1. 引言
金属锌粉作为橡胶工业必不可少的添加剂,也被广泛用于涂料、医药、玻璃行业 [1] [2]。超细锌粉是一种高性能金属材料,制备锌粉是开发利用锌资源,提高其附加值的有效途径 [3]。制备超细锌粉的传统工艺以粗锌为原料,对原料的要求高,对杂质的要求很严格 [4] [5],存在步骤复杂、能耗高、金属损耗严重等不足 [6]。随着我国工业对超细锌粉的需求不断增大,亟待开发短流程制备超细锌粉技术,提高其附加值的有效途径,还有效避免了二次能源的浪费,降低了原料成本。有色冶炼过程产生大量的氧化锌烟尘,富含锌金属元素,目前已有大量研究对其资源化利用以回收有价金属 [7] [8] [9] [10] [11]。然而,利用氧化锌直接制备超细锌粉的研究尚未有相关报道。本研究采用的还原–精馏技术制备超细锌粉工艺技术,具有工艺流程简短、金属直收率高、且热能利用率高的优点,已建成工业化试验,以低品位氧化锌烟尘为原料、焦炭为还原剂,结合有价金属铅、锌的高温挥发特性,探究超细锌粉的回收效果,研究结果为氧化锌烟尘的资源化利用提供基础数据和参考借鉴。
2. 试验
2.1. 原料
试验采用的低品位氧化锌烟尘为灰黑色粉末,产自于云南省某铅锌冶炼企业,化学成分见表1。其主要化学成分主要为:Zn 32.40%、Pb 0.94%、S 19.98%、CaO 10.59%、MgO 0.93%、Al2O3 1.12%、SiO2 3.75%、Fe 7.99%、As 0.28%、F 0.13%、Cl 0.14%。试验采用的还原剂焦炭化学成分见表2。
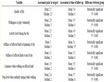
Table 1. Components of the low grade dust of zinc oxide
表1. 低品位氧化锌烟尘的化学成分(wt%)
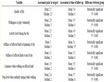
Table 2. Components of the reducing coke
表2. 焦炭的成分分析
2.2. 工艺流程
采用低品位氧化锌烟尘制备超细锌粉,以实现锌、铅有价金属资源化利用。其工艺流程图见图1。在还原剂焦炭和助剂石灰的作用下,氧化锌烟尘在电炉还原挥发熔炉,转化为蒸汽形态,经过冷凝后流入熔锌炉保温,脱除锌浮渣后转入铅塔,通过多次回流除铅形成高纯度锌蒸气,直接冷却形成的高纯度金属锌粉。副产的锌浮渣和高铅锌可回用或外售,水淬渣用于生产建筑材料。
3. 理论分析
利用氧化锌烟尘铅锌制备超细锌粉是一个高温反应过程,铅、锌及其氧化物的物理特性对反应的影响甚大。其熔点、沸点及挥发情况见表3。
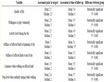
Table 3. Melting point and boiling point of lead, zinc and their main compounds
表3. 铅、锌及其主要化合物的熔点和沸点
超细锌粉制备工艺反应过程中,氧化锌烟尘中金属氧化物与C直接发生还原反应,生成金属单质 [9]。随着反应进行,CO逐渐产生后参与反应,促进生产金属单质。其主要反应如下:
(1)
(2)
(3)
(4)
炉料从100℃逐渐加热到1000℃,炉料中的PbO首先被还原,随着炉料温度的升高,经历固态PbO与CO反应生成固态Pb、液态Pb,液态PbO与CO、C反应生成液态Pb的过程。炉料加热到1000℃~1300℃,炉料中40%的ZnO被还原成Zn,随着反应的进行,炉料熔化造渣,ZnO会熔于渣中,还原变得越来越难。因此,矿热电炉生产高纯锌粉的关键在于炉料造出较高熔点的渣,从而使得低温下炉料ZnO尽可能多被还原成Zn蒸气 [10]。
反应体系热量对物质的反应过程至关重要。采用HSC热力学计算软件(Chemistry7.0)对反应体系进行热力学分析 [12]。其热力学数据如表4所示,四个反应均为吸热反应,随着温度的升高,ΔG逐渐减小。随着温度的逐渐升高,反应(3)和(4)先发生,符合Pb的挥发温度较低的物理特性;氧化锌挥发为锌蒸气的起始温度由反应(1)的关系曲线计算为948℃。
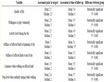
Table 4. Relationship between temperature and reduction reaction ΔG of lead and zinc oxides
表4. 铅、锌氧化物还原反应ΔG与温度的关系
注:表中热力学数据采用HSC Chemistry 7.0热力学模拟软件计算获得。
4. 结果与讨论
4.1. 运行情况
为充分对氧化锌烟尘中有价金属进行综合回收,采用还原-精馏工艺制备高附加值的超细锌粉,氧化锌在电炉1000℃~1200℃温度下还原挥发后,经冷却直接进入熔锌炉保温,温度设为500℃,去除锌浮渣后的锌液转入铅塔,在1100℃~1200℃温度下高温挥发,锌完全蒸发为蒸气,经过多次冷凝后冷却形成超细锌粉;铅塔出口得到富集的高铅锌。氧化锌烟尘与焦炭的配比约为10:1,混合物料在整套设备的停留时间约为6 h,工艺运行期间,熔锌炉、铅塔运行稳定、温度正常,锌回收率高。
4.2. 超细锌粉回收效果
在中试运行期间超细锌粉的含量以及直收率见表5,所得超细锌粉的纯度维持在99.991%,而其直收率高达在93.199%。工艺回收效果显著,工艺条件稳定,能够实现氧化锌的资源化利用。
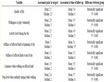
Table 5. Content and direct yield of superfine zinc powder
表5. 超细锌粉的含量及其直收率
4.3. 副产物成分分析
高温条件下,有价金属铅、锌在挥发过程中会损耗部分金属,随电炉焙烧进入到水淬渣。熔锌炉保温时,杂质元素随锌浮渣排出,同时带走大量的金属锌;铅塔在1100℃左右温度时,已经过提纯的锌挥发为蒸气,金属铅随高铅锌从塔底排出。分别对产生的锌浮渣、高铅锌和水淬渣进行成分分析,结果如表6所示。
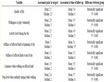
Table 6. The component of the water-quenched slag
表6. 副产物成分分析(%)
4.4. 产品表征
4.4.1. 高纯锌粉粒径分析
本研究获得产品超细锌粉的粒度分布见图2。不同粒径的产品数量与其粒度的对数函数成正态分布,超细锌粉的粒径介于2~20 μm,其中粒径为8 μm的锌粉累积分布高达14%。本产品粒径大小均匀,说明控制条件精准。
4.4.2. SEM分析
超细锌粉分别在1000倍和5000倍电镜下的微观形貌见图3。
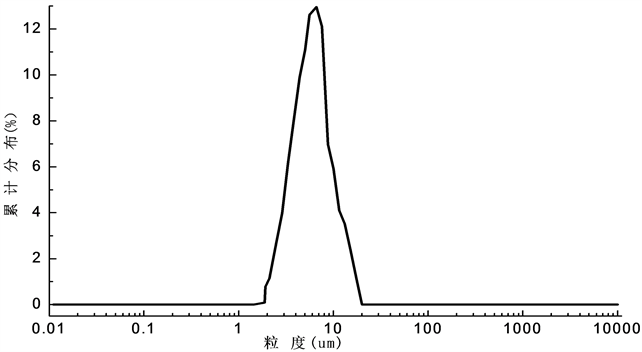
Figure 2. Particle size distribution of superfine zinc powder
图2. 超细锌粉粒径分布图
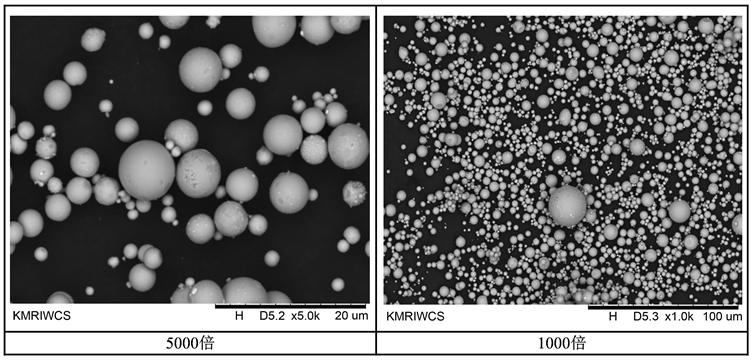
Figure 3. Scanning mirror diagram of superfine zinc powder
图3. 超细锌粉的扫描电镜图
由图3可以看出,超细锌粉粒径分布比较均匀、颗粒大小相近、呈球形、表面杂质较少,而表面出现杂质的球形锌粉形状不规则。分析猜测,超细锌粉在冷凝成型时,其形状易受到杂质的影响,锌粉的形貌可能直接与其纯度存在联系。
5. 物料衡算
5.1. 总物料平衡
本研究采用低品位氧化锌烟尘作为原料、焦炭为还原剂、石灰为助剂,还原–蒸馏法工艺处理后产出产品超细锌粉和副产物锌浮渣、高铅锌和水淬渣,并折算出烟气及其他损失。工艺的总物料平衡见表7。
5.2. 元素平衡
低品位氧化锌烟尘制备超细锌粉工艺的锌、铅元素平衡分析见表8。
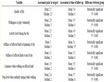
Table 8. Element balance of zinc and lead
表8. 锌、铅元素平衡
从表8可以看出,高温挥发后的锌主要进入主产品超细锌粉中,其比例高达93.20%。水淬渣中的金属锌量很低,仅为总锌量的0.35%。工艺处理过程的铅元素主要富集于高铅锌中,其占比为92.32%,锌浮渣中铅的比例达5.32%,水淬渣固化的金属铅是总铅的2.45%。元素平衡计算结果表明,该工艺能够实现有价金属铅、锌的高效回收。
6. 结论
1) 利用低品位氧化锌烟尘还原–精馏制备超细锌粉,产品纯度高达99.991%,锌直收率为93.199%,表明还原–精馏工艺处理氧化锌烟尘制备超细锌粉是可行的。
2) 元素平衡结果表明,锌主要富集于产品超细锌粉中,铅元素主要富集于高铅锌中,其占比为92.32%。
3) 超细锌粉的制备工艺流程简单、操作简便,有价金属回收效果显著,能够为氧化锌烟尘高附加资源化利用提供参考。
基金项目
省部共建复杂有色金属资源清洁利用国家重点实验室开放课题(CNMRCUKF1804);云南省科技计划项目(2018FD137)。
NOTES
*第一作者。
#通讯作者。