1. 引言
钢包作为钢铁冶炼的重要容器,起着运输、浇注和炉外精炼作用 [1] 。本厂钢包分整体和剥拆两种。整体钢包指全部更换内衬的钢包,剥拆钢包指更换部分内衬的钢包 [2] 。整体钢包浇注料用量13.5吨,剥拆钢包浇注料用量约7.0吨。
本厂钢包采取套浇工艺,内衬工作层和永久层为同种铝镁浇注料,无保温层结构。其结构如图1所示 [2] 。
钢包浇注料由不同颗粒级别的不定型耐火材料组成,施工时加入适当比例的水以确保浇注料具有良好的流动性,搅拌后放入钢包内,采用振动棒进行振动使其致密,并按照规定的时间养护 [3] 。加入的水分少部分在养护期间自然干燥除去,大部分存留在浇注料内,为确保生产安全和钢包的良好使用,必须对钢包进行一定的烘烤。
浇注后钢包的烘烤为新包烘烤 [4] 。新包烘烤的目的不仅是将钢包浇注料中水分缓慢充分排出、更重要是使钢包的内衬达到一定的温度以形成较好的晶相结构,提高抗冲刷和蓄热保温作用,最终起到减小
1.包壳;2.耐火纤维板;3.浇注料;4.透气砖;5.座砖
Figure 1. Schematic diagram of ladle lining structure
图1. 钢包内衬结构示意图
使用过程中温差过大而导致的内衬热应力过度集中,减少内衬出现剥落、断裂等现象,提高钢包使用寿命的目的 [5] [6] 。
在钢包烘烤器的发展过程中,有三个方面的进步对提高钢包烘烤的效率和质量比较明显:1) 钢包加盖、2) 烧嘴的改进、3) 余热的利用 [7] 。其中烧嘴的改进又经历了简易高速烧嘴、油气两用烧嘴、自身预热式烧嘴和蓄热式烧嘴四个阶段,目前大多数烘烤器为蓄热室烘烤器 [8] 。蓄热式钢包烘烤装置集自身预热式烧嘴和新型蓄热式燃烧技术于一体。它主要由换向阀、蓄热室、烧嘴及换向控制装置等主要部分组成。一般分为空气预热、煤气不预热和空气煤气双预热两种形式 [9] 。
李丽丽等 [10] 以某钢厂180 t钢包和蓄热式烧嘴为基础建立了物理模型,选取包衬中心界面的若干点进行温度跟踪,设定若干初始条件,模拟出不同氧浓度和烘烤时间下钢包跟踪点温度变化趋势图,并进行现场实验,发现实际工况和数值工况几乎相吻合,且钢包从冷包烘烤到工作最低要求温度,经历了升温速度从快变慢的过程,在烘烤12 h后升温速度明显下降,到16 h后温度变化即不明显,而随着富氧量的增加,烘烤时间也应逐渐减少,富氧到25% 时需要14.6 h,富氧到29%时仅需要13.9 h。
2. 浇注料热重分析和钢包烘烤工艺方案设定
目前本厂钢包烘烤器主要由一个钢结构和耐火材料做成的钢包盖和垂直于钢包盖安装的烧嘴构成,采用立式放置 [7] 。为节约能源,降低成本,本厂技术人员在结合上述分析和以往钢包烘烤工艺提出新的烘烤工艺。新烘烤工艺如下:整体钢小火24小时、中火18小时、大火8小时;剥拆钢包小火16小时、中火16小时、大火8小时。
实验设备:综合热分析仪:型号:STA449C,生产厂家:德国耐驰仪器制造有限公司;手持红外测温仪:生产厂家:香港希玛,型号:852B,测量范围为−50℃~950℃,精度:1℃。
首先对浇注料进行差热热重分析 [11] 。现场取样粉碎加入6%的水搅拌均匀。其差热热重曲线如图2所示。
图2为浇注料样品DSC-TG曲线。由TG曲线可知,样品从室温加热到115℃有大量失重,失重为6%,主要是加入的水。样品的主要失重阶段为50℃至115℃,且观察DSC曲线可知样品在60℃存在一个明显的吸热峰,根据样品的组成,可以判断此阶段的失重主要为配加的水。随着温度的不断升高直至结束,浇注料还有一定的失重,但较小为0.5%。
通过测量得知烘烤终点时刻钢包内衬包口温度可以达到813℃。以浇注料样品DSC-TG曲线分析为基础。针对新烘烤工艺开展现场实验,但由于设备限制包膛内部的温度无法精准测量,结合实际情况采用手持红外测温仪测量钢包外壳的温度作为参考温度 [12] [13] 。
本实验钢包热状态研究和数据分析的思路为 [12] :浇注料差热分析→提出优化方案→现场温度测量→温度数据分析确定钢包烘烤是否饱和。根据新烘烤方案开展相关工业实验,对烘烤过程钢包包壳测温点的温度进行测量并记录 [10] [13] 。
实验方案如下 [10] [12] [13] [14] :在新烘烤工艺下以钢包包底为零位,距离包底0、100、210、800、1200、1600、2200 mm的位置作为测温点,标记为1-7#。钢包烘烤一段时间后开始测温,每隔一段时间测温一次。
3. 数据采集和分析
本实验的主要目的是验证新烘烤工艺下钢包浇注料是否达到热饱状态,也确认浇注料中加入的水完全除去。烘烤阶段钢包截面温度分布规律大致相同,故取某一时间点进行分析 [1] 。通过对烘烤过程中测温点温度场的分布和在不同阶段升温速率的分析来确认浇注料是否达到热饱和状态。本次实验数据采集
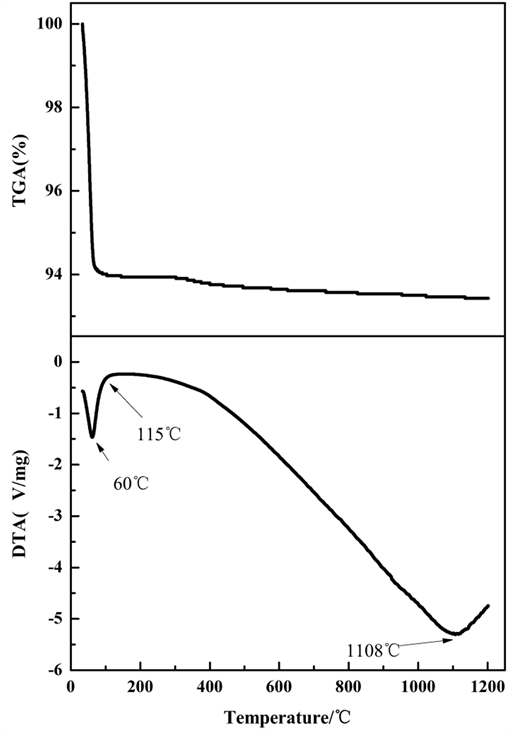
Figure 2. The DSC-TG curve of ladle pouring material
图2. 钢包浇注料DSC-TG曲线
分整体钢包和剥拆钢包两种。初步分析比对发现两种类型的钢包在新烘烤工艺下温度场分布几乎相同。剥拆包浇注料用量约为整体包的50%,而烘烤时间为整体包80%,故本文只对整体钢包作细致分析。
整体钢包烘烤过程中测温点温度场分布和变化如表1和图3所示。
由表1和图3可知钢包外壳温度与烘烤时间基本上呈正比关系 [10] [12] [13] [14] ,烘烤结束时距离包底0.8 m至1.6 m的区间温度在221℃至230℃,包口位置温度高达到303℃。40小时后此区间温度场差异不大几乎重合。特别是在中火结束大火开始时,各点的升温曲线几乎重叠。钢包此区域的温度趋于一致,说明在烘烤后期钢包上部的温度趋于平衡,此区域浇注料达到热饱和状态。烘烤结束时包底0.00 m至0.21 m处温度差异较大,仍具有一定的升温空间。钢包烘烤到第47小时最低温度在1#测温点处为123℃,已高于浇注料水分几乎完全分解的115℃。但现场浇注料用量与热重分析量存在巨大差别,且钢包外壳具有一定的封闭性,考虑到气体的扩散以及煤气热值的波动,为确保安全生产需要在高于浇注料完全失水的温度下保温一定的时间。本厂钢包浇注料内衬具有一致性,比热、导热率等物性参数相同。研究表明耐材浇注料的导热和厚度呈线性关系。将终点温度和壁厚做乘积,包底380 × 132 = 50,160,包墙210 × 228 = 47,880,二者相差2280,考虑到包口散热的因素,说明钢包受热较为均匀。
钢包烘烤过程中测温点在不同阶段的升温速率也是判断烘烤是否饱和的指标之一。测温点在中火和大火阶段的升温速率如表2所示。
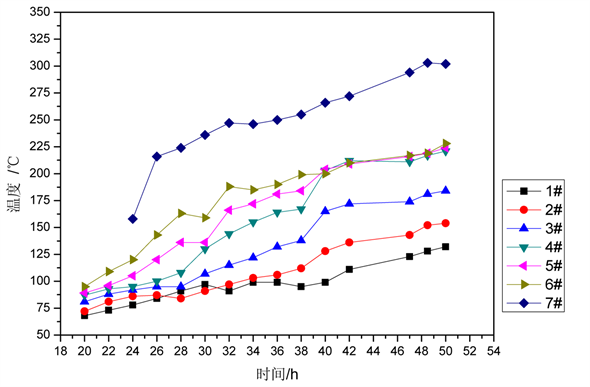
Figure 3. Temperature changing curve during the ladle baking process
图3. 整体钢包烘烤过程中温度变化曲线
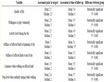
Table 1. Temperature field distribution in the process of ladle baking (˚C)
表1. 整体钢包烘烤过程中温度场分布(℃)
由表2可知在烘烤过程中只有0.21 m以下测温点在大火阶段的升温速率大于中火,其中包底最为明显,其大火阶段的升温速率是中火阶段的2倍。其他区域测温点大火升温速率明显低于中火 [10] 。
综上分析说明烘烤结束时钢包已达到热饱和状态水分几乎全部除去。新烘烤工艺的钢包在使用过程中跟踪观察未出现异常情况,实践进一步证明新烘烤工艺能够满足容积40吨钢包安全生产的需要。在后期的工作中要做好钢包气孔的疏通,以便烘烤过程中水汽的排出,确保烘烤效果。
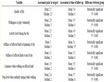
Table 2. Rate of heating during middle and big fire phases at the temperature measuring point
表2. 测温点中火和大火阶段升温速率
4. 节约效益
新烘烤工艺相比就烘烤工艺整体包缩短8小时、剥拆包缩短6小时,中火煤气消耗约200元/小时。根据2016年数据:整体包和剥拆包比为:9.3:90.7,包龄77.65炉,每炉单重38.00吨算得吨钢降本0.4193元。
5. 结论
在分析浇注料差热热重和以往钢包烘烤工艺的基础上提出了钢包烘烤新工艺,通对对钢包测温点烘烤结束时刻温度场、不同阶段升温速率的分析以及上线使用发现新烘烤工艺能满足生产的需要。