1. 介绍
铑作为一种非常珍贵的稀有贵金属,世界上73%的原生铂族金属的生产与南非的布什维尔德复合体有关,而其余的铂族金属储量主要集中在俄罗斯、津巴布韦、美国和加拿大 [1] ,国内产量匮乏。铑作为催化剂使用后残留在有机废液中,国内缺乏有效的回收手段。相比于国外,我国针对铑催化剂回收的研究较少,铑金属回收困难,从而造成资源的浪费,在国内多采用焚烧法,其生产工艺复杂,易出现环境污染、回收效率过低等问题,极大增加了铑催化剂二次使用的难度 [2] 。目前,铑催化剂的回收方法主要包括以萃取、沉淀分离、吸附分离和离子交换为主的湿法冶金工艺和以焚烧和熔融富集为主的火法冶金工艺 [3] 。随着人们对贵金属研究的深入,逐渐涌现一些优秀的新方法,比如随着生物技术的迅速发展和人类环保意识的增强,生物吸附技术成为金属回收的新兴领域。生物吸附是金属离子与生物质的吸附、离子交换、微沉淀和配位的技术 [4] 。
1.1. 铑的性质
铑(Rh)是一种过渡金属元素,颜色为银白色,有的略带黄色或灰色,其密度为12.41克/立方厘米 [5] ,在所有元素中仅次于铂。铑的熔点为1964℃,沸点为3695℃,硬度为6.0至6.5,仅次于钨、铼和钻石。铑是一种顺磁性金属,是一种良好的导电体和热导体,具有优秀的电导率和热导率。此外,在化学性质方面,铑是一种高度反应性的金属元素,它可以与许多元素和化合物发生反应,并在很多化学反应中发挥着重要的催化作用。
1.2. 铑的应用
铑是一种极为珍稀的金属元素,被广泛应用于多个领域。这一元素的稳定性、化学反应性和坚硬性使得它在催化剂、铂族金属合金、电子器件、医疗器械和纳米材料等领域中扮演着重要的角色 [6] 。
在催化领域中,铑的应用尤为突出。由于其极高的活性和选择性,铑被广泛应用于许多关键反应的催化剂中,例如氢化反应、羰基化反应、不对称合成等。此外,铑还可用于水相催化、气相催化和溶液催化等多种催化反应条件下,具有极高的催化效率和活性。
除了在催化领域中的应用,铑还可用于制备高强度、高温度合金,这种合金通常用于航空航天和高温设备中 [7] 。铑也常被用于制备电阻器和电容器等电子器件,以及制备医疗设备,如心脏起搏器和人工关节等。
此外,铑还具有优异的稳定性和抗氧化性,使得它成为纳米材料制备中的重要原料 [8] 。铑纳米颗粒具有优异的催化性能和电化学性能,在生物医药、环境保护、能源储存等领域中有着广泛的应用前景 [9] 。
总之,铑的重要性不仅在于其极为珍贵和稀有的特性,更在于其在多个领域中所发挥的独特作用,这使得它成为了现代工业和科学技术中不可或缺的重要元素之一。
1.3. 铑催化剂的应用
铑是一种非常重要的催化剂,它在多个领域都有广泛的应用。其中最常见的应用是在汽车尾气净化中。由于车辆尾气中含有有害的氮氧化物和碳氢化合物等物质,这些物质对环境和人类健康都有着不可忽视的危害。使用铑催化剂可以有效地将这些有害物质转化为无害物质,从而大大降低尾气对环境的污染。
此外,铑催化剂在石化、化学合成、制药和生物化学等领域中也有广泛的应用 [10] 。例如,在石化工业中,铑催化剂可以用于合成高分子聚合物、制备合成橡胶和合成塑料等。在化学合成领域,铑催化剂可以用于合成复杂的有机分子,加速化学反应的速率和选择性。在制药和生物化学领域,铑催化剂也被广泛应用于生产化合物、制备医药品和研究生物分子反应等方面。
铑催化剂的优势不仅在于其能够提高反应速率和选择性 [11] ,还在于它能够降低能量消耗和环境污染。相较于传统的化学合成方法,铑催化剂的使用可以使得反应条件更加温和,减少废弃物的产生,从而减少对环境的污染。因此,铑催化剂的应用不仅促进了生产和科研的发展,也有助于保护环境和人类健康。
除了上述领域,铑催化剂在其他领域中也有一定的应用性。例如,在电子工业中,铑催化剂可以用于制备电子元件和电路板等。在冶金工业中,铑催化剂可以用于提取贵金属和分离金属元素等。可以看出,铑催化剂在多个领域中都有着广泛的应用,其重要性和作用不容忽视。
2. 铑的回收工艺
20世纪70年代,人们开始重视铑作为催化剂的运用,学术界和工业界开始了从废催化剂中回收铑的研究。从废催化剂中回收铑金属通常由三个主要过程组成:预处理、浓缩富集、精炼 [12] 。预处理是指对废催化剂进行必要的溶解并使铑离子游离出来;浓缩富集是分离废催化剂中载体和铑离子的重要步骤;精炼是对浸出液中的铑进行浓缩提纯。浓缩富集是整个回收工艺中最重要的环节,直接影响回收率和成本。根据铑回收方法的差异,铑的回收工艺可以分为火法冶金、湿法富集和生物富集。
2.1. 火法冶金工艺
火法冶金工艺指铑废料通过将助熔剂在高温下分离熔融状态的金属和非金属物质 [13] ,再使用金属收集剂形成含铑的合金,铑金属通过适当的再精炼技术从合金中回收,然后研磨,筛分和分离材料,最后进一步精炼和纯化金属。火法回收废料中铑的方法主要有焚烧法、等离子体熔融法、金属捕集法、热氯化法和高温挥发法等。图1为火法冶金工艺流程图。因为其工艺简单,不需要化学添加剂和高回收率,火法冶金成为工业废料中回收有价值元素的最普遍方案,火法冶金工艺从废料中提取贵金属在工业上被广泛应用。在火法回收贵金属中,催化剂中的非贵金属在高温下加热,在熔融状态下与附加造渣材料形成熔渣,利用密度差的原理,在熔体的上部漂浮除去熔渣,而贵金属被其它贱金属捕获以形成合金,该合金下沉到溶液的底部,经冷却后的进一步处理。
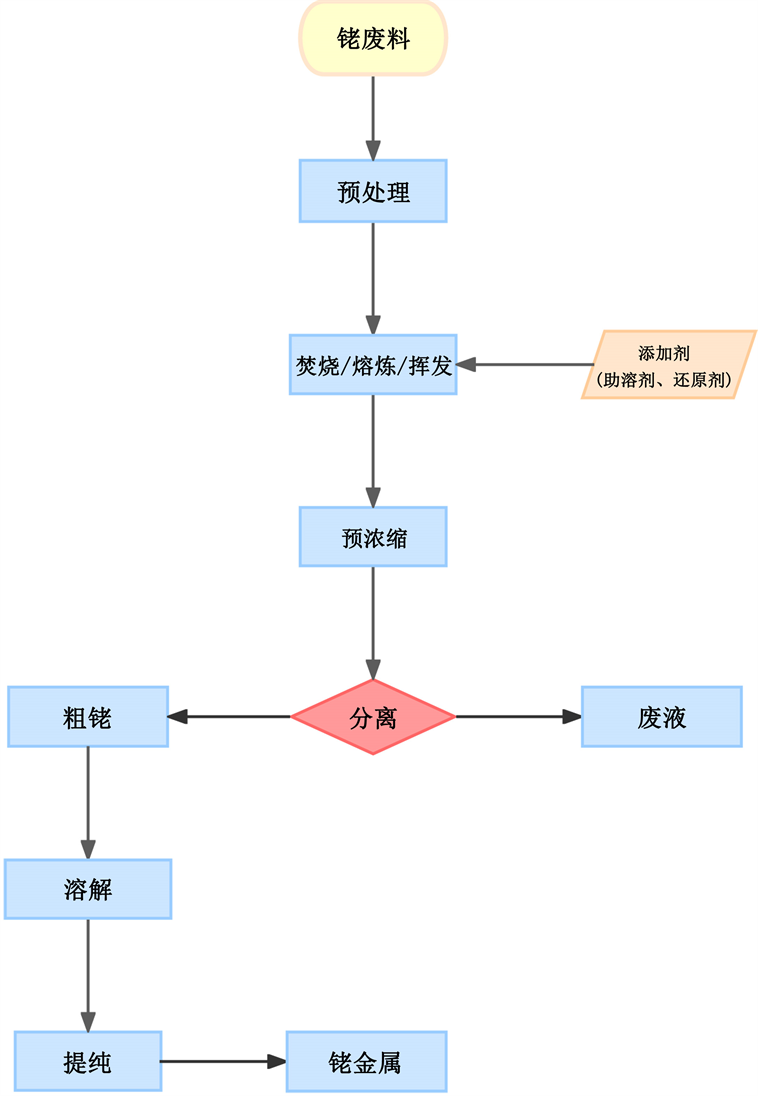
Figure 1. Flow chart of rhodium recovery by pyrometallurgical process
图1. 火法冶金工艺回收铑的流程图
2.1.1. 焚烧法
焚烧法主要采用焚烧的方式,将含有可燃材料的铑废料进行燃烧来破坏铑金属与载体之间的连接,然后进一步的收集铑金属。焚烧法的具体原理是将铑废料的载体进行脱碳操作,然后加入适当的助燃剂等,在富氧环境下焚烧,充分燃烧后得到铑灰 [12] 。然后对铑灰进行再次溶解,溶解之后对溶液中的铑进行还原操作,得到粗铑,最后对粗铑进行纯化提炼,回收得到最终产物。
焚烧法采用高温焚烧,易产生二噁英、氧化磷等有毒物质,同时对焚烧炉等设备要求较高,而低温焚烧能够有效避免这个问题,并且使尾气排放符合国家的质量控制标准。因此,王建忠等人提出,使用减压蒸馏的方法对物料进行浓缩,再加入氢氧化钠,可以加快有机物的降解,并降低灰化温度,以此来达到减少烟尘的作用,避免了烟尘携带,从而增加铑的回收率。并且产生的尾液中,铑含量较低,通过金属置换可以有效回收,灰化铑收率达到99%以上 [14] 。具体实施工艺为:首先通过减压蒸馏设备,控制温度在50~100℃之间递增,蒸馏后物料呈现凝胶状。接着在物料中加入氢氧化钠来降解有机物,取10份减压蒸馏的尾渣加入1份氢氧化钠,慢慢升温,温度到达150~200℃之间时物料发生皂化反应,熔融成液状,并有轻沸鼓泡现象,保持200℃的温度2 h,其后在2 h内将温度升至500℃,焚烧物料4 h。然后将低温焚烧好的物料,加入同比例的热水中,洗涤两次,过滤。水洗后的滤渣烘干后,放入马弗炉中600℃保温4~5 h [14] ,进行深度脱碳。最后进行酸洗,除去大部分锌、铁等贱金属。
焚烧法普遍采用800℃以上的高温焚烧 [14] 。因为其工艺简单、不需要化学添加剂等优点,在工业上被广泛应用,但由于铑废料中含有大量有机物,焚烧过程中极易产生爆燃现象,不稳定性极强,难以操控,操作不当会对人身安全产生威胁,焚烧也会产生大量的烟尘,部分铑会被烟尘携带,从而造成流失,影响铑金属的回收率。
2.1.2. 熔炼法
熔炼法的原理是提供足够高的温度来熔化金属,加入焦炭,熔剂和熔炼捕集剂,使得废催化剂中的铑与捕集金属结合形成合金并沉到底部,而载体部分通过与所施加的造渣材料一起形成渣而进入渣相,以实现铑与催化剂载体的相互分离 [15] 。本工艺流程较短,贵金属生产效率高,无废水废气产生,铑富集度高。该过程是材料熔化,合金下沉,而炉渣漂浮,使炉渣和金属彼此分离,如图2为熔炼法流程图。由于废催化剂中的铑含量通常较低,因此需要将炉渣和合金良好分离以确保高回收率。在该方法中,渣和金属之间的比重差异大,并且渣和合金的分离是优异的。
李勇等人 [16] 使用熔炼法从失效汽车尾气催化剂中富集回收铂钯铑,通过对捕集剂的选择、磁性铁用量对贵金属回收率的影响、焦炭用量对贵金属回收率的影响、熔剂CaO用量对贵金属回收率的影响、熔炼时间对贵金属回收率的影响、熔炼温度对贵金属回收率的影响,得到最佳熔炼工艺为:反应时间4 h,捕集剂选择为Fe3O4,磁性铁用量为废料的20%,还原剂焦炭占比9%,熔剂CaO占比40%,熔炼温度1450℃,在此条件下,金属铂钯铑的综合回收率可达到97%以上。
熔炼法工艺流程短;效率高,无废水、废气产生,富集效果优异。但是,该方法不太适合含SiO2的材料以及高温条件下器械的使用寿命短等问题依旧有待改善。
2.1.3. 金属捕集法
金属捕集法与熔炼法相似,如图3所示,利用熔融金属如Fe、Cu、Pb、Bi作为捕集剂,添加一定的还原剂、造渣剂等,通过高温还原熔炼,使铂族金属与捕集剂形成合金 [17] ,实现铂族金属的回收。该方法的主要考虑因素是熔体的类型和捕集剂的选择。其中捕集剂主要考虑其与铂的互溶性、熔点、夹带熔渣的金属的损失和捕集剂的化学性质。从而能够有效解决铑废料的载体难以溶解,或者含有低品位铂族金属等问题。因此金属捕集法特别适用于处理难溶性载体和铂族金属含量极低的废催化剂。
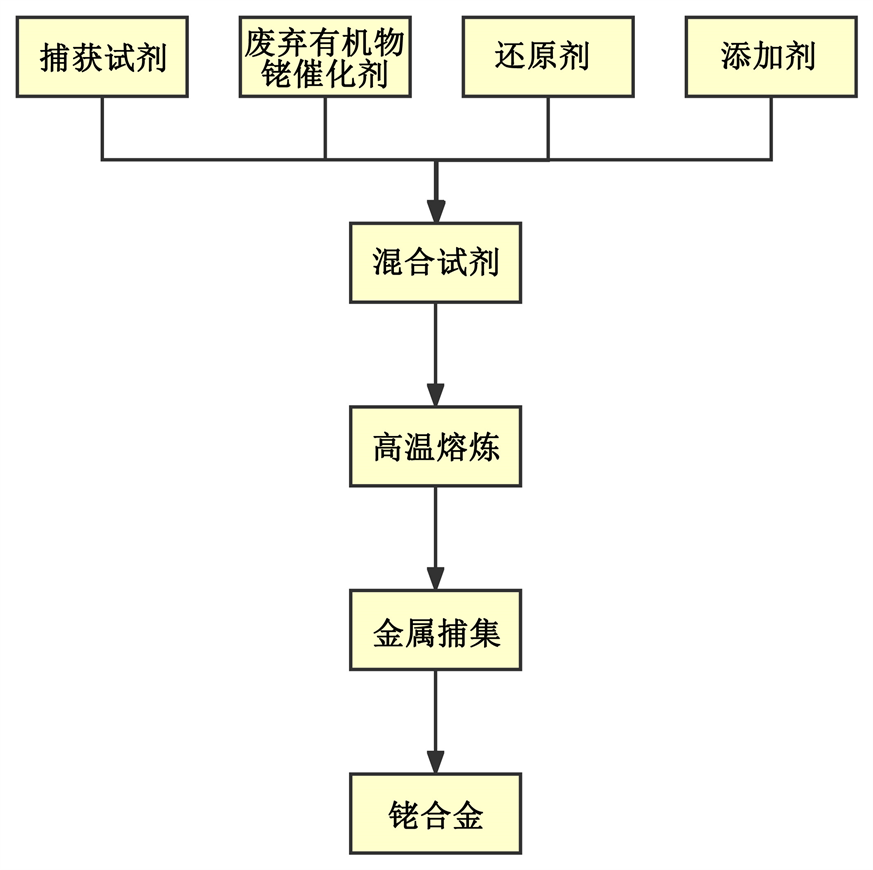
Figure 3. Flow chart of metal capture method
图3. 金属捕集法流程图
赵家春等人 [18] 使用铜捕集法回收铂族金属,计算反应的ΔGTΘ-T关系,采用Factsage软件计算CaO-Al2O3-SiO2-MgO系相图及相应的渣黏度,以及铜−铂族金属相图,并进行分析。通过实验验证,结果表明铂族金属氧化物优先于氧化铜被还原为金属态,结合从铜−铂族金属相图,铜能与铂、钯、铑连续固溶形成合金;证实了铜捕集法从失效汽车催化剂中回收铂族金属的可行性。当固定捕集剂氧化铜配比40%,还原剂焦粉配比为6%,熔炼保温时间5 h,在熔炼温度1400℃,碱度1.05的条件下,铂、钯、铑回收率分别为98.2%、99.2%、97.6%。
张福元等人 [19] 以低熔点(271.3℃)、高密度(9.808 g/cm3)、绿色无毒的金属Bi作为捕集剂,火法熔炼废汽车催化剂富集Pd、Pt和Rh,配入Na2CO3、硼砂、SiO2进行造渣,在熔渣碱度0.71、硅硼质量比0.94:1的条件下于1100℃的环境熔炼10 min,使用1.9 g的金属Bi作为捕集剂,可以使Pd、Pt、Rh的回收率分别为98.90%、95.02%、97.00%。然后重复操作,将熔渣二次熔炼,Pd、Pt、Rh的回收率均大于99%;熔炼过程中Pd、Pt、Rh优先被还原,以原子态或原子团簇形态与金属Bi键合,可形成α-Bi2Pd、Bi2Pt、Bi4Rh等二元金属间化合物,有利于降低体系自由能,实现金属Bi对Pd、Pt、Rh的良好捕集。
金属捕集法具有原料适应性强、操作成本低、熔融环境要求低、捕集效率高、生产规模大等优点,但使用各种金属作为捕集剂也都具有相应的优点和缺点 [20] ,如使用Fe可高效捕集铂族金属 [21] ,但铁的熔点高达1535℃、熔炼能耗大;Pb可氧化冶炼高度富集铂族金属,但铅具有毒性、污染环境;镍锍和铜捕集铂族金属后难以分离捕集剂,分离工艺复杂、成本较高。
2.1.4. 挥发法
挥发法是指在高温下用氯气和氯化剂处理废催化剂使其形成铂族金属的可溶性氯化物或气态氯化物 [18] ,然后,使用水、碱性溶液、氯化物络合物或吸附剂将其吸收,达到循环利用的目的。除此之外,也可以通过挥发和氯化除去部分载体,从而达到富集铂族金属的效果。
日本专利提出 [22] ,在Rh的氯化处理方法中,使用包含Ru和Rh等(Pt, Pd, Ru, Rh, Ir, Os)的铂族金属的原料与平均粒径 ≤ 100 μm的氯化钠粉末混合;将混合物在氯气中进行氯化焙烧处理,从而蒸发形成氯化物的铂族金属,使铂族金属成为可溶性盐,然后对处理过的材料进行浸水处理,从而回收铂族金属。
氯化气相挥发法具有工艺简单、试剂用量少、能耗低等优点,但生产过程中高温氯化对设备有腐蚀作用,废催化剂存在吸附氯气的现象,整个回收过程中需要处理大量有毒气体。此外,氯化处理不当,也会对人体和环境造成危害。
总之,火法工艺由于其工艺流程短,回收率等优点,被广泛利用,火法回收技术依旧是今后铑二次资源回收的主要技术。因此,火法回收铑的研究仍需要不断地改善与迭代。
2.2. 湿法冶金工艺
湿法冶金依赖于酸或碱等溶液来溶解金属组分 [23] ,然后将其浓缩和纯化以回收所涉及的金属 [24] 。湿法工艺主要包括预处理、浸出和萃取过程。溶解是预处理的关键一步,也是将载体与废料中的铂族金属分离的最重要步骤之一。通常溶解会使用三种方法:载体溶解法、活性组分溶解法和全溶解法 [25] 。载体溶解法是将失效的催化剂载体溶解,使铂族金属富集在不溶性渣中,化学性质稳定,不易被普通无机酸侵蚀。载体溶解法适用于以γ-Al2O3为载体的催化剂的处理 [26] ,但如果载体为α-Al2O3,溶解率不高,必须用其他方法分离α-Al2O3。此外,碱溶法对设备要求高,并且存在固液分离操作困难等问题。活性组分溶解法是与载体溶解法相反的一种方法,是使用一种或多种氧化剂盐酸溶液溶解废料中的铂族金属组分,使[PtCl2]6−、[PdCl2]4−、[RhCl2]6−离子形成进入溶液,然后从溶液中萃取出来。采用活性组分溶解法,试剂消耗少,回收成本低,回收率高,但浸出渣中仍含有较高含量的铂族金属,容易造成大量浪费。全溶解法是在氧化剂存在下将载体和废料的活性组分两者溶解到溶液中,与一种或两种酸混合,然后从溶液中提取铂族金属。该方法能保证铂族金属的高回收率 [27] ,但酸耗高,处理成本高,且与载体溶解法相似,只适用于以γ-Al2O3为载体的催化剂的处理。将废料溶解之后,还需要使用不同的工艺进行处理,根据这些方法的不同,可分为氧化法、还原沉淀法、溶剂萃取法和离子交换法等,下面具体介绍这几种工艺。
2.2.1. 氧化法
中性分子加成到配位不饱和的低价过渡金属有机配合物上,使过渡金属的氧化态和配位数均升高的反应叫作氧化加成反应,如图4所示是Wilkinson配合物的氧化加成反应。常见的氧化法是将铑废料溶解后破坏铑簇,使其游离在溶液中,然后添加氧化剂将铑离子氧化,使铑以离子形态进入溶液,最后进行富集回收。
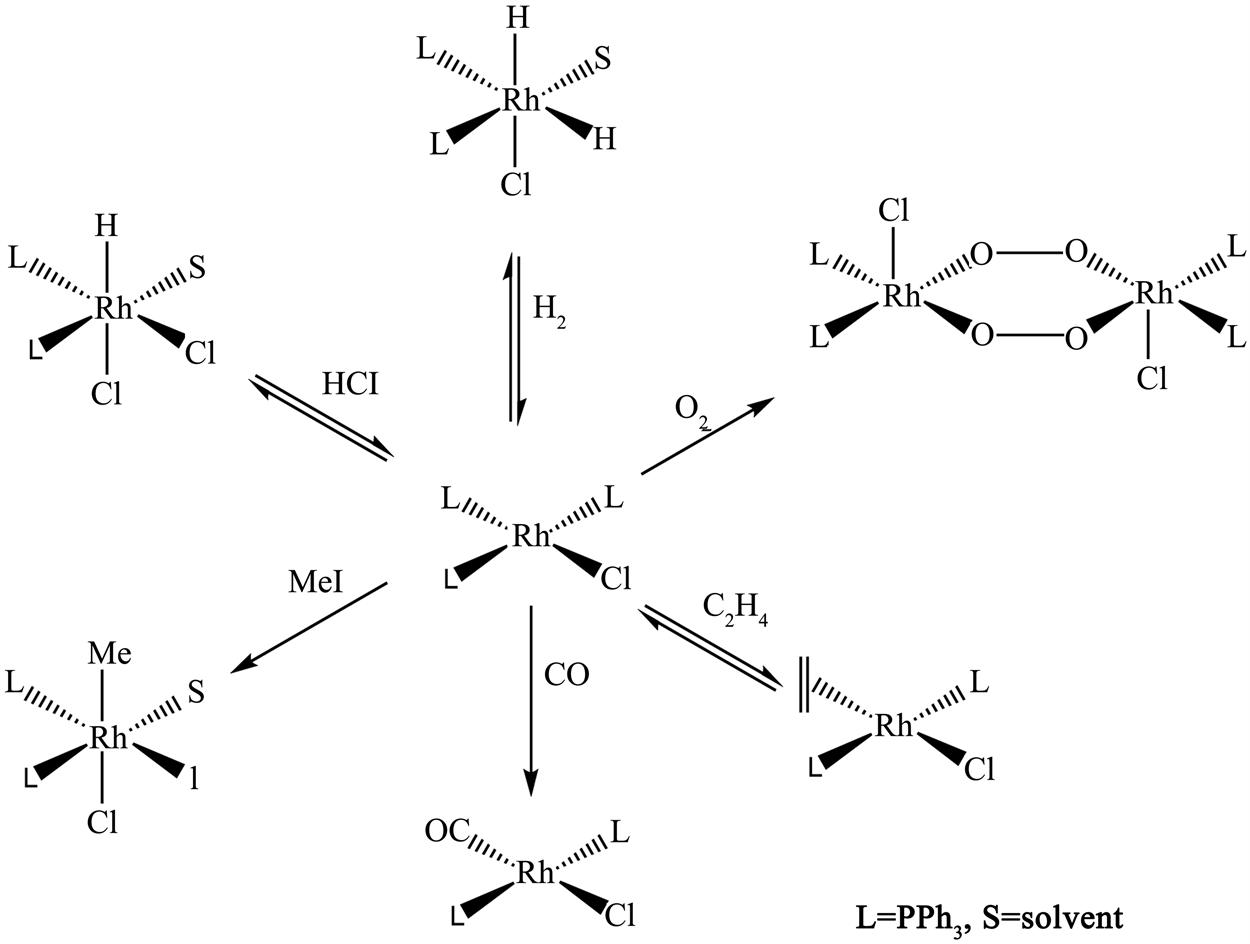
Figure 4. Oxidation addition reaction of Wilkinson complex
图4. Wilkinson配合物的氧化加成反应
C.A. Nogueira等人 [28] 在盐酸介质中使用铜离子氧化浸出废催化剂中的铑和钯。具体方法如下:使用了足量的盐酸(HCl 37%)和氯化铜(CuCl2∙2 H2O),确保温度控制与搅拌速度控制的情况下进行搅拌,计算反应时间。随着反应时间从纸浆中收集少部分试样,离心,并将澄清溶液送去分析,随时间跟踪反应进程。在每个实验结束时,过滤悬浮液,用软化水洗涤固体,干燥并称重。然后通过电感耦合等离子光谱发生仪(ICP-AES)进行Pd和Rh的分析,分析温度,浓度,反应时间对于铑和钯回收效果的影响,并得出结论:当T = 80℃,t = 4 h,[HCl] = 6 M,[Cu2+] = 0.3 M时获得的最大浸出产率为Pd的95%和Rh的86%。
氧化法减少了设备需求,避免了焚烧带来的污染与高能耗,且工艺简单,操作便捷,但铑回收率较低。
2.2.2. 沉淀法
沉淀法是从废催化剂中回收铂族金属的最常用方法,分为沉淀分离法和共沉淀分离法。主要方法是在样品溶液中加入共沉淀剂和还原剂后,共沉淀载体在沉淀过程中通过吸附、包埋、混晶等方式与载体一起从溶液中沉淀出来,从而与基体元素分离。常用的沉淀剂有硫脲、硫化钠、亚硝酸钠、氯化铵等。
B. Raju等人 [29] 从不含Pt的萃余液中回收铑,加入硫化铵调节pH值约为8.5,然后加热至60℃并在此温度下保持30分钟,冷却并使溶液沉淀。过滤,用酸化蒸馏水(pH = 4.0)洗涤沉淀的铑以除去Mg杂质,并烘干以得到纯硫化铑。铑的回收率 > 99%。沉淀法使用不同的沉淀剂 [30] ,提供H源、Cl源、CO源、acac源试剂,加入三苯基膦(TPP),产生容易沉淀的物质,如RhCl (CO) (TPP)2、HRh (CO) (TPP)3及Rh (CO) (acac) (TPP),以从废催化剂中分离Rh。该工艺简单、成熟,部分失活催化剂直接活化。然而,催化剂失活程度越高,越难以形成沉淀。结果,回收率大大降低,表明其严重依赖于废催化剂溶液中Rh催化剂的活性。
还原沉淀法的优点是设备简单、投资少、处理量大。然而,不方便的操作和缓慢的反应速度限制了其应用。此外,在添加沉淀剂时引入其他元素,特别是含有金属元素的沉淀剂,增加了后处理的难度 [30] 。产生的污泥量大且难以回收利用,容易产生污泥的二次污染。
2.2.3. 萃取法
萃取法是通过选取不同的萃取剂,同铑废液中的铑产生作用生成新的配合物,再通过萃取,实现铑的富集回收。Thomas James Bell等人 [31] 采用疏水性铵基离子液体和CMPO或TODGA作为萃取剂,成功地从硝酸水溶液中萃取铑(III)。Andrew I. Carrick等人使用伯胺(2-乙基己胺)与伯酰胺(3,5,5-三甲基己酰胺)协同作用下,使铑配合物以离子对[(HLA3RhCl6)]的形式存在于有机相中,然后通过水汽提直接回收,成功从4M盐酸中萃取超过85%的铑。
溶剂萃取法是一种高效的分离方法,具有分离效果好、操作简单、安全性高、能耗低等优点 [26] 。但是萃取使用的大部分萃取剂有毒、易燃且易挥发,选取适宜的萃取剂是关键。此外,萃取法还存在选择性不高、反萃取难等问题。
2.2.4. 吸附法
吸附法基于通过吸附剂吸附某些元素或离子,一般来说,吸附法主要使用离子交换树脂技术进行吸附分离。离子交换法是通过使用离子交换剂交换溶液中的离子的分离方法。图5展示了一种通过树脂分离Pt、Pd和Rh的流程图。离子交换树脂因其对铂金属离子的高容量和选择性以及交换剂颗粒的机械强度和韧性而闻名。离子交换树脂是一种具有多种功能基团的高分子离子交换剂,根据其所含官能团的性质,离子交换树脂可分为七类:强酸、弱酸、螯合、氧化还原、弱碱、酸碱两性和强碱 [24] 。
专利CN102912128A中 [32] 提出一种用阴离子交换树脂分离提纯铑的方法,首先将树脂活化,采用D315离子交换树脂,接着将2倍树脂体积的5N浓度的HCl酸,以线速度2 m/h通过树脂层,并浸泡2~4 h,用软水,以线速10 m/h通过树脂层,洗至出水pH = 2~3用2倍树脂体积的2% NaOH,以线速度2 m/h通过树脂层,并浸泡2~4 h,用软水,以线速10 m/h通过树脂层,洗至出水pH = 8~10;下一步进行离子交换:将配制好的铑酸溶液,以8 m/h的线速度通过树脂层;最后用2%质量分数的NaOH以线速度2 m/h通过树脂层,至流出液无色,收集流出液,采用icp法测定其中铑含量,铑收率大于95%。
AleksandarN等人 [33] 使用三种不同的树脂,分别是Lewatit (德国)生产的强碱树脂(LewatitM + MP600);由Purolite (UK)生产的弱碱树脂(PuroliteS985)和由Dow (USA)生产的螯合型树脂(XUS43600.00),在室温下使用内径为10 mm的玻璃色谱柱,用载有含铂族金属的树脂的浆液填充柱,得到树脂床高度与柱直径的近似比率为6:1。然后以2 BV/h (10 mL/h)的速率从下到上添加洗脱液5小时,选择性洗脱树脂中的铂族金属离子。每30分钟收集通过树脂的1 BV (5 mL)洗脱液的样品,直到总共10 BV (50 mL)洗脱液通过柱。洗脱5小时后,用去离子水以10 BV/h的速率洗涤树脂。测量并记录所用去离子水的体积,并取溶液样品进行分析。对三种不同树脂中的每一种重复这些步骤。最后结果表明,弱碱硫脲官能化的XUS43600.00螯合树脂表现出显着更大的吸附选择性,可完全洗脱Pt和Pd,但对于铑的吸附与洗脱还需要进一步的研究与对树脂不同基团的选择。另外,AleksandarN等人 [34] 还对离子交换树脂技术过程中酸度和氯化物浓度的影响、溶液老化的影响、温度的影响等方面,得出结论,在弱酸性溶液中,温度越高,铑离子的水合速率越快,没有形成中性络合物,并且可以减少所谓的“老化”。
吸附法分离具有分离效率高、选择性好、成本低、设备和操作简单等优点,因此,吸附法的前景也更值得期待。同时其反应速度慢、树脂处理困难、易产生二次污染等问题也亟需解决。
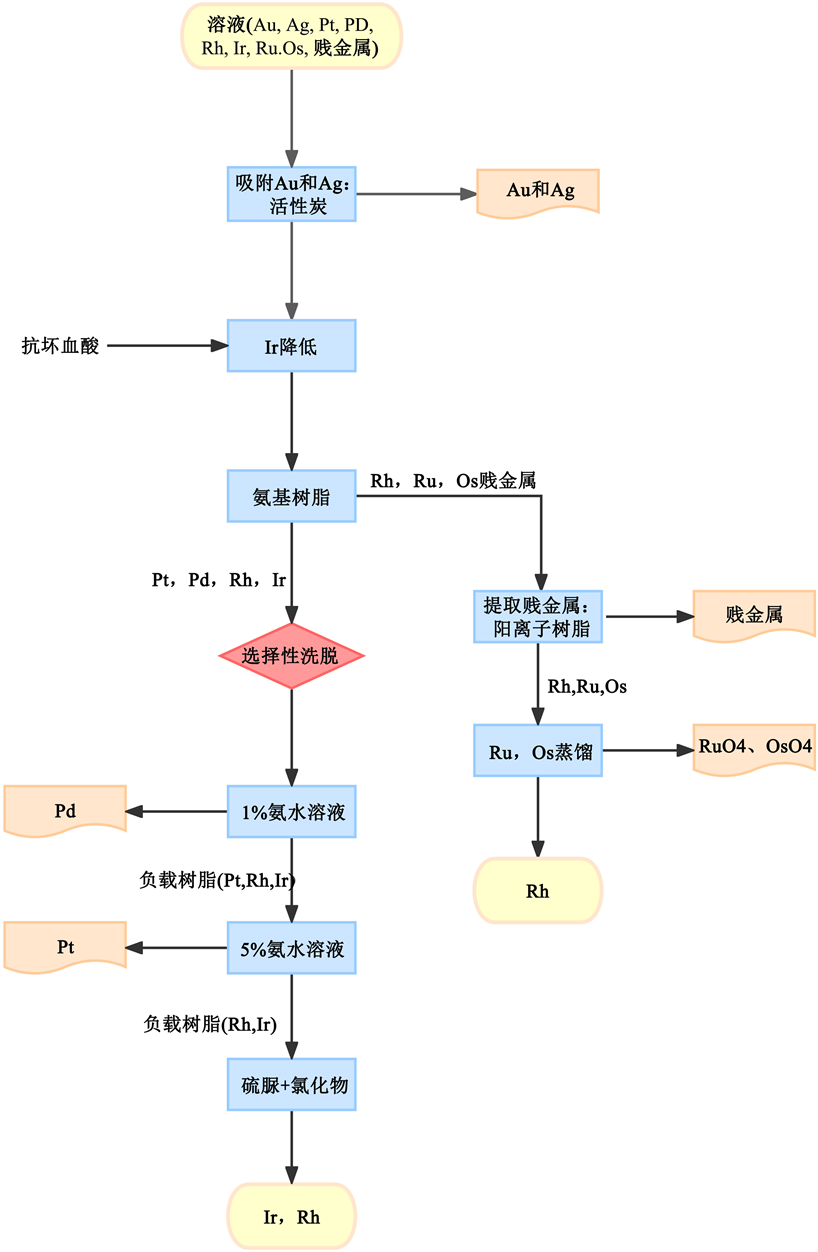
Figure 5. Flow chart of resin separation Pt, Pd, and Rh
图5. 树脂分离Pt、Pd和Rh流程图
与火法冶金工艺相比,湿法冶金方法优点十分明显:适合于低成本的小规模处理;回收的贵金属质量优良;温和的反应条件和低能耗 [35] 。但是,它被以下问题困扰:工艺复杂,损失一定量的贵金属;碱性或酸性浸出剂腐蚀性强,对环境造成不可避免的二次污染 [36] ;萃取中的萃取剂和稀释剂具有高毒性,对环境和人类健康造成潜在威胁;产生大量废水,其中含有难以处理或回收的废化学溶剂。因此,继续研究开发一种低成本和避免环境污染的贵金属回收工艺依旧很有必要。
2.3. 其他工艺
生物吸附 [37] 是利用活性或非活性微生物及其代谢产物(包括酵母、细菌活性物质、细菌、真菌、藻类和一些生物废弃物),通过物理相互作用和/或化学反应(包括络合和沉积、氧化还原和离子交换等)吸附金属。生物质的状态(活性或非活性)、生物材料的类型、金属溶液的化学性质和环境条件基于细胞表面上的官能团与金属离子之间的金属离子的螯合和络合、离子交换和静电相互作用形式的物理化学相互作用都会影响生物对金属吸附。Minjie Gao等人 [38] 以高密度培养的废巴斯德毕赤酵母和表面展示Rh金属肽的重组巴斯德毕赤酵母(P. pastoris GS-R)为吸附剂,研究了Rh (III)的吸附性能,在生物量为0.25 g·L−1,pH为1.2,温度为30℃,吸附时间为2 h,对废弃毕赤酵母和毕赤酵母GS-R的最大吸附率分别为55.69% (110.1 mg·g−1)和75.03% (142.11 mg·g−1)。
Kin-ya Tomizaki等人 [39] 研究了从含有稀HAuCl4和H2PtCl6 (各5.0 × 10−5 M)和含芳香族氨基酸的肽(各2.0 × 10−4 M)的混合物的均匀水溶液中选择性回收贵金属。Abdusalam Uheida等人 [40] 测试了钯(II)、铑(III)和铂(IV)在Fe3O4纳米颗粒上的吸附效果。研究表明,Fe3O4纳米粒子可用于从稀盐酸溶液中去除Pd (II)、Rh (III)和Pt (IV),纳米颗粒表现出良好的动力学特性(平衡时间 < 30 min)和在pH = 2.5下对Pt (IV)、Pd (II)和Rh (III)的高吸附负载能力(即pH < 30 min)。0.068、0.103和0.149 mmol·g−1)。铁氧化物纳米颗粒显示出对Rh (III)离子的高亲和力,并且在Pd (II)和Pt (IV)离子共存时主要吸附Rh (III)离子。
这些方法具有原料便宜,容易获得等优点,但技术相对来说并不成熟,仍需进行继续研究。结合火法冶金工艺和湿法冶金工艺,下面具体总结了这些回收方法的优缺点(表1)。
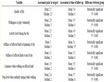
Table 1. Advantages and disadvantages of common recycling methods
表1. 常见回收方法的优缺点
3. 总结
由于贵金属在工业催化剂、功能材料和电子产品中的大量使用,存在多种贵金属的二次资源,以及加工过程中出现的环境污染问题,对贵金属的二次资源富集技术需要更高的要求。本文综述了铑废料的回收方法。这些方法主要分为湿法冶金、火法冶金,这些方法都有各自的优缺点,仍需不断改进与发展。在目前的工业实践中,火法冶金工艺具有处理周期短、废水排放量少、经济成本低等优点。然而,它需要大量的能源和投资,并造成环境污染。相反,湿法冶金是允许以温和的反应条件和低能耗为代价的小规模加工。但是,相应的工艺是复杂并且产生大量的含有废化学溶剂的废水。目前的技术是依旧有很大缺陷,离工业化还有很长的路要走。
目前,废铑催化剂的回收主要依赖于高温处理、湿法金属分离和随后的纯化工艺的组合。由于大规模处置的需求和环保要求的不断提高,除了开发新的回收工艺外,还需要进一步优化现有的回收工艺,完善废催化剂回收的产业链。建议从贵金属二次资源的特殊性出发,加大对二次资源回收技术开发的投入,逐步建立健全高效的贵金属回收体系,从而达到能够在不增加环境负担的情况下有效利用二次资源,同时保持一定的经济效益。