1. 引言
铝合金具有塑性高、抗腐蚀的功能特点,同时也是优良的导电、导热金属材料,在电化学储能行业常用于制造电芯极柱、壳体和巴片等。铝的化学活性高,经一系列暴露于自然环境的生产过程,其表面发生自然氧化形成厚度约2~30 nm的氧化膜 [1] ,该氧化膜表层结构疏松多孔,如图1所示,易吸收水分、油污和其他污染物;在后道的激光焊接过程中,因激光焊接熔池体积较常规熔化焊小很多,且深宽比很大,熔池冷却结晶速度极快,易形成密集的气孔缺陷,严重影响焊缝质量 [2] 。
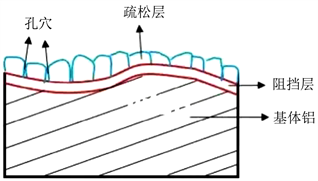
Figure 1. Schematic diagram of aluminum alloy oxide film structure
图1. 铝合金氧化膜结构示意图
为提高铝合金焊接质量,除恒温恒湿的焊接环境、惰性气体焊道保护和稳定的焊接参数外,母材焊接区域的表面状态也尤为重要,必须实施适当的预处理措施。行业内传统的氧化膜去除方法有物理方法(机械打磨、超声波等)、化学方法(酸溶、碱蚀等)和电化学法(阴极剥离、直接还原等) [3] ,而新兴的激光清洗预处理被普遍认为更具高效、无污染、几乎无损伤等优点 [4] 。
国外学者A. W. Alshaer [5] 等使用Nd:YAG激光器(Neodymium-doped: Yttrium Aluminium Garnet; Nd:Y3Al5O12)对AA6014铝合金进行焊接前激光预处理,验证焊缝气孔可明显减少;Haboudou [6] 等采用化学脱脂、220和800级金刚砂纸(P220、P800)、喷砂以及激光清洗方法预处理A5083铝合金表面,横向对比同样表明焊前激光预处理方法更能显著降低焊缝气孔率。
以上研究提及的“气孔率”均是对单道焊缝内的气孔缺陷体积占比进行核算,且仅部分试样的结果表征不足以量化激光清洗预处理的稳定性提升比例和经济效益;本文参考国内学者栗红星 [7] 等的实验方法,分别使用化学方法(无水乙醇擦拭)、物理方法(P800砂纸打磨)和激光清洗三种工艺预处理电芯极柱,后在一致焊接条件、同种焊接母材下施焊,横向对比焊后质量,经批量焊接验证后统计三种试样的合格率,以量化焊缝质量的稳定性和气孔缺陷改善比率。
2. 实验材料、设备和方法
2.1. 母材物料
使用单一品牌、同批次物料实验,品牌电芯极柱和定制巴片母材均为1060铝合金,主要化学成分如表1所示;品牌电芯外观和上盖极柱结构如图2所示,巴片为带有定位孔的几字形结构,且统一经过研磨表面预处理,批次、时效一致,如图3所示。
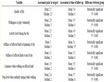
Table 1. Main chemical composition of 1060 aluminum alloy
表1. 1060铝合金主要化学成分
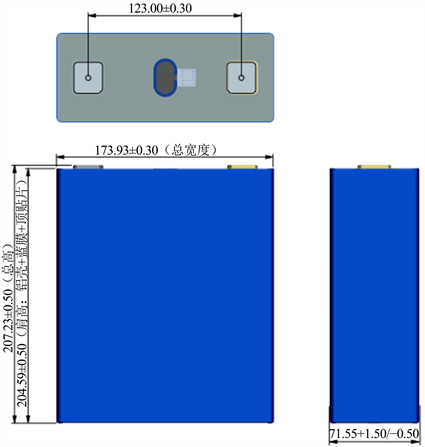
Figure 2. Appearance of cells and upper cover pole
图2. 电芯外观和上盖极柱结构
2.2. 激光设备
激光清洗设备型号UWLLWIPG250WMBVA1,集成250W IPG脉冲光纤激光器、寻址定位摄像头和集中除尘管路等,激光器性能参数见下表2。
激光焊接设备型号YLS-4000/2000-AMB-P,具备将两种不同波长激光复合,使两束激光的轴线在空间重合,运用主波段激光深熔焊接、次波段激光预热缓冷并适度热传导焊接的复合焊功能,产品示意如图4所示。
2.3. 预处理和焊接接头
预处理措施仅用于电芯极柱上表面,巴片正反双面维持来料状态、压缩空气除尘;预处理措施分别为工业无尘擦拭纸蘸取无水乙醇擦拭、P800金刚砂纸手工打磨和激光清洗,擦拭和打磨措施是对整个极柱上表面,而激光清洗仅限¢14 mm的圆形区域,如图5所示。
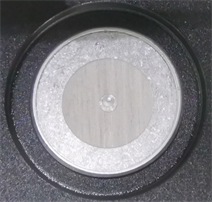
Figure 5. Pole state after laser cleaning
图5. 激光清洗后的极柱状态
焊接接头为巴片和极柱形成的搭接接头,其剖面结构示意见图6,中间孔洞为巴片与极柱的定位孔,焊缝外观形态为图7所示的环焊缝。
2.4. 焊接过程和工艺
极柱预处理、巴片定位放置和激光焊接等工序均在自动化产线完成,其流转节拍为45 s,即预处理完成后90 s便压装、施焊,工序流程如图8所示,焊接参数设定见表3,焊接轨迹为外径11.5 mm、中径10.5 mm的圆形螺旋线,如图9示意。

Figure 8. Experimental process flowchart
图8. 实验工序流程图
2.5. 焊接质量评定标准
激光焊接参数和设备经调实验证后,可以规避焊偏、虚焊、漏焊等常规缺陷,实验结果的判定仅关注表面气孔类缺陷和有效熔深、熔宽,经目视检查出现焊缝表面爆孔即为不合格,缺陷外观形貌如图10所示。针对出现爆孔缺陷的实验样件,进行剖切和宏观金相检查,要求有效熔深0.8~2.0 mm、有效熔宽 ≥ 1.8 mm,有效熔深和熔宽示例见图11。
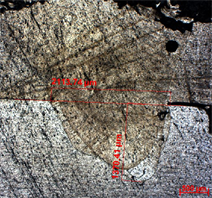
Figure 11. Effective penetration depth and width
图11. 有效熔深、熔宽示例
3. 结果与讨论
实验过程累计焊接电池模组(单模组含26颗电芯、52处极柱) 224套、焊接焊缝11,648条,其中分别有12套模组进行无水乙醇擦拭和砂纸打磨预处理,均出现可观的爆孔缺陷焊缝;激光清洗预处理的焊缝因爆孔缺陷发生频次极低,增大焊接模组至200套,形成如下表4实验结果。
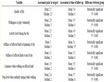
Table 4. Statistics of experimental results
表4. 实验结果统计
剖切27例存在焊缝爆孔缺陷的实验样件,经宏观金相测定,其有效熔深、熔宽均符合标准规范,仅在焊缝内存在少量微小气孔,部分缺陷试样如图12所示;据此分析,激光焊接熔深的大小主要与激光吸收率有关 [7] ,而巴片上表面经统一研磨、表面状态一致,故激光吸收率、焊缝热输入理论一致,过程中的气体析出、气孔形成对有效熔深和熔宽的形成无显著影响,爆孔位置可经修复焊接后继续使用。
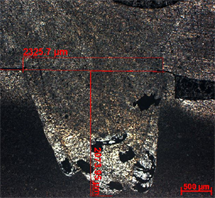
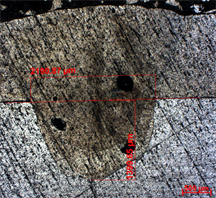
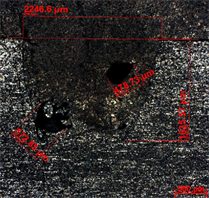
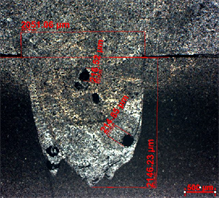
Figure 12. Macroscopic metallography of samples with hole defects
图12. 部分爆孔缺陷试样的宏观金相
经激光清洗预处理的实验样件,统计其不合格率仅为无水乙醇擦拭的1/80、砂纸打磨的1/120,爆孔缺陷呈2个数量级的降低,显著提升焊接质量稳定性和产品加工经济性。浅析其原因:砂纸打磨预处理受限于人工作业,难以控制清除面积和深度 [2] ,在清除大部分氧化膜的同时有一定残留;无水乙醇并不具备化学腐蚀特性,但其是一种极易挥发的良好有机溶剂,通过擦拭可清除表面污染物,且快速挥发后无残留,疏松氧化膜及其内部的结晶水、化合水则无法去除;而激光清洗直接作用于氧化膜和表面污染物,使之短时间内汽化蒸发、表面脱附,同时受表面形成的金属蒸汽流影响而带动逸出,有效减少氢、氧元素的引入。
4. 结论
1) 激光清洗较砂纸打磨、无水乙醇擦拭预处理,能获得更好的去除污染物和氧化膜效果。
2) 激光清洗预处理有更高的可靠性和稳定性,能降低爆孔缺陷概率至砂纸打磨的1/120、无水乙醇擦拭的1/80。
3) 激光焊接过程中的气体排出、气孔生成对有效熔深和熔宽的形成无显著影响,出现爆孔异常的焊缝可经修复焊接后正常使用。
4) 激光清洗预处理工艺,并不能完全规避气孔类缺陷,仍需加强焊接过程质量控制。