1. 引言
近年来,陶瓷3D打印技术作为新型无模制造工艺逐步发展起来,该技术集数控技术、CAD技术和先进材料制备技术为一体,不仅缩短了材料的生产周期,还节省制造成本,更为重要的是该技术能够制备出多自由度的陶瓷产品,缓解了快速增长的市场需求与相对落后的制备技术之间的矛盾,该技术被誉为“第三次工业革命最具有标志的生产工具”,越来越受到国内外的关注 [1] [2] [3] [4]。
熔融沉积成型技术(FDM)作为目前应用最广泛的3D打印技术之一,具备打印速度快、成本低、操作简单等优点 [5] [6]。 在1988年由Crump等 [7] 首次提出,这种技术采用热熔型丝状材料作为打印原料,材料长丝在略高于其熔点的温度下连续供应到喷嘴并在其内加热,从而可以容易地通过喷嘴挤压形成层,挤压后,材料在先前的打印层上立即凝固,打印完一层后平台会下降一定的高度,以便下一层的打印。
在20世纪90年代美国Argonne国家实验室和Rutgers大学首次将陶瓷材料与计算机融合并在机械装置内进行了3D打印,利用熔融沉积成型技术制备了Al2O3喷嘴座,烧结密度98%,强度824 ± 110 MPa [8] [9]。 与传统的FDM相比,陶瓷FDM技术的特点是将陶瓷粉体掺入有机粘结剂中,并加入无定性基料结合剂生成复合材料,然后将复合材料放入打印设备中在稍高于其熔点的温度下熔化,通过计算机控制打印路径制备陶瓷生坯。最后通过脱脂处理后的生坯在适宜的高温条件下烧制成陶瓷部件 [10]。 1995年,罗格斯大学的Danforth报告了FDM技术在陶瓷制备中的首次应用,使用了Al2O3和Si3N4填充粘合剂系统。由于烧结件中存在空隙等缺陷,最终烧结密度不合格(75%~90%),但未发现分层 [5]。
由于以长丝或浆材作为原料的FDM工艺局限性太大,研究人员最近提出了由粘合剂和高固含量粉末的混合物制成的颗粒或颗粒的替代原料作为3D打印的原料。Lu等 [11] 将60 vol%固相含量的氧化铝粉末与热塑性聚乙烯醇缩丁醛和聚乙二醇(PEG)溶剂基混合物混合,将得到的糊状物预先填充在不锈钢注射器中,并通过微型挤出机(50,000步/r微型步进电机)进行注射成型氧化铝陶瓷件。而Anna Bellini等 [12] 则基于FDM工艺开发出一种新型挤出系统,这种挤出系统主要是由具有高精度定位系统的微型挤出机组成,并且用颗粒状材料代替细丝,这种替代增加了材料组合的可用性,并且可以使用商用注塑材料作为原料,然后用高压挤出机挤出,原料的粘度值能达到100 Pa·s。从事金属注射成型的研究人员从中得到启发,提出了通过螺杆挤压和颗粒原料来增材制造不锈钢零件的方法。在国内,深圳大学的一个研究小组也提出了一种FDM工艺,使用与粉末注射成型机相同的原料混合物 [13]。 该研究小组使用不锈钢粉末和热塑性石蜡基粘合剂,通过螺杆挤出机挤出,研究了生坯和烧结挤出长丝的材料性能。
本文开发了一种基于螺杆挤出的陶瓷材料熔融沉积工艺,设计了基于FDM技术的螺杆挤出系统,通过模拟分析和实际实验对系统的结构和工艺参数进行了优化,并成功打印了复杂结构的陶瓷零件。最后,测试了打印材料的性能,并对零件的微观形貌进行了表征,为后续研究工作的开展打下了基础。
2. 实验部分
2.1. 螺杆挤出系统设计
基于FDM的螺杆挤出系统主要由进料漏斗、塑化螺杆、料筒、加热圈、测温电偶、步进电机和喷嘴等部件组成。打印过程中,物料通过进料漏斗进入挤出料筒,步进电机在控制系统的控制下驱动螺杆将物料往喷嘴处输送,与此同时加热圈在温控系统的控制下保持略高于物料熔点的温度,物料在料筒中熔融,并在螺槽中被压实和均化,然后被输送到喷嘴的物料被选择性的沉积到打印平台上,一层完成后,打印平台下降一层的厚度进行下一层的沉积,如此循环形成所需要的陶瓷坯体。
本文使用的螺杆被设计成槽深渐变型三段式螺杆,螺杆主体部分由加料段、压缩段和计量段组成。螺杆的直径设计为12 mm,长径比为17,加料段螺槽深度为3 mm,计量段螺槽深度为1 mm,螺杆与料筒之间的间隙根据加工精度设计为0.05 mm。螺杆挤出供料模块如图1所示。
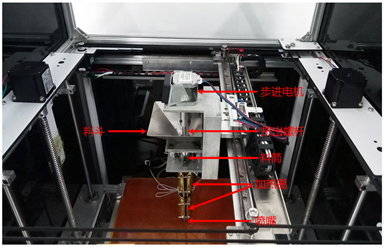
Figure 1. Structure of screw extrusion modulus
图1. 螺杆挤出模块结构
2.2. 打印耗材制备
采用3 mol%氧化钇稳定的氧化锆粉末,其平均粒径为0.15 μm,比表面积为8.21 m2/g (YSZ-FD-M3.0,江西九江泛美亚高科技材材料有限公司)。粘结剂主要由乙烯–乙酸乙烯酯共聚物(EVA) 25%,聚乙烯(PE) 20%、石蜡(PW) 50%和硬脂酸(SA) 5%组成。首先将陶瓷粉末和粘结剂在加热温度为140℃~150℃的双辊机(SK-160,上海双翼橡塑机械有限公司)上混合40~50分钟,然后冷却至室温,最后使用颚式破碎机将喂料破碎成直径3~5 mm左右的颗粒状材料。
2.3. 挤出流量模拟
根据螺杆的设计参数,使用ANSYS软件的建模功能构建螺杆计量段的几何模型和流道求解域模型,如图2所示。由于螺杆挤出系统中的螺杆是转动的,利用相对运动原理,假设螺杆附近区域流体流速与螺杆转速相同,设置为动网格模型。为了减少因螺杆运动而重复进行网格划分的工作量,本次模拟中使用了Ployflow软件包提供的网格叠加技术(Mesh Superposition Technique,简称MST)来生成有限元网格。主要分两个部分进行网格划分,即螺杆结构部分和流场求解域部分,求解域采用八点六面体单元网格划分,螺杆部分采用四面体单元网格划分,然后使用MST技术进行网格叠加。
(a) 螺杆计量段几何模型
(b) 求解域几何模型
Figure 2. Geometry modeling of screw
图2. 螺杆几何模型
2.4. 挤出流量和挤出线材直径测试
在不同喷嘴直径下(喷嘴直径选取0.2 mm、0.4 mm、0.6 mm、0.8 mm和1.0 mm),探究螺杆转速(在0~25 r/min范围内选取)和挤出温度(在130℃~190℃选取)对挤出流量和挤出线材直径的影响。以1分钟为单位时间进行挤出,共收集3组挤出线材的实验结果,使用电子天平进行称量取平均值作为该工艺参数下的挤出流量。取3组挤出线材,采用游标卡尺测其直径,取平均值。
2.5. 打印、脱脂和烧结工艺
在挤出温度190oC、螺杆转速15 r/min、喷嘴直径0.6 mm条件下,分别在打印层厚为0.1、0.15和0.2 mm时,打印60 mm × 7 mm × 6 mm的长方体样条。
首先将打印好的陶瓷生坯放置于50℃的煤油中进行溶剂脱脂24 h,样品取出后在45℃的烘箱中干燥20 h。热脱脂过程中,首先将脱脂炉以100℃/h的升温速率加热至200℃,然后再以9.5℃/h的升温速率加热至600℃,在600℃保温30 min。热脱脂完成后,将样品置于烧结炉中,烧结炉以2.5℃/min的升温速率加热至1500℃,在1500℃保温2 h。
2.6. 性能测试与显微结构观察
根据GB/T6569-2006精细陶瓷弯曲强度试验方法,使用计算机伺服拉伸试验机(PT-1176,D1919SFRX,宝达仪器有限公司)测量陶瓷3D打印的氧化锆标准样条的三点抗弯强度。使用场发射扫描电子显微镜(FESEM, S-4800, Hitachi, Japan)观察挤出线材和3D打印氧化锆样品的显微结构。
3. 结果分析与讨论
3.1. 螺杆挤出流量
不同挤出温度和螺杆转速下质量流量的模拟和实验结果如图3所示,挤出线材如图4所示。由图3可知,无论是模拟分析还是实际挤出实验,挤出温度对挤出流量的影响都较小,与图4结果一致,这有利于打印过程的精确控制。但螺杆转速对挤出流量的影响较大,随螺杆转速的增加有显著增加。实际实验的挤出量与模拟的挤出量基本接近,但普遍存在偏差。模拟和实验结果的误差一方面是由于模拟中采用的是等温模拟,而实验中温度是有波动的,另一方面模拟中选用幂律模型的本构方程,未考虑弹性行为的影响。此外模拟中没有充分考虑喷嘴阻力对挤出流量的影响。
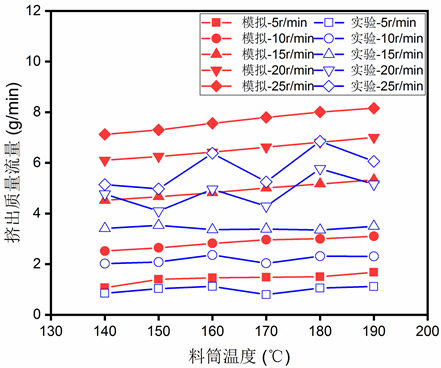
Figure 3. Relationship between extrusion flow rate and temperature, screw speed
图3. 挤出质量流率与挤出温度、螺杆转速的关系
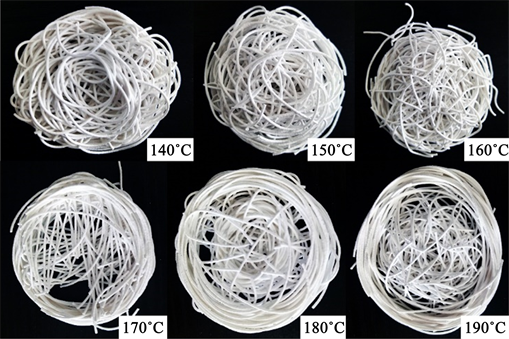
Figure 4. The picture of extruded wire at different extrusion temperatures (0.6 mm, 15 r/min)
图4. 不同挤出温度下挤出线材实物图(0.6 mm喷嘴、螺杆转速15 r/min)
3.2. 挤出线材直径
图5为螺杆转速15 r/min时,不同喷嘴直径下,线材直径随挤出温度的变化。实验结果表明,挤出温度对线材直径的影响较大,当挤出温度升高时,氧化锆喂料的挤出线材直径变小,最终与喷嘴直径一致。出现这一现象的原因可能是聚合物粘合剂PE和EVA被用作原料中的可流动载体,导致了挤出膨胀现象。如图6所示,挤出膨胀在低温挤出时尤其明显,在挤出温度为130℃的情况下,随着螺杆转速的增加,挤出线材直径波动大,甚至出现难以挤出的现象。这表明在低的挤出温度下,挤出线材的直径不稳定且不可控,不利于3D打印过程的精确控制。在挤出温度为190℃时,挤出线材表面光滑(图7(a)),断面均匀致密(图7(b))。
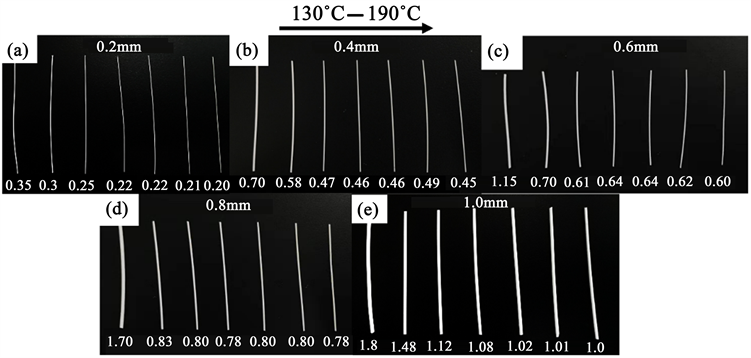
Figure 5. Relationship between extrusion wire diameter and temperature: nozzle diameter (a) 0.2 mm; (b) 0.4 mm; (c) 0.6 mm; (d) 0.8 mm; (e) 1.0 mm
图5. 线材直径随挤出温度的变化:喷嘴直径(a) 0.2 mm;(b) 0.4 mm;(c) 0.6 mm;(d) 0.8 mm;(e) 1.0 mm
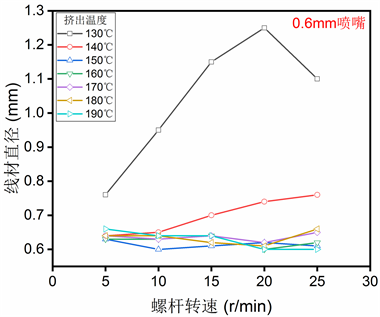
Figure 6. Relationship between extrusion wire diameter and screw speed (0.6 mm)
图6. 挤出线材直径随螺杆转速的变化(0.6 mm喷嘴)
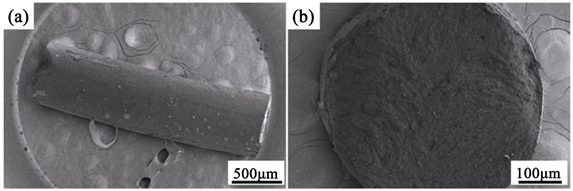
Figure 7. SEM image of extruded wire (a) Surface; (b) Cross section
图7. 挤出线材SEM图(a) 表面;(b) 截面
3.3. 可靠性分析
抗弯强度的韦布尔模量通常用于反映材料强度的分散性。韦布尔分布函数可以用以下公式表示 [14]:
(1)
等式两边取自然对数可得出:
(2)
在上式中,Pn,
,
和m分别表示断裂几率,对应样品的抗弯强度,特征强度和韦布尔模量。
不同打印层厚样品的韦布尔分布如图8所示。结果表明0.1 mm,0.15 mm和0.2 mm 3个打印层厚度下的韦布尔模量分别为4.83,5.89和4.14。在打印层厚度为0.15 mm时可以获得可靠性相对较高的氧化锆陶瓷,但与等静压成型等工艺相比,本研究得到材料的韦布尔模量相对较低,这可能源自可能存在的层间空隙或层间结合不充分,将在后续工作中进一步研究。
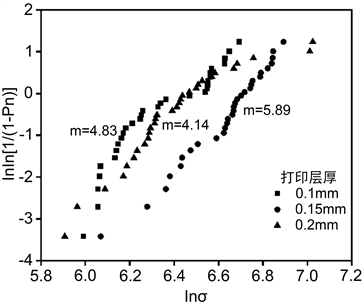
Figure 8. The Weibull distribution of flexural strength of zirconia ceramics with different print layer thicknesses
图8. 不同打印层厚下氧化锆陶瓷抗弯强度的韦布尔分布
3.4. 微观形貌分析及复杂形状陶瓷部件制备
氧化锆生坯和烧结体的表面和截面的SEM图像如图9所示。从图9(a)可知,打印坯体表面结构均匀,局部放大图上可以看到的纤维的状粘结剂分子。如图9(b)所示,高温烧结后得到的氧化锆陶瓷材料结构致密,晶粒尺寸均匀。
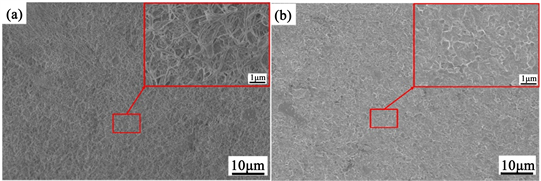
Figure 9. SEM image of (a) The cross section of the printed green body; (b) The cross section of the sintered body
图9. (a) 打印坯体断面;(b) 烧结体断面的SEM图
图10所示为采用基于螺杆挤出的FDM设备成型制备的复杂形状陶瓷零件。图10(a)为氧化锆齿轮,外圈的大齿轮与内圈小齿轮一次打印成型,烧结后齿轮之间配合良好,证明了此方法具有较好的维形能力和打印精度。图10(b)为打印的氧化锆扭曲空腔体。图10(c)和图10(d)为改变填充方式后打印的蜂窝结构。
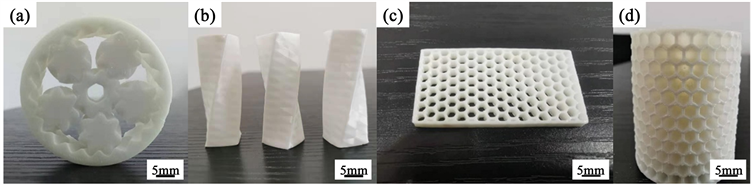
Figure 10. Complex zirconia parts fabricate by 3D printing (a) Gear; (b) Twisted hollow structure; (c) Rectangular honeycomb; (d) Cylindrical honeycomb
图10. 陶瓷打印件(a) 齿轮;(b) 扭曲花瓶;(c) 长方形蜂窝;(d) 圆柱形蜂窝
4. 结论
采用螺杆挤出机构的FDM平台适合高固相含量氧化锆颗粒混合料的3D打印。研究表明,挤出质量流量主要取决于螺杆转速,而挤出温度对挤出质量流量影响不大。在较高的挤出温度下可以获得均匀稳定的挤出线材,有利于打印过程的精确控制。合理的打印层厚有利于提高材料的可靠性,低可靠性可能源自层间空隙和不充分的界面结合。FDM方法利于制备结构致密、晶粒均匀的氧化锆陶瓷,在制备复杂形状陶瓷部件中体现了较好的维形性能和尺寸精度。
基金项目
这项工作得到了中国国家自然科学基金(批准号51572035)的资助。
NOTES
*通讯作者。