1. 引言
随着铁路跨越式大发展步伐的加快,重载、高速逐渐成为当今乃至以后一段时间内铁路发展的目标,铁路货车运用频次显著增加,对其运用安全性是严峻的考验,从而对铁路配件连接的可靠性、安全性提出了更高的要求。拉铆钉又被称为虎克螺栓,最早是为航空航天工业开发,因为其独特的环槽结构、高夹紧力和抗剪力、高耐腐蚀性和连接过程环保等优点被铁道部引进并应用于铁路货车领域 [1] 。本文以C70E型通用敞车为研究对象,研究铁路货车典型拉铆连接结构的可靠性。
C70E型通用敞车车体前后从板座与牵引梁腹板之间采用了型号为LMY-T22的拉铆钉连接,局部结构如图1所示。
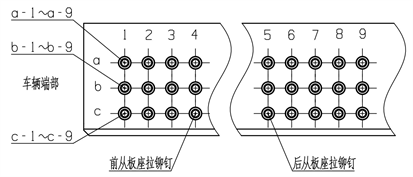
Figure 1. Typical riveting connection structure of C70E
图1. C70E型通用敞车典型拉铆连接结构
拉铆连接结构可靠性分析普遍采用有限元方法进行,铆钉局部有限元建模的难点在于提出一种可以在保证计算效率的同时,最大程度模拟铆钉与夹紧件之间接触关系的有限元模型。本文旨在通过有限元法对C70E型通用敞车典型拉铆连接结构进行有限元仿真,得到铆钉群的受力分布,找出局部铆钉群中受力最大的铆钉,并通过DVS-EFB 3435-2技术公报对其进行可靠性评估。
2. 拉铆连接结构有限元建模方法
2.1. 探究模型介绍
为了对拉铆连接结构有限元建模方法进行探究,本文以两块尺寸均为365 mm × 110 mm的铆接板作为研究对象,铆接板上开了两个相同孔径的圆孔用于铆接,其铆接区域厚度为10 mm。两块铆接板分别用两颗型号LMY-T16的拉铆钉连接。其连接结构如下图2所示。
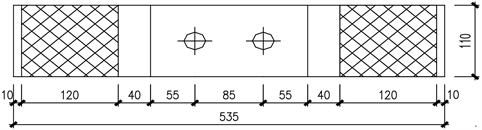

Figure 2. Research model of rivet connection
图2. 拉铆连接探究模型
2.2. 实体单元模型
铆接结构相对于传统的焊接结构在其受力及力的传递上都较为复杂,为了更加准确的获取铆钉于其周边区域的真实受力情况,现需要对其结构进行有限元建模。为了保证有限元仿真结果的可靠性,本文采用Solid185实体单元离散拉铆钉,基于铆接后拉铆钉是铆死,套环是不能拆卸的,如果想将零件拆分,必须将拉铆钉破坏的特征,考虑将铆钉的套环与铆钉杆之间在有限元建模时就将其作为一体。此模型将作为后续铆接结构有限元简化方法的评判基准。
为了模拟铆钉与连接件之间的接触关系,在铆钉与夹紧件之间建立弹性体接触,同理两块夹紧件之间也进行同样的处理,这样可以最大程度的模拟铆接结构的真实连接关系,并在铆钉杆连接段中部建立预紧力单元并施加预紧力。其中接触单元可以在一定程度上模拟铆接结构之间的摩擦效应,而预紧力单元则可以模拟铆钉在冲压完成后对夹紧件的挤压效应。拉铆连接实体单元模型如下图3所示。
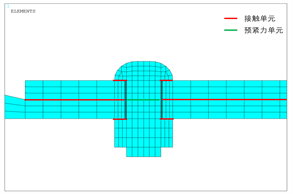
Figure 3. Solid element finite element model
图3. 实体单元有限元模型
2.3. 简化梁单元模型
温朋哲提出采用壳单元离散铆接板,MPC184刚性梁单元模拟铆钉杆,在此基础上分别采用三种建模方法模拟铆钉杆与铆接板之间的连接关系,并通过对比分析得出采用壳单元模拟连接关系的方法最合适 [2] 。陈海欢通过基于MSC.NASTRAN有限元分析软件,用四种简化模型计算分析单搭接多排铆钉连接结构的钉载分配,并对其进行对比研究,结果表明:采用CBAR/RBAR/CBUSH组合单元模拟紧固件可准确计算钉载 [3] 。
铆钉杆的模拟方式有多种,常见的有弹簧单元模拟方式、普通梁单元模拟方式以及刚性梁单元模拟方式。在针对大型铆接结构的整体应力分布进行评估的情况下,推荐使用刚性单元对铆钉杆进行模拟。铆钉与夹紧件之间接触关系使用BEAM188梁单元模拟,BEAM188单元是线性的每个单元有两个节点,每个节点上有6或7个自由度,包括3个平动自由度和3个转动自由度,该单元非常适合线性、大旋转大应变的非线性计算。梁单元简化模型由MPC刚性梁单元模拟铆钉杆,并由单元的两端节点发散一把单元类型为BEAM188的梁单元至铆钉与被铆接件的接触面节点来模拟接触关系。简化模型如下图4所示。
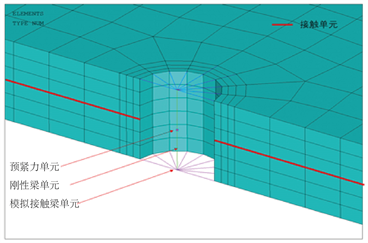
Figure 4. Simplified finite element model of beam element
图4. 梁单元简化有限元模型
3. 前后从板座铆接结构受力情况分析
3.1. 前后从板座拉铆连接结构建模
为了解C70E车体牵引梁前后从板座拉铆连接结构可靠性和安全性,并且找出局部铆钉群中受力最大的铆钉,现取上心盘至端梁处的一段牵引梁及其拉铆连接结构(前后从板座)作为分析对象,模型前处理在Altair HyperWorks 2019平台进行,计算和后处理均基于有限元分析软件ANSYS进行。牵引梁与前后从板座均采用8节点实体单元Solid185进行离散,铆钉采用上述简化建模方法建立,结构有限元模型如图5所示。

Figure 5. Finite element model of rivet joint structure
图5. 拉铆连接结构有限元模型
前后从板座拉铆连接结构主要由三种材料组成,牵引梁制造材料为Q450NQR1,前后从板座制造材料为C级钢,T22拉铆钉制造材料为45 Mn2。结构各部分制造材料及其力学性能如下表1所示。
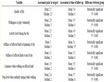
Table 1. Structural manufacturing materials and mechanical properties
表1. 结构制造材料及其力学性能
寻找铆钉群中最大受力铆钉的主要思路为:使用梁单元模拟铆钉的模型,在前后从板座的工作面上以均布载荷的形式施加拉伸或者压缩纵向载荷,并且通过ANSYS后处理提取铆钉各个工况下的受力情况,节点的支反力由Fx、Fy和Fz三部分组成,其中由x方向和z方向的力共同反应了铆钉所受到的剪切力,而y方向的支反力在一定程度上反应了铆钉的预紧力。并且通过铆钉杆的节点编号对铆钉位置进行定位,前后从板座的铆钉编号图如图6所示。
3.2. 载荷工况
根据TB/T 3550.2-2019《机车铁道车辆强度设计及实验鉴定规范车体第2部分:货车车体》6.2.4条规定,取第一工况纵向拉伸载荷为1780 kN、纵向压缩载荷为1920 kN;第二工况纵向压缩载荷为2500 kN。根据铆钉生产商所提供的数据,用于前后从板座与牵引梁腹板之间连接的T22铆钉安装预紧力为175 kN。前后从板座结构强度分析计算工况表如表2所示。
3.3. 前后从板座拉铆钉受力情况
根据计算结果得知,在P1工况下,前从板座受到1780kN纵向拉伸力的作用,前从板3号铆钉受到最大横向力,大小为25565.92 N,同理在P2和P3工况下,后从板座分别受到1950 kN和2500 kN纵向压缩力的作用,同样为3号铆钉受到最大横向力34503.97 N。P1及P3工况下受力最大的六颗铆钉受力情况如下表3和表4所示。
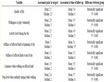
Table 3. Force of rivets under P1 working condition
表3. P1工况下铆钉受力情况
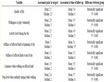
Table 4. Force of rivets under P3 working condition
表4. P3工况下铆钉受力情况
4. 拉铆连接可靠性校核
4.1. 剪切连接铆钉失效模式
前后从板座与牵引梁腹板之间的铆钉连接可以将其认为是剪切连接铆钉,根据德国VDI2230《高强度螺栓连接的系统计算单个圆柱螺栓连接》规定,剪切连接的承载能力在静载荷下受到三种可能的失效模式的限制 [4] [5] :
失效模式1:当剪切连接受到较大的剪切力时,钉杆被剪断导致连接失效,即此时已超出了拉铆钉的剪切承载能力。
失效模式2:当被连接件的厚度较小,且剪切连接受到较大的剪切力时,连接孔壁压力过大,导致孔变形而发生失效。
失效模式3:由于连接孔的存在,被连接件的应力截面被削弱。当剪切连接的孔距和边距太小时,其应力截面处会产生较大的应力,导致被连接件损坏而发生失效。
4.2. 基于DVS-EFB 3435-2剪切铆钉校核
根据DVS-EFB 3435-2的计算步骤对后从板座最大受力铆钉进行可靠性评估,防滑安全系数(
)、超过屈服点的安全系数(
)、表面压力安全系数(
)和疲劳断裂安全系数(
)应遵照DVS-EFB 3435-2指定执行。由上表得知后从板座3号位置铆钉受到最大横向力,故对该铆钉进行校核。
确定传递所需要的最小夹紧力
和直径确认。对于T22型号10.9级拉铆钉已知参数如表5所示。
根据DVS-EFB 3435-2的计算步骤对后从板座最大受力铆钉进行可靠性评估,防滑安全系数(
)、超过屈服点的安全系数(
)、表面压力安全系数(
)和疲劳断裂安全系数(
)应遵照DVS-EFB 3435-2指定执行。由上表得知后从板座3号位置铆钉受到最大横向力,故对该铆钉进行校核。
最小夹紧力 :
最小可预紧横截面面积 :
已知T22拉铆钉应力截面积为309.46 mm2,校核满足要求。
确认拉铆钉及夹紧件回弹量(
、
)并确定载荷系数
。计算所需要参数如下表6所示。
由以上计算参数可得铆钉头回弹量
值为7.02 × 10−8 mm/N,铆钉杆回弹量
值为3.58 × 10−7 mm/N,自由加载槽回弹
值为0 mm/N,成型槽回弹量
值为1.73 × 10−7 mm/N,套环回弹量
值为1.12 × 10−7 mm/N。
拉铆钉总回弹
:
由上述计算参数可得替代变形锥锥角正切值
为0.41,变形锥极限直径
:
由上述结果可知
,夹紧件的回弹量
:
载荷系数
:
对剪切连接三种失效形式校核所需参数如下表7所示。
根据接合面平均粗糙度可得压陷量指导值
为11.5 μm,由嵌入导致的预紧力损失
:
允许的装配预紧力
:
最小剩余夹紧力
:
计算结果表明优化模型最小残余预紧力
大于需要的夹紧力
,故失效模式1校核满足要求。
允许剪切载荷
:
剪切安全系数
等于4.93大于标准规定1.25,故失效模式2校核满足要求。
允许承载压力
:
剪切安全系数 等于6.21大于标准规定1.0,故失效模式3校核满足要求。
5. 结论
本文以C70E型通用敞车车体作为研究对象,对其典型拉铆连接结构进行有限元建模,在有限元法的基础上找出铆钉群中受力最大的铆钉,并通过DVS-EFB 3435-2对其进行可靠性评估,计算结果表明前后从板座受力最大铆钉满足标准要求,且安全系数较大,拥有优化空间。