1. 引言
印制线路板(PCB)是将导线嵌入绝缘材料制成设计线路及电子元件的印制板,是电子元器件的支撑体,是电子元器件电气连接的载体 [1] [2] 。随着5G技术的推出和电子技术的不断发展,国家对高端芯片的研发和制备需求不断增加 [3] [4] 。由于铜具有优良的导电性并且成本相对较低,因此PCB元件常通过铜迹线连接,然而没有保护涂层的非嵌入铜线很容易发生氧化,影响电子器件的功能完整性和电子设备的可靠性 [5] ,因此需要对PCB的铜线路进行表面处理。中高端技术需求的PCB表面处理技术主要有化学镀镍浸金(ENIG)和化学镀镍钯浸金(ENEPIG),化学镀金层平整度高,具有良好的抗氧化性和可焊性等优良性能 [6] ,因而被广泛关注和研究。这两种技术虽可满足PCB使用的性能要求,但仍存在一些缺陷。李晓倩 [7] 等人对ENIG的黑焊盘现象进行了分析,ENIG的工艺过程比较复杂,如果工艺参数控制不当,焊接后易出现“黑盘(Black Pad)”缺陷,使焊点出现可靠性问题。贾莉萍 [8] 等人对ENEPIG表面处理常见品质缺陷进行了研究,结果表明ENEPIG工艺由于生产制成能力不稳定,所以仍无法完全杜绝“黑盘”发生,还会出现渗镀、漏镀、金面粗糙和金面异色等问题。为避免这些问题出现,PCB生产厂家一般会将键合区域的镀金层厚度做到1 μm以上 [9] ,极大增加了生产成本。同时由于镀金常用氰化物体系 [10] ,但氰化物属于剧毒性物质,氰离子毒性强大,废液难以处理不但污染环境,还会侵蚀用于绘制电路图案的光致抗蚀剂膜 [11] 。
基于上述问题,本文对PCB板铜线路化学镀技术进行改良和创新,优化镀层性能,提高镀层耐蚀性,扩大PCB板铜线路的应用。根据原子氢析出理论 [12] ,化学镀镍磷的反应机理总共分为四步:
(1)
(2)
(3)
(4)
本实验采用绿色环保化学镀新工艺,研究了化学镀镍磷体系,以不同镀液pH值、添加剂浓度和施镀温度得到的镀层在3.5% NaCl溶液中的电化学分析结果为衡量指标,对所得镀层在NaCl溶液中的塔菲尔曲线和电化学阻抗谱进行分析,研究了其耐蚀性。对在最优工艺参数条件下得到的镀层的微观结构和元素组成进行了表征与分析。将上述工艺应用于PCB板铜电路制备镍磷镀层,并对印制电路基板进行了中性盐雾测试和可焊性测试,从多方面了解本工艺在PCB铜导线表面处理的应用潜力。
2. 实验
2.1. 主要试剂及仪器
T2紫铜棒,纯度 > 99.0%;NiSO4·6H2O,含量 ≥ 98.5%;NaH2PO2·H2O,含量 ≥ 98.0%;NaOH,含量 ≥ 96.0%、Na2CO3,含量 ≥ 99.8%、Na3PO4·12H2O,含量 ≥ 98.0%;Na2SiO3,含量 ≥ 95.0%;PdSO4,含量 ≥ 99.0%;NaCl,含量 ≥ 99.5%;NH3·H2O,含量25.0%~28.0%、H2SO4,含量95.0%~98.0%、H2O2,含量 ≥ 30.0%,以上试剂均为分析纯AR。复合添加剂,分析纯AR。溶液均采用去离子水配制。
P-1型单盘金相抛光机,转速700 r/min;数显恒温磁力搅拌水浴锅,温度范围室温±5℃~100℃,转速0~2500 r/min;pH828型pH计,量程0.00~14.00 pH;WGZ型精密鼓风干燥箱,温度范围室温±10℃~250℃。
2.2. 化学镀工艺流程
以紫铜为基体,化学镀镍磷的工艺流程为:砂纸打磨→除油→去离子水洗→微蚀→去离子水洗→酸洗→去离子水洗→活化→去离子水洗→化学镀→去离子水洗→干燥。
初始化学镀镍的配方和工艺条件为:NiSO4·6H2O 30 g/L,NaH2PO2·H2O 20 g/L,复合添加剂70 g/L,pH = 6.0,温度75℃,时间60 min。
2.3. 镀层形貌表征及性能测试
2.3.1. 电化学分析
使用科思特CS310M电化学工作站测试试样在3.5% NaCl溶液中的动电位极化曲线(PDP)和电化学阻抗谱(EIS),采用电化学工作站内置软件对数据进行拟合。测试采用三电极体系,其中辅助电极为铂电极,参比电极为饱和甘汞电极(SCE),工作电极为化学镀镍试样(暴露面积1.13 cm2)。
2.3.2. 形貌表征
使用德国蔡司(ZEISS) GeminiSEM 300型场发射扫描电镜(FESEM)及其附带的能谱仪(EDS,型号牛津Oxford Aztec X-max80)分析镀层的表面微观形貌和元素组成。
2.3.3. 物相组成分析
使用日本岛津XRD-6100型X射线衍射仪分析镀层的相结构。
2.3.4. 表面化学组分分析
使用美国赛默飞ESCALAB XI+型X射线光电子能谱仪对镀层表面化学组分进行分析。
2.3.5. 印制电路基板中性盐雾测试
参照GB/T 10125-2021《人造气氛腐蚀试验盐雾试验》标准,使用LYW-015型盐雾腐蚀试验箱进行中性盐雾腐蚀实验。
2.3.6. 印制电路基板可焊性测试
参照IPC J-STD-003B-C1《印制电路板的可焊性测试浮焊测试》标准,使用FX320型无铅纯铁锡炉对镀层进行可焊性测试。
3. 结果与讨论
3.1. 化学镀镍工艺参数优化
3.1.1. 镀液pH值优化
镀液pH值会影响镀层中磷元素的含量,通常在酸性镀液条件下得到的高磷镀层具有良好的耐腐蚀性。研究了镀液pH值分别为3.0、4.0、5.0时得到镍磷镀层的耐腐蚀性。图1(a)为不同镀液pH值下得到的镍磷镀层在3.5% NaCl溶液中的极化曲线。腐蚀电位(Ecorr)、腐蚀电流密度(icorr)、阳极分支斜率(βa)与阴极分支斜率(βc)数据列于表1中。由表中数据可以看出,铜基体的icorr = 6.466 μA/cm2,不同镀液pH条件下得到的镍磷镀层试样的腐蚀电流密度均明显小于铜基体,说明镍磷镀层的耐蚀性均优于铜基体。其中当镀液pH为4.0时得到的镀层腐蚀电流密度最小,icorr = 1.239 μA/cm2,表现出最好的耐腐蚀性。

Figure 1. (a) Polarization curve, (b) Nyquist diagram and (c) Bode diagram of coatings at different pH
图1. 不同pH下镀层的(a) 极化曲线,(b) Nyquist图和(c) Bode图
根据原子氢析出理论提出的反应机理,并结合实验结果分析可知,当镀液pH值较低时,镀液中H+浓度过高,会抑制化学镀还原反应的正向进行;镀液pH值增加虽可以促进反应的进行,但同时又会导致镀液稳定性下降,影响镍磷镀层的微观形貌,进而使镀层耐腐蚀性下降。
为了进一步研究镍磷镀层的耐腐蚀性,测试了不同pH值下镀层腐蚀过程中的交流阻抗谱,获得了样品的Nyquist图(图1(b))和Bode图(图1(c))。通常容抗弧直径、低频阻抗模值和相位角越大表明镀层耐蚀性越好。由图1(b)可知,镀液pH = 4.0时得到的镀层容抗弧直径最大。由图1(c)可知,此时镀层低频阻抗模值最大,相位角更接近90˚,且较高相位角对应的频率范围更宽,说明此条件下得到的镀层耐蚀性更优异。
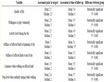
Table 1. Coating corrosion data of coatings at different pH (from Figure 1(a))
表1. 不同pH下镀层腐蚀数据(来自图1(a))
注:βa、βc分别为Tafel曲线阳极分支和阴极分支的斜率。
阻抗测试结果可用如图2的软件内嵌等效电路图进行拟合,其中Rs为工作电极和参比电极之间的溶液电阻,Rct1为镀镍层的反应电阻,Rct2为铜基体的反应电阻,利用恒相电位元件(CPE)代替纯电容元件,CPE1对应镀镍层,CPE2对应铜基体,采用Rct1 + Rct2来表征镀镍层的耐蚀性能。后续工艺参数优化实验的阻抗测试结果均采用图2等效电路图进行拟合。表2是采用该等效电路计算所得的各参数的拟合值,从表中数据可以看出,当镀液pH = 4.0时,Rct1 + Rct2的值最大,为29.6 kΩ·cm2,说明此条件下镀层的耐腐蚀性最好,此结果与Tafel极化曲线拟合数据一致。结合极化曲线和电化学阻抗谱数据,在镀液pH = 4.0时所得到的镀层具有最好的耐腐蚀性能,因此选择pH = 4.0进行后续优化实验。
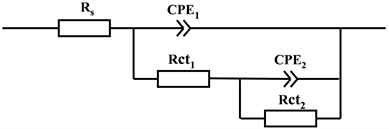
Figure 2. EIS data fitting equivalent circuit model
图2. EIS数据拟合等效电路模型
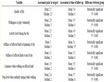
Table 2. Equivalent circuit fitting data of coatings at different pH
表2. 不同pH镀层的等效电路拟合数据
3.1.2. 复合添加剂浓度优化
添加剂不但可以抑制亚磷酸镍沉淀的产生,还可以起到缓冲剂的作用,影响镀液稳定性和镀层表面质量。以10 g/L为浓度梯度,研究了复合添加剂浓度30 g/L~70 g/L时得到镍磷镀层的耐腐蚀性。图3(a)为不同复合添加剂浓度下得到镍磷镀层的极化曲线,当添加浓度为30 g/L、40 g/L、50 g/L、60 g/L、70 g/L时,镀层的icorr分别为1.134 μA/cm2、1.505 μA/cm2、1.383 μA/cm2、1.845 μA/cm2、1.239 μA/cm2,由此可以看出,不同复合添加剂浓度条件下得到的镍磷镀层试样的腐蚀电流密度均明显小于铜基体,当添加剂浓度30 g/L时得到的镀层腐蚀电流密度最小,表现出最好的耐腐蚀性。
实验结果表明,复合添加剂在化学镀液中可同时作为络合剂和缓冲剂,因此可以起到稳定镀液和维持镀液pH值稳定的作用。当添加剂浓度在30 g/L时化学镀液最为稳定,因此得到的镍磷镀层表面更为平整致密、缺陷更少。当添加剂浓度过高时反而会降低镀层的耐腐蚀性,并且会增加镀液成本,造成原料浪费。
由图3(b) Nyquist图可以看出添加剂浓度为30 g/L时镀层容抗弧直径最大。从图3(c) Bode图可以看出,此浓度下得到的镀层低频阻抗模值最大,且相位角更接近90˚,较高相位角对应的频率范围更宽,说明此条件下得到的镀层耐蚀性更优异。
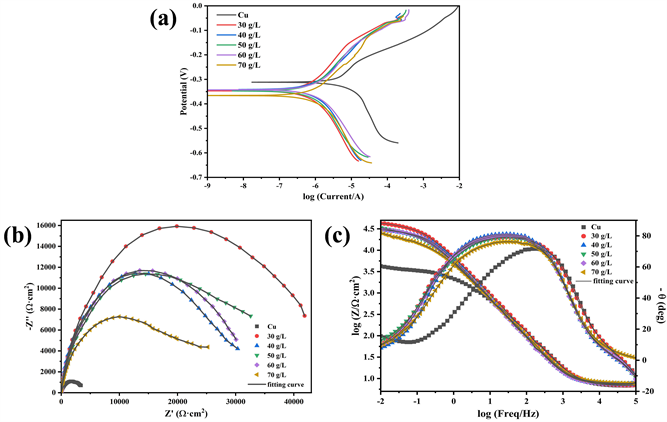
Figure 3. (a) Polarization curve, (b) Nyquist diagram and (c) Bode diagram of coatings with different concentrations of composite complexing agents
图3. 不同复合添加剂浓度下镀层的(a) 极化曲线,(b) Nyquist图和(c) Bode图
采用等效电路计算所得的各参数的拟合值,当添加浓度为30 g/L、40 g/L、50 g/L、60 g/L、70 g/L时,镀层Rct1 + Rct2的值分别为53.9 kΩ·cm2、39.5 kΩ·cm2、45.6 kΩ·cm2、37.2 kΩ·cm2、29.6 kΩ·cm2,由此看出当复合添加剂浓度30 g/L时Rct1 + Rct2的值最大,说明此条件下镀层的耐腐蚀性最好。此结果与Tafel极化曲线拟合数据一致。结合极化曲线和电化学阻抗谱数据,说明在复合添加剂浓度30 g/L时所得到的镀层具有最好的耐腐蚀性能,因此选择复合添加剂浓度30 g/L进行后续优化实验。
3.1.3. 施镀温度优化
温度为化学镀过程提供必要的活化能,也会影响反应速率的快慢,进而影响表面形貌和性能等。研究了施镀温度分别为65℃、75℃、85℃时得到镍磷镀层的耐腐蚀性。图4(a)为不同施镀温度下得到镍磷镀层的极化曲线,具体数据列于表3中。从表中数据可以看出,当施镀温度为65℃时得到的镀层腐蚀电流密度最小,icorr = 0.982 μA/cm2,表现出最好的耐腐蚀性。
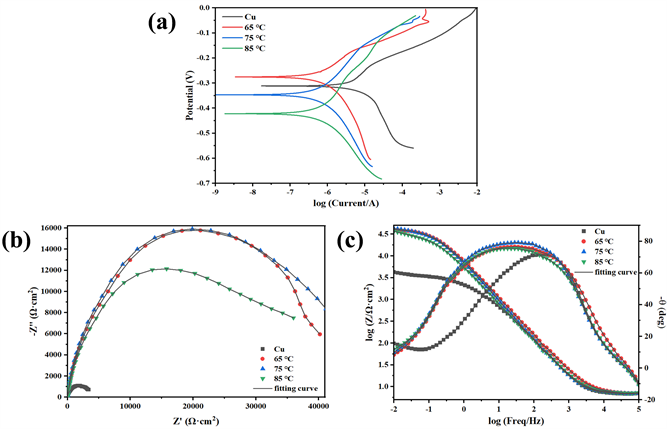
Figure 4. (a) Polarization curve, (b) Nyquist diagram and (c) Bode diagram of coatings with different temperature
图4. 不同施镀温度下镀层的(a) 极化曲线,(b) Nyquist图和(c) Bode图
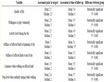
Table 3. Corrosion data of coatings at different plating temperatures (from Figure 4(a))
表3. 不同施镀温度下镀层腐蚀数据(来自图4(a))
实验结果表明,温度影响镀层的沉积速率和镀液稳定性,进而影响镀层表面形貌和耐腐蚀性能。随着温度的提高,镀层沉积速率加快但是镀液的稳定性逐渐降低,导致得到的镀层致密性降低,表面缺陷增多,镀层均匀性下降,并且可能出现镀层表面局部团聚等现象发生,导致镀层的性能降低。
由图4(b) Nyquist图可以看出,在施镀温度为65℃和75℃时镀层容抗弧直径相差不大,但均优于85℃时的镀层。从图4(c) Bode图可以看出,65℃和75℃下得到的镀层低频阻抗模值基本相同,但75℃下镀层的相位角更接近90˚。
采用等效电路计算所得的各参数的拟合值。当施镀温度为65℃、75℃、85℃时,镀层的Rct1 + Rct2值分别为51.5 kΩ·cm2、53.9 kΩ·cm2、38.1 kΩ·cm2。当施镀温度为75℃时Rct1 + Rct2的值最大,该结果与Tafel极化曲线拟合数据中温度65℃下得到的镀层icorr最小的结果不一致,但65℃下镀层的Rct1 + Rct2值仅比75℃下镀层略小。结合极化曲线和电化学阻抗谱数据,施镀温度65℃时所得到的镀层也具有很好的耐腐蚀性能,同时降低施镀温度有利于节能减排和节约生产成本,因此选择65℃作为最优施镀温度条件。
刘海萍 [13] 分析比较了通过ENIG和ENEPIG工艺制得镀层在3.5% NaCl溶液中的耐腐蚀性。其中ENIG镀层的icorr = 2.872 μA·cm2,ENEPIG镀层的icorr = 1.007 μA·cm2,通过本优化工艺得到的镍磷镀层的icorr = 0.982 μA/cm2,相比ENIG和ENEPIG镀层表现出更好的耐腐蚀性。
综上,采用单因素变量法,通过工艺参数优化实验,依次对镀液pH值、复合添加剂浓度和施镀温度进行优化,确定了化学镀镍磷镀层的最优配方和工艺参数为:NiSO4·6H2O 30 g/L,NaH2PO2·H2O 20 g/L,复合添加剂30 g/L,pH = 4.0,温度65℃,时间60 min,并对该条件下得到的镍磷镀层进行形貌结构表征和可靠性测试。
3.2. 表面形貌及元素组成
最优条件下得到镍磷镀层的微观形貌FESEM图如图5(a)所示,从图中可以看出,镍磷镀层由大量胞状颗粒组成,具有典型的非晶胞状结构。由于复合添加剂的加入,镀层表面更为平整,无孔隙和裂缝,可以将铜基底完全覆盖。与上述镀层的表面组成相对应的EDS图谱(图5(b))表明,该镀层表面镍、磷元素质量分数分别为85.92%和10.48%。
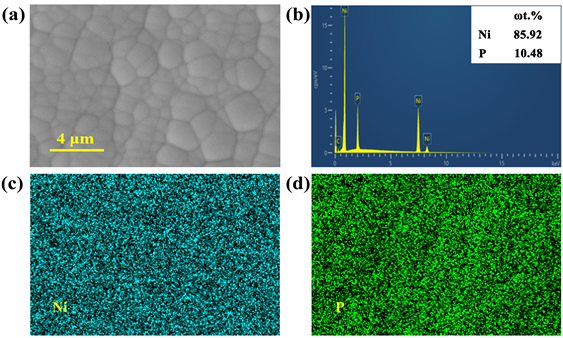
Figure 5. (a) FESEM, (b) Element weight radio, EDS-mapping of (c) Ni and (d) P of coating surface under optimal conditions
图5. 最优条件下镍磷镀层表面(a) FESEM图,(b) 元素重量比,EDS-mapping图:(c) Ni,(d) P
根据ASTM 733B-04标准,镍磷镀层中磷元素含量1%~4%为低磷镀层,5%~9%为中磷镀层,>10%时为高磷镀层,证明所得到的镀层为高磷镀层。磷元素的存在使镍磷合金不存在晶粒和晶界,非晶合金比同类多晶材料具有更强的抗腐蚀能力,增加其在腐蚀介质中的稳定性,因此高磷镀层具有很好的耐腐蚀性 [14] 。从图5(c)和图5(d)中可以看出镀层表面镍和磷元素分布非常均匀,无局部团聚现象的出现,证明得到的镍磷层结构致密,成分均匀。
3.3. 物相组成分析
由图6可知,最优条件下得到的镍磷镀层XRD图谱在2θ = 44.5˚的位置出现了一个较宽的馒头峰,该峰对应的是镍磷镀层的特征峰,其结构处于非晶态,这可能是由于镀层中的磷形成高度无序的晶格,导致其结构变成非晶态。对比标准卡片PDF#04-0836 [15] ,在43.30˚、50.43˚、74.13˚出现的明显尖锐的衍射峰分别对应Cu的(111)、(200)、(220)晶面,为铜基体的衍射峰,可能是因为形成的化学镀镍层较薄,X射线透过镀层采集到了铜基材的信息。
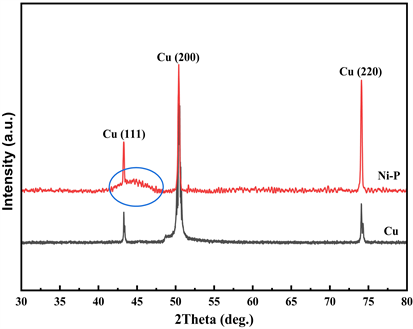
Figure 6. (a) FESEM, (b) Element weight radio, EDS-mapping of (c) Ni and (d) P of coating surface under optimal conditions
图6. 最优条件下镍磷镀层表面(a) FESEM图,(b) 元素重量比,EDS-mapping图:(c) Ni,(d) P
3.4. 镀层化学组分分析
采用XPS对最优条件下得到的镍磷镀层表面的化学组分进行了分析,图7(a)显示了测量光谱中有明显的Ni 2p、P 2p和O 1s峰,结果表明镀层主要由Ni、P组成,O的存在可能是镀层表面轻微氧化和污染造成的。如图8(b),在Ni 2p谱图中,852.3 eV和869.5 eV处的峰表明Ni以单质形式存在,855.6 eV和873.2 eV处的峰值属于Ni2+,分别属于Ni2+ 2p3/2和Ni2+ 2p1/2,表明Ni处于氧化态,861.6 eV和879.1 eV处的峰分别对应Ni2+ 2p3/2和Ni2+ 2p1/2的卫星峰 [16] 。同样,如图7(c),在P 2p谱图中,129.1 eV和130.0 eV处的峰表明镀层中存在P的单质形式,133.2 eV处的峰属于P5+,是磷的氧化态 [17] 。在图7(d) O 1s的谱图中,出现在531.6 eV的峰对应Ni(OH)2,529.9 eV和532.3 eV的峰分别对应NiO和Ni3(PO4)2,镍和磷的少量氧化态应源自暴露于空气中的表面涂层的轻微氧化,而不是化学沉积过程 [17] 。
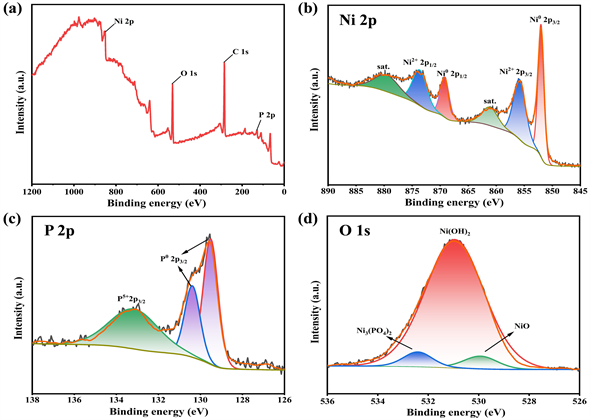
Figure 7. XPS spectra of (a) Full spectrum, (b) Ni 2p, (c) P 2p and (c) O 1s for the Ni-P coating under optimal conditions
图7. 最优条件下镍磷镀层XPS图谱:(a) 全谱;(b) Ni 2p;(c) P 2p;(d) O 1s
3.5. 中性盐雾测试
将最优工艺参数应用于PCB板铜线路表面处理,将覆盖镀层的PCB试样悬挂在盐雾箱内进行中性盐雾实验,样品测试采用质量分数5 ± 0.5%的NaCl溶液连续喷雾,溶液pH值为6.5~7.2,盐雾试验箱温度为35℃。不同盐雾喷雾时间点样品表面锈蚀情况如图8所示,从图中结果可以看出,中性盐雾时间达到864 h时样品表面仍无明显异常,说明该镍磷镀层具有良好的耐中性盐雾腐蚀性能。
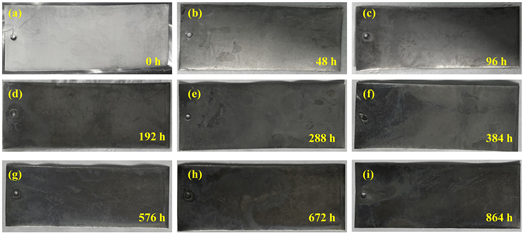
Figure 8. Surface condition of samples with different salt spray corrosion times
图8. 不同盐雾腐蚀时间样件表面情况
3.6. 可焊性测试
使用FX-320型无铅钛锡炉对最优条件下化学镀镍磷的PCB样件进行可焊性测试,锡炉温度为255℃,焊料使用Sn 96.5% Ag 3.0% Cu 0.5%,助焊剂使用ROL0,浸锡时间为5 s。试样在测试前先进行表面除油和清洗,然后105℃烘烤1小时。测试合格判定标准为:样品锡面应该有≥95%的面积均匀、光滑、润湿良好。剩余的面积允许存在小针孔、退润湿、表面粗糙等缺陷,但不能集中在一个区域。
可焊性测试前后对比图如下图9所示,从图9(a)浸锡前和图9(b)浸锡后的对比图可以看出,经过浸焊测试后,焊盘均被焊料润湿,上锡面积 ≥ 95%,且无不良润湿现象。附着膜分布均匀、连续且光滑,测试判定为合格,证明该镍磷镀层具有良好的可焊性。
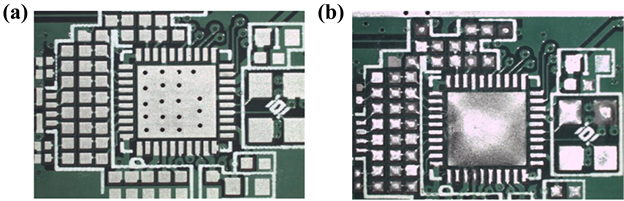
Figure 9. Photos before and after soladerability test: (a) before; (b) after
图9. 浸焊测试前后对比图:(a) 浸锡前;(b) 浸锡后
4. 总结
本文通过加入一种实验室自研的复合添加剂改良传统的化学镀镍磷工艺,获得了更为致密的化学镀镍磷镀层,并采用单因素变量法,依次对镀液pH值、复合添加剂浓度和施镀温度进行了优化。
1) 以镀层在3.5% NaCl溶液中的电化学测试结果为衡量指标,得到最优的镀液配方和工艺参数为:NiSO4·6H2O 30 g/L,NaH2PO2·H2O 20 g/L,复合添加剂30 g/L,pH = 4.0,温度65℃,结果表明镀层具有良好耐腐蚀性。
2) 对最优条件下得到的镍磷镀层进行形貌与成分分析,结果表明,由于复合添加剂的加入,所得镀层平整致密,无孔隙和裂缝,由大量胞状颗粒组成。镀层表面Ni和P元素分布均匀,镀层为高磷镀层,并呈非晶态结构。
3) 将最优工艺条件应用于PCB板的铜线路表面化学镀镍,得到的镀层经中性盐雾腐蚀864 h后样品表面仍无明显异常,证明镀层具有良好的耐盐雾腐蚀能力。浸焊测试后焊盘上锡面积 ≥ 95%,且无不良润湿现象,附着膜分布均匀、连续且光滑,证明镀层具有良好的可焊性。
因此通过该化学镀镍磷工艺得到的镍磷镀层可以达到目前ENIG和ENEPIG工艺的性能要求。
基金项目
武汉工程大学第十四届研究生教育创新基金(项目编号:CX2022442)。
NOTES
*通讯作者。