1. 引言
在不锈钢材料发展的百年历史中,奥氏体不锈钢生产量和使用量占不锈钢总产量及用量的70%以上,304不锈钢作为奥氏体不锈钢家族中重要的一员,因其具有良好的耐蚀性(特别是耐浓酸、强碱腐蚀环境方面有优良的性能)、耐高温、优良的力学性能、冲压、弯曲等热加工性能,使得304不锈钢大量地用于石油、化工、电站、长输管线、造船、核工业。304不锈钢在我国标准代号为1Cr18Ni9不锈钢,又称18/8不锈钢,是一种传统不锈钢 [1] ,美国ASTM、日本JISG标准体系针对304不锈钢棒材、型材、板材、带材的生产制备均有成熟的生产工艺,我国也有相应的国标与之对照 [2] 。
2012年,受国际形式影响,我国大多数民营企业转型生产304不锈钢,工艺路线为:电弧炉(中频炉)熔炼 + AOD + 连铸连轧。某企业所生产的304不锈钢热轧棒表面有黑色线层,酸洗后仍然存在,经打磨后,发现有气孔和微裂纹,导致产品成批报废。
针对企业在生产中出现的问题,课题组分析了黑色线层的夹杂物,微观组织、合金元素分布等,通过与基体对比分析,找出黑色线层及缺陷产生的原因,采用控制连铸坯质量稳定性等手段,所生产的热轧棒质量全部合格,提高产品成材率。
2. 样品基本情况介绍
企业生产的304不锈钢线材表面出现黑线,线材规格及种类见表1,生产工艺为20 T中频炉熔炼 + 10 T冷料(高铬、高镍铁、304不锈钢) + 30TAOD + 中间包 + 连铸坯 + 连轧,所生产的304热轧棒表面有黑色层,酸洗后仍然存在,经打磨后,发现有气孔和微裂纹,导致产品成批报废,宏观形貌见图1。从图1可以看出,不同直径的试样上面都存在黑线,黑线放大后可以看出有沟槽,有些黑线都是连续和贯穿整个长度的,而且黑线不止一个,尺寸粗细不一。1#试样为φ20 mm的圆棒,其沟槽宽度最大。而其他3个φ5.5 mm的圆棒上面的黑线相对较细,从外表面未发现折叠现象。
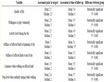
Table 1. The description of sample appearance
表1. 试样外观说明
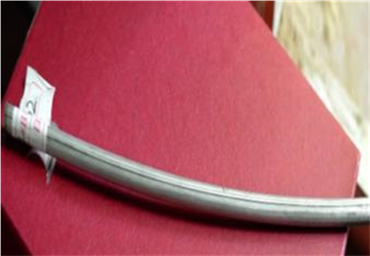

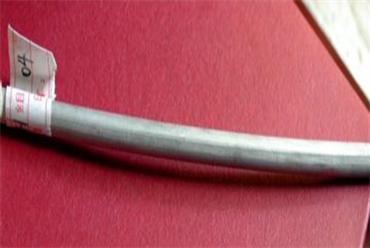
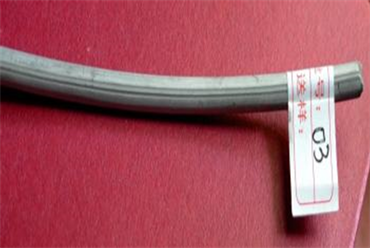
Figure 1. The Macroscopic appearance of black line defect
图1. 黑线缺陷宏观形貌
3. 能谱分析
能谱是材料或组织分析的常用手段,为考察黑线区域的成分与其它部位成分上是否存在差异,对4个试样黑线(沟槽部位)和基体部位分别进行了能谱分析,分析结果见图2~图5,1#沟槽部位与平整部位的能谱分析两者成分接近,组织形貌接近。
2#试样宽槽及平整部位进行能谱分析见图3,各部位成分、形貌基本一致。
3#、4#试样宽槽及平整部位进行能谱分析,各部位成分、形貌基本一致。形貌见图4、图5。
(a)
(b)
Figure 2. The Sample energy spectrum analysis (a groove position; b flatting position)
图2. 1#试样能谱分析(a沟槽部位;b样平整部位)
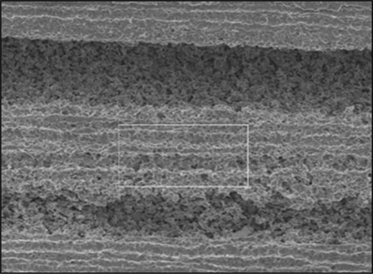
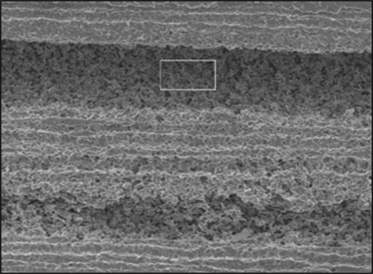
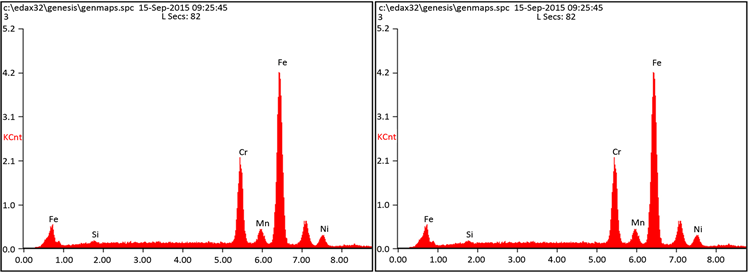
(a) (b)
Figure 3. The Sample energy spectrum analysis (a groove position; b flatting position)
图3. 3#试样能谱分析(a沟槽部位;b样平整部位)
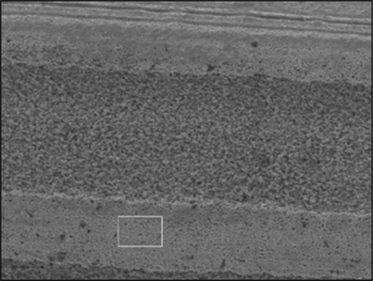
(a) 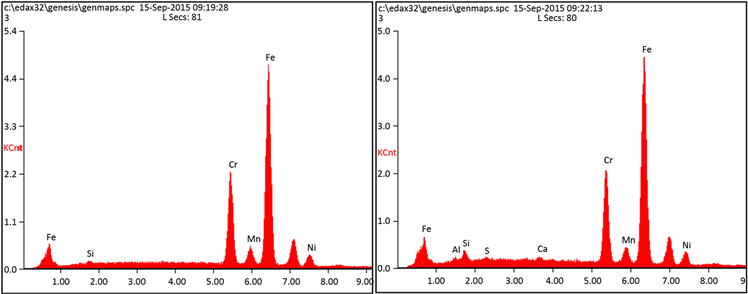
(b)
Figure 4. The Sample energy spectrum analysis (a groove position; b flatting position)
图4. 3#试样能谱分析(a沟槽部位;b样平整部位)
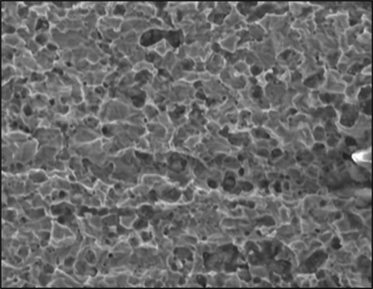
(a) 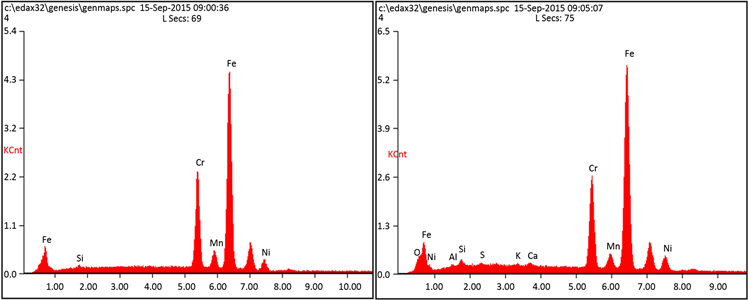
(b)
Figure 5. The Sample energy spectrum analysis (a groove position; b flatting position)
图5. 4#试样能谱分析(a沟槽部位;b样平整部位)
从能谱分析结果来看,沟槽部位与平整部位的主要成分差异不大,组织形貌接近。为了更直观地对比沟槽部位与平整部位成分的差异,对1#、4#两个试样进行了线扫描能谱分析,图6、图7。1#试样左侧颜色较深部位是沟槽部位,而右侧是平整部位。从图6可以看出,Fe、Cr、Ni、Mn核心元素的成分分布基本均匀,而Si、O在个别部位的存在富集。如Si、O在平整部位富集,存在重叠现象,表明这些部位可能有硅酸盐存在。
4#试样中中间部位颜色稍深的部分是沟槽部位,两侧颜色较浅的部分则是平整部位。从图7可以看出,与1#试样的线扫描结果一样,Fe、Cr、Ni、Mn核心元素的成分分布基本均匀,而Ca、Si、O在平整部位的个别位置存在富集。
线扫描的结果表明,在沟槽即黑线部位不存在夹杂物的富集。
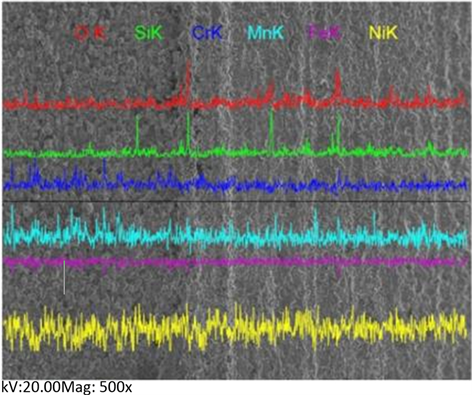
Figure 6. The Line scanning energy spectrum analysis of 1# Sample
图6. 1#试样线扫描能谱分析
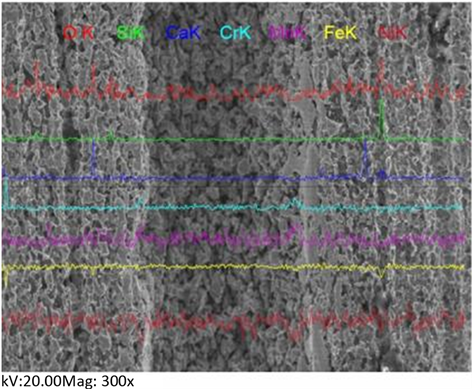
Figure 7. The Line scanning energy spectrum analysis of 4# Sample
图7. 4#试样线扫描能谱分析
4. 微观组织分析
4.1. 夹杂物分析
图8为1~4#试样的夹杂物形貌,夹杂物为黑色颗粒相,呈球形弥散分布。1#试样的夹杂物尺寸最大,但不超过10 μm;随着变形程度增加,夹杂物尺寸减小,2#、3#及4#试样中的最大尺寸夹杂物月6 μm左右。与肉眼可见的黑线相比,夹杂物要细小的多,夹杂物是非连续的颗粒状,与黑线连续的线状不同。
(a) (b)
(c) (d)
Figure 8. The Inclusion morphology(a 1#, b 2#, c 3#, d 4#)
图8. 夹杂物形貌(a 1#, b 2#, c 3#, d 4#)
4.2. 组织分析
试样经不同粒度的砂纸打磨并抛光后,采用王水腐蚀,金相组织如图9所示,1~4#试样基体组织为奥氏体,在奥氏体中存在孪晶组织。组织中的黑色颗粒相为夹杂物。金相组织中未发现碳化物。
5. 结论
1) 黑线(沟槽)部位的组织、成分与平整部位没有明显差异,不会产生成分偏析和析出物。
2) 宏观黑线是通条连续的,试样中的夹杂物弥散分布且尺寸细小,因此从黑色沟槽的连续性分布以及存在方向,可以确定夹杂物并不是产生表面缺陷的直接原因,而是由连铸棒坯在轧制过程中受力形成的拉痕,拉痕的形成通常由外部的缺陷或润滑不良引起。
3) 课题组在跟踪生产流程发现,由于当时气温较高,粘在连铸坯表面的保护渣细小颗粒没有完全脱落,由于反复热轧所产生大量的黑线及裂纹。
(a) (b)
(c) (d)
Figure 9. The Microstructure (a 1#, b 2#, c 3#, d 4#)
图9. 组织形貌(a 1#, b 2#, c 3#, d 4#)
4) 为有效脱除连铸坯表面的保护渣细小颗粒,企业在连铸工艺中增加冷却水流强度,加大冷却速度,连铸坯表面质量得到有效保证,所生产的热轧棒质量全部合格。