/8,31/2 in平式及外加厚油管接箍;开口尺寸116 mm;移运质量53 kg。
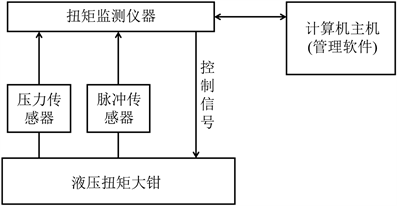
Figure 4. Block diagram of torque monitoring system
图4. 扭矩监测系统框图
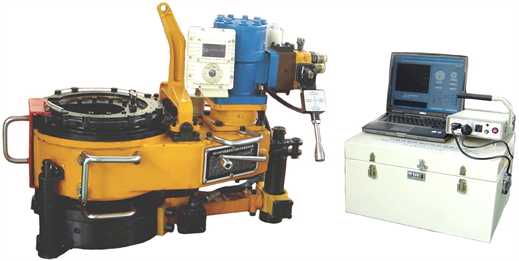
Figure 5. Real picture of torque monitoring system
图5. 扭矩监测系统实物图
扭矩监测仪器采用弹性体扭矩传感器测量扭矩。该传感器是应变式传感器,零点稳定,检测精度高,抗干扰性能强,并由高可靠性电源供电,适用于多种场合全天候恶劣环境和各类腐蚀介质。
与液压动力站上的电磁卸荷阀配合,可实现上扣扭矩自动控制。根据作业工艺要求设置上扣过程参数,管体、接箍参数等。
扭矩仪主要技术参数:供电电压AC220V ± 15%,50/60 Hz;工作电压:DC24V (现场供电);消耗功率:200W Max;扭矩仪量程:6300 N∙m;检测精度 ≤ 1%;卸荷溢流80 L/min;卸荷响应:20 ms;扭矩显示器148 mm × 126 mm × 48 mm。
4.2. 管长检测装置
4.2.1. 装置的机械结构
根据油管长度测量模型,可制备现场油管长度检测装置。图6是油管长度检测装置机械部件设计图,其中动力组件如图7所示。
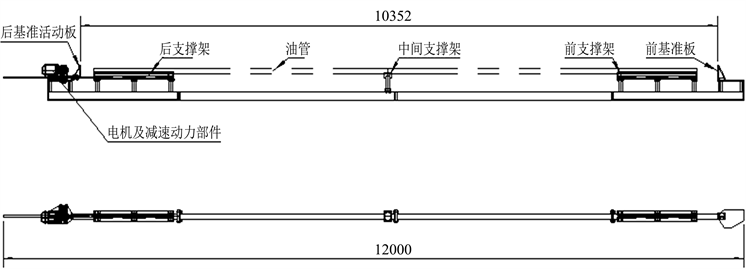
Figure 6. Design drawing of tubing length detection device
图6. 油管长度检测装置设计图
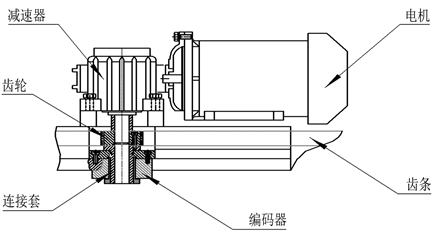
Figure 7. Schematic diagram of power components
图7. 动力组件示意图
4.2.2. 装置的控制模块
油管管长检测装置设计有配套的控制柜,内部为整个油管管长检测装置的控制核心,包括有PLC控制模块、数据显示屏等。其模块组成如图8所示。
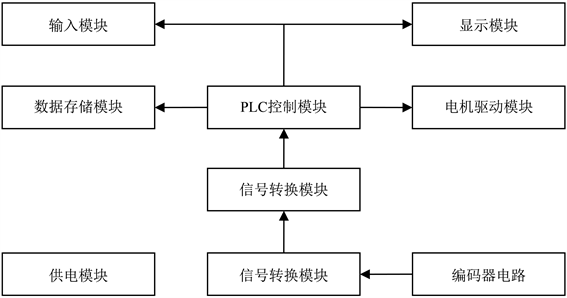
Figure 8. Control part of the circuit module diagram
图8. 控制部分电路模块图
4.2.3. 装置的显示界面
通过程序设计,将测量出的长度数据,在显示屏上显示出来。显示界面包含有:主界面、参数设置、查询界面。
主界面包含的信息有:管长、累计管长、计数、年月日、时分秒,和查询按键。累计数据可手动清零,以便于每次新作业的时候重新统计下管总长度。
5. 关键技术与创新点
5.1. 完成油管扭矩监测系统的研制
该系统可以很直观分析旋扣扭矩质量,有效地监测旋合转矩,并对下管作业过程进行管理,对出现的问题及时进行分析、解决,可杜绝套管螺纹松、紧质量的问题。该系统还能够有效地监督厂商提供的油管质量,在旋合过程中可及时发现因螺纹配合公差上的质量问题,作为第一手测量数据,作为凭据与套管厂商交涉,并且可杜绝套管因出厂时质量问题带来的工程事故隐患。
5.2. 完成油管管长检测装置的研制
通过油管管长检测装置,实现了对每根管长的测量、记录,可以清楚准确知道所下管长的深度,为技术分析提供有效依据。
5.3. 创新点
1) 建立了扭矩–圈数模型,实现了油管扭矩的精确测量。
2) 运用传感器技术,实现了对油管长度的精确测量。