1. 引言
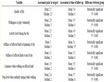
Table 1. Classification of optical films
表1. 光学薄膜分类
光学薄膜根据不同性质及用途,分类的方式也不同,如表1所示。增透膜又称减反射膜,用于降低光学器件表面的反射率,从而提高器件的透射率,作为发展历史最久、应用最广的光学薄膜,对生产实践具有重要意义。在复杂光学系统中,镜片数目众多,若在与空气相邻的表面未镀制增透膜,导致光能量的损失,降低成像亮度。另外镜片表面因反射形成的杂散光到达像面,影响了成像质量。
随着应用需求的不断提升,增透膜的要求随之越来越高,例如在大功率激光系统中,为避免高能量激光破坏光学元件,要求表面的反射率极低。在宽波段探测系统中,为达到提高像平衡、成像质量、探测距离的要求,更宽波段的增透膜需求广泛。宽带增透膜(Broadband Anti-Reflection Coating)广泛应用于光学元件,如透镜、滤光器、激光器和太阳能电池板等。
一般来说,增透膜由多层光学膜层组成,每一层的折射率都不同。在光线垂直入射时,这些薄膜层的厚度和折射率可以调整,以抵消光线的反射。这样就可以实现对宽波段光的最小反射和最大透射。在这个过程中,如果膜层的材料选择不当或制作工艺不当,可能会引起膜层的吸收,导致光线能量的损失,从而影响器件的透射率和性能。宽带增透膜的低损耗特性是指该膜层对光线的吸收很小,能够实现最大程度的光学透射,保证器件的高透过率和高性能。
2. 增透膜制备研究现状
2.1. 增透膜原理
增透膜的工作原理 [1] :对于单层反射膜,在薄膜层厚度为1/4的入射光时,两个相邻的光的光程差异为p,也就是振荡的方向相反,重叠的结果就是没有反射。在这种情况下,反射膜的折射率等于基底的折射率的平方根乘以入射介质的折射率。而单层增透膜只能针对某一波长进行减反射,其他波段的入射光反射率仍然很高,对于某一波段想要达到反射率为零只能镀双层膜或者多层膜来达到目的。一些基底往往需要涂上反射层,例如太阳能电池的原材料硅。宽带增透膜的制备方法和材料选择对其损耗特性影响很大。制备过程中需要精确控制膜层厚度和材料的成分、形貌等,以确保薄膜具有较高的光学透过率和较低的反射率。同时,需要选择合适的材料,如二氧化硅、氧化铝等高折射率材料,以实现较高的光学透过率和较低的损耗。宽带增透膜的低损耗在于可以减少光能的损失,从而提高光学器件的效率和稳定性,特别是对于一些高精度、高要求的光学器件来说,低损耗特性非常重要。
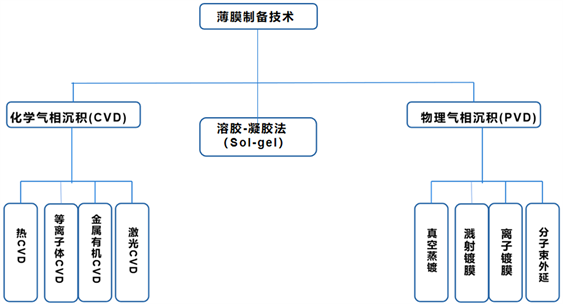
Figure 1. Classification of film preparation technologies
图1. 薄膜制备技术分类
一个典型的例子是在太阳能电池中使用硅,这是通过在硅太阳能电池板的表面生产具有成本效益和可重复的宽膜来实现的。镀上反射膜可以降低透光率,同时增加基底材料对光线的吸收。由于宽带增透膜的结构设计和制备方法,使其能够在一定波长范围内实现高透过率和低反射率,同时保持很低的能量损耗。它不仅可以降低能源成本也能提高能源转换效率 [2] [3] [4] [5] 。为了获得一个均匀的膜层,人们采用不同的制备工艺进行了研究。现在研究的重点也在集中于宽带增透膜的研究与制备。2022年白宇等 [6] 采用MgF2/SiO2堆叠式减反射结构,正面辅以SiO2或MgF2减反射膜,其背面入射处的外量子效率(EQE)明显增加2.35%。采用此方法,可使双玻组件的双面比达到95.16%,对提高双玻组件发电效率十分重要。
2.2. 薄膜制备技术
薄膜制备技术是一种将材料制成薄膜的工艺,广泛应用于半导体、光学、电子、医疗等领域。常见的薄膜制备技术包括:化学气相沉积、溶胶–凝胶法以及物理气相沉积法等,如图1所示为较常见的镀膜工艺分类。不同的薄膜制备技术具有不同的优缺点,需要根据实际需求选择适合的制备技术。
2.2.1. 化学气相沉积
化学气相沉积(Chemical Vapor Deposition,简称CVD)是指通过化学反应在基板表面沉积固态材料的一种表面涂覆技术。其主要特点是利用气相反应物在高温下进行化学反应并沉积在基板表面上,从而形成薄膜。其中通常使用的增透膜制备方法是通过控制沉积的材料和气氛来制备多层膜。常见的方法是在CVD过程中使用多种前体材料,例如SiH4、NH3、N2O和TiCl4等,以产生所需的光学性质。常用来沉积增透膜的方法是热CVD、等离子体增强CVD等。
热CVD是一种CVD方法,利用高温来促进反应物质的化学反应,从而形成薄膜。在热CVD过程中,反应物质被加热到高温(通常在800~1100℃之间),使其发生热化学反应。由于高温可以提高反应速率和扩散速率,因此可以使反应物质在短时间内快速反应,形成薄膜。等离子体增强化学气相沉积(PECVD)是一种利用等离子体激活反应气体并使其沉积在衬底上形成薄膜的技术。PECVD通常在低压下进行,其基本原理是将气体放置在两个电极之间形成放电,从而激发气体分子产生等离子体。等离子体中的离子和自由基与反应气体发生反应并沉积在衬底上,形成薄膜。这种方法通常用于制备硅基薄膜,例如氢化非晶硅薄膜、氮化硅薄膜等。表2为热CVD和等离子体增强CVD在制备成本和生产效率等方面的对比。
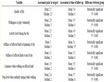
Table 2. Comparison of thermal CVD and PECVD
表2. 热CVD和等离子体增强CVD对比
2012年,Lee Youngseok等 [7] 研究了等离子体增强化学气相沉积系统制备的用于太阳能电池的减反射涂层的SiNX:H薄膜的稳定性。稳定性测试使用各种形式的应力进行,例如长时间的热循环、湿度和紫外线照射。本研究证实了双层增透膜对外部应力是稳定的。
2013年,Erik R. Klobukowski等 [8] 以[[(tBuO)3SiO]2-Ti(OiPr)2]为前驱体。使用单一来源的异金属氧化铝的能力,在500℃下整合。以及将薄膜制造工艺整合到工业装配线在工业化条件下生产AR薄膜的可能性。
2015年,朱登华等 [9] 采用低压化学气相沉积法(LPCVD)在制绒的单晶硅片衬底上制备了B掺杂ZnO (BZO)的透明导电薄膜,研究了B2H6掺杂量、沉积时间对BZO薄膜的微观形貌、导电性能及光学减反性能的影响。本研究还表明在制绒单晶硅片衬底上制备BZO薄膜均呈现“类金字塔”的绒面结构,使得表面平均反射率由15%明显降低至5%左右,表现出优异的光学减反性能。
2020年,Yin Chaoyi等 [10] 采用低温等离子体增强原子层沉积(PEALD)技术提高了紫外(UV)激光器用HfO2/SiO2减反射(AR)薄膜的激光诱导损伤阈值(LIDT),从化学组成、光吸收、表面散射和激光电阻等方面分别研究了前驱体曝光时间对PEALD SiO2薄膜性能的影响和生长温度对PEALD SiO2和HfO2薄膜性能的影响。
2022年,Hang Liangyi等 [11] 基于薄膜材料的折射率特性,提出了一种简单易操作的减反射膜(ARC)设计方法。设计了高透射率、宽带(400~800 nm)、折射率可调的三层单面和双面ARC,其透射率分别为99.2 %和98.5 %。由非化学计量比的氧氮化硅和通过PECVD技术在玻璃衬底上形成的氮化硅薄膜组成。
2023年,Li Zhaoyi等 [12] 采用低压化学气相沉积法制备氮化硅波导具有更低的损耗和更好的工艺重复性。使用类似于铜互连CMOS工艺的雾状花纹方法在8英寸硅片上成功制备了400 nm厚的氮化硅波导,并证明了在1550 nm处的传播损耗仅为0.157 dB/cm,在1580 nm处的传播损耗仅为0.06 dB/cm。
总体来说,热化学气相沉积(CVD)和等离子体增强化学气相沉积(PECVD)都是常用的薄膜制备技术。热CVD在制备高品质膜上具有优势,而等离子体增强CVD则更适合制备复杂化学组成的膜。热CVD更适用于制备高品质的光学、电子、磁性、防腐蚀等膜,而等离子体增强CVD适用于制备包括氮化硅、氧化硅、碳化硅、氟化硅、磷化硅等材料的绝缘膜、导电膜、抗反射膜等。
2.2.2. 溶胶–凝胶法
溶胶–凝胶法(Sol-gel) [13] [14] 的前驱体是高化学活性组分得化合物,在液相下将这些原料均匀混合,并进行水解、缩合化学反应,在溶液中形成稳定的透明溶胶体系,通过提拉、涂覆 [15] 等工艺过程在基体上得到减反射膜。溶胶–凝胶法制膜可以通过低熔融温度、易移动、易反应控制、非常均匀的材料制备、固体制备、成型、老化、干燥、脱水、溶剂控制和组装、老化时间、时间和温度等因素合成,并形成致密的薄膜,制备过程如图2所示。
2010年,刘永生等 [16] 采用溶胶–凝胶技术制备了一种新型的低折射率纳米膜,并对其结构、性能和对电池效率的影响进行了探讨。
2013年,Amita Verma等 [17] 利用旋涂技术在硅(Si)晶片和微滑块玻璃衬底上沉积了溶胶–凝胶法制备的铝(Al)掺杂氧化锌薄膜。薄膜中Al:Zn原子比分别为0.05、0.1、0.2、0.3。薄膜表现出优异的光学透过率(90%),折射率在1.47~1.53之间。薄膜在波长为600 nm时已表现出约3 %的反射率。
2015年,赵松楠等 [18] 以正硅酸乙酯为前驱体,采用酸催化与碱催化溶胶混合的方式调控了溶胶折射率,并配制了双层复合膜所用的两种溶胶,制备出了351 nm处透过率大于99.5%,527 nm透过率大于98%,1053 nm透过率大于98%的三波长增透膜。本研究通过理论模拟与实验相结合的方式研究了以双层膜的方式实现三波长增透的途径。
2018年,Sun Laixi等 [19] 通过氧等离子体处理和溶胶–凝胶镀膜技术相结合的方法,优化涂覆过程中的等离子体处理时间和提拉速率,处理后的FEP薄膜与未处理样品相比,透光率提高了4.7%。在这种情况下,透过率超过99 %,宽波段范围从600~950 nm。
同年,Genghua Yan等 [20] 在钠钙玻璃上制备了顶层折射率为1.12,底层折射率为1.30~1.40的双层增透膜。通过调节制备参数,使峰谷透射率值之间的数值差异逐渐减小,即制备了宽带增透膜。使得双层增透膜的透光率达到99.04%,在300~1200 nm波长范围内平均透光率达到95.49 %。
2020年,Fardo F. M.等 [21] 以正硅酸乙酯和丁氧化钛为前驱体,通过溶胶–凝胶工艺制备了机械稳定、粘附玻璃的双层薄膜。椭偏法测得二氧化钛和二氧化硅钛复合层的折射率分别为2.1和1.7,其物理厚度分别约为65 nm和81 nm。本研究表明可以在设计的可见光光谱中心(550 nm)处获得四分之一波长的光学厚度,透射率提高3.4 %。
2023年,沈斌等 [22] 采用溶胶凝胶法制备得到以正丙醇锆和正硅酸乙酯为前驱体的ZrO2和SiO2溶胶,通过TFCalc光学薄膜软件模拟了ZrO2/SiO2三层“宽M型”基频二倍频减反膜并使用提拉法制备得到了该均匀膜层。三层减反膜在527 nm和1053 nm处的透过率约为99.5%,且透过率大于99%的波长范围均超过150 nm。经热处理后的膜层表面均方根粗糙度为1.34 nm,表面平整性良好;并运用1-on-1激光损伤阈值测试方法测得该减反膜的零几率激光损伤阈值达到36.8 J∙cm−2 (1064 nm,, 10.7 ns)。
同年,Manna Srikrishna等 [23] 使用溶胶–凝胶浸涂法,利用异丙醇钛(TTIP)、八水合氧氯化锆(ZOC)和嵌段共聚物P123 (表面活性剂)的稳定溶胶制造涂层,然后在80℃/2小时内干燥,并在400℃/小时内加热。涂层玻璃在700至1100纳米波长范围内的平均透射率增加了3%,这是因为其RI值比基底低,同时涂层具有化学和热稳定性。
溶胶–凝胶法在制备增透膜方面有着广泛的应用。相较于其他方法,溶胶凝胶法具有许多优点,如制备过程简单,成本低廉,对于不同的基材有很好的适应性,并且能够制备大面积、均匀的薄膜。溶胶–凝胶法在增透膜的应用中,最常用的是二氧化硅(SiO2)和氧化铟锡(ITO)薄膜。制备的薄膜具有优异的光学性能,能够满足各种光电器件的需求,如太阳能电池、LED灯、显示器等。此外,还有许多其他的应用,如防反射涂层、光学滤波器、光学镜片、光学涂层等。
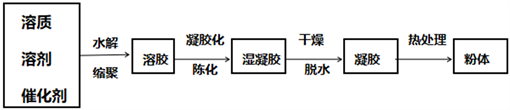
Figure 2. Sol-gel preparation process
图2. 溶胶–凝胶技术制备过程
2.2.3. 物理气相沉积
物理气相沉积(Physical Vapor Deposition,简称PVD)是一种常用的薄膜制备技术,它是利用物理过程,通过将固体材料升华成气态,让其在真空条件下沉积到基底表面,形成所需的薄膜结构。PVD技术包括多种不同的方法,如真空蒸镀、磁控溅射等。
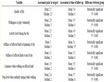
Table 3. Comparison of three commonly used physical vapour deposition methods
表3. 三种常用物理气相沉积法对比
真空蒸镀 [24] 是一种利用电子束、阴极材料、高频电源等设备在高真空环境下将阴极材料加热蒸发,然后沉积在基材表面形成薄膜的技术。其基本工艺流程包括:真空抽气、加热、蒸发、沉积等步骤。磁控溅射 [25] 是一种利用高能离子轰击靶材表面产生金属离子的方法,将离子沉积在基底上制备薄膜的技术。在磁控溅射过程中,通过加热靶材,靶材表面的金属原子被高能粒子轰击并发生电离,形成离子态金属原子,经过磁场的聚焦和加速作用,将离子束引向基底表面,然后在表面沉积形成薄膜。离子镀膜 [26] 是一种利用离子源将物质离子化,并利用离子动能将其沉积在基底表面的表面处理技术。通常采用的离子源有离子枪和离子束源,利用高能离子轰击目标物质表面,使其离子化并沉积在基底表面,形成一层均匀、致密、粘附力强的薄膜。如表3为三种常用的物理气相沉积方法从制备成本、生产效率等方面的对比。
2013年,Li Minghua等 [27] 对采用常规工艺制备的1.56 × 1.56 mm2 mc-Si太阳电池,利用电子束蒸发技术在标准SiNx:H上沉积一层SiO2进行了实验。对灰黄色、紫色、深蓝色和绿色细胞进行了300~1100 nm的半球反射率和I~V测量。着色SiO2/SiNx:H DARC电池的效率与标准SiNx:H浅蓝电池相当,显示了着色电池在工业应用中的潜力。
2014年,阙立志等 [28] 以QK3为基底设计了一种宽带可见光区增透膜(增透波长0.4~0.8 μm),工艺实现采用了电子束蒸发物理气相沉积的方法,薄膜材料仅含有TiO2和SiO2,并分别作为高低折射率材料。利用Edinburgh光谱仪对双面镀制该膜系样品的透过率进行测量,结果表明平均透过率达97.73%。环境测试表明,薄膜具有良好的稳定性和牢固度。
2015年,Bruynooghe S等 [29] 采用将反应离子刻蚀SiO2薄膜制备的亚波长结构作为最外层与磁控溅射制备的传统薄膜材料构成的多层系统相结合的方法,针对BK7玻璃基片,设计了一种混合涂层,以最小化其在400~900 nm光谱范围内的残余反射率。本研究还表明,由于纳米结构表面的特性,复合涂层具有很好的全向性,实现了较低的残余反射率。
2016年,孙亚军等 [30] 以电子束物理气相沉积的方法在CaF2基底上设计了一种近红外宽带增透膜,这种薄膜具有良好的附着力和牢固度,可以应用于对产品可靠性要求较高的环境中。
2018年,Nancy Sharma等 [31] 采用电子束蒸发技术沉积,使用Filmstar TM软件对单层和多层增透膜的单层厚度进行了优化。利用各种光谱技术如紫外-可见分光光度计和Gonio分光光度计对涂层的性能进行了表征。单层增透膜和多层增透膜的峰值透过率分别为96.41 %和94.09 %。
2019年,Adem Yenisoy等 [32] 采用等离子体辅助电子束蒸发技术在工艺参数优化良好的硅基片上镀制了由氧化铝(Al2O3)和锗(Ge)层分别作为低和高折射率材料的多层增透膜。硅基增透膜是第一种在中波红外(MWIR)波段以最少的层数在1400 nm宽光谱范围内实现了99.7%以上的平均透过率的增透膜。
2022年,Ruud Christian J等 [33] 基于溅射的牺牲致孔剂工艺来制备多层纳米多孔SiO2涂层,其折射率可调至neff = 1.11。利用这种方法本研究展示了一种具有出色的广角AR性能(可见光谱中单边平均反射率从正入射时的0.2%到40˚时的0.7%不等),良好的附着力和有前途的环境耐久性的阶梯状双层AR涂层。
同年,Addie Ali J等 [34] 利用磁控溅射技术合成一种非晶氮化碳CNx薄膜,作为用于c-Si太阳能电池的新型双功能增透膜(ARC)。通过测量反射率、光电转换效率和外部量子效率,研究了CNx薄膜的性能。在550 nm波长处的最小反射率为0.3%,在宽波长范围内实现的外部量子效率超过90%。
在制备增透膜方面,真空蒸镀、磁控溅射和离子镀膜都有广泛的应用。真空蒸镀通常用于金属氧化物薄膜的制备,具有较高的膜层致密性和较好的光学性能,但是制备过程较为复杂且生产效率较低。磁控溅射通常用于制备金属和合金材料的薄膜,具有高质量和较高的生产效率,但膜层致密性较差,不适合制备高质量的增透膜。离子镀膜则可以制备高品质的增透膜,但是设备成本高且制备过程复杂。在应用领域上,除了都适用的光学器件和电子期间外,真空蒸镀更适用于太阳能电池,磁控溅射更适用于能源器件,而离子镀膜更适用于摄像头镀膜。
制备薄膜是一项重要的技术,化学气相沉积、溶胶–凝胶法和物理气相沉积法是三种常见的增透膜制备技术。虽然它们都可以制备高质量的薄膜,但它们之间存在差异,包括制备成本、生产效率和薄膜质量等方面。因此,在选择合适的薄膜制备技术时,需要仔细考虑这些因素。如表4对这三种技术进行详细对比分析。
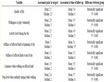
Table 4. Comparison of three film preparation techniques
表4. 三种薄膜制备技术对比
3. 总结与展望
宽带增透膜是一种可以在广泛的波长范围内实现高透过率的光学薄膜,因此在许多领域中得到广泛应用,如太阳能电池、光学显示器件、光通信设备等。目前,宽带增透膜的制备技术已经取得了一定的进展和突破。常用的制备宽带增透膜的方法是采用多层膜设计,通过选择不同材料以及不同层厚度来实现。利用化学气相沉积、物理气相沉积、溶胶–凝胶等技术制备多层膜,可以实现对不同波长范围的透过率进行调控。
近年来,新型材料的发现和新工艺的应用也在宽带增透膜制备方面带来了重要的进展。例如,金属有机化合物、无机有机杂化材料、钙钛矿等材料的使用和发展,有望为制备更高效、更稳定的宽带增透膜提供新的途径。同时,利用仿生学原理和纳米技术制备的新型表面纹理结构也在增强光学器件的性能方面展示了潜在的优势。随着新材料、新工艺和新技术的不断涌现,宽带增透膜的制备将会越来越高效和可靠,透过率和反射率的优化也将更为精细和广泛。同时,随着对光学器件精度的要求不断提高,对宽带增透膜在性能稳定性、可靠性、耐久性方面的研究也将更为深入。
基金项目
项目资助信息:海南省自然科学基金高层次人才项目(622RC671)、海南省自然科学基金项目(120MS031)和国家自然科学基金项目(62174046,62064004,61964007,61864002)。
NOTES
*通讯作者。