1. 引言
在长期使用过程中,由于受到外力冲击或者处于恶劣环境的影响,结构表面会出现损伤。损伤的发生直接导致结构局部刚度下降,并且相当大的一部分损伤肉眼难以观察,也不易被仪器检测出来。如果不检测到损伤区域,随着时间的推移,该结构将出现损坏和失效,并对人们的财产和生命构成威胁。因此,结构安全检测越来越受到重视。
基于结构动力响应的损伤检测方法一直是国内外损伤识别研究方向的热点,利用模态数据进行损伤检测是使用最广泛的方法之一。由于与其他定位技术相比,模态曲率对于狭窄的损伤,例如缺口更加敏感 [1] [2] ,很多研究者对曲率模态及其衍生参数的损伤识别展开了研究。Garrido等人 [3] 开发了一种量化模态曲率简单支撑梁损伤的方法
王龙等人 [4] 基于曲率模态损伤前后变化率对梁结构进行损伤定位,并与模态应变能法的损伤检测效果进行了对比,结果表明,曲率模态变化率损伤检测方法更加准确快捷。
袁雪松等人 [5] 利用损伤状态的一阶曲率模态差对简支梁进行损伤识别,并提出一种采用函数拟合构建未损伤状态曲率模态曲线的方法。
Gorgin等人 [6] 提出了一种基于板的一阶振型主曲率的损伤识别方法,结果表明,由结构第一阶振型定义的表面主曲率对损伤敏感,最大主曲率可用于突出结构上的损伤。
孙淑文 [7] 将曲率模态差和小波变换两种方法结合在一起识别结构的损伤,结果表明会比单一方法具有更好的损伤识别能力。
Cao等人 [8] 中提出了一种基于模态曲率的损伤定位方法。为了克服经典模态曲率程序噪声灵敏度的缺陷,该方法使用Teager能量算子–小波变换模态曲率,表现出更高的抗噪性,可用于扫描激光测振仪获得的模态数据。
在工程应用方面,呙中睴等人 [9] 对桥式起重机主梁进行损伤检测,验证了曲率模态分析技术不仅能准确诊断主梁的损伤位置,还可判断梁的损伤程度。
利用曲率模态进行结构损伤检测的研究主要集中在梁板结构上,对曲面结构的损伤识别研究较少。本文以航空发动机活门为研究对象,利用曲率模态差法对曲面结构进行损伤识别试验研究。
2. 基本理论
曲率模态(Curvature Mode)。作为模态参数,曲率模态是弯曲结构弯曲振动的一种独特的固有变形模态。因为曲率模式是结构中性表面的变形模态,所以它对结构的局部变化相对敏感,并且可以反映其局部特性的变化。因此,该理论被引入到弯曲构件的损伤识别中。当梁弯曲时,中性轴的曲率计算如下:
(1)
其中E是材料的弹性模量,I是截面的惯性矩,M是弯矩。
由公式(1)可以推断,梁上某一点的曲率与相应的结构刚度成反比;也就是说,结构刚度的变化可以通过曲率来反映。
考虑到结构一般在线弹性范围内,从材料力学的角度来看,构件的曲率公式如下:
(2)
其中
是位移。在小变形的情况下,公式(2)可以转换为
(3)
在引入曲率模式的定义后,
是
的二阶导数,
是曲率模态,
是位移模态。
在有限元分析中,通过模态分析获得的振动模态通常是位移矩阵,通过使用中心差分法计算其变化规律可以容易地获得曲率模态。
在实际的结构损伤检测过程中,可以使用加速度传感器以及相应的采集系统来收集结构振型。
结构的整体位移矩阵
,可以根据结构上测量点在特定时刻的位移
计算得出。
曲率模态
可以使用位移矩阵的中心差分法得到,如下所示:
(4)
式中,
是传感器
到i的距离,
是传感器i到
的距离。
通过对曲率模态做差,得到曲率损伤因子DI
(5)
结构损伤曲率模态可以直接反映结构损伤过程中的刚度变化。如果结构的损伤很小,可以使用最大归一化方法对曲率模式进行归一化。由式(1)可知,结构出现损伤后其物理特性将发生改变,该变化可通过模态参数进行反映,因此,通过检测模态特性的变化可对结构进行损伤识别,曲率模态对结构损伤的变化尤为敏感,通过计算结构在第m阶固有频率下损伤后与损伤前的曲率模态差的绝对值,可对结构的损伤位置进行定位:其中
为损伤后的第m阶曲率模态,
未损伤时的第m阶曲率模态。该方法通过对比选定阶数下的模态曲率差值进行损伤检测。
3. 实验设备及流程
将活门试件固定在试验台上,打开激光测振仪和激光探头。首先在试样表面设立基准面并设立激光测点。然后利用激光测振仪自带的信号发生器生成一虚拟信号,经功率放大器驱动激振器。最后,利用激光探头自动扫描试样进行振动测量。激光探头依次扫描测点,PSV-500激光多普勒测振仪根据每个测点的位移形成活门的位移模态,选择目标阶的共振峰附近的频率段,激光测振仪即可分析出对应阶的模态振型。实验示意图如图1所示。
4. 损伤位置识别
利用结构曲率模态对结构损伤敏感的特点,选取活门作为研究对象,对基于曲率模态测试的裂纹位置的识别方法进行研究。裂纹属于结构损伤的一种。在实验研究的初期,为避免对试样造成损伤而导致后期无法获得试样完好时的模态振型,故在对该损伤检测方法进行可行性分析时,利用附加质量块的方法来模拟结构损伤。再利用激光测振仪测量试样损伤前后的模态振型,通过对比分析为接下来的研究提供基础。
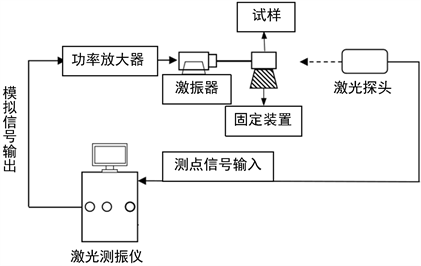
Figure 1. Schematic diagram of the mode of curvature measurement by laser vibrometer
图1. 激光测振仪测量曲率模态示意图
4.1. 活门无损伤时模态测量
为了测量活门在无损伤时的模态振型。将活门与作动器按用卡箍进行连接。利用激光测振仪测量结构的位移来获得结构与低阶时的模态振型。
试验时利用激光测振仪产生一虚拟扫频信号经功率放大器驱动作动器。在活门待测区域的表面均匀布置一组5 × 17的矩阵测点。利用激光测振仪对每个测点进行遍历测量,获取结构无损伤时的模态振型。模态测量装置图如图2所示。
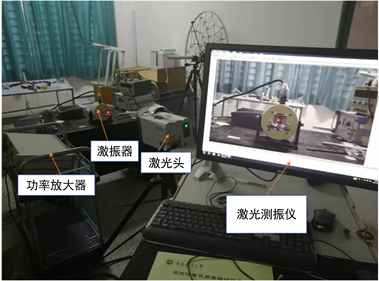
Figure 2. Diagram of a modal measuring device
图2. 模态测量装置图
4.2. 活门有损伤时模态测量
在进行活门有损伤的研究中,利用附加质量块的方法模拟活门的结构损伤。试验时在活门待测区域的活门内壁粘贴一质量为2 g的磁铁。按无损伤时的布点方式,重复激光测振仪测量活门模态的步骤,获得活门损伤后的模态振型。
4.3. 对比分析
将测得的模态振型导入MATLAB程序中,运用中心差分法,求出损伤前后的曲率模态,进行差值计算,可得到各测点的曲率模态差。图3给出了以曲率模态差为损伤参数的第一阶、第二阶和前两阶的损伤参数直方图。在布点阶段设置了5 × 17的测量点,对应图中的方格,不同的颜色代表在不同行,峰值处代表损伤参数最大值处,则为损伤发生的位置。将各点损伤参数与活门上的点相对应,实验中质量块布置在测点(10, 3)的位置,与实际检测出的位置一致,实验结果表明利用结构损伤前后的曲率模态差可很好的识别损伤位置。
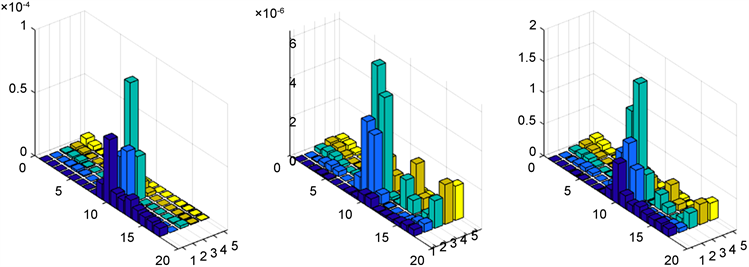
Figure 3. Histogram of damage parameters
图3. 损伤参数直方图
图4给出了损伤结果与活门布点的直观对应关系。横纵坐标代表了测点的位置。光点所在的位置,代表了损伤的位置。

Figure 4. Visual diagram of valve damage location
图4. 活门损伤位置直观图
5. 损伤程度方法研究
在附加质量块实验验证了曲率模态差可以对活门进行损伤位置识别的基础上,对活门进行不同程度的裂纹加工,来观察损伤参数DI的变化。首先采用线切割方式对活门进行裂纹加工,活门裂纹如图5所示。
利用激光测振仪对无裂纹活门进行模态测量,获取无裂纹活门的模态振型。在活门上布置5 × 9矩阵测点,如图6所示。再重复相同的步骤并采用相同的测点布置方式测量有裂纹活门的模态振型。
将测得的有裂纹活门的模态振型数据和无裂纹的模态振型数据代入MATLAB程序,即可计算出活门损伤前后的曲率模态及裂纹位置。图7给出了活门裂纹位置的指示图。根据计算结果和活门测点网格的对比。该计算结果在竖直方向上位置准确无误,在水平方向上出现了微小的偏差,这可能是由于更换试样过程中的位置偏移引起的。损伤定位精度满足实际生产加工要求。由此可见利用试件的曲率模态可以很好地识别出裂纹的位置。
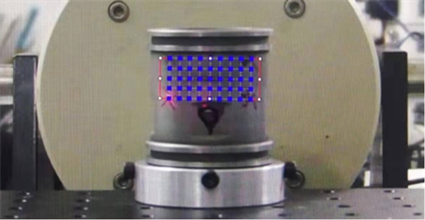
Figure 6. Valve measurement point layout
图6. 活门测点布置图
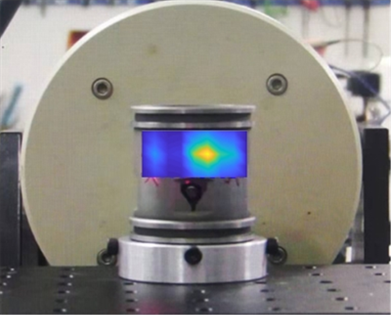
Figure 7. Valve crack location indication
图7. 活门裂纹位置指示图
为了对活门进行不同损伤程度的实验研究,设置两种不同程度的损伤,即在活门表面向下分别切割1 mm、2 mm。分别如图8、图9所示。
将活门损伤后的模态振型导入MATLAB,同时调入数据库中无裂纹活门的标准模态振型。利用中心差分法所示的MATLAB程序计算各测点的损伤参数。图10、图11分别为活门在两种种裂纹损伤下的损伤参数直方图。在布点阶段设置了5 × 9的测量点,对应图中的方格,不同的颜色代表在不同行,峰值处代表损伤参数最大值处,则为损伤发生的位置。
将峰值处的损伤参数因子提取出来,图12给出了损伤活门峰值处的损伤参数直方图,1号是活门无损伤的实验,损伤参数因子为0;2号是裂纹为1 mm时的最大损伤因子0.017;3号为裂纹为2 mm时的最大损伤参数因子0.028。随着活门裂纹深度的增加,损伤点的峰值呈上升趋势。即裂纹损伤程度越大,则利用本文提出的裂纹检测方法计算的损伤参数越大。可将曲率模态差(DI)作为损伤参数衡量损伤程度。
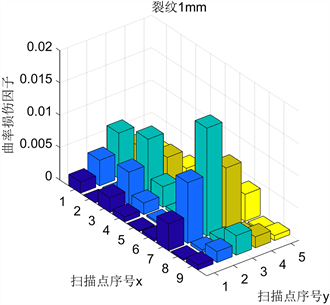
Figure 10. Crack depth 1 mm damage parameter histogram
图10. 活门切割深度1 mm的损伤参数直方图
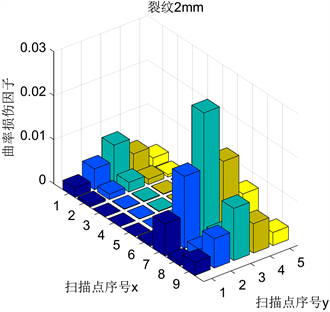
Figure 11. Crack depth 2 mm damage parameter histogram
图11. 活门切割深度2 mm的损伤参数直方图
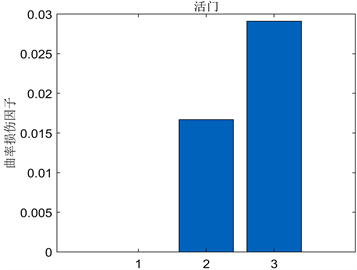
Figure 12. Histogram of damage parameters at the peak of the injury valve
图12. 损伤活门峰值处的损伤参数直方图
6. 总结
本文进行了基于曲率模态参数的结构损伤识别的研究。具体以某款航空发动机的活门为原型,在活门表面切割不同深度的裂纹来模拟结构损伤,并提取低阶曲率模态参数,通过引入曲率损伤因子DI以确定损伤位置和损伤程度,主要结论如下:
1) 通过对结构损伤前后的曲率模态参数进行对比,发现损伤前后曲率模态变化明显,可以根据损伤前后曲率模态的突变位置来进行损伤识别。
2) 通过对不同损伤程度的载体进行了曲率模态测试,分析了相关测试数据,引入曲率损伤因子DI作为损伤指标,可以很好地衡量结构的损伤程度。
3) 通过对活门的实验研究可以发现,基于结构损伤前后曲率模态变化的损伤检测方法不仅适用于简单的梁结构,也适用于复杂的曲面结构。