1. 引言
TC1钛合金以其优异的强度和抗蠕变特性而广泛用于航空发动机叶片,压气机盘和叶盘等重要部件上 [1] 。然而,TC11的硬度较低,耐磨损性能较差,对于其作为原材料生产的零部件长期服役于恶劣的环境中,如长期承受交变载荷和高温高压的耦合作用,极易造成零件表面的磨损损伤或失效,甚至造成灾难性事故 [2] 。因此,采用表面改性技术在零件表面熔覆高性能的熔覆层,提高零件的表面强度和抗磨损性能是非常有必要的 [3] 。据报道,表面改性技术主要以激光熔覆、冷/热喷涂、磁控溅射、电火花沉积、化学气相沉积、物理气相沉积和等离子熔覆等 [4] [5] [6] [7] 。等离子熔覆技术可以实现基体和熔覆材料的高强度冶金结合,组织致密,熔覆缺陷少,并且其具有的热转化效率高、成本低、熔覆材料范围广泛、对工作环境要求低等特点,使其在工业生产和科学研究中得到了广泛应用 [8] 。
高熵合金自从被提出以来,因其具有独特的微观结构和优异的综合力学性能而收到了研究者的极大关注 [9] 。高熵合金所具有的四大效应,使其能够倾向于形成体心立方结构(BCC),面心立方结构(FCC)和密排六方结构(HCP) [10] 。研究表明,高熵合金具有良好的抗氧化性和耐磨损性能,并且有望成为航空航天领域的新型材料。然而,为了使高熵合金具有更加优异的耐磨损性能和力学性能,近年来,广泛的学者通过向高熵合金中添加碳化物,使其产生碳化物增强相而提高综合性能成为了研究热点。李想等 [11] 通过离子熔覆制备WC增强镍基合金涂层,发现该熔覆层的硬度是基体的4~6倍。Yan等 [12] 探讨了WC含量对不锈钢表面激光熔覆镍基熔覆层的影响,结果表明,WC含量的增加导致熔覆层的显微硬度和耐磨损性能均有显著的提升。但是,对于向高熵合金中添加碳化物,原位合成其他形式的碳化物增强相的研究较少。
研究表明,适量Al元素的添加可导致高熵合金体系向BCC结构转变,并且可提高合金耐磨损性能 [13] ;Mo元素的添加可以同时提高高熵合金的强度和硬度 [14] ;适量Zr元素的添加可改善合金体系微观组织 [15] ;适量的Si元素可提高高熵合金的抗氧化性能和耐腐蚀性能 [16] ;碳化物陶瓷颗粒的添加可显著提升高熵合金体系的硬度和耐磨损性能 [17] 。因此,本文作者利用等离子熔覆技术,探究通过向AlMoZrSi基础高熵合金中添加Cr3C2增强颗粒,从而原位合成其他形式碳化物增强相的高熵合金。分析Cr3C2的添加对其微观组织,显微硬度和耐磨损性能的影响。
2. 试验材料与方法
以TC11钛合金为熔覆基材,通过DK7720型电火花数控线切割机床将其切割为100 mm × 80 mm × 5 mm的尺寸。Al,Mo,Si(纯度,即质量分数分别大于99.5%)单质金属粉末和Zr (原子百分比含量为Al:66.7%,Zr:33.3%)以及Cr3C2粉末作为熔覆原材料。五种金属粉末的粒径均在70~250目之间。AlMoZrSi高熵合金粉末按照等原子比称重配置,Cr3C2粉末的添加是在AlMoZrSi高熵合金粉末的基础上按照质量百分比配置。将配置好的粉末使用XQM-4L型球磨机以粉球质量比为5:1,300 r/min研磨3小时后放入XMA-2000型干燥箱,100℃的温度干燥1小时,随箱冷却至室温,保证熔覆材料的流动性。在熔覆实验开始之前用砂纸对TC11钛合金表面打磨除去油污及氧化物,然后用酒精进行超声清洗并且干燥。
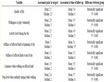
Table 1. The plasma cladding process parameters
表1. 等离子熔覆实验参数
等离子熔覆实验是基于MOTOMAN UP6型工业机械臂和配备有同轴送粉的DML-V02BD型等离子焊机完成。熔覆过程中以高纯氩气作为保护气体,保护熔池免受氧化。实验参数如表1所示。使用电火花数控线切割机床将所制备的高熵合金熔覆层连同基体沿横截面切割成5 mm × 5 mm × 8 mm样品,并采用60#~3000#粒度的砂纸和粒径为2.5 µm的金刚石悬浮抛光液对其进行研磨和抛光处理。采用配备有能谱仪的QUANTA FEG 450型热场发射扫描电子显微镜(SEM)观察和分析样品的微观组织以及化学成分。采用XRD-7000X型X射线衍射仪(XRD)进行物相分析;衍射角范围为20◦~100◦,扫描速度为5◦/min。采用HXD-1000TMB型维氏硬度计测量熔覆层的显微硬度,载荷为200 gf,保载时间15 s,每个样品测量15个点,从熔覆层顶部开始向着基体方向,每个点间隔为500 µm。利用HT-1000型球盘式摩擦磨损试验机对熔覆层进行干摩擦磨损实验。摩擦球材料为Φ6 mm的Si3N4球,法向载荷为15 N,实验时间30 min,主轴转速318.8 r/min。利用KLA-Tencor D-100型二维轮廓仪测量磨痕截面面积、扫描电子显微镜(SEM)和能谱仪(EDS)分析磨损形貌和化学成分。为了方便表述,下文中将AlMoZrSi(Cr3C2)x (x = 7.5%, 10%)高熵合金熔覆层测试样品分别记为样品1和样品2。
3. 结果与分析
3.1. 微观组织
图1所示为AlMoZrSi(Cr3C2)x (x = 7.5%, 10%)高熵合金熔覆层的XRD图谱。可以看出,样品1和样品2均由体心立方结构(BCC)固溶体和MC (M: Ti, Si, Zr, Mo)型碳化物构成 [18] [19] 。两个样品中均未检测到Cr3C2的峰,可见Cr3C2在等离子熔覆的过程中已全部溶解,并且参与了MC型碳化物的生成。因为熔覆层成分含有大量的Al大量的元素,它会促进面心立方结构(FCC)向BCC的转变。即Al元素的原子半径相对于其他组元较大,原子之间半径尺寸差异增大,将会导致晶格畸变程度加强,并且BCC结构较为疏松,因此合金体系会向BCC结构转变 [20] 。所以两个样品中均未检测到FCC结构。通过Jade9.5软件检测BCC峰与Al5Ti3相较为符合,说明该高熵合金体系中出现了类似Al5Ti3结构的固溶体。高熵合金中固溶体由于组元间结合力的不同,往往会出现偏聚而形成元素富集区,Al元素与体系内其他元素有较大的混合焓,因此在该体系中Al元素和其他组元有较大的亲和力,容易形成元素偏聚现象。

Figure 1. X-ray diffraction pattern of the sample
图1. 样品的X射线衍射图谱
图2所示为两个样品截面形貌、高倍表面形貌及其对应的EDS元素分布图。从图2(a1)和图2(b1)可以看出熔覆层成型良好,组织致密,基体与熔覆层结合良好,具有明显的融合线。通过高倍SEM进一步分析表明,如图2(a2)和图2(b2)所示,两个样品均由黑色的基体相和灰色相组成。且两个样品灰色相均以层片状晶体结构分布在黑色基体相中。采用EDS对两个样品的黑色基体相和灰色相进行成分分析,四相化学成分列于表2中,并且通过EDS分析表明Ti元素出现在了熔覆层中,这是因为在等离子熔覆过程中,会在基体TC11表面形成一个熔融区,也正是因为该区域的存在才会使得熔覆材料与基体实现良好冶金结合,同时Ti元素的渗入也能达到熔覆层的稀释效果。丁林 [21] 也得出类似的结论,在激光熔覆Co基粉中,元素与基体之间的互相扩散促进了平面晶体的形成,表明激光熔覆制备的熔覆层与基体是冶金结合的。通过表2数据可知,样品1和2的基体相富含高占比的Al和C,还包含了一定量的Ti元素,层片状灰色相富含较高的C,Ti和Si元素。这表明两个样品的微观结构基本类似。结合表2,EDS图片和XRD分析结果可知,两个样品黑色相均为Al5Ti3和富C的BCC高熵固溶基体相,而灰色相均为MC型碳化物陶瓷相。因此,通过等离子熔覆制备的AlMoZrSi(Cr3C2)x(x=7.5%, 10%)高熵合金熔覆层,黑色BCC基体相因富集较多的Al和Ti元素将会赋予高熵合金优异的塑性,而MC型碳化物硬质陶瓷相将会赋予合金良好的强度。
从以上微观结构分析结果可知,两个样品中主要存在MC(M: Ti, Si, Zr,Mo)型碳化物。对熔池中可能发生的化学反应进行热力学分析,可以起到控制熔覆层组织和性能的目的 [22] 。在等离子熔覆过程中,基体表面、AlMoZrSi和Cr3C2粉末溶解,熔池中主要存在Al、Mo、Zr、Si、Ti、C和Cr等元素。熔池凝固过程中可能发生的反应如下式(1)。

Figure 2. The cross-sectional morphology, microstructure and the corresponding EDS element distribution of the samples
图2. 样品的截面形貌、微观形貌及其对应的EDS元素分布图
M + C = MC (1)
根据热力学计算软件(HSC chemistry version 9.5)计算了TiC、SiC、ZrC和MoC在200~2400℃的吉布斯自由能值(ΔG),结果如图3中所示。从图中可以看到TiC、SiC、ZrC和MoC的ΔG在200~2400℃温度范围内均为负值。从热力学角度来讲,说明在等离子熔覆的过程中它们在熔覆层中生成是可自发进行的 [23] 。所以上述MC型碳化物是在等离子熔覆AlMoZrSi(Cr3C2)x (x = 7.5%, 10%)高熵合金的过程中原位合成的。

Figure 3. Gibbs free energy curve of chemical reaction with temperature change
图3. 化学反应随温度变化的吉布斯自由能曲线图
3.2. 显微硬度
图4显示了所制备高熵合金熔覆层横截面沿深度方向的显微硬度分布。由图可知基体,样品1和样品2的平均显微硬度分别为390.3 HV,846.33 HV,1009.27 HV。显然,基体的显微硬度是最低的,当添加7.5%Cr3C2后样品1的显微硬度较基体有很大的提升。Cr3C2的含量增加到10%时,样品2的平均显微硬度较样品1又提升了162.94 HV。样品1和2的平均显微硬度分别是基体的2.17和2.56倍。可见Cr3C2的添加对于提高基体的显微硬度具有显著的效果。样品1和2显微硬度的增加主要归结于三个原因 [24] :一是添加的Cr3C2在熔覆的过程中分解并且固溶于基体相和层片状碳化物相中,并且含有较大原子半径的Zr和Mo置换固溶于固溶体中,使固溶体的晶格发生畸变,同时Zr和Mo偏聚于位错周围,阻碍了位错滑移的产生,起到了固溶强化的作用。二是原位合成的MC型碳化物分布在层片状碳化物相的晶间,MC型碳化物是高硬度的硬质颗粒,并且原位合成的MC型碳化物的含量随着Cr3C2的增加也会增加,位错滑移会使硬质碳化物颗粒相在基体相和层片状碳化物相的晶界出产生堆积,起到了晶界强化的作用。三是原位合成的MC型碳化物弥散分布在层片状碳化物相的熔覆层中,起到了弥散强化的作用。分析样品的显微硬度分布曲线可见,样品顶部区域显微硬度是最高的,逐渐向基体靠近的区域,显微硬度有个明显下降的趋势。这是由于在等离子熔覆过程中会在基体表面的熔融区形成一个一定区域的热影响区,此区域的温度急剧升高,然后又急剧降低,导致该区域的微观结构发生变化。样品2的显微硬度高于样品1的,这是由于样品2相较于样品1具有较多的Cr3C2添加量,熔覆过程中析出的C含量高于样品1,导致原位合成的MC型碳化物含量高于样品1,硬质碳化物的强化效果高于样品1.
3.3. 摩擦磨损行为
图5(a)所示为样品的摩擦磨损截面二维轮廓曲线。从图中可以看出,JT的磨损截面形貌轮廓尺寸最大,样品1的磨损截面形貌相较于JT有明显的缩小,样品2相较于样品1在深度上有所减小。这在一定程度上体现出了Cr3C2的添加对于提高JT的耐磨损性能有积极的作用。
样品的磨损率根据以下公式(2)计算 [25] 。

Figure 4. Microhardness distribution of sample cross section
图4. 样品横截面显微硬度分布图
(2)
W (mm3/N/m)是磨损率,V (mm3)是磨损体积,F(N)是摩擦磨损实验中施加的法向载荷,L(m)是滑动距离。图5(b)是基体、样品1和2的磨损率示意图。从图中可以看出基体的磨损率最高。样品2的磨损率最低。这充分的体现了Cr3C2的添加对于降低磨损率,提高耐磨损性能具有显著的作用。这是由于Cr3C2的加入使得在熔覆过程中溶解析出了Cr和C原子,Cr原子固溶于BCC基体相中,起到了固溶强化的效果;熔覆层中原位生成的碳化物弥散分布在熔覆层中,起到了弥散强化的效果;熔覆材料中含有大量的Al和Mo等大量的合金化元素,该元素的存在会加剧晶格畸变的程度,因此熔覆层基体组织主要以BCC相为主。在固溶强化、弥散强化和晶格畸变的加持下致使两个含有Cr3C2的熔覆层磨损率下降,耐磨损性能提升。
(a) (b)
Figure 5. The wear cross-section morphology and wear rate of the sample
图5. 样品的磨损截面形貌和磨损率
为了进一步探究熔覆层的磨损机理,对JT,样品1和2的磨损表面形貌进行了扫面电镜表征,结果如图6所示。图6为三个样品的磨损机理示意图。图6(a)为JT的磨损形貌图。从图中可以看出磨损面塑性变形现象明显,存在着许多沿着摩擦方向的塑性变形犁沟,主要以磨粒磨损和粘着磨损为主。图6(b)为样品1的磨损形貌图,摩损初期,硬度较低的基体相遭受了摩擦球表面硬质点的严重切削作用,产生了许多较为严重的塑性变形和平行于摩擦方向的犁沟。随着磨损进入稳定磨损期,塑性变形逐渐产生加工硬化现象,使得软基体相塑性变形表面硬度上升,韧性降低。在交变应力的作用下,逐渐剥落和形成粘合坑。因此磨损表面较为平整,主要以粘着磨损为主。这可归因于熔覆层显微硬度的提升以及原位生成的MC型碳化物的强化作用。图6(c)为样品2的磨损形貌图。从图中可以看出该样品还是以粘着磨损为主,但是相较于样品1来看,样品2则表现出了更为平整的磨损表面。这可归因于更多的MC型碳化物的存在使得晶界强化效应增强,有效的阻碍了位错和晶粒滑移的发生。在稳定磨损阶段,使得熔覆层在交变应力的作用下难以产生塑性变形,并且原位生成的MC型碳化物的存在有效降低了摩擦球硬质点的切削作用,使得摩擦面主要以粘着变形为主,粘着变形导致材料的去除率降低。因此样品2主要以粘着磨损为主。从以上的分析可得,样品2的耐磨损性能最佳。主要是由于样品2具有较高的显微硬度和更多的MC型碳化物的强化作用。

Figure 6. The wear morphology of the sample; (a1)~(b1) are the wear profiles of the matrix, sample 1 and sample 2, respectively; (a2)~(b2) are the local high-power wear morphologies of the matrix, sample 1 and sample 2, respectively
图6. 样品的磨损形貌图;(a1)~(b1)分别为基体,样品1和样品2的磨损全貌;(a2)~(b2)分别为基体,样品1和样品2的局部高倍磨损形貌
4. 结论
应用等离子熔覆技术制备的AlMoZrSi(Cr3C2)x (x = 7.5%, 10%)高熵合金熔覆层主要以BCC基体相和MC型碳化物相组成。其中MC型碳化物相主要以层片状共晶的形式分布在BCC基体相中。BCC基体相赋予了熔覆层良好的塑性,使得熔覆材料和基体材料冶金结合良好,而MC型碳化物相使得熔覆层具有较高的显微硬度和良好的耐磨损性能。BCC相和MC型碳化物相的综合作用使得AlMoZrSi(Cr3C2)x (x = 7.5%, 10%)高熵合金具有较强的综合力学性能。
AlMoZrSi(Cr3C2)x (x = 7.5%, 10%)高熵合金熔覆层的显微硬度分别是基体的2.17和2.56倍,磨损率较基体分别提高了19.2%和26.5%,磨损机理主要以粘着磨损为主。添加wt10%Cr3C2的高熵合金熔覆层表现出了最高的显微硬度和最好的耐摩擦磨损性能。
基金项目
国家自然科学基金(52075235);甘肃省科技计划项目(2022JR5RA314, 22YF7WA151, 22YF7GA138, 23CXGA0151);甘肃省教育厅产业支撑计划项目(2022CYZC-31)和甘肃省科协创新驱动力工程项目(GXH20230817-10)。
NOTES
*通讯作者。