1. 引言
电子束选区熔化(Selective Electron Beam Melting, SEBM)增材制造可以高效率制备复杂结构高温合金部件,被广泛用于航空航天、生物医疗等领域 [1] [2] [3] [4] 。但在电子束选区熔化成形过程中产生的气孔、裂纹、熔化不良等缺陷会导致构件强度下降、疲劳寿命缩短等问题 [5] ,这些问题与成形过程中的温度分布和冷却速率具有直接关系。因此,准确监测和控制电子束选区熔化成形过程中的温度分布和温度变化对于提高制件的质量和性能至关重要。
在电子束选区熔化过程中,电子束在粉末层上进行逐层扫描,选择性熔化粉末材料,因此温度监测需要对电子束扫描面的多点温度分布进行同步采集。同时考虑到电子束扫描速度快,扫描区域的温度变化迅速,为了获取扫描加热过程中某区域的详细温度变化情况,一般需要高速采样(比如10 ms采样一次)。由此可知,为了准确掌握电子束扫描区域的温度分布和变化,需要进行多点同步高速温度采集。
目前常用的温度检测方法主要分为接触式测温和非接触式测温两大类 [6] 。非接触式测温主要基于图像处理技术的辐射测温法,如文献 [7] 基于CCD摄像机实现对焊接温度场的实时监测,文献 [8] 利用红外测温仪设计了一种焊接温度监测系统,但测温时要透过真空室观察窗口,易受到环境因素的影响。而接触式测温系统比较简单、运行相对可靠,且测量精度较高,其中利用热电阻和热电偶测温法是最常用的接触式测温方法。文献 [9] 采用K型热电偶设计了一种四通道的电阻钎焊焊接温度的高速采集装置,文献 [10] 基于K型热电偶设计了一种多路温度采集与控制系统,这些多点测温系统都采用多路、分时采集的方式,即单片机对多个温度点依次进行采样,当采样通道数量很多且采样频率很高时,第一个点与最后一个点的温度采样时间可能会产生一些偏差。
因此,针对电子束选区熔化增材制造扫描区域多点、高速、同步温度采集的需求,采用K型热电偶作为温度传感器,使用PIC18F26K80单片机设计温度采集模块,选用ADM2587E作为收发器并基于Modbus通信协议构建RS-485通信网络,采用LabView开发出具有测温系统控制,温度数据处理、显示与存储的功能的上位机软件,开发出一种9点同步测温系统,可以实现对电子束选区熔化增材制造过程中多点温度的同步测量,满足温度采集需求。
2. 多点同步测温系统设计
2.1. 总体方案设计
针对电子束选区熔化增材制造扫描区域多点、高速、同步温度测量需求,克服现有温度采集仪器多路、分时复用难以实现同步测温的不足,本系统重点从硬件电路和软件控制两个方面进行设计,实现高速、同步测温。首先硬件电路采用模块化设计,每一路温度采集模块都采用独立的单片机进行AD采样,并保证各个温度采集模块的信号传感、滤波处理电路的延时,以及单片机的时钟保持一致,做到信号和采集同步;然后多个温度采集模块采用RS-485串行总线进行组网,各个模块共同接入RS-485网络可以同时接收启动采集命令,确保温度采集的同步启动;最后,上位机程序通过RS-485串行通信网络广播启动温度采集命令,使各个模块同步接收到启动命令并同步开始温度采集,从而实现电子束选区熔化增材制造扫描区域多点、同步温度测量。
根据上述设计思路和电子束选区熔化增材制造多点同步测温的需求,设计了9点同步测温系统,其系统构成框图如图1所示。该系统主要由9路温度采集模块、RS-485串行通信电路、供电电源和上位机软件组成,其中温度采集模块又包括K型热电偶、热电偶调理电路、温度采集电路,以及PT100冷端补偿电路等。
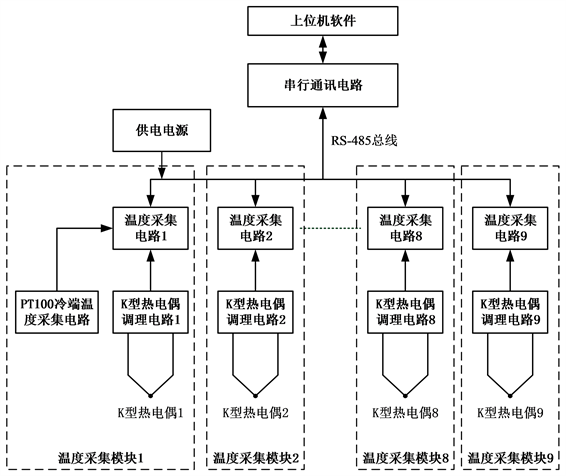
Figure 1. System configuration block diagram
图1. 系统构成框图
多点同步测温系统工作时,将热电偶安装在各个测温点,其输出的电压信号连接热电偶调理电路进行滤波和放大,然后再连接至温度采集电路进行温度转换。9个温度采集模块通过RS-485总线组成串行通信网络,当上位机软件通过RS-485接口广播启动温度采集命令时,各个温度采集模块同步接收启动温度采集命令并立即开始温度采集,然后按照相同的采样间隔时间自动进行采样并将温度数据暂存在单片机的RAM中,达到设定的采样点数后自动停止;在采样结束后,上位机软件通过RS-485总线请求各个温度采集模块依次将采集的数据上传。同时,设置了PT100冷端温度采集电路,根据其测量的冷端环境温度对热电偶测量结果进行补偿,以提高测温精度。
2.2. 热电偶测温原理
对电子束选区熔化成形区域进行温度监测,监测区域的最高温度约为1100℃,因此综合考虑温度范围、价格因素以及适用性,选用K型热电偶(镍铬-镍硅热电偶)作为温度传感器,其灵敏度、响应时间和分度范围都满足要求,且价格便宜。
根据IEC584-1标准,K型热电偶在温度为0℃~1372℃时的热电势E与温度T的关系表达式如下:
(1)
其中,E表示热电势,T表示温度,bi表示相应的系数。通过测得热电偶的热电势E,根据公式1就可以计算出当前的测量温度T。
在实际计算过程中,为减少软件运算计算量,采用最小二乘法原理,并采用自动分段方法 [11] 对K型热电偶的热电势与温度的关系进行分段拟合,得到各个温度区间的计算公式。将各个区间的公式嵌入到软件算法中进行温度计算,可以大大提高软件计算温度的运行效率。冷端温度为0℃时,K型热电偶热电势与温度的分段计算公式如表1所示。
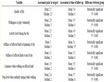
Table 1. Subsection calculation formula of thermoelectric potential and temperature of type K thermocouple
表1. K型热电偶热电势与温度的分段计算公式
2.3. 热电偶调理电路设计
当电子束选区熔化测温区域的温度为1100℃时,K型热电偶输出的热电势约为45.1 mV,该温度信号太小在传输过程中容易受到干扰,同时单片机的A/D采样模块参考电压为5 V,直接采样精度不高。因此,为了提高温度信号采样精度,采用高精度仪用放大器INA114设计了热电偶调理电路,对温度信号滤波和放大,其放大倍数约100倍。考虑到单级放大倍数过大,避免信号失真,采用两个INA114组成两级放大电路,如图2所示。
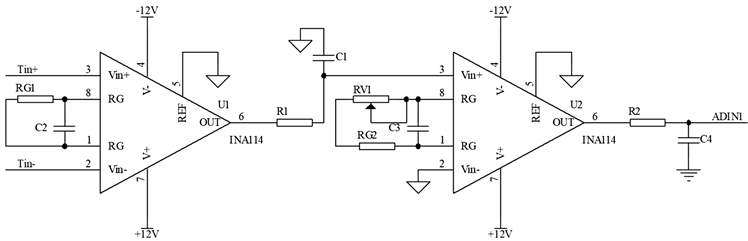
Figure 2. Thermocouple conditioning circuit
图2. 热电偶调理电路
在图3中,通过外部电阻
来设置INA114放大器的增益,第一级放大器的增益为:
(2)
第二级放大器的增益为:
(3)
两级放大电路的增益相乘可以得到热电偶热电势(Tin+ − Tin−)的增益G:
(4)
2.4. 温度补偿电路
热电偶工作时,其输出信号是工作端与冷端的热电势差,一般地,热电偶分度表中的冷端温度是参考0℃;然而,电子束选区熔化增材制造在真空室中进行,经过长时间加工真空室的温度可能上升到一百多甚至几百摄氏度,此时如果仍然采用表1分段公式来计算温度,则会由于冷端温度变化幅度大而导致测温不准确。因此,为了提高温度的测量精度采用PT100设计了冷端温度补偿电路,用来测量真空室的温度,并作为冷端补偿温度,以消除热电偶测量中由于冷端温度变化引起的误差,从而获得更精确的目标点温度数据。PT100冷端温度补偿电路如图3所示。
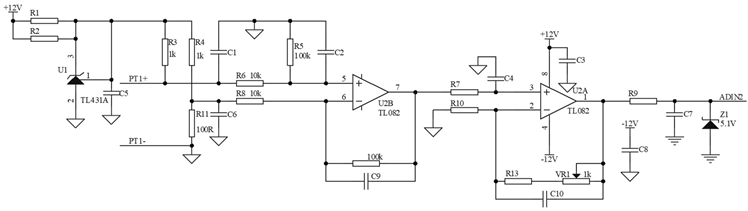
Figure 3. PT100 cold junction temperature compensation circuit
图3. PT100冷端温度补偿电路
在图4中,将PT100热电阻接入电路中,利用TL082放大其电压信号,设计跟随电路,将放大后的信号连接到PIC单片机的A/D输入端,PIC单片机会在温度采集结束后,将采集到的环境温度数据发送给上位机。上位机中计算得到PT100热电阻在温度T0、冷端温度0℃时的热电势
,K型热电偶在温度T、冷端温度为T0时的热电势
,则K型热电偶在温度T、冷端温度0℃时的热电势
为:
(5)
2.5. 温度采集电路
温度采集电路是电子束选区熔化多点同步测温系统的关键,主要功能是将热电偶调理后的温度信号转换为数字信号,并将这些数据传输给上位机进行处理和分析。这些功能主要由单片机实现,因此单片机是温度采集电路的核心,但目前通用的单片机同一时刻大都只允许一个通道进行A/D转换,通过单个单片机电路很难实现多路温度信号的同步采集。因此,为了实现同步温度采集的要求,采用9路温度采集模块并行工作的方案,每路温度采集模块都有独立的单片机。各单片机控制其A/D转换模块同步进行温度采集并将数据存储到单片机数据RAM中,温度采样结束后再将数据返回给上位机。
以电子束选区熔化温度采样如下要求为例进行计算,当采样持续时间10 s、采样间隔时间为10 ms时,总的采样点数为1 k个,如果选用12位A/D转换器,那么每个温度数据占用2个字节,总的存储空间至少为2 kB,则所选取的单片机的RAM容量至少要大于2 kB。因此,选择PIC18F26K80作为温度采集电路的单片机,其数据RAM容量为3.6 kB,A/D转换器为12位,最多可以记录约1.8 k个温度数据,能够满足上述温度采集的要求。为确保单片机数据不溢出,系统设定采样点数最大为1.5 k个,在采样间隔时间为10 ms的情况下,系统能够持续记录长达15秒的温度采样数据。以温度采集模块1为例,温度采集电路如图4所示。
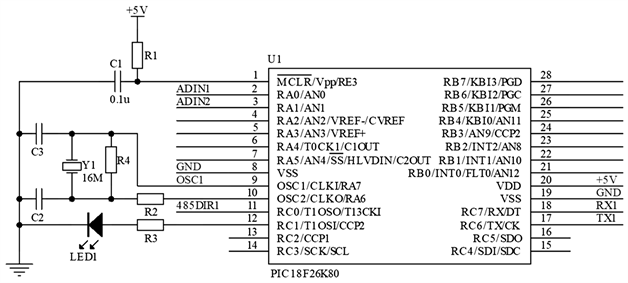
Figure 4. Temperature acquisition circuit
图4. 温度采集电路
单片机的外部晶振为16 MHz,RA0引脚连接K型热电偶调理电路,RA1引脚连接PT100冷端温度采集电路,其中冷端温度采集不需要高频率且只需要一路。
2.6. 串行通信电路
在电子束选区熔化多点同步测温系统中,串行通信电路是连接多个温度采集模块,实现命令和数据传输的通道。上位机需要向多个温度采集模块同时发送开始采集命令,实现一对多的命令广播。同时还需要实现上位机与各个温度采集模块之间的一对一的主从应答模式的命令和数据传输。RS-485接口采用差分传输的方式,其抗干扰能力强,传输距离远,级联能力强 [12] 。在多点同步测温系统中,能够保证命令和数据的准确传递,特别是当上位机需要将开始采集命令传递给多个温度采集模块时,RS-485接口允许一对多的广播通信,从而确保命令的同步执行。因此,采用RS-485构成半双工的多点同步测温系统的通信网络,选择ADM2587E作为温度采集模块RS-485收发器,其构成如图5所示。
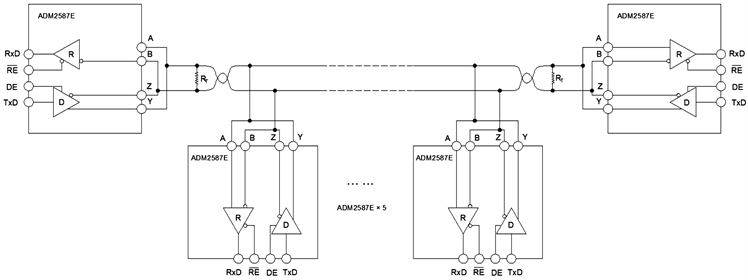
Figure 5. Temperature acquisition circuit
图5. RS-485半双工通信网络
在图5中,采用RS-485总线构成上位机与9路温度采集模块的串行通信网络,通信协议采用Modbus 协议,上位机发送指令时采用单播模式和广播模式。当发送开始采集命令时,上位机采用广播模式发送命令给各个温度采集模块,9路温度采集模块同时接收到命令并开始执行命令,不对广播消息做出应答;发送获取数据获取命令时,采用单播模式,上位机请求指定的温度采集模块,指定的温度采集模块接收到指令后将数据回传给上位机。
基于上述硬件电路设计,研制的多点同步测温系统实物如图6所示。其中,电源接口连接到+24 V电源,通讯接口连接至上位机串行通信接口,T1~T9接口分别连接9个K型热电偶,PT1接口连接PT100热电阻作为冷端温度补偿。
3. 软件设计
为实现上位机与各个温度采集模块之间的温度采集、数据传输,以及温度数据的处理和存储等,设计了多点同步测温软件,主要包括温度采集模块程序、上位机软件。
3.1. 温度采集模块程序
多点同步测温系统的温度采集模块设计主要包括单片机主程序、串口通信中断子程序、T1定时器中断采样服务子程序三部分。其中单片机主程序主要完成单片机的初始化、定时器T1的配置、与A/D采样有关的寄存器配置以及串口通信的配置。串口通信中断子程序负责接收上位机的命令,并对接收到的命令进行判断,并执行相应的操作。T1定时器中断服务子程序负责开始采集指令发出后,完成定时同步采样,采集到指定的采样点数后停止采样。程序流程图如图7、图8、图9所示。

Figure 7. SCM main program flow chart
图7. 单片机主程序流程图
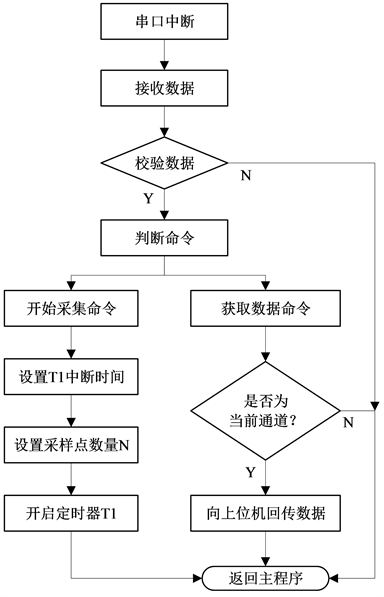
Figure 8. Serial communication interrupt subroutine
图8. 串口通信中断子程序
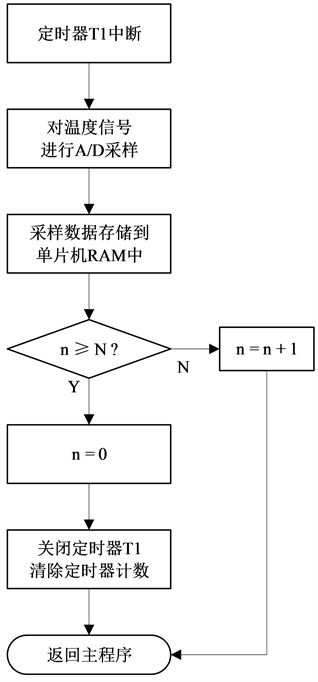
Figure 9. T1 timer interrupt sampling service subroutine
图9. T1定时器中断采样服务子程序
3.2. 上位机软件
3.2.1. 上位机软件界面
采用LabVIEW软件,使用图形化编辑语言G设计上位机程序,实现多点温度采集模块的控制、温度数据处理、存储及统计等功能。所设计的上位机软件操作界面如图10所示。
上位机软件界面分为上下两个部分,其中上半部分为控制部分,左侧为采集通道选择,可以选择1到9个温度采集模块,每个模块最多可以采集1500个温度点,并且各个温度采集模块为同步采集;中间部分为温度数据上传指示,温度采集结束后,当某个模块的温度数据上传成功后,相应的指示灯会点亮;右侧为温度采集控制部分,可以设置通信串口、A/D采样间隔和采样点数量,发送开始采集、获取数据指令,设置保存路径并保存数据,同时用户通过反馈进度条可以看到当前采样进度。软件下半部分为温度采集数据显示部分,左侧可显示各个采集模块本次温度采集的平均温度,右侧可以将采集到的温度数据曲线拟合并显示。
3.2.2. 多点同步测温工作流程
电子束扫描的速度很快,时间较短,若单片机实时将A/D转换的结果发送给上位机,由于总线上9个单片机不能同时传输数据,将导致上位机读取9块单片机的数据不同步。因此,单片机先存储A/D转换的结果,采样结束后,上位机一次性读取所有结果。
使用本系统进行测温时,首先在上位机软件中设置工作参数,上位机中发送开始采集命令并通过RS-485总线同步传输给9路温度采集模块单片机,9路单片机接收到命令后同时开始采样,并将A/D采样转换后的结果先存储在单片机中。温度采集结束后,上位机向9路单片机依次请求数据,9路单片机依次将采样数据回传给上位机,工作流程示意图如图11所示。
当上位机通过RS-485总线广播开始采集命令后,9路温度采集模块接收命令后立即启动温度采集指令,从而实现多个模块的同步温度采集。由此可知,各个模块同步采集的误差主要由串口接收偏差时间和单片机指令执行偏差时间组成。其中,ADM2587E接收串行命令并进行转换,查阅手册可知其接收偏差时间最大为
。由于9路单片机采用同样的时钟,且每个单片机收到命令后执行相同的程序,因此所耗费的时间也相同;每个单片机采用相同频率的晶振产生时钟,考虑到器件的差异性其时钟周期可能会稍有差异,但是最大的指令执行偏差时间不会超过单个指令周期
。故9路单片机同步采样时间最大误差时间t为
与
的和,即:
(6)
由此可知,当采样周期为10 ms时,同步采样的最大误差时间小于采样周期的万分之一,因此可以认为9个通道的温度采集是同步的。
3.2.3. 温度数据处理与存储
上位机软件中获取到的数据为单片机A/D转换后的结果,并非直接的温度数据,需要对数据进行处理。测温点温度T在相对于冷端温度T0时的热电势
的计算公式为:
(7)
式中,
为单片机采样热电偶调理电路获得的数据,
为热电偶信号经过调理电路后获得的增益。同样的,冷端温度T0在相对于0℃时的热电势
计算公式为:
(8)
式中,
为单片机采样温度补偿电路获得的数据,
为PT100热电阻经过温度补偿电路后获得的增益。
将(7) (8)带入到式(5)即可求得K型热电偶在温度T、冷端温度0℃时的热电势
,再将求解后的结果带入到表1中的分段计算公式,即可求出测温点的温度。
将上述计算过程集成到上位机软件中,在上位机软件中进行温度计算,并通过软件界面将数据可视化显示。同时,在上位机软件界面中可以选择数据保存路径,并将数据存储至一个xls表格文件中。数据保存的xls表格文件包含9列,每一行对应同一时刻9个测温点的温度值,便于后续数据的分析和处理。
4. 系统测试与分析
为确保温度测量的准确性和可靠性,实验开始前先对各个温度测量模块进行标定,采用冰水混合物标定温度传感器的0℃标定点;将标准黑体炉设定为1000℃,标定传感器的高温点。
设计一块150 mm × 150 mm的标定板,在其底部加工9个热电偶安装孔,然后将9支K型热电偶安装至工件底部的安装孔,使热电偶的测量端紧密的贴合9个温度测量点,其安装示意图如图12所示。
采用电子束在150 mm × 100 mm的标定板上高速扫描出100 mm × 100 mm的区域,当中心点(第5点)的温度达到799℃时,记录下多点同步测温系统测量到的9个温度点温度值,如图13所示。
从图中可知,位于扫描区域中心的第5点温度最高,达到了799℃;位于边界中心点的第2、4、6、8点的温度相近且较高,范围在768℃到773℃之间;而位于边界四个角的1、3、7、9点的温度最低,范围在740℃到748℃。实验所得数据与通用单点测温仪所测得数据相符,可以实现电子束选区熔化的多点温度实时测量。
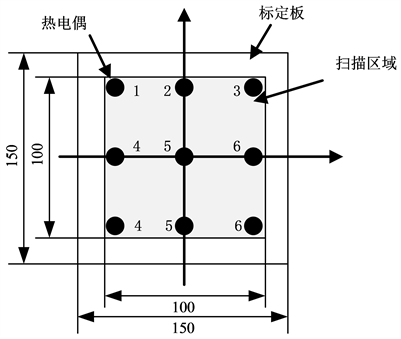
Figure 12. Schematic diagram of installation of thermocouple temperature measurement point (mm)
图12. 热电偶测温点安装示意图(mm)
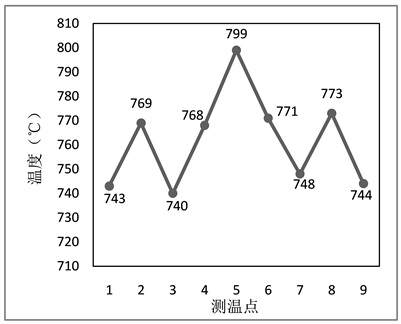
Figure 13. The temperature values of 9 points when the central point is 799˚C
图13. 中心点为799℃时9个点的温度值
5. 结语
针对电子束选区熔化增材制造过程中多点、高速、同步采集的需求,设计了一种9点同步测温系统。
(1) 实现了电子束选区熔化增材制造多点同步测温,能够同步采集9个测温点的数据,测温点采样间隔时间最快为1 ms,最大可连续采集1500个点,能够满足电子束选区熔化增材制造过程中多点、高速、同步的温度采集要求,为电子束选区熔化增材制造温度场监测和调控提供依据。
(2) 采用温度采集电路模块化设计、独立单片机A/D转换等手段提供了多点温度同步采集的硬件基础,采用RS-485组网和上位机广播命令方式实现了多个温度采集模块软件同步启动,在此基础上实现了多点温度同步采集,同步采集误差不高于0.28 μs。
(3) 温度采集模块采用模块化的设计方法,根据不同的应用场景、温度测量路数和测量范围可以灵活配置温度采集模块的数量,并选择不同类型的温度传感器,同时模块化的设计还具有很好的灵活性和扩展性,为系统应用的二次开发提供了便利。
基金项目
国家自然科学基金项目(51975036),广东省重点研发计划项目(2018B090904004)。
参考文献