1. 引言
锂离子电池自诞生以来,电极材料的研发和制造技术发展迅速。锂离子电池在手机、笔记本电脑、音响产品、电动工具、备用电源和汽车电源等领域的应用得以实现。据报道,锂电池市场在2020年价值342亿美元,预计在2027年将达到875亿美元。未来10年,随着锂离子电池应用领域的扩展,市场对锂离子电池的需求越来越大,锂离子电池将会应用到更多的领域。目前商业化的锂离子电池主要采用石墨作为负极,石墨的充放电效率高、导电性能良好、易于加工、质量轻、体积变化小、储量丰富。不过,石墨的理论比容量低也是其不可逃避的弊端,约为372 mAh/g [1] ,所以需开发更高能量密度的电极新材料。
硅的采用极大地提高了锂电池负极的比容量,其理论比容量能达到4200 mAh/g [2] [3] ,且硅具有电位平台较高,低温性能优良,成本较低,无毒无污染,安全性好等优点 [4] 。因此,硅被看作最具发展潜力的负极材料。但是硅在完全锂化后体积膨胀率高达300%,造成硅材料的退化,降低循环稳定性 [5] 。同时,活性层颗粒表面会形成一层SEI膜(Solid Electrolyte Interphase),在充放电过程中反复破裂和生长不能够稳定下来,进而导致容量损失、阻抗增加。此外,硅材料的电导率和离子扩散系数较低,使得锂离子难以高效地在活性材料中扩散,从而降低其倍率性能和容量利用率,这些因素严重制约了硅基材料的商业化应用。目前已经有大量的科研工作者针对这些问题进行了研究,其中包括纳米化、复合化和薄膜化等,这些策略都有助于提高锂电池的循环寿命 [6] [7] [8] 。碳化硅复合电极是针对硅循环稳定性差、石墨比容量低提出的有效解决方案 [9] [10] 。将石墨颗粒与硅颗粒有效结合制备成碳化硅颗粒,可以将不同材料的优点整合,其中,硅可以贡献高比容量,而石墨作为载体,可以缓冲硅锂化时的体积膨胀,并弥补硅的低导电率。这样可以有效保持负极良好的导电性,还能缓冲硅颗粒在循环过程中发生的破坏。锂化时巨大的体积膨胀会使硅颗粒破裂,脱锂时体积收缩会使硅颗粒与其他颗粒失去电接触,从而无法参与电化学反应,导致活性物质不可逆损耗 [11] 。同时,巨大的体积膨胀使得活性颗粒和SEI层之间机械失配,促进颗粒表面和SEI层产生裂纹,在电解液中露出新鲜的活性材料,生成新的SEI层消耗大量的Li+和电解液,从而导致容量损失和阻抗增加 [12] 。SEI形成和裂纹之间的这种正反馈会导致电极逐渐退化。
当下,快速充电是锂电池研究的热点之一。在日常生活中,比如手机充电、电动汽车充电,人们对充电速度提出了更高的需求。但是,较快的充电速率会引起锂离子浓度在厚度上不均匀分布,可能会导致锂离子在电极外层浓度高,靠近活性层和集流体界面的浓度低。本论文基于所提出的物理模型和原位测量系统,分别在0.1C (10小时完全充满)和0.2C (5小时完全充满)的充电倍率下,进一步分析不同充电倍率对碳化硅复合电极在电化学循环中对力学性能的影响。
2. 实验设定
2.1. 原位测试系统
图1展示了本工作中原位测量系统的示意图,设计了碳化硅复合电极作为工作电极。将组装好的电池放入手套箱中12 h,以确保电极完全被电解液浸湿。测量系统主要由模型电池、CCD相机、图像采集电脑三部分组成,如图1所示,调整好CCD相机的拍摄位置、角度和焦距,打开电脑的Camera Panel软件,设置每隔3分钟拍摄一张图片,原位拍摄该模型电池在电化学循环过程中碳化硅复合电极的弯曲变形过程,采集前五个电化学循环的变形图片。
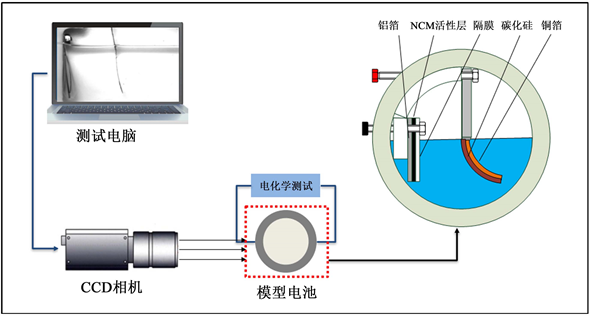
Figure 1. Lithium battery electrode in-situ test system
图1. 锂电池电极原位测试系统
2.2. 电化学测试
在室温下,将模型电池固定在补充光源下,电化学测试在充放电仪(NEWARE)中进行,设置为恒流充放电,电压设置范围为2.0 V~4.2 V,设置充电倍率分别为0.1C (10小时完全充满)和0.2C (5小时完全充满),相应的电流可计算分别为206.3 μA和412.6 μA。经过前期的实验观察发现当充电状态大于40%时,电极变形过大会触碰到模型电池壁面影响实验结果。因此,本文中实验充电状态SOC选择40%,即每个电化学循环分别充放电4小时,每个充放电之间静置3分钟,重复五个循环采集相关数据。
3. 建立模型
3.1. 碳化硅电极物理模型
力学分析为了解电池电极的工作机理提供了一种方法。图2(a)为实验中双层悬臂梁电极的几何形状,通过将活性层粘接在集流体上形成双层悬臂梁。
和
分别表示电极的活性层和集流体的厚度。随着锂离子不断嵌入活性层碳化硅中,引起活性层的体积发生膨胀,而集流体铜箔则抑制了这种体积的变化,从而导致双层电极发生弯曲变形,如图2(b)所示。建立坐标系,厚度方向与z轴一致,界面在x-y平面上,锂离子沿厚度方向从活性层的外表面嵌入和脱出。
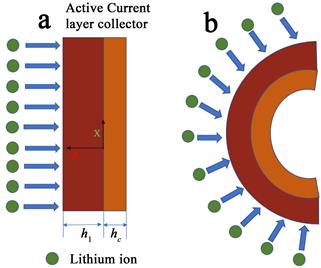
Figure 2. Structure diagram of silicon carbide composite electrode
图2. 碳化硅复合电极结构示意图
这里,x-y平面上的应变可以表示为:
(1)
式中,
为坐标z = 0处的平面内应变,
表示曲率,
表示电极的伸长。虽然复合电极的结构是复杂的,此处我们假设它是各向同性和完全弹性的。当电极以相对较小的充电速率进行电化学循环时,不管浓度在厚度方向上的梯度如何,可以假定浓度c是恒定的。电极的本构方程可表示为:
(2)
式(3.2)中,E1(c)为电极活性层的杨氏模量,随锂离子浓度变化,Ω为偏摩尔体积,−1/3E1Ωc为活性层中由扩散引起的应力。总的应力和弯矩平衡方程可表示为:
(3)
经化简计算,得到面内应变
的表达式:
(4)
边同除以
,令
,
,可得:
(5)
求解可以得到模量比
的表达式为:
(6)
根据一元二次方程求根公式,即可得到式(6)模量比RE关于曲率、电极尺寸参数和锂离子浓度的表达式。在第四循环过程中选取SOC0%、10%、20%、30%、40%、30%、20%、10%、0%八个点,并用测厚仪测量指定状态下的电极厚度。通过CCD相机实时拍摄记录电化学循环过程中的电极的弯曲变形过程,并利用图像处理软件GetData获取相应的曲率参数。由上述公式可以得到碳化硅复合电极的杨氏模量的变化过程,再结合式(4)和式(2),可以得到电化学循环过程中的应力变化过程。
3.2. 浓度梯度下的物理模型
如图3所示为碳化硅复合电极分别在0.1C和0.2C充电倍率下的在第四循环充电状态达到40%的弯曲变形。在充电过程中,随着锂离子不断嵌入到碳化硅活性层中,导致活性层体积发生膨胀,而集流体铜箔则抑制了这种体积的变化,从而导致双层电极发生弯曲变形。随着锂化程度的增加,进而导致电极的变形越来越大,最终达到图中所示的设置充电状态40%的最大弯曲变形。同时从图中可以看出,在相同的充放电状态下,较高倍率下的电极弯曲程度相对较大。0.2C充电倍率下会导致锂离子在电极外层(靠近电解液一侧)浓度较高,靠近活性层和集流体结合处界面的浓度较低。因此,针对0.2C充电倍率,建立物理模型时需要考虑到锂离子在电极厚度方向上有浓度梯度的问题。
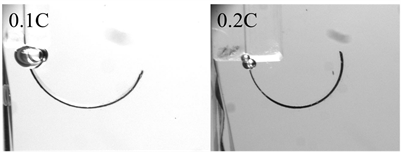
Figure 3. The bending deformation of silicon carbide composite electrode at 0.1C and 0.2C charge rate
图3. 碳化硅复合电极在0.1C和0.2C充电倍率下的弯曲变形
由式(2)和式(3)可以得出
和
的表达式为:
(7)
(8)
其中:
(9)
(10)
(11)
式(4.1)、(4.2)中,在高倍率下浓度不再是常数,而是一个关于z的函数。初步假设浓度c沿电极厚度方向呈线性关系的浓度梯度,即
。
将
代入式(4.1),可得:
(12)
其中:由式(2)和式(3)可以得出
和
的表达式为:
(13)
式(12)经化简可得曲率
表达式为:
(12)
(13)
将公式
代入式(8),可得:
(14)
式(14)经化简可得应变
表达式为:式(12)经化简可得曲率
表达式为:
(15)
(16)
4. 结果与讨论
4.1. 不同充放电倍率下的参数对比
4.1.1. 不同充放电倍率下的电压演化规律
图4所示为碳化硅负极分别在0.1C和0.2C充电倍率下,前五个循环中电压随时间的变化过程。锂化过程电压升高,相反脱锂过程电压降低。由图可知,在0.1C充电倍率下,其理论充放电时间为40 h,而实际充放电时间约为30 h,充放电效率为75%。在0.2C充电倍率下,其理论充放电时间为20 h,而实际充放电时间约为18 h,充放电效率为90%。在0.2C倍率下的库伦效率更高,即前五个循环该充电倍率下总的电化学性能更好。此外,在0.2C倍率下有较稳定的电压平台,约为4 V。因为在0.1C充放电倍率下,其稳定的电压平台形成较慢,而在0.2C下较快形成稳定的电压平台。本实验中前五个循环总的充放电效率0.2C优于0.1C。但从第五个循环开始,0.2C充放电倍率下的碳化硅电极的充放电容量相比在0.1C充放电倍率下开始明显衰减。在0.2C下,碳化硅电极在第五个循环的容量骤减是因为较大的弯曲变形在实验后期会加剧电极的机械损伤。
(a)
(b)
Figure 4. The voltage of silicon carbide anode changes with time at 0.1C and 0.2C charging rates
图4. 碳化硅负极在0.1C和0.2C充电倍率下电压随时间的变化
4.1.2. 电化学循环过程中的变形演化过程
图5所示为0.1C和0.2C充电倍率下碳化硅负极各个循环的最大和最小曲率的变化过程。可以发现除了第一循环以外,其余循环的最大曲率最小曲率呈线性上升趋势,最小曲率以较小的斜率线性上升,而最大曲率以较大的斜率线性上升。这可能是由于经过初次锂化脱锂后,第二到第五循环的碳化硅结构较稳定,最小曲率的上升可能主要由不完全脱锂引起;而第三到第五循环可能由于碳化硅产生损伤,导致最大曲率上升的幅度减小。第一循环脱锂后相比锂化前的曲率变化最大,可能是由于初次锂化脱锂引起碳化硅结构参数变化较大、锂离子残留较多以及不可逆副反应产生的影响等。
各个循环的最大曲率和最小曲率整体是呈上升趋势,最大曲率和最小曲率在第三循环后趋于稳定进入平台期,但最大曲率仍然以微小的变化略有上升。此外,可以发现第五个循环的最大曲率有较小的降低现象,可能是因为在前面的循环过程中电极出现了损伤,导致在第五个循环充电过程中没有达到预初设定的充电状态值。初次循环引起碳化硅结构参数的变化,但之后碳化硅结构趋于稳定,使得后续锂化过程的最大曲率增量基本相同。而0.1C充电倍率下的曲率变化则有显著区别,0.1C倍率下曲率无平台期,整体始终稳步上升。不同充电倍率下曲率变化的差异与锂离子在碳化硅中的浓度分布有关。
(a)
(b)
Figure 5. The curvature of silicon carbide anode changes with time at 0.1C and 0.2C charging rates.
图5. 碳化硅负极在0.1C和0.2C充电倍率下曲率随时间的变化
4.2. 不同充放电倍率下的力学性能对比
4.2.1. 模型系数识别
对于0.2C充电倍率下物理模型的表达式,需对其待定系数a、b进行识别,才可得到曲率
和应变
的解析式。以第四循环充电过程的实验数据为例,根据式(13)对待定系数a、b进行拟合求解。将已知参数代入
表达式,可得:
(17)
将已知参数代入式(13)即可得到式(18),用最小二乘法对式(4.10)进行求解,得出a = 26.83,b = ‒1.33,其中残差和平方为1.04 × 10‒5。将式(18)表示为
,将a、b数值代入
,将拟合值
与原始值Z对比,可以发现误差很小,如图6所示。
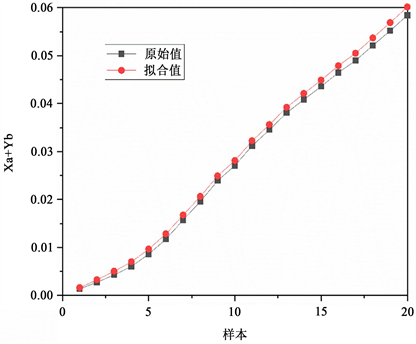
Figure 6. Error analysis of model fitting results
图6. 模型拟合结果误差分析
将a、b值代入式(13)和(15),即可得出在0.2C充电倍率下曲率
和应变
的变化情况。将曲率和应变代入式(2)和(6),可求出相应的杨氏模量和应力。
(18)
4.2.2. 碳化硅复合电极杨氏模量演化
由式(5)可以得到电极杨氏模量与曲率、电极结构参数和充电状态之间的代数关系,其中集流体杨氏模量为117 GPa。结合式(6),即可得到碳化硅复合电极在0.1C和0.2C充电倍率下第四循环中杨氏模量随充电状态的变化趋势,如图7所示。这里得到的杨氏模量考虑到了孔隙率、体积膨胀率和电极断裂等因素的影响,是整个复合电极的平均值。从实验结果可以看出,在0.1C充电倍率下,随着锂离子的不断嵌入,在SOC0%至SOC25%阶段,杨氏模量呈明显的递增趋势,从5.6 GPa增加到13.3 GPa;在SOC25%至SOC40%阶段,杨氏模量呈水平趋势,几乎不变。随着锂离子的脱出,杨氏模量降低至7.9 GPa。在整个充放电阶段,杨氏模量重合度较高,说明电极整个过程发生了较好的弹性变形,未有明显的塑性变形,电极性能较好。
而在0.2C充电倍率下,考虑了锂离子浓度随活性层厚度方向呈梯度变化。随着锂离子的不断嵌入,在SOC0%至SOC15%阶段,杨氏模量以较快的速度从10.2 GPa增长至15 GPa;在SOC15%至SOC40%阶段,杨氏模量以较为缓慢的速度增长至16.9 GPa。随着锂离子的脱出,杨氏模量线性降低至12.9 GPa。与0.1C充电倍率相比,0.2C倍率下的杨氏模量重合度较差,说明电极在较高倍率下发生了明显的塑性变形,电极性能较差。
(a) 0.1C
(b) 0.2C
Figure 7. The change of Young’s modulus of silicon carbide anode with charge state at 0.1C and 0.2C charge rate
图7. 碳化硅负极在0.1C和0.2C充电倍率下杨氏模量随充电状态的变化
4.2.3. 碳化硅复合电极应力演化
结合式(2),即可得到碳化硅复合电极分别在0.1C和0.2C充电倍率下第四循环中应力随充电状态的变化趋势,如图8所示。在锂化过程中,由于集流体活性层的体积膨胀进行约束,导致应力呈线性增长。当充电状态达到设置的最大值40%时,碳化硅复合电极所受到的压应力约为14.8 MPa。而在脱锂过程中,压力线性减小至最大值的17%,约为2.5 MPa。模型计算结果可知,电极应力在锂化脱锂过程中的重合度较高,没有出现明显的应力衰减现象,说明电极活性层表面并未产生明显裂纹。
而在0.2C充电倍率下,由于锂离子浓度梯度的存在,当充电状态达到设置的最大值40%时,碳化硅复合电极所受到的压应力约为12 MPa,比0.1C充电倍率下的峰值较小。而在脱锂过程中,压力线性减小至最大值的25%,约为3 MPa,比0.1C充电倍率下的最低值偏大。此外,由模型计算结果可知,电极应力在锂化脱锂过程中的重合度较低,有出现明显的应力衰减现象,说明电极活性层表面产生部分裂纹,电化学性能较差。因此较快的充放电速率会加剧电极活性层的机械损伤。
(a) 0.1C
(b) 0.2C
Figure 8. The change of stress of silicon carbide anode with charge state at 0.1C and 0.2C charge rate
图8. 碳化硅负极在0.1C和0.2C充电倍率下应力随充电状态的变化
5. 结论
本论文在提出碳化硅电极的原位测量系统和物理模型的基础上,考虑到快速充电会引起锂离子浓度c在厚度方向上分布不均,对于0.2C充电倍率,假设锂离子浓度在厚度方向上存在浓度梯度,进一步提出了一套考虑浓度梯度的物理模型。分别在0.1C和0.2C充电倍率下,对碳化硅电极组成的模型电池进行电化学循环,并对其进行多循环分析,得到:
1) SEI层主要在第一、二循环形成,消耗大量锂离子,因此第一、二循环的曲率变化与其他循环相比差异较大,放电时间较短。第三、四、五循环的曲率变化重合度良好,充放电前后曲率增量一致,说明碳化硅复合电极在第三、四、五循环保持稳定,锂离子反复脱嵌引起的损伤较小。
2) 快速充电导致锂离子在活性层分布不均,各局部应力应变有较大差异,充电过程中曲率变化的波动性较大,而慢充条件下锂离子移动缓慢分布均匀,曲率变化在充放电过程中均很稳定。
3) 锂化程度越高,电极的弯曲变形越大。在同一锂离子浓度下,快充引起的电极变形程度大于慢充,快充会引起活性层较大的损伤,而慢充对电极的损伤较小可以使其保持良好的结构。