1. 引言
在航空航天领域,SiCp/Al复合材料由于其较高的比强度、比刚度和摩擦学性能好等特点得到了越来越多的应用。然而,由于SiC颗粒与铝合金基体相异的材料特性和制备工艺的限制,使得复合材料存在孔洞间隙、界面缺陷等问题,考虑到SiCp/Al材料的应用领域的高要求,因此,如何进一步提升复合材料的综合性能逐渐成为研究人员的关注热点 [1] [2] [3] 。深冷技术在材料制备工艺 [4] 和辅助加工领域 [5] 的优点已经被广泛讨论与研究,黄珂 [6] 等开展了不同温度和不同应变速率下的超低温单轴拉伸试验,研究发现2195锂铝合金在超低温条件下延伸率和强度均有较大提升,且具有更大的稳定塑性变形区间。Wang [7] 等通过一系列力学测试和微观结构图片,综合分析了深冷处理对SiCp-AA2009人工时效后屈服强度和极限抗拉强度的增强效果。王运 [8] 等对航空Al7050合金进行了准静态压缩试验和高温霍普金森压缩试验,拟合得到了材料的JC本构模型,验证发现该模型对材料流动行为预测具有良好的准确性。Sun [9] 等通过TEP、SEM和TEM系统研究了深冷处理对SiCp/2009Al的析出特性的影响,分析了其对材料的力学性能强化机理。李建明 [10] 通过低温拉伸试验与低温霍普金森压缩试验建立了Inconel 718的低温Johnson Cook本构模型,并建立有限元仿真模型对切削形态与应力温度场进行了分析。然而,当前论文中关于超低温环境下SiCp/Al材料的低温流动行为与本构模型等未有研究,因此本文通过开展不同温度、不同应变率下的低温拉伸、扭转试验测试,研究该材料的低温力学性能,基于试验结果拟合SiCp/Al的超低温有限元仿真模型,并通过超低温铣削实验对模型有效性进行验证。
2. 低温力学试验
2.1. 试验材料
本文中的试验材料为通过粉末冶金法制备试验所需20% vol SiCp/2024 Al复合材料,即基体金属为2024铝合金,增强相为平均直径10 μm的SiC颗粒,体积分数为20%,材料的主要化学成分见表1,材料表面经抛光清洁后,在扫描电镜下观察得到SEM图像如图1所示,材料常温下的物理参数见表2。
2.2. 试验设计
开展SiCp/Al复合材料在温度范围−196℃、−100℃和20℃下的准静态拉伸试验,以及在0.001 s−1、0.005 s−1、0.01 s−1、0.1 s−1不同应变率条件下的超低温拉伸测试,设计试件的初始直径为5 mm,标距段长度为30 mm。为了获取更宽程度的应力三轴度范围,进行在−196℃超低温下缺口试件的准静态拉伸试验选择缺口半径为R = 2、R = 3与R = 9的试件,名义直径为6 mm,名义长度为69 mm,以及圆棒扭转试验,试件名义直径为6 mm,名义长度35 mm,为保证试验结果的有效性,每组参数重复三次,超低温拉伸试验现场如图2所示。
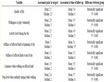
Table 1. Main chemical compositions of SiCp/2024 Al (wt%)
表1. SiCp/2024 Al复合材料的主要化学成分(质量分数,%)
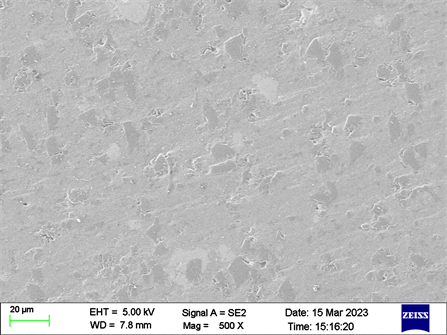
Figure 1. SEM of surface morphology of SiCp/2024Al material
图1. SiCp/2024 Al材料的表面形貌图像
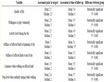
Table 2. Mechanical and physical properties of SiCp/2024 Al (T4)
表2. SiCp/2024 Al复合材料的机械物理性能(T4态)
3. Johnson Cook模型建立
Johnson Cook本构模型包含了应变强化、应变率强化与热软化效应,该模型是纯粹的唯象模型,认为三个因素为相互独立的微观机制,其具体形式为 [11] :
(1)
式中,A、B、C、m、n为材料参数,
为流动应力,
为真实应变,
为无量纲等效塑性应变率,
为参考应变率,
为无量纲化温度,T为试验温度,
为参考温度,一般为室温或试验研究温度,
为材料熔点。
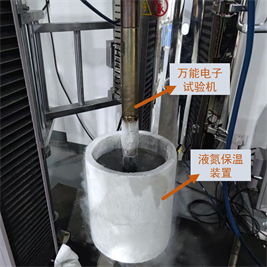
Figure 2. Cryogenic tensile testing equipment
图2. 超低温拉伸试验装置
Johnson Cook断裂准是从应力三轴度对材料断裂应变的影响入手,考虑温度和应变率的影响效应,其表达式为:
(2)
式中,
、
、
、
、
为材料参数,分别代表应力三轴度、应变率和温度对断裂应变的影响系数,
为应力三轴度,静水压力
。
3.1. Johnson Cook本构关系模型
本文研究SiCp/Al复合材料的超低温JC模型,因此定义参考温度
,同时定义参考应变率为
,结合不同温度和不同应变下试验结果进行本构关系模型部分的拟合。
在参考温度和参考应变率情况下,此时的本构模型可以简化为:
(3)
根据超低温准静态拉伸试验曲线获得材料屈服强度
,确定参数
,代入式(3)后对公式两端进行移项并取自然对数,可以得到:
(4)
根据准静态试验数据通过最小二乘法进行拟合得到
、
。
对于参考温度下不同应变率试验,JC本构模型简化为:
(5)
改写后可以得到:
(6)
选择一系列应力应变值,根据不同应变率下的试验数据,代入式(6)计算后并拟合得到斜率即为参数
。
对于参考应变率下不同温度试验,JC本构模型简化为:
(7)
同样的,选择一系列应力应变值,根据不同温度下的准静态试验数据,代入式(7)计算后并拟合得到指数即为参数
。
将上述拟合得到的材料参数代入Johnson Cook本构关系模型的数学表达式中,可以得到:
(8)
为了验证拟合SiCp/Al的超低温JC本构模型的有效性,将模型预测得到的流动应力与不同温度下试验结果进行比对,结果如图3所示,可以看到,JC模型能够较为准确的预测材料的真实应力。

Figure 3. Comparison of SiCp/Al true stresses with predicted values at different temperatures
图3. 不同温度下SiCp/Al真实应力与预测值对比
3.2. Johnson Cook断裂准则模型
在参考温度和参考应变率情况下,此时的断裂准则模型可以简化为:
(9)
应力三轴度影响系数D1~D3可以结合参考温度下的准静态拉伸试验与缺口圆棒准静态拉伸试验和扭转试验共同拟合得到,分别回收试验结束后断裂试件并对断面直径进行测量,计算材料的断裂应变,公式定义为:
(10)
基于三组试验不同应力三轴度下的断裂应变值,根据式(9)拟合曲线结果,可以得到模型参数分别为
,
,
。
在参考温度不同应变率情况下,断裂准则模型可以改写为:
(11)
将相应数据带入式(11)计算后,拟合得到斜率即为
。
同样的,在参考应变率不同温度下,断裂准则模型可以改写为:
(12)
将相应数据带入式(12)计算后,拟合得到斜率即为
。
将上述拟合得到材料参数代入Johnson Cook断裂准则模型的数学表达式中,可以得到:
(13)
4. SiCp/Al等效均质切削仿真模型建立
4.1. 二维简化铣削模型
根据本文所使用的两刃立铣刀结构特点,可以将侧铣加工的三维铣削过程转化为二维正交切削,转化过程如图4所示,从图中可以看到,铣刀一个刀刃的切削过程可以近似等效为正交切削,刀刃切入时,切削层厚度最大,切出时,切削厚度近似于零,即切削层的厚度在实时变化,采用以直代曲的思想将最大切削弧长作为切削长度,以直角三角形形状等效切削层,便可建立如图5所示的变厚度等效斜坡切削模型 [12] 。
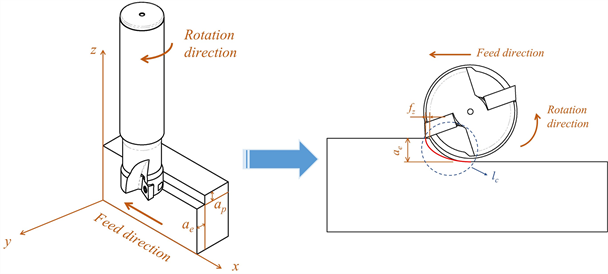
Figure 4. Side milling converted to 2D orthogonal cutting
图4. 侧铣加工转化为二维正交切削
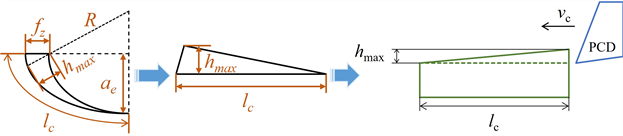
Figure 5. Equivalent slope cutting modeling
图5. 等效斜坡切削模型建立
斜坡模型中最大切削厚度
与切削弧长
计算公式如下:
(14)
(15)
式中,R为铣刀半径,
为径向切深,
为每齿进给量。
4.2. 有限元仿真设置
基于本文构建的SiCp/Al复合材料的超低温Johnson Cook模型和二维等效斜坡工件切削模型,使用商业有限元软件ABAQUS进行切削仿真的研究。根据均匀化理论,假设铝基体和SiC颗粒组成具有周期性排列的细观结构,且材料在边界层面受远场均匀应力的作用,那么SiCp/Al就可以等效为若干微单元结构通过周期排列而成,这样相对宏观应力分析单个胞元内部的作用可以忽略 [13] ,本文研究中将SiCp/Al整体作为宏观的均质材料进行研究,因此在仿真软件中建立等效二维均质切削模型,如图6所示。
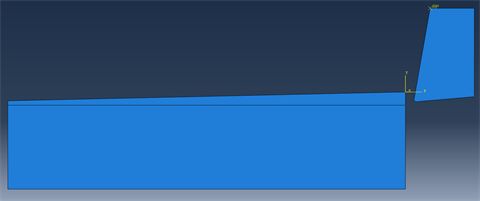
Figure 6. Finite element cutting model of equivalent slope workpiece
图6. 等效斜坡工件有限元切削模型
实验使用的铣刀刀片选择金刚石PCD材料,该材料具有超高硬度与耐磨、耐热等的优异性能,在复合材料与高强金属加工领域广泛使用,本文使用的PCD刀片前角10˚,后角5˚,刃尖角半径2 μm,刀具物理参数见表3。由于刀具材料强度远大于工件材料,为减小计算量,在仿真模型中将刀具定义为刚体。
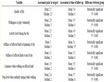
Table 3. Mechanical and physical properties of PCD
表3. 刀具材料物理性能
划分网格时,刀具与工件均选择CPE4RT作为网格单元类型,设置温度–位移耦合分析,该网格类型是一种四节点平面应变缩减积分单元,并且引入了沙漏控制。工件单元在切削表面密集,未参与切削加工部分稀疏,刀具单元从刀尖向内部逐渐变疏,由此减少计算耗时,网格划分结果如图7所示。
在仿真切削运动过程时,刀具表面与工件发生接触,工件材料内部也发生自接触,因此设定相互作用中,刀具表面为主接触面,工件表面与切削层部分为从接触面,定义接触类型为温度–位移耦合的显式动力分析,而工件与刀具之间的摩擦接触分别定义为切向的依据罚函数的摩擦,以及硬接触的法向摩擦。
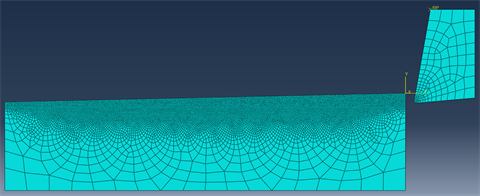
Figure 7. Equivalent slope workpiece finite element model meshing
图7. 等效斜坡工件有限元模型网格划分
对于仿真模拟低温切削加工过程而言,热对流边界的对流换热系数的设置至关重要,将直接影响到仿真结果的准确性。通过查阅文献,发现有学者研究了氮的状态对对流换热系数h的影响 [14] ,结果表明,液氮从喷头喷射至材料表面时,经历了液态到气态的转变,过程中对流换热系数随着液氮的温度升高而减小,当氮为液态时,即温度在77 K附近,h = 75,000 W/(m2K),在液氮与材料温差在160 K时,氮从液态转换为气态,此时对流换热系数急剧下降至15,000 W/(m2K),当对流边界温差较小时,对流换热系数在1500 W/(m2K)左右。
超低温立式铣床的主轴在切削加工前需要预冷至−160℃左右,铣刀的端面与刀片安装位置顶部均有液氮喷射孔,此时经过刀尖的液氮为气液共存态,综合考量后,设定刀具单元表面的对流换热系数h = 20,000 W/(m2K),刀具预定义初始温度场123 K。
由于液氮喷射至不同材料表面时的对流情况与材料本身的物理性质有关,对于SiCp/Al复合材料而言,其表面仍然是基体金属2024Al,因此本文引用文献中对于2024铝合金拉深成形时液氮冷却的仿真设置 [15] ,即h = 1000 W/(m2K),工件预定义初始温度场293 K。
设定模型的边界条件时,为模拟实际切削过程,使工件底部完全固定,限制各方向的位移,防止发生平移或旋转,对于刀具刚体赋予水平移动速度,该速度即为铣削实验中的切削速度,从而更加符合实际加工时的工况情境。
4.3. SiCp/Al超低温切削仿真模型的实验验证
4.3.1. 超低温铣削实验设置
为了验证所建立的SiCp/Al超低温切削仿真模型的有效性,开展超低温铣削实验进行实验验证。斜坡切削模型中切削层的最大厚度
与工艺参数中每齿进给量
和径向切深的大小
相关,因此,设置如下加工参数:固定切削速度与径向切深,以不同每齿进给量进行铣削实验,测量铣削力的值与仿真模型刀具单元反作用力输出结果对比,从而验证所建立有限元仿真模型的准确性,铣削参数的设置见表4。
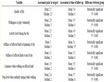
Table 4. Cryogenic milling experimental processing parameters
表4. 超低温铣削实验加工参数
铣削加工的工件尺寸为20 mm × 20 mm × 10 mm,在CVM 600超低温立式铣床上进行液氮辅助冷却超低温铣削加工,工件为20%体积分数的SiCp/Al复合材料,通过Kistler 9139AA测力计进行铣削力的实时测量,加工现场如图8所示。
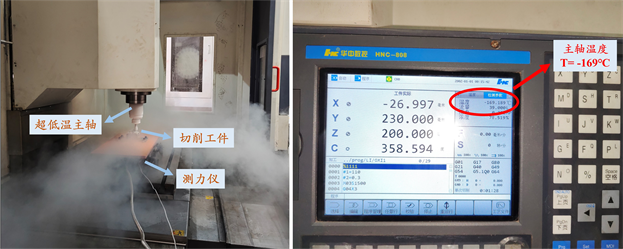
Figure 8. Liquid nitrogen assisted cooling cryogenic milling processing site
图8. 液氮辅助冷却超低温铣削加工现场
4.3.2. 铣削力结果对比验证
如图9所示,以fz = 0.05 mm/z实验数据为例,由铣削力测得结果,经过低通10 hz滤波后再进行零点漂移处理,取稳定铣削采集段的平均值作为铣削力大小,即该组Fx = 4.35 N,Fy = 2.45 N。
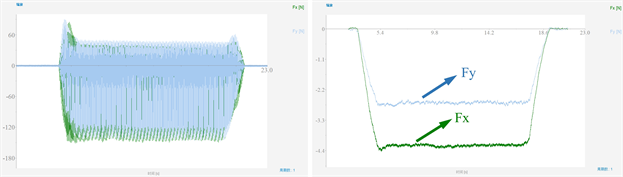
Figure 9. Milling force measurement results of cryogenic machining experiment
图9. 超低温加工实验铣削力测量结果
当每齿进给量fz = 0.05 mm/z时,仿真模型中最大厚度hmax = 10 μm,在刀具刚体上设置参考点,其支反力数据即为铣削力模拟数值,在ABAQUS中绘制其随时间变化曲线结果如图10所示,可以看到,二维等效斜坡模型对一个刀刃的切削过程进行模拟,铣削力随时间变化逐渐变小,将数据点导出至Excel后,分别取其全过程的平均值作为仿真铣削力的模拟结果,其中,Fx= 4.12 N,Fy = 2.24 N。
同样的处理方式,获得五组实验测量数据与仿真模拟数值后,再分别计算其合铣削力结果,对比如图11所示,将各组的结果进行对比可以发现,仿真模型能够准确地对超低温加工铣削力进行模拟,以上结果证明了本文基于拟合得到的低温Johnson Cook模型所建立的等效斜坡切削加工模型的有效性。

Figure 10. Finite element cutting model simulation milling force results
图10. 有限元切削模型仿真铣削力结果
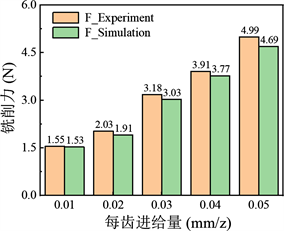
Figure 11. Comparison of simulated and experimental milling forces at different fz
图11. 不同每齿进给量下仿真与试验铣削力对比
4.4. SiCp/Al低温铣削仿真结果
4.4.1. 超低温铣削应力场仿真
根据所建立的等效斜坡工件超低温铣削模型,以每齿进给量fz = 0.05 mm/z为例,分析切屑形成过程中的应力场分布,仿真结果如图12所示。可以看到,由于超低温对材料的强化作用,切削过程中最大应力达到了1635 MPa,开始切削时,应力主要集中在刀尖部分,顺着刀具进给方向沿第一变形区拓展,接着,由于前刀面与切屑发生挤压与摩擦作用,使得应力集中部分向第二变形区移动,切削继续进行,工件表面发生裂纹失效,证明此时所受应力超过了材料断裂极值,最后形成三角形状切屑脱离工件表面。
4.4.2. 超低温铣削温度场仿真
同样的,以每齿进给量fz = 0.05 mm/z的有限元模型为例,分析超低温辅助加工技术对铣削过程温度场的影响,仿真结果如图13所示。
可以看到,切削开始时,由于液氮的降温效果,工件温度由293 K从表面向内部迅速降低,从刀尖部分温度场放大图可以发现,由于刀具的初始预定义场(即机床主轴的预冷)比工件低得多,因此,工件的切削区域温度比其余部分要低,而刀尖温度则略有升高,随之切削继续进行,工件温度逐渐降低至与刀具温度相同,切削区域的温度稳定在110 K左右,而已加工表面由于逐渐远离液氮喷射区域,温度降低速率下降,温度在130 K左右。综上所述,可以看到液氮冷却对工件材料与刀具以及切削区域的降温效果极为优异,因此使得超低温加工后的表面质量显著提升,同时也大幅降低了刀具磨损。
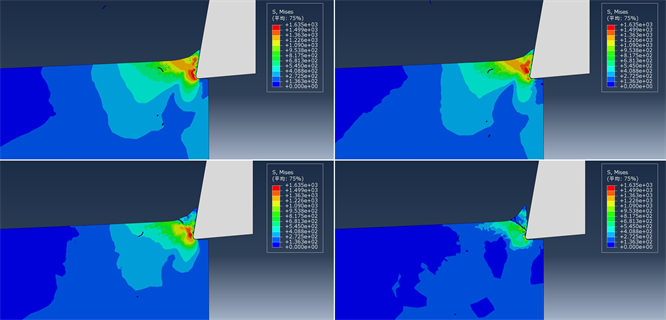
Figure 12. Stress field analysis of cryogenic milling process
图12. 超低温铣削过程应力场分析
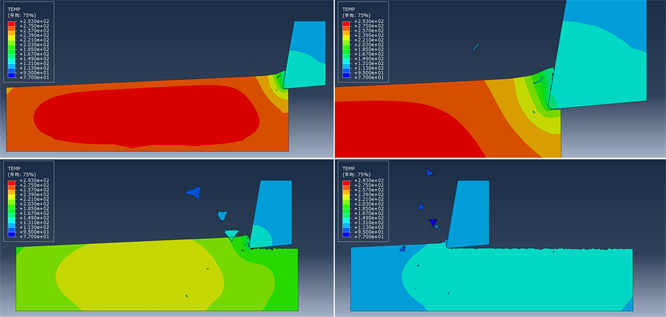
Figure 13. Temperature field analysis of cryogenic milling process (Unit: K)
图13. 超低温铣削过程温度场分析(单位:K)
5. 结论
(1) 本文基于Johnson Cook模型参数的获取方式,针对20% SiCp/Al复合材料进行了一系列的超低温力学性能试验,根据试验数据拟合构建了材料的超低温本构关系模型与断裂准则模型,利用不同温度下的材料流变曲线数据,对本构模型的预测性进行了验证。
(2) 从三维侧铣加工的机理出发,分析了刀具与工件之间的几何关系,从而建立等效二维斜坡工件切削模型,利用商业有限元软件Abaqus对SiCp/Al的超低温铣削过程进行了仿真模拟,结合超低温铣削加工实验测得的铣削力与仿真模拟输出铣削力进行了比对,验证了所建立模型的准确性。
(3) 利用所建立的有限元仿真模型,对材料的铣削过程中应力场与温度场变化进行了分析,发现由于低温环境对工件材料的强化效应,铣削过程中最大应力达到了1635 MPa;同时液氮介质具有极为优异的冷却效能,能够有效地降低刀具、工件与切削区域温度,这对工件表面加工质量与刀具磨损都是有益的。
基金项目
国家自然科学基金青年项目,SiCp/Al复合材料超低温磨削去除机理与表面完整性主动调控策略研究(52105470)。