1. 引言
随着我国特高压输电、高频信息技术及国防军工等领域的快速发展,为了降低噪声和铁损,提高能源利用率,高硅电工钢的市场需求量与日俱增。通用的高硅钢一般是指Fe-6.5 wt% Si,相比于传统Fe-3.0 wt% Si硅钢,其电阻率约提高一倍,磁各向异性常数K1约降低40%,磁致伸缩系数λs近似为零,在工频、中频、高频领域均可大幅降低铁损,节能效果显著,且可显著降低设备的噪音,实现电器设备的高速化、高频化、小型化、轻量化、节能化。因此,Fe-6.5 wt% Si高硅钢被认为是制备铁芯的最为理想的材料 [1] ,主要是用来制造高速高频电机、音频和高频变压器、扼流线圈和高频下的磁屏蔽等 [2] [3] 。
由于低温下有序相的出现使得高硅钢变得硬且脆 [4] ,高硅钢的塑性变形能力大幅下降,采用常规轧制工艺流程难以制备出板形良好的高硅钢薄板,从而限制了高硅钢在工业领域的生产及应用。目前,仅日本JFE公司采用化学气相沉积法成功地实现了高硅钢薄带的工业化生产 [5] ,但这种高温渗硅工艺需采用剧毒的SiCl4气体,并产生大量的FeCl2废气,严重污染环境,这与我国可持续发展战略相悖。
物理气相沉积(PVD)是一种物理气相反应生长法,相对于CVD法,PVD过程发生在真空条件下,其沉积层纯度高,无有害气体排出,属于无污染技术 [6] 。从生产能力和环境友好性的角度来看,PVD技术是一种很有前途的高硅电工钢制造技术。我国科研人员在采用PVD法制备高硅钢方面做了大量研究工作,揭示了硅的渗透机理和扩散过程,并申请了相关的专利 [7] [8] [9] 。然而,前人采用PVD技术制备取向高硅钢均选用了0.20~0.27 mm厚的取向硅钢工业板作为基体材料。一方面,由于取向硅钢工业板较厚,通过渗硅处理很难获得均匀的高硅电工钢。另一方面,取向电工钢工业板室温组织是已经发生了二次再结晶的粗大晶粒,在后续扩散退火过程中,其微观结构和织构几乎没有变化,粗晶对高硅电工钢磁性能产生负面影响。
鉴于此,本文以0.08 mm冷轧硅钢片为初始材料,采用磁控溅射法制备高硅钢。选择超薄冷轧硅钢片作为初始材料主要基于以下两个方面的考虑:一方面,超薄冷轧硅钢片在退火过程中可以释放变形储能,更有利于硅元素的均匀化扩散,另一方面,可以通过调控退火工艺,控制实验钢晶粒尺寸和织构,以期获得具有优异磁性能的取向硅钢超薄带。
2. 实验方法
本文以0.27 mm厚的3.0 wt.% Si取向硅钢商业板为初始原料,经过70%冷轧后获取冷轧取向硅钢超薄带,采用磁控溅射法制备超薄取向高硅钢。制备流程为:采用纯硅靶材,在真空气氛下对冷轧取向硅钢超薄带正面和背面各持续溅射3.5小时。沉积后,将沉积有“纯硅涂层”的样品以400℃/h的速度从室温快速加热至1150℃进行高温扩散退火,然后在炉中冷却至室温。在750℃、850℃、950℃、1050℃和1150℃下采集中间样品。在整个热处理过程中,所有试样都受到70% N2和30% H2混合气氛的保护,制备工艺路线如图1所示。采用辉光放电光谱测量各工艺下实验钢截面硅浓度梯度,采用配备有Oxford Instruments HKL Channel 5 EBSD系统的蔡司ULTRA 55扫描电子显微镜测量和分析微观织构,并通过D5000 X射线衍射仪测量宏观织构。采用扫描电子显微镜(SEM)检测实验样品横截面的成分和微观结构,采用MPG200D电工钢磁性能检测仪测定各工艺下实验钢的磁性能。
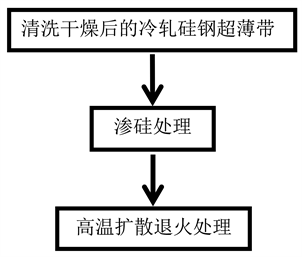
Figure 1. Basic path for preparing ultra-thin grain-oriented high silicon steel by siliconizing method
图1. 渗硅法制备超薄取向高硅钢基本路线
3. 实验结果与分析
3.1. 渗硅初始样品组织与织构
取向硅钢商用板宏观组织和织构如图2(a)~(b)所示。从{200}极图可见,取向硅钢商用板具有锋锐的Goss织构,取向偏差角 ≤ 10˚。组织均发生了二次再结晶,平均晶粒尺寸约为2~3厘米,如图2(a)。经过70%冷轧后,硅钢薄带呈现了Goss晶粒沿TD轴转向{111} < 112 >规律,这与单晶Goss形变规律基本一致 [10] ,最终形成了蓝色的{111}织构,在剪切带处含有少量的红色Goss晶核,如图2(c)~(d)所示。

Figure 2. The macrostructure and texture of initial samples; (a) The macrostructure of initial samples; (b) Initial samples {200} pole figure; (c) EBSD orientation maps of 70% cold rolling (d) 70% cold rolling {200} pole figure
图2. 初始样品组织与织构;(a) 初始样品宏观组织;(b) 初始样品{200}极图;(c) 冷轧70%晶粒取向成形图;(d) 冷轧70% {200}极图
3.2. 渗硅过程
(1) 扫描组织
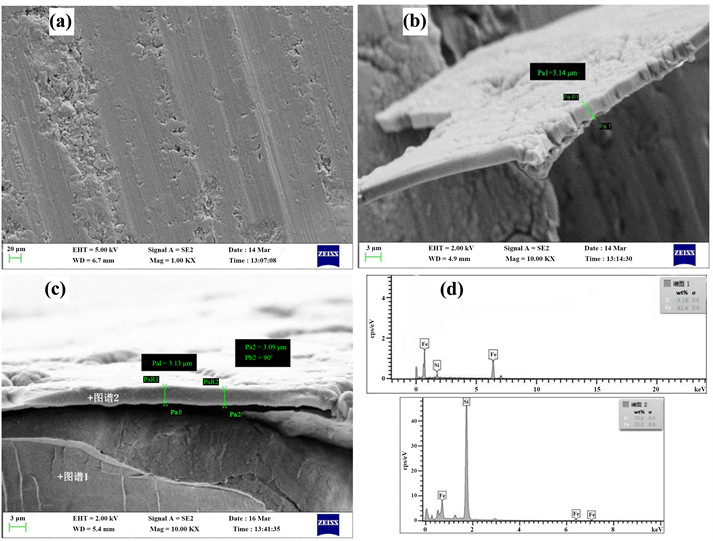
Figure 3. SEM images after siliconizing; (a) Morphology; (b) Surface micro-topography; (c) Lateral morphology; (d) Energy spectrum
图3. 渗硅后样品SEM图像;(a) 表面形貌;(b) 表面微观形貌;(c) 侧面形貌;(d) 能谱分析
图3为冷轧硅钢超薄带渗硅后的扫描形貌,由扫描及能谱分析可知,通过PVD法渗硅3.5 h之后,样品表层沉积的硅含量近80%,同时硅元素的分布较为均匀分散。另外,表层部分区域存在空洞现象,如图3(a)~(b)所示。分析其原因,主要是因为在沉积过程中,随着沉积速率的增加,沉积时间的延长,等离子体带电粒子轰击基体的表面引起基体的表面缺陷增多,对已经沉积的铁硅合金薄膜造成“烧蚀”,从而导致表层部分区域硅粉脱落。通过观察渗硅后表层空洞微观形貌以及侧面形貌可知,渗硅3.5 h后,表层沉积一层3 μm左右的“硅膜”。光谱1处为超薄带基体硅含量,图谱2为沉积层硅含量。从图3(c)~(d)图谱2可见,沉积层均匀分布并且硅纯度极高。
(2) 辉光放电光谱(GDS)
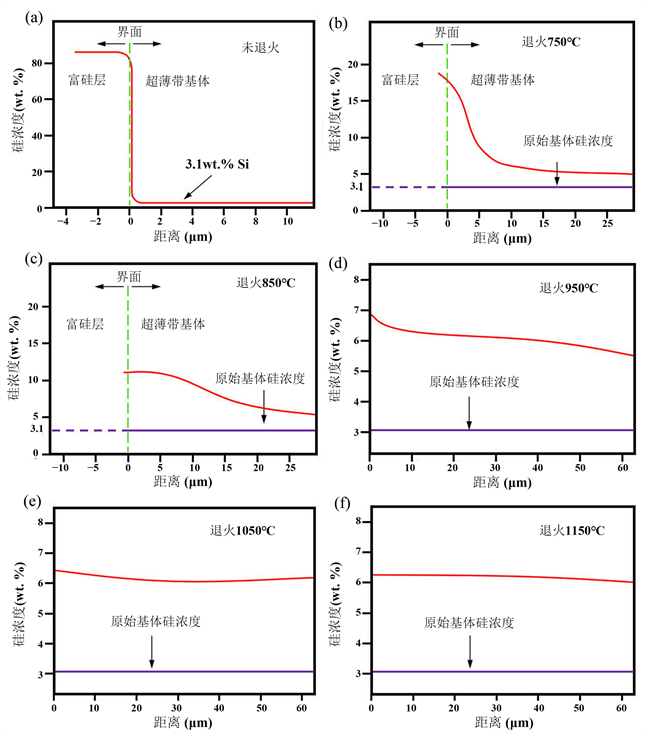
Figure 4. Silicon concentration detection under different annealing temperature; (a) Unannealed ; (b) 750˚C; (c) 850˚C; (d) 950˚C; (e) 1050˚C; (f) 1150˚C
图4. 不同退火温度下硅成分检测;(a) 未退火;(b) 退火750℃;(c) 退火850℃;(d) 退火950℃;(e) 退火1050℃;(f) 退火1150℃
将沉积“硅膜”后的样品在室温下以400℃/h升温速率升至1150℃进行高温扩散退火,并于750℃、850℃、950℃,1050℃和1050℃中间取样。图3为辉光离子放电成分检测结果。由成分检测结果可知,未经扩散退火的硅膜厚度约为3.2 μm,这与SEM图像结果基本一致,基体硅含量为3.1%,如图4(a)所示。随着退火温度的升高,基体硅含量明显上升,而“硅膜”厚度以及硅元素百分含量明显下降,硅元素浓度呈现梯度分布,如图4(b)所示。当升温至850℃时,“硅膜”厚度近乎为零,表明沉积后的硅膜完全渗入到硅钢薄带基体当中。退火温度越高,硅钢基体中的硅含量均匀化程度越高,如图4(c)。所示当升温至950℃时,基体中硅含量在6.0%~6.5%之间,实现了高硅钢薄板的制备,如图4(d)~(e)所示。随着退火温度继续升高至1050℃以及1150℃时,硅元素均匀分布于薄带基体中,硅含量稳定在6.2%左右,如图4(f)所示。
(3) 宏观组织及织构演变

Figure 5. Macrostructure and texture evolution; (a) Macrostructure at 750˚C; (b) ODF diagram at 750˚C; (c) Macrostructure at 850˚C; (d) ODF diagram at 850˚C; (e) Macrostructure at 950˚C; (f) ODF diagram at 950˚C; (g) Macrostructure at 1050˚C; (h) ODF diagram at 1050˚C; (i) Macrostructure at 1150˚C; (j) ODF diagram at 1150˚C
图5. 宏观组织及织构演变;(a) 退火750℃宏观组织;(b) 退火750℃ ODF图;(a) 退火850℃宏观组织;(d) 退火850℃ ODF图;(e) 退火950℃宏观组织;(f) 退火950℃ ODF图;(g) 退火1050℃宏观组织;(h) 退火1050℃ ODF图;(i) 退火1150℃宏观组织;(j) 退火1150℃ ODF图
由于本实验基体材料选用的是冷轧硅钢薄带,样品在渗硅扩散退火过程中也发生组织与织构的演变。图5为实验钢扩散退火过程中宏观组织及织构演变,图6为实验钢在不同的退火温度条件下晶粒尺寸和主要织构百分含量统计。与前期硅钢薄带再结晶退火过程中组织与织构演变规律一致 [11] ,即均发生了初次再结晶以及二次再结晶,初次再结晶织构仍然以强的Goss织构为主,如图5(a)~(b)所示,组织以细小的等轴状晶粒为主。当退火850℃时,晶粒略微长大,Goss织构强度最强,如图5(c)~(d)所示。随着温度的升高,晶粒尺寸明显增大,如图5(e)~(h)以及图6(a)。以织构诱发为驱动力的{113} < 361 >以及γ线织构吞并初次再结晶Goss晶粒异常长大,使得Goss织构锋锐程度严重恶化,造成二次再结晶织构极为混乱,织构组分主要以Goss、{113} < 361 >以及γ线织构为主,如图5(e)~(h)和图6(b)所示。由于扩散退火采用是随炉升温,升温速率较小,二次再结晶温度停留时间长,二次晶粒晶粒尺寸较大,因此以表面能为驱动力的三次再结晶现象没有发生,如图5(i)~(j)所示。
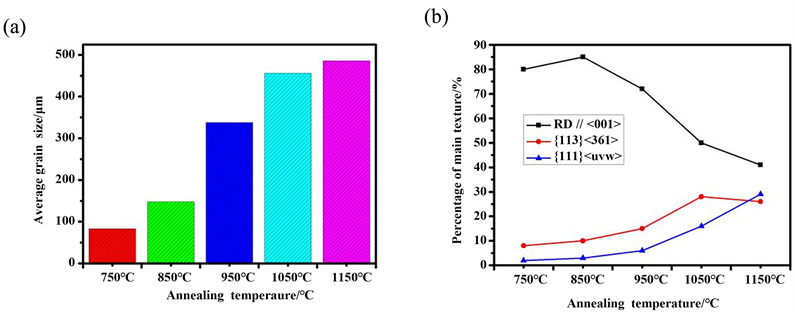
Figure 6. Quantitative statistics of average grain size and main textures; (a) Quantitative statistics of average grain size; (b) Quantitative statistics of main textures
图6. 平均晶粒尺寸及主要织构定量统计;(a) 平均晶粒尺寸统计;(b) 主要织构组分定量统计
3.3 磁性能
虽然扩散退火850℃,Goss织构最为锋锐,但由于扩散退火750℃以及850℃硅元素浓度沿厚度方向上呈现梯度分布,均匀化程度较差,表层硅百分含量超出了10%,因此本次只测得了退火950℃、1050℃以及1150℃样品磁性能,并与CVD法制备的取向高硅钢样品磁性能进行对比,如图7所示。需要说明的是CVD法制备的取向高硅钢基体采用的是取向硅钢成品板,渗硅过程中不发生组织与织构的变化,因此CVD法制备取向高硅钢的特点是晶粒尺寸大,Goss织构锋锐程度高。图7磁性能检测结果显示,随着退火温度的升高,B8值明显下降,这与Goss织构强度弱化有关。如图7(a)所示。不同频率下铁损均升高,这既与有益织构比重下降有关也与平均晶粒尺寸增大有关。另外值得注意的是,对比图7(b)~(d)可知,950℃~1050℃以及1050℃~1150℃直线斜率不同,即高频下铁损值于1050℃~1150℃上升的较快,这说明高频下晶粒尺寸在铁损中占的比重较高,晶粒尺寸越大,涡流损耗越高,从而导致铁损越高。与CVD法制备的取向高硅钢磁性能对比可知,采用PVD法制备的取向高硅钢B8值均高于CVD法,推测这与样品厚度有关(因为磁感与Goss织构锋锐程度有关,CVD法Goss织构锋锐程度更高),即本次实验硅钢薄带厚度为0.08 mm,而CVD法采用的是0.23 mm厚的取向硅钢工业板。对比同厚度(0.08 mm)的铁损数据可知,在高频下(10,000 Hz),PVD法制备的取向高硅钢铁损值在各个温度点均低于CVD,如图7(d),这与两种样品晶粒尺寸密切相关。在1000 Hz下,采用PVD法制备的取向高硅钢铁损值有两个温度点低于CVD法,即950℃以及1150℃,这说明虽然采用CVD法制备的取向高硅钢Goss织构强度高,但采用PVD制备的取向高硅钢样品于950℃以及1150℃在保证一定强度的Goss织构前提下,平均晶粒尺寸(320 μm~450 μm)远远小于CVD (2~3 mm)样品,因此有更低的铁损值。在1050℃温度下,PVD法制备的取向高硅钢Goss锋锐程度较差,百分含量仅有40%,两者铁损值相近,这说明采用CVD法制备的高硅钢强Goss织构抵消了平均晶粒尺寸大不利的影响。随着测试频率的下降(400 Hz),采用PVD法制备的样品仅有一个温度点低于CVD样品,表明400 Hz条件下,织构对铁损中的影响权重上升。
综上所述,采用PVD法制备取向高硅钢,扩散退火950℃及以上温度均可制备硅含量在6.2%~6.5%的高硅钢,退火1050℃以及1150℃,硅钢基体中的硅含量均匀化程度更高,但综合考虑织构以及磁性能因素,退火950℃,实验钢有益的Goss织构最强,磁性能最佳,可为取向高硅钢的商业化生产提供工艺借鉴。
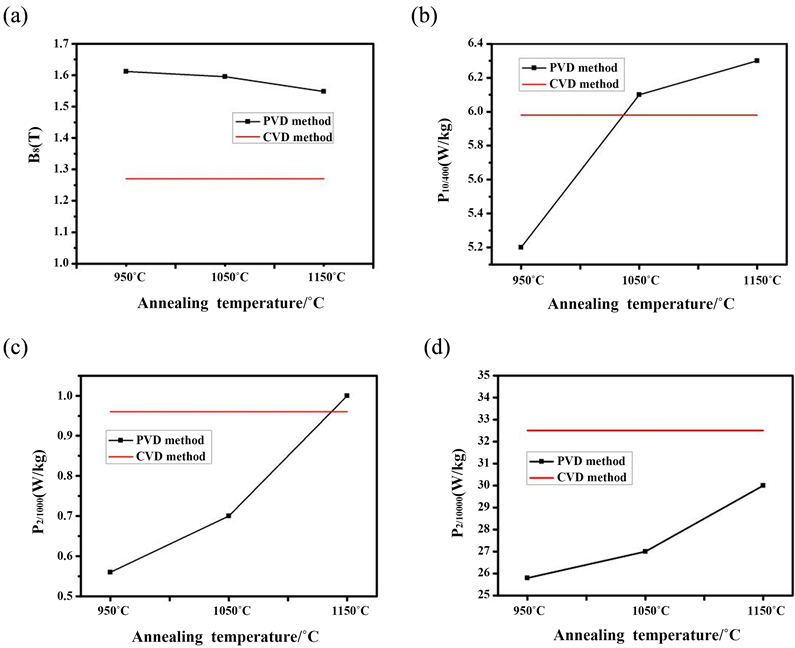
Figure 7. Magnetic performance; (a) Statistics of B8/50 values under different annealing temperature; (b) Statistics of P10/400 values under different annealing temperature; (c) Statistics of P2/1000 values under different annealing temperature; (d) Statistics of P2/10,000 values under different annealing temperature
图7. 磁性能检测结果;(a) 不同退火温度下B8/50数据统计;(b) 不同退火温度下P10/400数据统计;(c) 不同退火温度下P2/1000数据统计;(d) 不同退火温度下P2/10,000数据统计
4. 结论
本研究采用磁控溅射法制高性能取向高硅钢,靶材选用纯Si靶,基体材料选用3% Si取向硅钢冷轧超薄带,对沉积硅膜进行SEM测试分析,并对扩散退火过程中组织与织构演变以及硅元素分布进行了XRD检测以及GDS检测,现得到以下结果:
(1) 扩散退火对超薄带组织及织构的影响较大,随着退火温度的升高,超薄带发生了初次再结晶和二次再结晶,Goss织构的强度先增强后下降,由于升温速率的限制,硅钢薄带在扩散退火过程中并没有发生三次再结晶的现象。
(2) 在不同测试频率下,晶粒尺寸以及有益织构对铁损的影响比重不同,在高频(10,000 Hz)服役条件下,晶粒尺寸对铁损的影响更加重要,而在中频(400 Hz、1000 Hz)服役条件下,需要综合考虑织构与平均晶粒尺寸对铁损的影响。
(3) 综合考虑硅元素均匀化程度以及磁性能,建议采用950℃扩散退火制备高性能超薄取向高硅钢。
基金项目
辽宁省科技厅博士科研启动基金项目(2021-BS-259),辽宁省教育厅面上项目(LJKZ0610)。
NOTES
*通讯作者。