1. 引言
随着油气资源的需求量剧增,油气管网的建设力度不断提高 [1] [2] ,长输油气管道通常需要沿复杂地质条件敷设,因此管道易受滑坡、地震等地质灾害的威胁,严重影响管道的安全运行 [3] [4] [5] 。常规依靠人工巡检不仅成本高,而且安全风险大,随着近年来在线监测技术的发展,能够实现对管道的连续分布式监测,并进行管道实时安全性评估,因此得到了现场大规模应用 [6] [7] [8] 。开发现场管道监测系统能够实时掌握管道的受力情况,评估管道的安全状况,对油气管道的安全运营具有重要意义。
开发油气管道的应力监测系统,首先需要基于管道力学基础理论,对管道应力应变性能开展研究 [9] [10] 。Rajani等 [11] 首次针对滑坡作用,开展了管道受力情况的解析计算,确定了不同方向上的管道近似应力,但研究中未考虑管道与岩土间的相互作用对力学响应的影响。O’Rourke等 [12] 采用R-O模型分析了滑坡区管道的力学性能,但研究模型忽略了管道和土体之间的相对滑动对管道的自由变形能力的影响,导致模型对管道的应力分布和变形的预测精度较低。邓道明等 [13] 考虑了管道的非线性,考虑跨越管道的内力和形变,计算了管道的挠度,将悬空管道简化为大挠度的梁,而埋地管道看成半无限长的梁,考虑管道内压和温度变化时对管道应力的作用,研究管道的内力和变形情况。另外,在管道应力监测方面,包括电阻式应变计、振弦式应变计以及光纤光栅等多种监测方式 [14] [15] [16] 。Chou [17] 采用分布式应变传感系统研究了埋地管道屈曲变形监测,结合有限元模型验证了分布式传感系统对埋地管道进行分布式应变监测是可行的。王磊等 [18] 对忠县–武汉输气管线,建立了管道滑坡力学计算模型,通过求解确定了管道中部及两端为危险部位,另外研究了跨距、温差、运行压力、管道壁厚等因素对管道力学性能的影响。薛建等 [19] 自行研制了光纤光栅传感器对管道进行应力监测,同时还实现了温度补偿,使得管道应力监测结果更加准确。张银辉等 [20] 设计了一种基于云服务平台的远程实时监测系统对管道安全状态进行远程实时评估。
在管道应力监测的研究上,本文开展了油气管道应力监测系统的研究,首先设计室内实验对应变片贴片方案进行了优化,并通过了温度补偿方案的可靠性检验,基于此,利用设计的应力监测系统测试了不同运行压力条件下不同应变片应力数据,并对数据进行处理,将周向、斜向以及轴向三个方向的测试应变与理论计算结果进行对比,基于测试结果的可靠性,最后完成了管道应力应变监测系统设计与现场试验,并取得了良好的应用效果。
2. 天然气管道应力监测系统
目前,管道应力监测的主流技术有振弦式传感器、光纤传感技术、电阻应变片技术。其中,光纤传感技术不受电磁干扰、测试精度高,但传感器脆弱、使用寿命短,不能适应现场应用;振弦式传感器采用频率信号传输方式,抗干扰性能好,但结构复杂、体积大,不适用于管道监测;电阻应变片体积小、灵敏度高、温度补偿性能稳定且能适应现场恶劣环境。因此,优选了电阻应变片对管道应力进行监测,设计搭建了室内物理实验装置,针对管道应力应变片开展内压对管道应力影响的室内测试实验并进行贴片方案优化,构建了天然气管道应力监测系统。
2.1. 管道应力监测系统设计
2.1.1. 系统框架设计
自主研发应力监测系统的基本组成框图,如图1所示。系统主要分为应变采集仪无线数据收发器和远程监控计算机组成。现场选择监测点并在管道上安装应变传感器,每个监测点2个应变传感器监测12个应变值,数据自动传输无线数据收发器,并有GPRS系统自动上传基地监测中心,实现管道应力应变的实时监测预警。
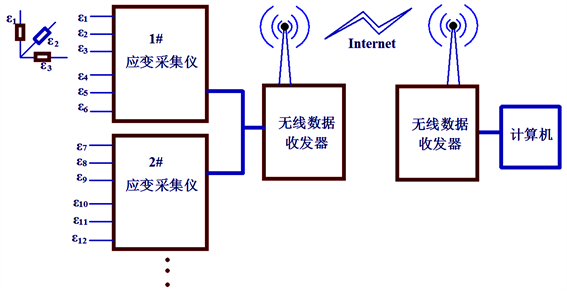
Figure 1. The basic composition block diagram of the stress monitoring system
图1. 应力监测系统的基本组成框图
2.1.2. 应变片选择
采用三轴直角应变花监测管道应变量,应变花由三个应变片组成,应变花方向如图2所示。可以直接得到管道的主应力方向,三轴直角应变花监测三个方向的应变,并结合管道的物理特征参数,利用公式计算出主应力的大小与方向。设计应变花由三个阻值为120欧的康铜丝应变片组成,灵敏系数为2.06,测试应变范围为20000 με。
2.2. 应力监测室内实验
2.2.1. 实验设备的设计
室内实验设计了长2米、直径为0.4米的圆形管道,管道两端封闭且设置有压力、温度监测装置,设备如图3所示。由于管道直径、壁厚大,且在密封条件下进行内压、外力作用实验,因此还需要进行应变片贴片方案优化,并检验不同运行压力下管道应力监测系统的可靠性。
2.2.2. 应变片贴片方案优化
由于不同贴片位置会对实际应力监测数据造成很大影响,且当监测的数据与实际轴向、径向存在偏差时,监测的数据还需要通过复杂的转换以获取管道本体所受轴向与径向应力。经过大量实验研究,结果表明在三通附近的两个应变花和其余的特性一致,环向均匀贴片与径向贴片方式较为合理,因此,以4个应变花的贴片方案为最优,4个应变片为圆周均匀布局,如图4所示。管道中间位置圆周表面对称粘贴4个应变花及对应的补偿块,且在有三通的附近粘贴2个应变花及其补偿块。
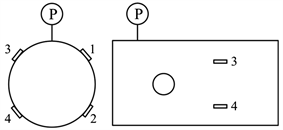
Figure 4. Distribution of strain monitoring sensors on the cross section
图4. 应变监测传感器在截面上的分布
2.3. 温度补偿方案与系统可靠性检验
2.3.1. 温度补偿测试实验
由于应变计与管道材料膨胀系数的差异,外界温度变化会导致应变计产生附加拉伸或压缩,在监测管道应力、应变时,系统要求灵敏度高,放大倍数达到1000倍以上;另外,采集器内部电路的温度变化引起测量结果的波动,导致监测结果的偏差。因此,采用高精度低漂移的两级放大电路来测量应变,还需要对采集器进行温度补偿。
通过设计应变采集器的温度补偿实验,装置流程图如图5所示,将温度探头设置在测量电路,应变仪装在一个导热良好的空盒子内,设置一个可控温的空腔,将空腔温度加热到30℃,然后断电,让空腔自然降温,记录温度和各通道应变输出值,采用线性回归得出偏移修正系数。
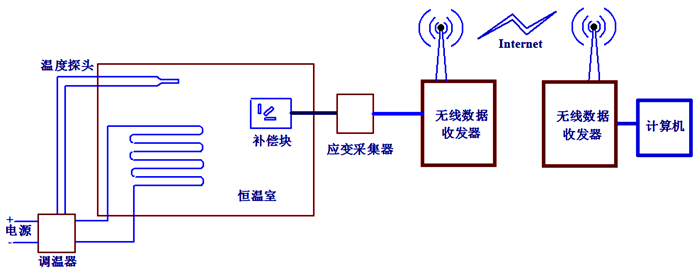
Figure 5. Temperature compensation experimental device
图5. 温度补偿实验装置
温度补偿应变修正结果如表1所示,结果表明:受温度影响的应变漂移较大,温度改变1℃,会造成2 με的误差,误差较大,因此,设置温度补偿装置对提高测试结果的精度极为重要。
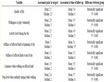
Table 1. Temperature drift correction experimental data of strain collectors
表1. 应变采集器的温度漂移修正实验数据
2.3.2. 温度补偿有效性验证实验
温度补偿验证实验需要将应变花粘贴在应变补偿块上,补偿块尺寸为30 mm × 30 mm,材质与管道材质一致,每个测量片和补偿片位于测量电桥的相邻桥臂进行补偿,为检验补偿效果,开展了实验测试。
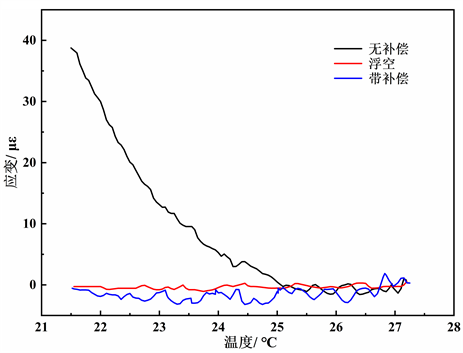
Figure 6. Temperature compensation validity verification experimental results
图6. 温度补偿有效性验证实验结果
不同温度下温度补偿有效性实验结果如图6所示,结果表明:随着温度的升高,无温度补偿的管道应变降低幅度大,而带补偿后应变波动较小,当温度升高5℃时,不带温度补偿的应变降低接近40 µε,而带温度补偿后变化量仅2 µε,证明温度补偿效果显著。
2.4. 管道应变数据监测可靠性检验
2.4.1. 应变片应力监测测试
测试应变片数据监测稳定性,设计室内实验,测试管道运行压力0~1 MPa内,共11个应变片监测应变变化结果如图7所示。结果表明:不同位置应变片均能有效采集管道应力受力时的应变数据,数据传输稳定性高,且能够有效反馈管道内压数值,表明应变片贴片方案合理,管道应变数据监测可靠。
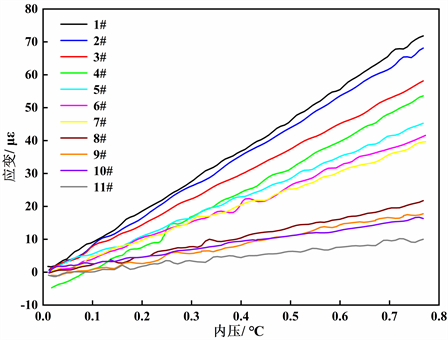
Figure 7. Internal pressure diagram of rosette strain output tube
图7. 应变花应变输出管内压关系图
2.4.2. 管道应力监测数据处理
根据薄壁壳体的无力矩理论 [21] 可以求得受内压的薄壁容器简体部分的应力值:
管道轴向应力:
(1)
管道周向应力:
(2)
式中,P为容器所受内压力,MPa;D为容器内直径,mm;t为容器壁厚,mm;
为轴向应力,MPa;
为周向应力,MPa。
薄壁容器受内压后,当其变形在弹性范围以内,容器壁各点的应力应变符合虎克定律 [22] ,即:
(3)
(4)
即可根据虎克定律求得
和
。
切应力:
(5)
式中,R0为薄壁圆筒的内、外半径之和的一半,mm;E为钢材的弹性模量,取2.10 × 105 MPa;
为泊松比,取0.3;
为轴向应变,µε;
为周向应变,µε;
为切应力,MPa;
为圆周率。
剪切模量:
(6)
切应变:
(7)
则45˚方向的应变
为:
(8)
2.4.3. 管道应力监测系统可靠性检验
首先对比了4个通道的应力监测结果与理论计算结果,分别对比轴向、斜向以及周向的应力误差,明确应力监测系统的可靠性。测试管道运行压力1 MPa,不同通道的应力结果如表2所示。从表2可以看出:改变管道泊松比为0.3、0.27,对比理论计算结果表明,不同通道的周向应力与斜向应力误差较小,轴向应力误差较大,而轴向应力主要由于两端受平板封头约束导致的,另外,2#通道的实测结果与理论值最接近。
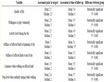
Table 2. Comparison of measured and calculated stresses at different monitoring points
表2. 不同监测点实测与计算应力的对比
以2#通道为例,测试不同压力条件下,周向、斜向以及轴向的应变,并与泊松比0.3的理论计算结果对比,结果如图8所示。
(a) 周向应变
(b) 斜向应变
(c) 轴向应变
Figure 8. Comparison of strain monitoring strain and theoretical calculation results for channel 2#
图8. 2#通道应变监测与理论计算结果对比
图8对比结果表明,2#通道周向、斜向应变理论值与实验值趋势、数值基本一致,说明贴片方案合理,通过应变片能够实现管道本体应力的有效监测。另外,图8(c)中轴向应变测试结果与理论计算结果存在一定偏差,但精度仍然符合工程精度要求,主要由于室内实验需要对试验管段进行密封处理,进而将管道两端进行了有效封堵及两端严格固定,由于管道两端受到约束,造成管道轴向应力监测值与两端无固定情况下理论计算值有一定偏差,但仍然满足实际管道应力监测要求。
3. 管道应力应变监测系统的现场应用
管道应力应变检测系统的现场应用选择昆明一处天然气埋地管道,为了实现现场实时监测预警,设计开发了在线监测预警平台,实现数据自动化采集并传输至云平台,通过平台实现数据浏览、风险预警以及视频远程监控功能。
3.1. 系统功能的实现
按照现场需求,设计开发了应力应变监测软件一套,软件界面如图9所示。应变采集器和数据收发器之间的有线方式的通信协议及程序实现;无线通信网络的设置、接口定义及数据服务器端的软件实现;远程端数据收发器和监控计算机之间的数据通信协议及程序实现;远程监测现场管道6个应变花共18个应变值,采集速率为0.1次/秒~10次/秒,应变采集器和数据收发器之间的有线方式以通信协议及程序实现,另外,采集2个天然气管道外壁温度,并传输至主控模块;管道内部流体压力,应变片供电、无线传输供电通过配套供电硬件实现。现场数据采集的传输由无线通信网络实时同步至服务器端的软件。
软件界面可展示6个应变花的应变值实时曲线,并可选择查看某一应变花进行主应变大小和方向的计算,如图10所示。所有数据可在线读取,形成应变和温度的数据报表,并实现数据的导出、保存。
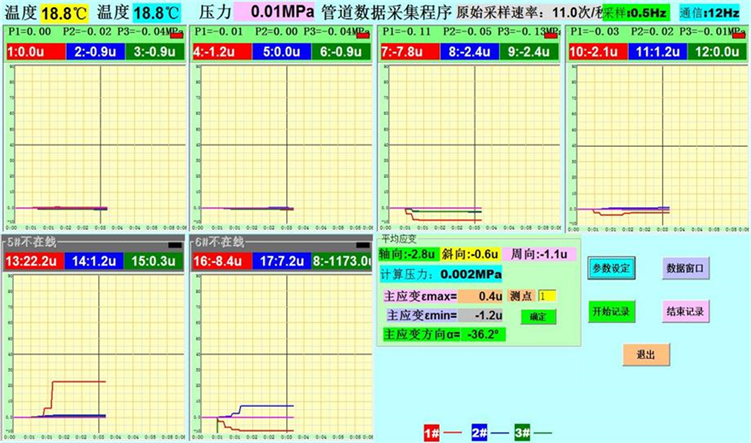
Figure 9. Main interface of pipeline data acquisition software operation
图9. 管道数据采集软件运行主界面图
3.2. 管道应变预警
根据GB/T 50470-2017《油气输送管道线路工程抗震技术规范》,计算监测管道轴向容许应变,确定管道应变预警阀值。监测管道为X80钢材,设计容许压缩应变为:
(9)
式中:
为管道容许压缩应变;t为管道壁厚,mm;D为管道外径,mm。
现场敷设管道外径406.4 mm,壁厚6.3 mm,通过计算管道容许压缩应变为0.496%,即4960。
将现场应变监测预警分为三级,分别设计应变阈值。一级预警阈值为40%容许应变,1984;二级预警阈值为60%容许应变,2976;三级预警阈值为80%容许应变,3968。
3.3. 现场监测数据分析
现场试验选取昆明一处天然气管道,在管道上设置2个监测点,采集了6月、7月两个月的管道轴向应变与温度,监测数据结果如图11所示。
结果表明:
1) 1号、2号监测点在6月份温度均呈现小幅度上升趋势,而7月份温度波动较大,2个月内1号监测点温度均高于2号监测点;
2) 1号监测点在6月份均表现为压缩应变,7月份月末由压缩应变转变为拉伸应变;2号监测点在6月份月末由压缩应变转变为拉伸应变,7月份均表现为拉伸应变。
3) 监测2个月内监测点轴向应变变化较小,应变值未达到预警值,管道安全性较高。
现场应用表明,自主研发的管道应力监测系统实验结果与理论计算结果吻合,贴片方案、应力监测数据可靠。通过对埋地管道处的地质移动情况进行监测,可以起到有效预防及应急维稳措施预警,也能为油气企业及时接收预警信息采取响应措施提供参考。
(a) 六月份
(b) 七月份
Figure 11. Monitoring point strain and temperature data
图11. 监测点应变、温度数据
4. 结论与建议
结论:
1) 采用电阻应变片周向贴片方案进行管道应力采集,并设计温度补偿系统进行修正,待温度补偿后管道应变波动明显减小,证明温度补偿效果显著。
2) 结合理论计算将监测应力数据转化为不同方向的应变,通过对比表明周向、斜向的应变转化精度较高,轴向应变存在较小误差,但符合管道应力监测的工程应用。
3) 将系统投入现场应用,现场采集了2个监测点2个月内的应变、温度数据,实践结果表明,系统能够稳定应用于现场管道监测,实现管道远程安全预警。
建议:
管道应力监测通过现场的有效实践,建议可将该系统在重点地质灾害区域进行全面推广,实现管道全线路油气管道地质灾害预警,保障管道安全运行。
支持项目
校企合作项目《燃气支线管道重点监测段的管道应力分析和监测研究》(KKX0201905023)。