1. 引言
某气井采气管线气液混输,输送介质包括未经处理的原料气和气田水,日输水量50~60方,气田水为弱酸性,pH值为6~8,矿化度120 g/L,Ca2+浓度4000~4500 mg/L,
浓度20,000~70,000 mg/L,水型为氯化钙水型。管线为L360QS无缝钢管,管线腐蚀穿孔形貌如图1、图2所示,发生失效的部位为底部焊缝和管材基体,均位于6点方向。
针对采气管线失效,目前最常采用的方式为对失效样品进行理化检测等,以明确失效原因并制定针对性预防措施。本次对失效管段进行了一系列分析及检验,以找出管线腐蚀穿孔的原因,防止此类事故再次发生 [1] 。
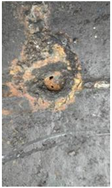
Figure 1. Macroscopic morphology of perforation in weld
图1. 焊缝处穿孔宏观形貌图

Figure 2. Macroscopic topography of pipe body cavity
图2. 管体坑洞宏观形貌图
2. 样品制备
2.1. 金相样品和扫描电镜样品
用锯弓用手工锯断取样,在此附近取样,样品分成2类:腐蚀物表面形貌样品和室温冷镶嵌样品。为了避免加热温度对腐蚀产物的影响,采用冷镶嵌。用金相砂纸磨样,金刚石抛光膏进行机械抛光,然后进行金相和扫描电镜分析。最后采用2%硝酸酒精腐蚀抛光面金相组织分析。
2.2. XRD样品
在管段腐蚀情况较多的位置附近刮取粉末样,用研磨器研磨后过筛进行XRD物相分析。
2.3. XPS样品
取腐蚀坑洞深度较深的位置用锯弓手工锯断取样,样品大小为5 × 5 × 3 mm。
2.4. 化学成分样品
将锯下的管段外侧未受腐蚀的表面截取30 mm × 30 mm规格样品,采用直读光谱仪进行化学成分测试。
样品编号及详细信息如表1所示。
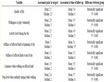
Table 1. Experimental sampling information
表1. 实验取样信息
3. 理化检测
3.1. 化学成分分析
使用直读光谱仪对取样管段进行化学成分分析,结果如表2所示。结果表明:3个取样位置即管体、焊缝附近以及焊缝的化学成分均小于标准GB/T9711.3所要求值,满足该标准,而且P的含量远低于标准,C的含量也低于标准,材质比较好。
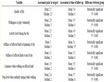
Table 2. Chemical composition analysis of corroded pipe
表2. 腐蚀管线化学成分分析结果
3.2. XRD分析
在管体腐蚀坑表面(编号1-5#)、焊缝穿孔位置附近(编号3-7#)刮取粉末,经过干燥并用玛瑙研磨器研磨后过筛制取粉末进行XRD分析,结果如图3、图4所示。结果表明:二者均含有FeS、Fe2O3、C,焊缝穿孔位置附近还含有部分FeCO3和CaCO3。
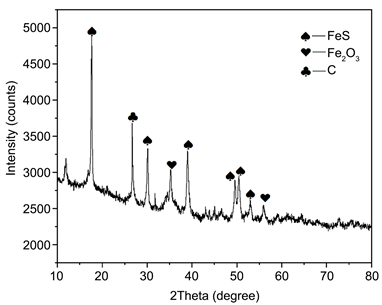
Figure 3. XRD results of pitting pit surface (1-5#)
图3. 管体点蚀坑表面(1-5#) XRD结果
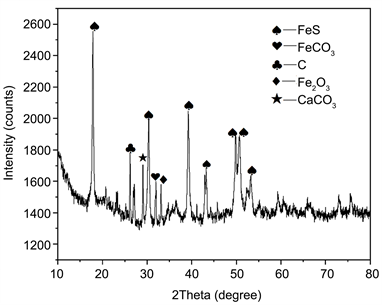
Figure 4. XRD results near the perforation of the weld (3-7#)
图4. 焊缝穿孔位置附近(3-7#) XRD结果
3.3. XPS分析
在管体腐蚀坑附近(编号1-6#)、焊缝穿孔位置两侧(编号3-8#、3-9#)各取一个5 mm × 5 mm × 3 mm的块状样品表面进行XPS分析,其结果如图5、图6、图7所示。结果表明:这些样品表面的主要成分均为Fe2O3、FeS、FeCO3,与XRD结果相符;同时含有少量FeCl3、S、Fe2(SO4)3,这可能是管道介质中的H2S和CO2引起腐蚀的结果。
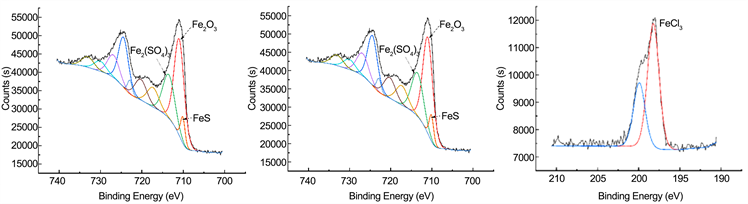
Figure 5. Tube body corrosion pit near (1-6#) XPS results
图5. 管体腐蚀坑附近(1-6#) XPS结果
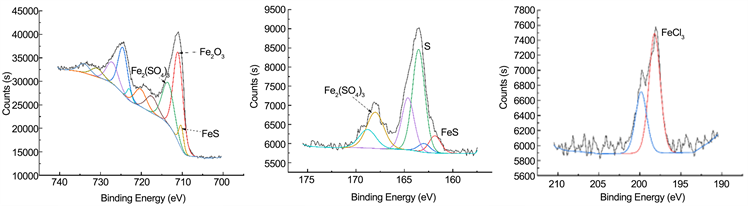
Figure 6. Weld hole location near (3-8#) XPS results
图6. 焊缝穿孔位置附近(3-8#) XPS结果
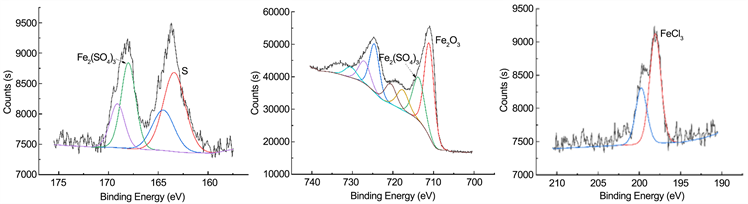
Figure 7. Weld hole location near (3-9#) XPS results
图7. 焊缝穿孔位置附近(3-9#) XPS结果
3.4. 扫描电镜分析
焊缝穿孔附近坑洞中腐蚀层表面有片状、不规则形状和晶体状,不均匀腐蚀严重。EDS点扫检测到不规则的腐蚀物含有C、O、Cl和S,面扫发现晶体状主要含硫,结合其形貌可以推测为单质S。检测到穿孔处腐蚀产物有很高的S (3.63%)和Cl (22.25%)。这说明Cl造成的点蚀非常严重。而管体坑洞处含量低,低于焊缝坑洞附近的含量,分别是Cl为3.04%,S为1.65%。这也说明在焊缝处容易导致点蚀,点蚀坑洞发生后大量
富集,进一步加剧不均匀腐蚀。
3.5. 冶金质量分析
对焊缝处抛光观察夹杂物,夹杂物都是点状硅酸盐类,焊缝中夹杂物尺寸约为30 μm,偏大,说明焊接过程中排渣不是很好。对基体中夹杂物进行分析发现夹杂物也是球状硅酸盐类,但是偏聚严重,一些地方尺寸较小10 μm左右,一些地方35 μm左右,说明冶金质量不是太好,尽管S、P含量低,除渣效果不理想。
3.6. 金相组织分析
采用硝酸酒精对抛光后样品腐刻,焊缝组织为针状铁素体 + 晶界铁素体 + 魏氏组织,热影响区组织为铁素体 + 针状铁素体,基体为珠光体 + 铁素体。这3个区域的组织都属于正常组织。
4. 分析
对于湿气管线而言,内腐蚀是导致管线失效的主要形式 [2] ,而焊缝是整条管线的薄弱环节,由于焊接操作和自身性能特点等原因,在服役过程常常会先于管体发生腐蚀破坏,影响生产 [3] [4] 。
基于以上分析及检测结果,该管线腐蚀穿孔原因总结为以下几个方面。
(1) 焊缝穿孔位置和管体坑洞位置为管线6点方向,说明此处聚集较多气田水,为腐蚀发生提供了较好的介质环境。水中
含量高达20,000~70,000 mg/L,pH4~6属于弱酸性,同时伴有酸性H2S、CO2气体,腐蚀环境较为苛刻。高的
在6点位导致了点蚀,而焊缝组织不如基体组织耐蚀性好,所以在焊缝处优先发生点蚀,由于6点位沉积气田水,这加剧了腐蚀速度。
(2) EDS检测到穿孔处腐蚀产物有很高的S (3.63%)和Cl (22.25%)。这说明Cl造成的点蚀非常严重。而管体坑洞处含量低,低于焊缝坑洞附近的含量,分别是Cl为3.04%,S为1.65%。这也说明在焊缝处容易导致点蚀,点蚀坑洞发生后大量
富集,进一步加剧不均匀腐蚀。
(3) 管体冶金质量不是很好,夹杂物为点状(球状),但是不均匀,有的尺寸达到35 μm左右。在6点位处如果有聚集的大夹杂物,会产生
引起的点蚀。
总结说来,6点位的高含量的
气田水沉积导致点蚀,最后引起焊缝处穿孔。基体腐蚀坑洞是因为夹杂物聚集+高含量的
气田水沉积导致点蚀最后失效。
5. 结论与建议
5.1. 结论
(1) 该管线焊缝和管体基体组织正常,管体、焊缝附近以及焊缝的化学成分均小于标准GB/T9711.3对L360QS材质的要求值,满足该标准,而且P的含量远低于标准,C的含量也低于标准,管体材质比较好,焊接所用的焊条(丝)选择合理,但冶金质量不是很好,夹杂物为点状(球状),但是不均匀,有的尺寸达到35 μm左右。在6点位处如果有聚集的大夹杂物,会产生
引起的点蚀。
(2) 6点位的高含量的
气田水沉积导致点蚀,最后引起焊缝处穿孔。基体腐蚀坑洞是因为夹杂物聚集 + 高含量的
气田水沉积导致点蚀最后失效。
5.2. 建议
针对该类似采气工艺管线,一是控制管线气田水沉积;二是完善管线缓蚀剂防腐工艺,如:增加清管预膜装置,定期开展缓蚀剂预膜;或者使用具有优良耐磨性能的内腐蚀控制技术 [5] ,如:内涂层管线或内衬陶瓷等。