1. 引言
背面钝化、背面金属局域接触以减少背面复合是提升太阳电池转换效率(h)的必要途径。PERC (Passivated Emitter and Rear Cell)电池 [1] 是一种背面采用介质膜钝化,背面金属电极与硅衬底(Si)之间进行局域接触的电池结构,相较常规(Al-BSF)太阳电池有如下优点:1) 钝化介质膜介于金属和p型硅(p-Si)之间避免两者直接接触,降低表面复合速率;2) 有效地避免电池片翘曲,减少破损和降低成本;3) 介质膜具有背反射作用,光子在背表面反射回前表面过程中还有一次被吸收的机会,使在硅能隙附近波长部分的内量子效率增加。通过背面钝化,电极局域接触,转换效率可提高0.5%以上 [2] 。
激光是对背面介质膜开口实现局域电极接触制备PERC太阳电池的主要手段,有两种实现方式,一是烧蚀介质膜 [3] ,二是激光烧结接触(LFC) [2] 。但是激光过程会损伤硅基体,不利于太阳电池转换效率提升。光刻是制备PERC的另一途径,但不论是光刻还是激光技术,相对于产业化丝网印刷技术来说,都需要新增价格高昂的设备,且工序繁复,控制要求高。
为便于产业化应用及成本控制,该文以成本低廉、技术成熟的丝网印刷方式作为研究、制备背面局域接触电极及电池的技术手段,监测分析串联电阻(Rs),并研究降低串联电阻的途径和方向。需要指出的是,除了电极局域接触外,背面抛光、背面钝化介质膜、背面局域电极接触区域尺寸和间距等参数均是影响PERC太阳电池性能的重要变量,但该文主要目的是研究降低丝网印刷制备局域背电极接触电池串联电阻的途径和方法,对背表面状态及钝化介质膜未作优化,钝化介质膜选用常规钝化减反射氮化硅(SiNx)膜。为与背表面有良好抛光及钝化的PERC太阳电池相区别,该文中将未经良好钝化的背钝化电极局域接触太阳电池简称为LCC (Local Contact Cell)。
2. 研究方式
串联电阻对太阳电池的输出特性有重要意义,监测串联电阻对太阳电池结构、工艺的设计、控制和优化具有重要意义,光照条件下晶体硅太阳电池串联电阻测试方式有单曲线法和双曲线法。
1) 单曲线法测试串联电阻
晶体硅太阳电池可用单二极管直流模式 [4] 表示,如式(1)所示:
(1)
式中,q——电子电荷;k——玻尔兹曼常数;T——绝对温度;Rsh——并联电阻;Rs——串联电阻;n——太阳电池二极管品质因子;ID——太阳电池反向漏电流;IL——光生电流。
由式(1),在忽略高阶无穷小条件下,太阳电池并联电阻及串联电阻分别为太阳电池电流(I)-电压(V)曲线上当V → 0及I → 0处的斜率 [5] ,如式(2)所示:
(2)
因而,并联电阻越大、串联电阻越小,太阳电池I-V曲线越接近矩形,则填充因子(FF)越大,其他参数不变的情况下越有利于提高转换效率。由此,并联电阻、串联电阻是影响填充因子和最大输出功率(Pm)的直接因素 [6] ,所谓单曲线法就是在标准条件(AM1.5,25˚C、1000 W/m2)下测试太阳电池I-V曲线,根据式(2)可得串联电阻。
2) 不同辐照强度双曲线法测试串联电阻
标准条件下测试太阳电池短路电流(Isc)、开路电压(Voc)及I-V曲线,曲线上最大功率点(Pm)电流、电压为Im、Vm;在光强E (AM1.5,25℃,入射功率Pin < 1000 W/m2)下测得短路电流及开路电压Isc,E,Voc,E,测试曲线上某一点(IE、VE)处太阳电池pn结的电流与标准光强下最高输出点处的结电流相等,则两状态下太阳电池的结电压亦相同 [7] ,如式(3)所示:
(3)
忽略光电导对串联电阻的影响,由式(3)得:
(4)
不同辐照强度双曲线法的测试结果表征了太阳电池在最佳工作点Pm附近时的串联电阻,对于太阳电池转换效率(h)及填充因子(FF)的衡量至关重要,如式(5)、(6)所示为转换效率及填充因子定义表达式:
(5)
(6)
其中A为太阳电池面积,所以该文采用德国Berger测试仪分别在标准测试条件及500 W/m2光照入射功率下测试LCC的输出参数及I-V曲线,选取满足条件的点,由式(4)求解得串联电阻。
3. 实验及结果讨论
3.1. 实验流程
以156 mm × 156 mm的p型多晶硅(mc,p-Si)为衬底,电阻率约为1.5 W∙cm。首先进行表面清洗,使前表面织构形成具有减反射效果的结构,烘干后高温磷扩散使前表面薄层反型形成发射极区(n-Si),扩散层方块电阻平均为85 W/□,二次清洗去除表面的磷硅玻璃并去边,烘干后在前表面用等离子增强化学气相沉积(PECVD)法沉积氮化硅(SiNx)膜(膜厚约80 nm,折射率约2.18)。然后分成两组,如图1所示,一组是Al-BSF太阳电池,为参考组;另一组是LCC,在背表面采用PECVD沉积SiNx膜后丝网印刷银(Ag),烘干后在背表面丝网印刷Ag并烧结,完成LCC制备。用德国Berger测试仪测试两组太阳电池片在标准条件下的输出参数开路电压(Voc)、短路电流(Isc)、填充因子(FF)及转换效率(h),分析串联电阻(Rs)。
3.2. 结果及讨论
Al-BSF太阳电池及LCC标准测试条件下输出参数统计平均值如表1所示,Al-BSF太阳电池转换效率为17.44%,由于串联电阻过大,LCC的转换效率为8.95%,Al-BSF太阳电池串联电阻平均为2.74 mW,LCC串联电阻为21.34 mW,是Al-BSF太阳电池的8倍。串联电阻过高,不仅造成LCC的短路电流过小,为7.792 A,而且会降低LCC的填充因子,仅为48.20%,比Al-BSF太阳电池相对降低38.68%,LCC实现的转换效率仅为Al-BSF太阳电池的51.32%。从表中可以看出,LCC的开路电压为579.7 mV,比Al-BSF低44.9 mV (相对低7.19%),其中LCC背面未进行良好抛光是原因之一,背面用SiNx做钝化介质膜无法取得良好钝化效果是原因之二。

Figure 1. Manufacturing process for local contact p-Si cells (LCC)
图1. 丝网印刷p-Si局域接触太阳电池制备流程
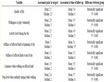
Table 1. Mean value for parameters of both reference cells (Al-BSF) and (LCC)
表1. 两组不同结构太阳电池I-V测试参数统计平均值
从制备流程(图1)可知,Al-BSF太阳电池及LCC之间的背面电极接触方式不同,串联电阻的差异由背面电极造成。表1中,LCC背面局域接触电极形成机理如下,Ag中含有对SiNx介质膜具有良好刻蚀性的玻璃料,一定温度下玻璃料刻蚀SiNx使Ag与p-Si接触形成合金,实现电极制备。串联电阻高可能由以下原因所致:1) 高温烧结过程中LCC背表面朝下放置在传送履带上,温度低于前表面,浆料刻蚀性能减弱使SiNx介质膜成为接触阻挡层,从而提高串联电阻;2) 由于重力作用,Ag中的玻璃料下沉,削弱对SiNx膜的刻蚀使之成为阻挡层,从而提高串联电阻;3) 常规Ag适用于与前表面磷扩散的n-Si发射区形成欧姆电极,而LCC背表面为p-Si,Ag在与p-Si合金形成电极过程中可能会由于接触区掺杂类型的改变而造成失配。
为能够具体分析LCC串联电阻高的原因,该文首先将表1中LCC进行二次烧结,为保证Ag中的玻璃料能充分刻蚀背面SiNx膜,在第二次烧结过程中将LCC背表面朝上,而前表面朝下放置在烧结传送履带上。二次烧结后串联电阻降低幅度极小,仅降低约2 mW,但转换效率减小到4.26%。由此可见,二次烧结后LCC的串联电阻改善很小,但转换效率降低了52.40%,这是因为二次烧结造成前表面电极过烧而损坏发射极,导致漏电过大,故而转换效率急剧减小,开路电压降低为342.2 mV。可见,丝网印刷制备LCC电池时,Ag中玻璃料对背面SiNx的刻蚀性能或者刻蚀程度不是串联电阻大的原因,可排除上述原因(1)和(2)。
为深入研究分析上述可能原因(3),该文在Ag中掺入具有一定刻蚀性的铝浆料(Al),Al在元素周期表中为III-A组元素,最外层电子数为3,Si为IV-A组元素,Al在半导体Si中扩散掺杂后,多数载流子为空穴,是p型杂质。试验测试发现,在Ag中进行Al掺杂后,串联电阻减小,极大地改善LCC输出参数,可见,背局域接触电极Ag中进行Al掺杂可有效改善Ag与p-Si之间接触的匹配性。为深入了解Al掺杂量对串联电阻的影响,该文对LCC背面局域接触电极的Ag进行不同程度的Al掺杂,同时采用双曲线法监测串联电阻,如图2所示。
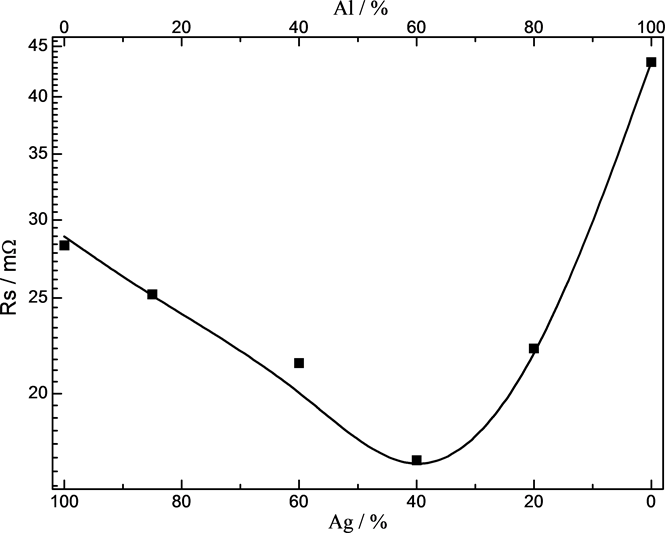
Figure 2. Influence of aluminum (Al) dopant on the series resistance (Rs) of the LCC
图2. 串联电阻随Al掺杂量的变化趋势
可见,随着Ag中Al掺杂量的增大,串联电阻先减小后增大:当Al掺杂量为0%时,Rs = 28.27 mW;随着Ag中Al掺杂量的逐渐增加,串联电阻逐渐减小,当Al掺杂量为60%时串联电阻达到最小值17.11 mW;此后,随着Al掺杂量的继续增加,串联电阻快速增大,当Al掺杂量为100%时,串联电阻为43.38 mW。
Al掺杂量小于60%,Ag中掺入Al后,在高温烧结过程中介质膜被刻蚀后形成混合金属(Ag、Al)与p-Si直接接触的通道,与Si共同合金形成电极。在这个过程中,Al还起到如下作用:1) Al向p-Si内扩散,使电极接触的区域掺杂形成p+-Si,与衬底p-Si构成高低结,形成局域背场,降低串联电阻的同时有效提高电池开路电压;2) Al掺杂后,p+-Si中空穴载流子浓度高于p-Si,降低电池串联电阻;3) Al掺杂的Ag电极,与p-Si接触形成电极,改善Ag与p-Si之间相互接触的性能,减小接触电阻,降低LCC的串联电阻。
但是,如果对Ag进行过量掺杂反而不利于串联电阻的降低,当Al掺杂量超过60%,串联电阻随着Al掺杂量的逐渐增大而快速增大,这有两个方面的因素:1) Al对SiNx介质膜的刻蚀性比Ag弱,随着Al掺杂量不断提高,部分SiNx介质膜介于金属与p-Si之间成为接触阻挡层,极大的提高了串联电阻;2) Ag电阻率约为1.65 × 10−10 W∙cm,Al电阻率约为2.83 × 10−10 W∙cm,相同形状及尺寸情况下,电极电阻随着Al掺杂量的提高而增大,串联电阻增大。
值得指出的是,Ag进行Al掺杂后,在丝网印刷区域形成LCC局域背接触电极过程中,Al向p-Si内扩散,使电极接触区域实现掺杂形成p+-Si,与p-Si共同构成高低结形成局域背场,有效提高LCC的开路电压,与文献 [2] 结论一致,如图3(a)所示。随着Al掺杂量的不断增加,p+-Si层的掺杂浓度不断提高,激发的局域背场效果更好,因而开路电压随Al掺杂量的不断增加而增大,当Al掺杂量为0%时开路电压为579.4 mV,Al掺杂量为100%时开路电压为597.4 mV,比掺杂前提高18 mV;若掺杂量较低(≤60%),开路电压随着Al掺杂量的逐渐增加明显提高;若掺杂量较高(≥60%),随着Al掺杂量逐渐增加,开路电压变化趋于平缓,改变幅度较小。

Figure 3. Open circuit voltage (Voc) (a); fill factor (FF) (b); and conversion efficiency (h) (c) of LCC for different Al dopant
图3. 开路电压(Voc) (a);填充因子(FF) (b)及转换效率(h) (c)随Al掺杂量的变化
由式(5)、(6)知,单位面积太阳电池开路电压、短路电流、填充因子及转换效率之间的相互关系为h = Voc × Isc × FF/Pin,Al掺杂对开路电压的改善有利于提高转换效率。由式(2)知,串联电阻是影响填充因子的直接因素,填充因子随Al掺杂量变化如图3(b)所示,当掺杂量为60%时填充因子及转换效率达到最大值,此时,转换效率为11.57%,较未掺杂时(h = 8.98%)提高2.59%。过高(≥60%)掺杂量虽有利于提高LCC的开路电压,但由于串联电阻增大,填充因子减小,转换效率减小,如图3(c)所示。
由此,丝网印刷制备LCC时,与p-Si接触的金属电极Ag中掺入适量的p型杂质Al有助于改善串联电阻,同时在高温烧结过程中Al向p-Si内侧扩散形成重掺杂p+-Si区,形成局域背场提高开路电压,改善转换效率。但Al电阻率大,且对介质膜的刻蚀性弱,Al掺杂过量会提高串联电阻,降低转换效率。
4. 结论
该文以丝网印刷方式制备LCC,以双曲线方法监测串联电阻、研究降低串联电阻及提高转换效率的方法和途径。在Ag中掺入适量的p型杂质Al,有助于降低串联电阻、提高开路电压和转换效率。当Al掺杂量达到60%时,串联电阻降低11 mW,开路电压提高18 mV,转换效率提高2.59%。若掺杂量较小,串联电阻随着掺杂量增大而减小,填充因子增加,转换效率不断提高;但若掺杂量过高,由于Al电阻率较高,且对介质膜刻蚀性能弱,则串联电阻随着掺杂量增加而快速增大,填充因子减小,虽然开路电压能够得到进一步改善,但转换效率却不断减小。
NOTES
*通讯作者。