1. 背景
我国海上油田平台的生产水外排渠道有两种:一种是生产水处理达标后排海;另一种是生产水处理达标后注入到需要注入水开发的油藏地层。海上油气田产量的逐年增加,伴随着海上平台生产水处理量不断增大,对常规的生产水处理工艺发起挑战,海上平台目前使用的生产水除油技术主要以隔油气浮过滤组合技术和水力旋流技术为主 [1],两种技术有其各自优劣势。
隔油气浮过滤组合技术优势是物料适用性强、除油效果稳定、能高效去除乳化油、各设备易单独调控和改造。劣势一是总投资大、总占地空间太大,不适合可用空间小的平台;二是电耗大、运行运费高;
水力旋流技术优势是占地空间小、投资及运行费用较低、分离快速、操作简单,对15 μm以上油滴的分离效率达90%。劣势一是为维持高效分离区间的旋流场强度,其操作弹性小;二是由于旋流分离原理的限制,无法分离10 μm以下的乳化油的要求。
基于海上油田生产水处理现状,结合新材料及流体力学技术的发展,采用分级分步处理的思路,开发了亲疏水异性组合纤维束物理强化破乳为核心的聚结除油工艺技术,将游离态的分散油、悬浮油及乳化油通过分级分步的方法进行快速高效分离。该技术设备占地面积小、操作简单、节能环保、快速高效,有着较好的应用前景。但对于聚结除油技术在海上油田的应用研究仍需不断评价、深入、优化 [2]。
2. 聚结除油装置简介及运行存在问题
2.1. 聚结除油装置简介
聚结除油装置采用模块化设计 [3],包括一级进口整流分布器模组、二级粗粒化模组、三级改性波纹强化沉降模组、四级纳米改性分离模组,将所有模组通过工艺手段整合在立式容器中,该工艺优化了平台生产水处理流程,由斜板 + 气浮两级处理可缩减为一级处理,既保证了水处理效果,也节省了装置的占地面积。
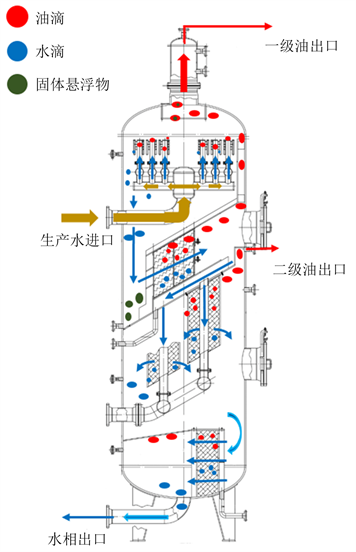
Figure 1. Schematic diagram of fluid flow during unit operation
图1. 装置运行流体流动示意图
聚结除油装置运行时,装置内流体流动示意图见图1。其中,棕黄色为生产水,红色为油相,蓝色为水相。一级集油腔排放比例1%~3% (1 m3/h~3 m3/h),预计1000 ppm降至200 ppm左右(每小时集油约80 L);二级集油腔排放比例0.5%~1% (0.5 m3/h~1 m3/h),预计200 ppm左降至50 ppm左右(每小时集油约18 L)。
聚结除油装置反洗时,为保证反洗效率,通入压力应不小于0.6 MPa的氮气,通入时长根据现场反洗情况来定。在来液含油物性(粘度小于1000 mPa∙s;密度 < 0.95 mg/L)非重质粘度油品时,氮气通入方式为间歇性通入,时间间隔为1分钟或0.5分钟。当来液品质较差,有堵死纤维床层的风险时,应缩短反洗周期。
2.2. 装置运行存在问题
1) 装置高频次反洗
自海上油田某平台生产水处理系统扩容改造完成后,经调试聚结除油装置投入运行。但由于油田油品性质属高粘重质稠油(密度955 kg/m3),生产分离器水相出口(聚结除油装置入口)油含量长期高于2000 mg/L,甚至超过3000 mg/L,为保证出口水质,需要对聚结除油装置频繁反洗,给平台操作人员增加工作强度,同时产生的大量反洗水给平台污水罐、污水泵等设备带来压力。为保证处理效果,聚结除油装置不同处理量下反洗频次见表1。
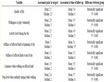
Table 1. Coalescence degreasing unit backwashing cycle
表1. 聚结除油装置反洗周期
2) 装置出口伴有含油絮团
因进液水质指标高于装置入口设计值,同时由于地层采出液与各类水处理药剂的综合作用所产生含油絮团 [4],导致反洗周期较短。含油絮团基本形态见图2,絮团不呈现连续油膜或球形油滴形状,表现为表面粗糙的不规则团状结构,而絮团内的多孔结构为原油提供了大量附着点位。此类含油絮团形成主要原因如下:
① 原油为高粘重质稠油,油品密度高达955 kg/m3,聚结除油装置出水口离四级纳米改性分离模组较近,四级纳米改性分离模组二次捕集后释放的油滴未充分沉降,同时受模组表层及内部含油絮团扰动,部分上浮、部分被出水夹带。
② 聚结除油装置四级纳米改性分离模组内含油絮团,逐渐累积、充满、脱落,絮团在紧凑空间内上浮困难,四级纳米改性分离模组设计为深度分离功能,其强化沉降功能较弱,导致部分含油絮团被夹带。
③ 絮状物流动性差,导致在四级纳米改性分离模组腔体内累积,部分气泡推动絮状物随水相排出,造成出口含油波动性超标。

Figure 2. Basic morphology of oil floc in fourth stage module
图2. 水相出口含油絮团基本形态
3. 工艺优化及评价
针对海上油田某平台新增生产水处理系统所反映的问题,计划从聚结除油装置入手,以设备改造为主,处理药剂浓度调整为辅,两方面共同开展优化聚结除油工艺,满足平台生产需求,具体如下:
3.1. 装备结构优化
1) 将聚结除油装置的四级纳米改性分离模组进行调整改造,将具备深度分离的纤维模块见图3更换为具备快速沉降功能的强化模块见图4。
2) 通过三级改性波纹强化沉降模组压力表口引入气相吹脱管线,紧贴四级纳米改性分离模组进口布置,设备运行时,利用作业平台现有氮气(纯气相,非溶气水),间歇性吹脱存留在强化模块内的含油絮团;同时在四级纳米改性分离模组盖板下方100 mm处加装伞状收油槽,收集到的油通过四级纳米改性分离模组压力表口排出见图5。
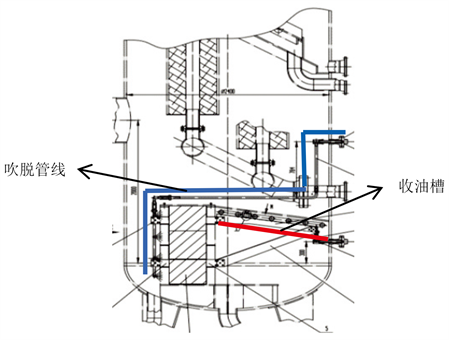
Figure 5. Schematic diagram of fourth stage module modification
图5. 四级模组改造示意图
3.2. 工艺评价及药剂优化
为了验证优化后模组的处理效果,制造模拟四级纳米改性分离模组小试装备,在聚结除油装置三级改性波纹强化沉降模组出口(四级纳米改性分离模组入口)接入小试设备,开展为期13天现场试验,同时调整水处理药剂BHQ08及BHQ133的浓度。
在药剂调整优化前,聚结除油工艺水处理药剂浓度BHQ08为30 mg/L,BHQ133为10 mg/L,为使聚结除油工艺处理效果达到最佳,调整两种水处理药剂的浓度,使其达到最优使用浓度,由表2可以看出,不同药剂浓度下小试装备出口水质情况,因此处理药剂的最优浓度BHQ08为15 mg/L,BHQ133为15 mg/L。
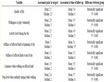
Table 2. Outlet water quality of small-scale test equipment with different reagent concentrations
表2. 不同药剂浓度小试装备出口水质情况
注:BHQ08为反向破乳剂,BHQ133为清水剂。
将两种处理药剂浓度调至在15 mg/L后,对小试装备、聚结除油装置进行数据检测,取样点分别设置在聚结除油装置入口、聚结除油装置出口,小试装备入口、小试装备出口,对四个取样点进行取样化验,由图6可以看出,聚结除油装置入口来液性质不稳定,水中含油量超出装置设计能力,最高水中含油为3409 mg/L,平均水中含油为2944 mg/L,经未优化改造的聚结除油装置处理后,聚结除油装置出口平均水中含油为94 mg/L,处理效果欠佳,经优化后的小试装备和处理药剂共同作用下,小试装备入口平均水中含油为137 mg/L,小试装备出口油含量平均值在30 mg/L左右,满足生产需要。

Figure 6. Comparison diagram of oil content in water at each position of small-scale test
图6. 小试试验各位置水中含油对比图
4. 优化后的应用效果
完成聚结除油装置优化改造工作后,恢复生产处理流程,处理药剂BHQ08浓度设定为15 mg/L,处理药剂BHQ133浓度设定为15 mg/L,调试运行45天,通过监测不同流量下的聚结除油装置进出口水中含油量以及反洗周期的变化,对聚结除油装置优化后的效果进行再评估 [5]。
依照流量的变化,整个调试运行过程可分三个阶段:
1) 第一阶段:处理流量170 m3/h,聚结除油装置在此阶段调试运行15天,入口平均水中含油为2815 mg/L,出口平均水中含油为39.5 mg/L,反洗周期13天。
2) 第二阶段:处理流量200 m3/h,聚结除油装置在此阶段调试运行15天,入口平均水中含油为2799 mg/L,出口平均水中含油为44.3 mg/L,反洗周期10天。
3) 第三阶段:处理流量230 m3/h,聚结除油装置在此阶段调试运行15天,入口平均水中含油为2803 mg/L,出口平均水中含油为49.8 mg/L,反洗周期9天。
综上所述,由表3和图7可以看出,在不同流量下,聚结除油装置在改造后,反洗周期显著增长;入口平均水中含油相差无几,出口平均水中含油由94 mg/L降至44.6 mg/L。
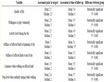
Table 3. Comparison of backwashing cycles before and after modification of coalescence degreasing unit
表3. 聚结除油装置改造前后反洗周期对比
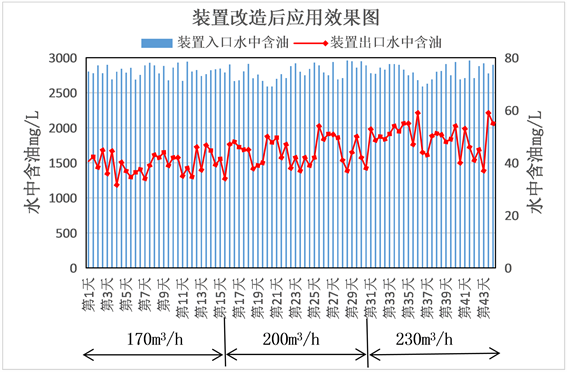
Figure 7. Application effect drawing after device modification
图7. 装置改造后应用效果图
5. 结论
由于海上油田“高含水”以及平台作业空间受限等因素,聚结除油工艺应运而生,聚结除油装置在应用过程中,存在高频次反洗、处理效果不理想的问题,通过对聚结除油装置结构的优化改造,更换了四级模组的功能模块,加装气相吹脱管线、收油槽;同时优化了处理药剂浓度,使聚结除油装置达到处理要求。
1) 将四级纳米改性分离模组中纤维模块更换为强化模块,突出四级模组的快速沉降功能。
2) 经现场试验验证,处理药剂BHQ08和BHQ133最优浓度均为15 mg/L,生产水处理效果达到最优。
3) 在额定处理量230 m3/h运行情况下,聚结除油装置反洗频次由1次/1天降到1次/9天,减轻了操作人员的作业任务。
4) 在聚结除油装置入口水中含油为2900 mg/L左右时,出口平均水中含油由94 mg/L降到44.6 mg/L,平均除油效率达到98.4。