1. 引言
随着经济与科技的快速发展,大型零件已经在航空航天、高速铁路、核电、风电、大型工程机械、大型模具制造等领域得到越来越广泛的使用。这类零件通常具有结构尺寸大、形状复杂、重量大、制造精度要求高等特点。大型零件结构特点决定了其加工方式的特殊性,现在,大型零件的加工主要采用整体制造法。整体制造法是指用大型机床对整块毛坯进行加工获得所需零件。但采用大型机床对大型整体工件进行加工常存在以下问题:
1) 严格的厂房/地基要求:安装重型机床需要建造高大的厂房和牢固的地基 [1] ,大型机床在切削过程中,刀具与工件间产生的切削力、机床本身重量、机床运动部件旋转产生的动力等会通过机床结构作用于地基,因此高性能的地基是保证大型机床稳定切削的必备条件,同时为防止外界激励对机床产生影响,地基还需具有好的隔振效果,目前大型机床地基的设计常采用有限元法进行仿真设计 [2] [3] [4] [5] [6] 。但仿真结果较实际情况差别较大,需反复仿真、试验才能满足大型机床的安装要求。由此可知,大型机床严格的地基/厂房要求势必造成机床高的安装及运行使用成本。
2) 机床装配周期长:大型机床在机床制造企业装配调试好后,在运往用户生产场地前往往需重新分解机床,待机床大型零部件运往生产场地后,再重新进行装配调试,同时由于零部件尺寸大、重量大,零部件搬运较困难(需具有大吨位起重装置),装配调试周期长。
3) 工件安装定位难:通常大型工件的加工与使用场地相互分离,因工件自重及加工时的支承状态与使用时的不一致,需根据工件毛坯形状对大型工装进行调整,同时为确保工件在机床中处于正确的加工位置,需人工调整定位或寻位加工 [7] ,费力耗时。
4) 大型机床中辅助设备能耗大、使用率低:由于大型设备通常需安装在专门的生产车间内,环境温度控制及辅助设备的能耗占比例较大。以某大型加工中心机床为例,机床各功能中,主轴、冷却单位、冷却系统、液压系统、伺服系统等系统耗用了88%的电力,而耗用的电力中只用25%直接用于切削加工 [8] ,其余全部由辅助设备消耗,导致大型机床辅助设备能耗(如冷却系统、液压系统、伺服系统等)较普通机床高,特别是此类机床为某项工程或产品所定制,难以应用于其他产品的生产,经济性不好并且难以承接社会化的服务。
2015年5月国务院印发“中国制造2025”,部署全面推进实施制造强国战略,作为我国实施制造强国战略的第一个十年行动纲领,实现中国制造向中国创造的转变,中国速度向中国质量的转变,中国产品向中国品牌的转变,完成中国制造由大变强的战略任务。基于以上背景,在已有机械加工制造模式基础上,探索一种新的加工模式用于大型零件的高效高精加工尤为必要。此外,在机械制造技术基础课程中,主要以常规中小尺寸零件的制造为基础进行授课,对大型或超大型零件的加工并未涉及太多。本文在已有加工制造模式的基础上,提出一种基于群机加工的大型零件加工模式,并对其涉及的关键技术问题进行了讨论。
2. 常规的机械制造方法
按照零件由原材料或毛坯制造成为零件的过程中,质量M的变化,可分为ΔM > 0,△M = 0,ΔM < 0,三种原理,即材料累加成形原理就、材料基本不变原理、材料去除原理,不同原理采用不同的制造方法。
2.1. 材料累加成形制造
材料累加法制造(MIM)制造出现于上个世纪80年代,通过材料逐渐累加成型。这一工艺又称RP技术(Rapid Prototyping)。其优点是:无需编程,即可以成型任意复杂形状的零件,而无需刀、夹具等生产准备活动。典型代表我3D打印技术。
3D打印技术是一种以数字三维模型文件为基础,将计算机内的三维数据模型进行分层割片,得到各层数据,计算机根据隔层数据信息来控制激光器(或喷嘴)有选择地逐层烧结(固化,热熔凝结等)形成层层微小厚度的实体,再熔结、聚合、黏结使各层黏结成一体,最终造出实体模型。与传统的去除材料加工技术不同,因此又称为添材制造(Additive Manufacturing)。3D打印技术是制造业领域正在迅速发展的一项新兴技术,它涵盖了产品生命周期前端的“快速原型”(rapid prototyping)和“快速制造”(rapid manufacturing) 相关的打印工艺、技术和应用。3D打印需要依托多个学科领域的技术,至少包括信息技术、精密机械和材料科学三大技术。近年来,3D打印技术发展迅速,在各个环节都取得了长足进步。通过与数控加工、铸造、金属冷喷涂、硅胶模等制造手段结合,该技术已成为现代模型、模具和零件制造的有效手段,在航空航天、汽车摩托车、家电、生物医学等领域得到了一定应用,在工程和教学研究等应用领域也占有独特地位。图1为3D打印技术涉及的关键技术。
2.2. 材料基本不变成形制造
材料基本不变成形制造,主要属于材料成形课程的研究范畴。主要指铸造、锻压和焊接等热加工工艺。铸造技术是将通过熔炼的金属液体浇注入铸型内,经冷却凝固获得所需形状和性能的零件的制作艺术。其优点是:制造成本低,工艺灵活性大,可以获得复杂形状和大型的铸件,在机械制造中占有很大的比重,如机床占60%~80%,汽车占25%拖拉机占50%~60%。铸件的质量直接影响着产品的质量,因此,铸造在机械制造业中占有重要的地位。锻压是锻造和冲压的合称,是利用锻压机械的锤头、砧块、冲头或通过模具对坯料施加压力,使之产生塑性变形,从而获得所需形状和尺寸的制件的成形加工方法。焊接是通过加热、加压,或两者并用,使同性或异性两工件产生原子间结合的加工工艺和联接方式。焊接应用广泛,既可用于金属,也可用于非金属。图2为铸造、锻压及焊接三种典型制造方法的零件及设备。
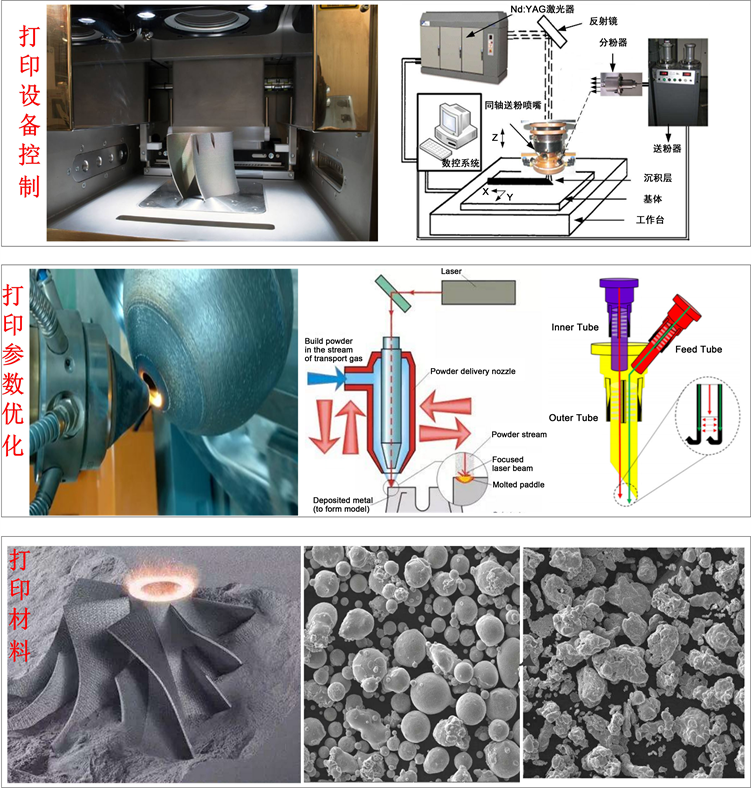
Figure 1. Some key technologies in 3D Printing
图1. 3D打印涉及的部分关键技术
2.3. 材料去除原理
材料去除原理主要指切削加工,该加工过程是通过刀具和工件之间的相对运动及相互力的作用实现的。工件往往通过夹具安装在机床上,机床带动刀具或工件或两者同时进行运动。切削过程中,有力、热、变形、振动、磨损等现象发生,这些现象的综合作用决定了零件。典型的设备是数控切削机床。数控机床和基础制造装备是装备制造业的“工作母机”,一个国家的机床行业技术水平和产品质量,是衡量其装备制造业发展水平的重要标志,《中国制造“2025”》将数控机床和基础制造装备列为“加快突破的战略必争领域”。数控机床和基础制造装备是制造业价值生成的基础和产业跃升的支点,是基础制
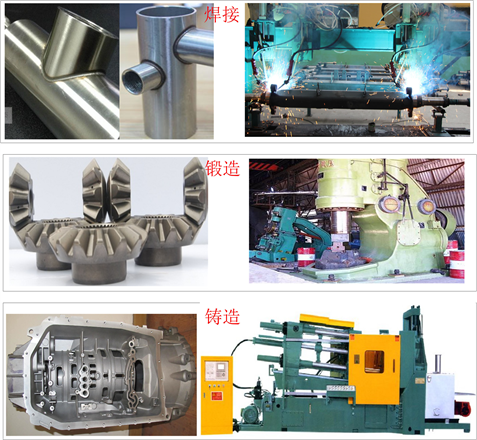
Figure 2. Parts and processing equipment for casting, forging and welding
图2. 铸造、锻造及焊接对应的零件及加工设备
造能力构成的核心,唯有拥有坚实的基础制造能力,才有可能生产出先进的装备产品,从而实现高价值产品的生产。与发达国家相比,我国机床行业起步晚,发展时间较短,技术相对落后。我国机床产业规模虽然位居世界首位,但却面临着产业结构不合理、自主创新能力不足等多项挑战。高精、高效以及智能化的数控机床是未来我国机床行业的发展方法。图3是数控机床涉及的部分关键技术。
3. 大型零件的加工设备
大型零件的加工需要采用特殊结构的大型机床设备,目前的大型机床结构有如下几种:
1) 普通大型机床结构。普通大型机床主要由串联运动机构组成,其结构类型主要有动柱式结构、龙门结构以及桥式结构。动柱式机床又名固定工作台机床,采用固定工作台结构,切削运动由立柱的移动实现;龙门式机床采用两立柱固定,工作台往复运动实现切削运动;桥式机床采用工作台和立柱固定,横梁移动的结构方式实现切削运动。在实际生产中,应根据大工件特征选择所需类型。如三峡工程大型叶片采用5FZG龙门式铣镗床(德国进口)进行加工,波音公司采用Minumac 30 TH龙门式数控铣床对飞机大型零件进行加工,西门子公司采用CINCINNATI龙门式数控铣床对大飞机零部件进行加工,国内某企业采用DF6030型动柱式机床(国产机床)对大型工程机械零件进行加工,机床工作面尺寸为16,000 mm × 4000 mm。目前此类机床结构在普通大型零件加工中得到应用。
2) 混联大型机床。在普通大型机床中,双摆头是关键部件,其性能对工件的加工精度产生直接影响,高性能双摆头制造成本高,且控制复杂。随着并联机构技术发展,并联机构运动定位精度可控制在一定程度,将串联导轨与并联加工头混合即形成混联机床。如PKMTRICEPT SL公司生产的混联机床用于大型机翼工件加工,StarragGroup集团DorriesScharmann公司采用具有Sprint Z3主轴头构造Ecospeed混联机床对大型飞机工件进行高效加工(图4所示),加工时工件不动,刀具运动切削,加工表面质量好,材料去除率高。总体而言,混联大型机床在大飞机大型零件中应用较广泛。
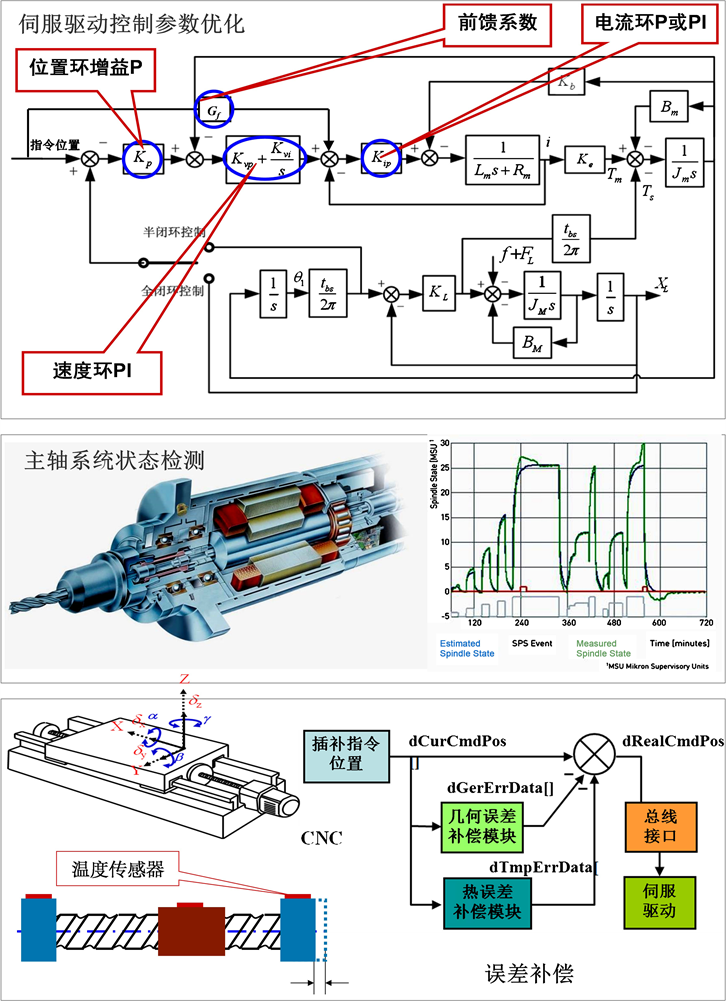
Figure 3. Some key technologies of CNC Machine Tools
图3. 数控机床涉及的部分关键技术
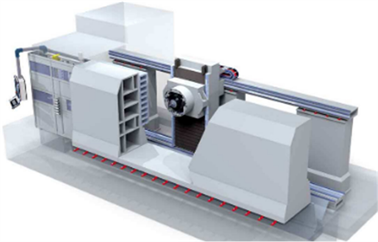
Figure 4. Machining wings by Ecospeed Hybrid Machine Tool with Sprint Z3 spindle head
图4. 采用Sprint Z3主轴头的Ecospeed混联机床加工机翼
3) 大型专用机床。针对超大型工件,如采用以上两类结构对工件进行加工,机床尺寸会非常庞大,因此常采用专用机床对其进行加工。如沈阳机床集团研制专用机床,对磁悬浮列车导轨梁上的部位进行加工,加工时导轨梁由两台五轴三联动加工中心面对面同时加工,导轨梁固定,两侧的机床运动完成所有加工工序;另一类专业机床采用模块化结构,不同功能的模块可构造成不同类型的专用机床。可重构机床最早由美国密西根大学提出,其期望机床能满足模块化,可变化,可集成等功能。构造非正交轴可重构机床,主轴单元可在弧形立柱上移动,可实现五个不同角位置平面及孔的加工。
4. 群体加工模式涉及的关键技术问题
群体加工的核心思想在于采用“蚂蚁啃骨头”的制造模式,使用多台小型设备对大型零件进行加工。工作过程示意图如图5所示,即采用多个小型设备同时对零件的不同加工部位进行加工。在群体加工模式中,需要关注一下关键技术问题。
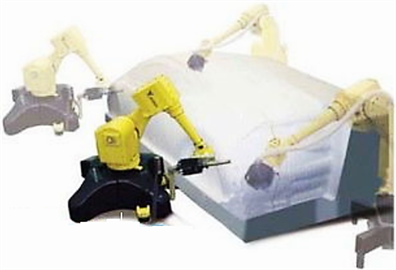
Figure 5. Group machining schematic diagram of large parts
图5. 大型零件的群体加工示意图
1) 群机协同控制技术。针对大型零件不同的加工部位,协同控制指的是多台加工设备共享工作空间,共同完成加工部分。加工时需要充分考虑多台设备共同作用下对零件加工精度的影响,形成高效的同步控制方案,例如多台设备同时加工时加工系统的动态特性协调控制问题、加工变形协调控制问题、加工误差协调控制问题以及加工效率的协调控制问题。
2) 绿色制造工艺规划问题。绿色制造是“中国制造2025”的重要组成部分。绿色制造技术是以传统制造技术为基础,并结合环境科学、材料科学、能源科学、控制技术等新技术的先进制造技术,其目标是使产品在制造过程中对环境的负面影响最小,资源利用率最高。群机加工中应该充分考虑群机设备的加工工序、加工路径、协同运动以及加工过程能源利用对环境的影响。
3) 注重智能化技术在群机制造中的应用。
智能制造技术是在现代传感技术、网络技术、自动化技术、拟人化智能技术等先进技术的基础上,通过智能化的感知、人机交互、决策和执行技术,实现设计过程、制造过程和制造装备智能化,是信息技术和智能技术与装备制造过程技术的深度融合与集成。制造系统正在由原先的能量驱动型转变为信息驱动型,要求制造系统表现出更高的智能。智能制造技术从不同角度具有不同的组成。从智能设备层面来讲,应该具备以下典型功能:工况感知与智能识别、性能预测与智能维护、智能规划与智能编程、智能数控与伺服驱动。从智能制造系统层面来讲,应具备:系统建模与自行组织、智能制造执行系统、智能企业管控、智能供应链管理、流程智能控制。从智能服务角度来讲,应该具备:服务感知与控制的互联、工业产品智能服务、服务过程的智能运控、制造物联网与物流智能服务、制造与服务的集成共享和协同。
4) 群机加工的数字孪生技术。
数字孪生(digital twin)是以数字化方式创建物理实体的虚拟模型,借助数据模拟物理实体在现实环境中的行为,通过虚实交互反馈、数据融合分析、决策迭代优化等手段,为物理实体增加或扩展新的能力。作为一种充分利用模型、数据、智能并集成多学科的技术,数字孪生面向产品全生命周期过程,发挥连接物理世界和信息世界的桥梁和纽带作用,提供更加实时、高效、智能的服务。基于群机加工模式,通过与外界传感器的集成,在数字管理系统实现对群机加工中的所用任务进行管控与分析,比如群机加工的全生命周期健康管理、生产工序的管控与调整、生产实时数据的挖掘与分析、加工过程多物理尺度和多物理量的建模等。
5. 结论
文中对机械制造中常规的加工方法进行介绍,并对涉及的关键技术问题进行讨论;对大型零件的加工设备进行详细介绍,针对其加工中存在的问题,提出群机加工模式;对群机加工模式中存在的关键技术,即群机协同控制技术、绿色制造工艺规划技术、智能化技术以及数字孪生技术进行了说明。