1. 引言
电动主给水泵系统,由三台50%额定流量的电动主给水泵组成,正常工况下两台主给水泵运行,一台给水泵备用。每台电动主给水泵组由前置泵、电动机、液力联轴器及压力级泵等串联布置组成。电动主给水泵组将除氧器的水抽出并升压送到蒸汽发生器。同时压力级泵能响应变速要求,以保证在反应堆整个热负荷范围内向蒸汽发生器提供不同的给水流量。该电动主给水泵组在运行期间需进行切列运行,泵的启停导致管道承受严重的水力冲击。该研究针对不同运行工况下泵组中联管所受到的水力载荷及动力载荷计算管道受力及位移情况,判断管道及支架强度是否满足规范要求,同时需考虑支架位置优化和布局,减小管道应力、降低支架断裂风险。
目前国内通过FLOWMASTER计算软件计算水泵在变工况运行时水流冲击力的压强变化已经十分成熟,通过FLOWMASTER一维流体软件计算峰值压力,以此确认管道强度是否满足要求 [1] [2] [3],同时通过改变支架形式及安装方式降低管道应力及支架断裂风险。
本文通过FLOWMASTER计算管道受水流冲击力强度和频率的数值解,将该数值解作为CASERII软件的边界条件,对管线的一次应力和二次应力进行计算分析,并根据ASME B31.1-2012规范中的相关内容对结果进行评估,分析应力是否满足要求。这种时程分析法可以快捷高效的计算水流冲击力,同时保证计算结果的准确性。
2. 水锤力计算模型
2.1. 压力峰值估算模型
水锤实际上是由于水流速度变化而产生的惯性力。当突然启停泵时,由于启停时间短、流量变化快,因而水击压力往往较大,而且压力波的瞬态变化过程剧烈。由于管壁具有弹性和水体的压缩性,水击压力将以弹性波的形式沿管道传播。水击波传播过程中,在外部条件发生变化处(即边界处)均要发生波的反射。其反射特性(指反射波的数值及方向)决定于边界处的物理特性。
水锤计算基本公式:
a. 钢管中水锤波传播速度α值:
式中:1425——声波在水中的传播速度(m/s);
ε——水的弹性模量,ε = 2.1 × 104 (kg/cm2);
E——管壁的弹性模量,E钢 = 2.1 × 106 (kg/cm2);
D——压力管道的内径(mm);
δ——管壁厚度(mm)。
b. 水锤波在水管中传播来回一次所需时间:
式中:L——压力钢管总长度(m);α——水锤波传播速度(m/s)。
为计算流动条件变化引起的瞬时最大压力增幅,引入瞬时水锤计算方程 [4]:
ΔP为压力震荡变化值Pa,ρ为介质密度kg/m3,ΔV为介质速度变化m/s。该公式可用于水锤发生时计算最大压力震荡值。
2.2. 水锤力的数值解法
通常在求解管道中的水锤问题时,均是把流动看做一维非定常流动,它的基本方程可推导如下。
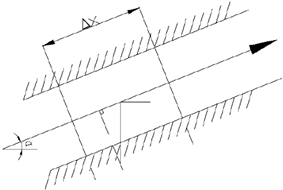
Figure 1. Schematic diagram of micro-element segment
图1. 微元段示意图
运动方程:
为了推导流体在管道中作不定常流动的运动方程,在管道中取一长为∆x的流体微元,如图1所示,该微元的横截面积等于管道的横截面积A,根据牛顿第二定律应有
(1)
作用在微元流体段上的力由三部分组成,即压差力,重力以及摩擦力或粘性阻力,忽略高阶小量之后,这三部分力在x方向的投影可依次表示为
上述压力差的表达式不仅适用于等截面的管道,对于锥形等变截面管道也是正确的,粘性阻力表达式是利用了管道沿程损失公式,式中的f就是沿程损失系数,通常和流动的雷诺数Re以及管道的相对粗糙度有关。
微元流体段的质量为
加速度在流体力学里常用欧拉法表示,在X方向的加速度分量可表示成
式中,
称作当地加速度,
称作迁移加速度。
把以上诸式带入(1)可得
(2)
这就是管道中不定常流动的方程。
对于液体流动,经常可用任意基准算起的水力坡度线高度H来代替压强p,它们之间的关系是
(3)
式中,Z是管子中心线在x处的标高,把H带入到
中,有
因此运动方程还可写成
(4)
式中,用
代替了
,这样可以保证粘性阻力的方向始终是同速度的方向相反。
连续方程:
对于所取微元段流体,不管它如何运动,根据质量守恒原理,总有
(5)
展开此式并稍作整理后有
(6)
以上就是考虑了管道响应的连续性-动量方程 [5] [6],FLOWMASTER等软件,都是通过设置边界条件和几何条件,利用内置求解器求解微分方程来分析管道的水锤问题。
3. 建模过程
3.1. 一维流体建模过程
选取电动给水泵上下游的稳定压力源边界,对泵及管道系统进行建模。模型以ADG除氧器为上游压力边界,主给水高压进口联箱为下游压力边界,三列电动给水泵组从除氧器取水,增压后通过管网将除氧水送至高压加热器 [7]。建模节点如图2所示:
边界条件设定为除氧器压力:8.07 bar.g,主给水高压进口联箱压力:77.5 bar.g。选择基于压力的瞬态求解器,不考虑传热模型,忽略温度变化对流体物性参数的影响,流体设为定温。根据时程分析方法,建模后启动瞬态计算,输出中联管不同工况下所有弯头处的压强,并得出每个弯头处的受力曲线。
3.2. 管道应力建模过程
根据现场实际情况,同时建立两个管道模型(图3、图4),模拟支架A15未断裂和支架A15已断裂(即认为取消A15支架约束)两种情形(下文简称为模型一和模型二)。
根据水力载荷计算的切列、停机、启机三种工况(下文简称工况一、工况二、工况三),将输出的时程响应谱导入进CAESARII软件中,根据水锤特性选取受影响的弯头、孔板、三通处节点进行加载,对管线进行频谱分析。同时对管线的一次应力和二次应力进行分析计算,并根据ASME B31.1-2012规范中的相关内容进行评估结果。
模型先进行静力分析,然后通过DYNAM模块进行动态分析,动态分析中选取响应谱分析对水锤响应进行模拟。本报告选取保守的结论,同时也根据水锤简化计算公式进行等效静力计算对比结论。管道模态只取前12阶进行展示。
4. 水力建模结果
4.1. 工况零
稳态工况:
三台泵组其中1/2号泵组处于运行状态,3号泵组处于停泵状态,此时前置泵出口管线压力为2.1 Mpa,压力级泵出口压力为7.75 Mpa。在稳态下的管线压力值与电厂监测系统中同样位置压力测量值相同。因此可确保该流体计算模型计算准确性。
4.2. 工况一
切列工况:
初始状态下1/3号泵组处于运行状态,2号泵组处于停运状态。在0 s时刻,3号泵组停运,经4 s后完全停止。在第5 s时2号泵组启动,经过6 s,2号泵组运行达到额定工况。计算该运行过程之中的中联管水锤力,输出管道水锤力随时间变化关系,如图5和图6所示。
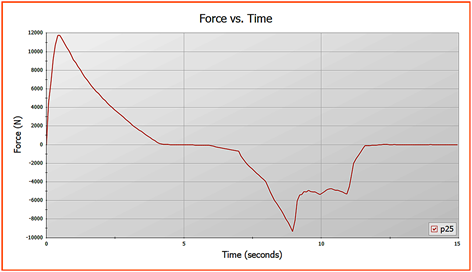
Figure 5. Water hammer force curve of No. 2 Pump
图5. 二号泵中联管水锤力变化曲
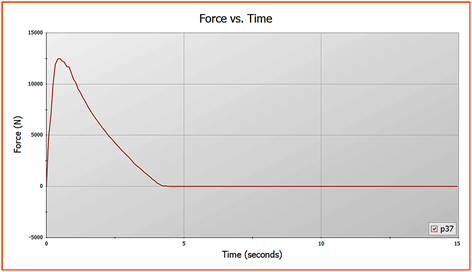
Figure 6. Water hammer force curve of No. 3 Pump
图6. 三号泵中联管水锤力变化曲
4.3. 工况二
停机工况:
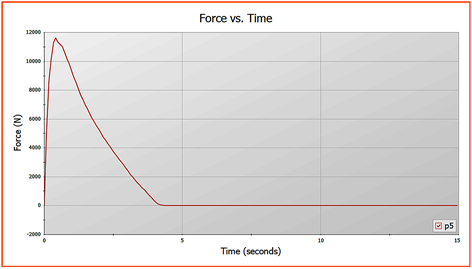
Figure 7. Water hammer force curve of No. 1 Pump
图7. 一号泵中联管水锤力变化曲
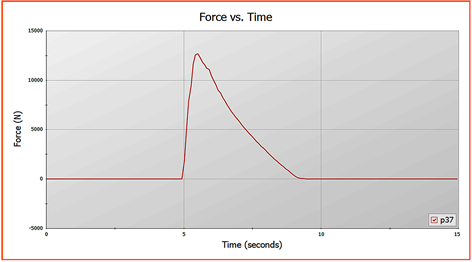
Figure 8. Water hammer force curve of No. 3 Pump
图8. 三号泵中联管水锤力变化曲
初始状态下1/3号泵组处于运行状态,2号泵组处于停运状态。在0 s时刻,1号泵组停运,经4 s后完全停止。在5 s时刻,3号泵组停运,经4 s后完全停止。2号泵组始终处于停运状态。计算该停机过程之中的中联管水锤力,输出管道水锤力随时间变化关系,如图7和图8所示。
4.4. 工况三
启机工况:
由于软件计算迭代需要,泵的初始运行状态需从额定工况开始,因此初始状态下三台泵组处于停运状态可设置为0秒时刻三台泵组均为额定工况,1 s时刻同时全部停止。在4 s时刻,1号泵组启动,经6 s后达到额定工况。在11 s时刻,2号泵组启动,经6 s后达到额定工况。计算该启机过程之中的中联管水锤力,输出管道水锤力随时间变化关系,如图9和图10所示。
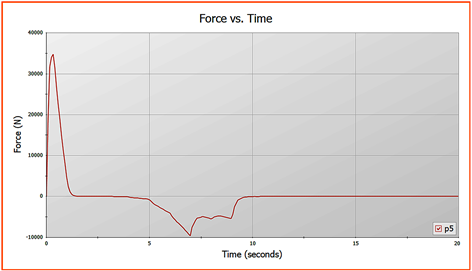
Figure 9. Water hammer force curve of No. 1 Pump
图9. 一号泵中联管水锤力变化曲
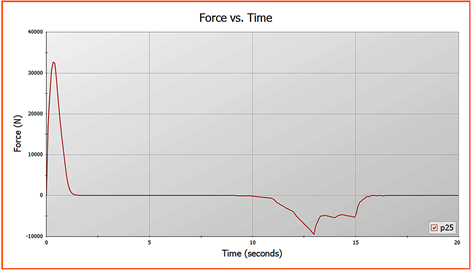
Figure 10. Water hammer force curve of No. 2 Pump
图10. 二号泵中联管水锤力变化曲
5. 管道应力建模结果
模型先进行静力分析,然后通过DYNAM模块进行动态分析,动态分析中选取响应谱分析对水锤响应进行模拟。本报告选取保守的结论,同时也根据水锤简化计算公式进行等效静力计算对比结论。管道模态只取前12阶进行展示(表1)。
5.1. 管道应力分析结果
管道一次应力、二次应力及动态应力均通过校核。管道一次应力、二次应力结果见表2,管道动态分析三种工况应力最大工况(切列工况)结果见表3。
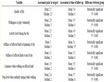
Table 2. Primary and secondary stress analysis result
表2. 一、二次应力分析结果
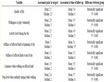
Table 3. Cut out condition stress analysis result
表3. 切列工况动态应力分析结果
5.2. 断裂支架(A15支架)载荷
各工况支架A15节点载荷如表4所示。
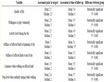
Table 4. A15 node load under various working condition
表4. 各工况支架A15节点载荷
5.3. 断裂支架(A15支架)位移
各工况支架A15节点位移如表5所示。
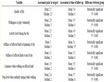
Table 5. Displacement of A15 node in working condition
表5. 各工况支架A15节点位移
从上述结果可得,在切列工况2号泵组中联管A15支架动态载荷最大,其绝对值为2946 N,叠加X方向静态载荷478 N,A15支架所受压力2468 N或拉力3424 N,在其允许载荷范围之内(18,000 N)。A15支架在动静态叠加后,X方向最大位移为−0.05~0.30 mm,Y方向最大位移为−9.32~0.01 mm,Z方向最大位移为−10.98~1.69 mm。
综上所述,在管道自重、热胀及起停泵冲击力等作用下,管道应力满足要求,A15支架载荷在允许载荷范围之内。取消A15支架管道强度仍满足标准要求,但是取消A15支架载荷重新分布,会导致部分支架和泵接口载荷、中联管上下游支架载荷进一步增大,不利于现场设备稳定运行。
6. 改进方案
将A15支架结构型式从图11改为图12,取消管道侧的铰链结构,用固定支撑件代替。
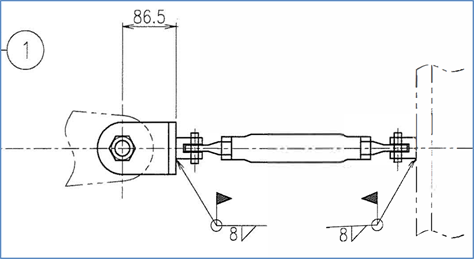
Figure 11. Support structure before transformation
图11. 改造前支架结构
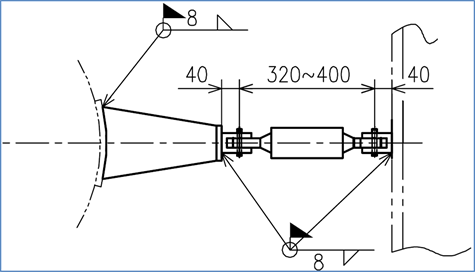
Figure 12. Support structure after transformation
图12. 改造后支架结构
原始A15支架由于铰链销与销座之间存在间隙且该结构为不稳定形式。不可避免的导致在管道产生热位移时会使件铰链与拉杆之间产生角度。根据管道图纸信息,设备运行时管道存在向下5.48 mm的热位移,根据该热位移值在CAD软件中对支架结构进行画图计算,会导致件铰链与拉杆之间产生12˚的角度,如图13所示。其角度值超过规范中6˚要求。
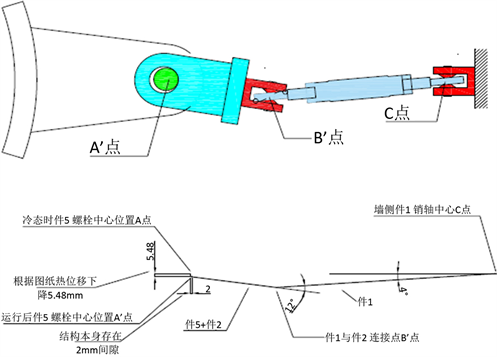
Figure 13. The original A15 support produce an angle during operation
图13. 运行时原A15支架产生角度
改进后A15支架取消原铰链结构,将拉杆直接与管道销座相连。根据上文对管道热位移及水力载荷的叠加效果,管道在运行时会产生向下10.98 mm的位移,此时热位移值远大于图纸所示管道热位移值。即使支架安装时,维修人员现场实施存在拉杆两端水平高度偏差9 mm的督查,在此极端工况下,拉杆与销座仅产生3˚角度,满足支架运行6˚偏移角度要求。可保证现场A15支架稳定运行。改进后支架偏移情况如图14所示。
对新增焊缝进行校核:
根据章节5,A15支架受到最大拉力F = 3424 N,新增焊缝钢板的厚度为δ1 = 12 mm,焊缝长度为L = 80 mm。根据RCCM H3282.2角焊缝焊喉截面应力极限最小值为125 MPa。
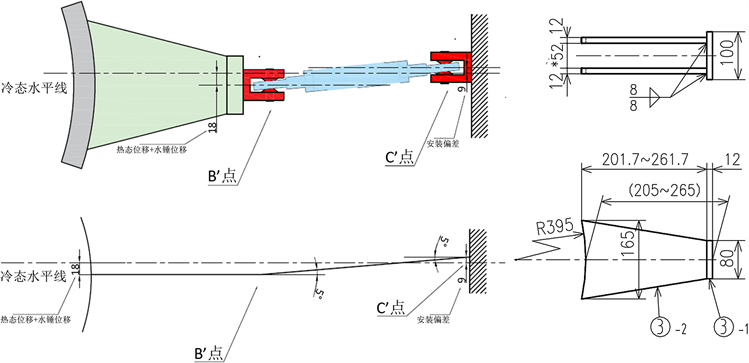
Figure 14. The A15 support produce an angle during operation after transformation
图14. 运行时改进后A15支架产生角度
新增钢板焊缝强度满足要求,结构工作安全。
7. 总结
本文通过水力学和结构力学软件的瞬态分析功能,建立了核电厂电动主给水泵系统各工况下的流体和管道应力分析模型。利用FLOWMASTER软件模拟得到流体冲击造成的管道两端受力不平衡图谱,为CASERⅡ管道应力建模提供输入条件,计算不同运行工况下水流冲击力产生的应力影响和疲劳振动影响。根据受力不平衡的时程图谱分析水锤的时程分析方法,可以清晰的计算出水锤力的真实强度和频率,准确判断管道是否存在应力超标情况,便于高效快速评估电厂水泵运行造成的管道振动问题,为管道改进方案提供准确的参考依据。CPR1000核电厂类似泵组运行造成的水锤问题均可采用该时程分析方法进行评估研究。