1. 引言
钻爆法和硬岩掘进机(TBM)是硬岩地层中的隧道开挖的主要方式。相比于传统钻爆法,TBM法具有掘进速度快、施工工期短、作业安全、对周边环境扰动小和综合经济效益高等优点。但TBM在掘进过程中,由于地层条件的复杂性及施工参数的难确定性,会发生滚刀磨损甚至破坏的情况,需要进行开仓换刀,严重影响着掘进的效率。这一点在较为坚硬的花岗岩地层中尤为明显。
评价滚刀破岩效率及抗磨损性能最常用的方法是开展滚刀切割破岩试验。基于滚刀切割破岩试验的结果,一些学者提出了对实际工程具有指导意义的结论和建议。马洪素等 [1] 和Yin等 [2] 研究了岩石节理间距以及节理面角度对切割的影响,探究了若干个不同节理角度和间距下岩石受到切割时裂缝产生的形式的情况。刘京铄等 [3] 通过线性切割试验发现互相垂直的两个方向上的围岩压力差值越大,岩石更容易被切割。Gertsch等 [4] 开展了粗颗粒红石英上滚刀破岩的线性切割试验,得到法向力与切向力随贯入度及刀间距增大而增大的普遍结论,同时指出作为切割系数随贯入度增大而近似线性增大但却几乎与刀间距无关的结论。Zhang等 [5] 通过模拟滚刀在不同环境(干燥、淡水、海水)下的切割工况,指出了适当的湿润环境能够缓解滚刀切割受到的磨损,为不同地下水环境中的盾构开挖工程提供了参考。
上述研究均采用的是线性切割试验,而更为精确地反映真实的破岩条件需要开展全断面回转切割试验。由于现有的全断面回转切割平台数量较少,相关研究也相对较少。Pan等 [6] [7] 基于郑州国家重点实验室的全断面回转试验平台,采用水泥砂浆代替实际岩石的方式,获得了回转切割条件下三向力随贯入度和切割半径的变化规律,滚刀所受的三向力在切割半径减小的过程中具有不断增大的趋势,在对其数据结果分析的基础上,同时还提出了一个临界切割半径的概念,即切割半径在超过这一值之后滚刀受力随半径变化的影响不再显著。温森等 [8] 通过对砂岩和花岗岩复合试样进行回转切割试验,获得了软硬交互地层平均法向力、平均扭矩随贯入度和刀间距的变化规律。
此外,还有一些学者通过有限单元法 [9] [10] 或离散单元法数值模拟 [11] [12] [13] 对滚刀破岩性能及力学机理开展了研究。
由此可见,虽然已有大量有关滚刀破岩切割试验的研究,但回转切割试验研究较少且岩样的尺寸均较小,与真实场景有一定的差异。本研究基于上海隧道工程有限公司自主研发的大尺寸回转切割试验平台,通过对施工现场取样的花岗岩试样开展大尺寸回转切割试验,模拟更为贴近实际工程的破岩条件,探求关键施工参数对破岩效率的影响规律,从而指导实际工程施工。
2. 试验设计
2.1. 试验装置
如图1所示,本研究所采用的切割试验系统主要包括两部分:切割系统和岩石回转系统。切割系统由水平液压千斤顶控制,用以调整切割角度,与岩石回转系统协调完成切割。岩石回转切割系统通过电动机输出扭矩控制岩石盘面回转,相对固定刀具回转运动。另外,还有刀具固定装置、提供刀盘稳定支撑的门式刚架等辅助性装置。切割过程中各系统和装置协同作业,共同完成切割试验。试验装置所能容纳的最大岩盘直径为3.2 m。
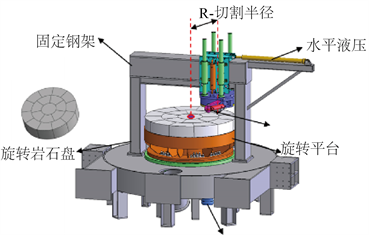
Figure 1. Illustration of the rotatory cutting apparatus
图1. 回转切割装置示意图
2.2. 测试系统
如图2所示,滚刀上方安装FC3D500三轴传感器,测量滚刀在切割过程中沿空间X、Y、Z三个方向的作用力,分别对应滚刀的滚动力、侧向力和法向力。三轴传感器的主要技术参数为:
(1) 尺寸:500 mm × 500 mm × 80 mm;
(2) 测量量程:Fx:0~150 kN;Fy:0~150 kN;Fz:0~300 kN;
(3) 精度等级:0.5%;
(4) 工作温度:−25~+50℃。
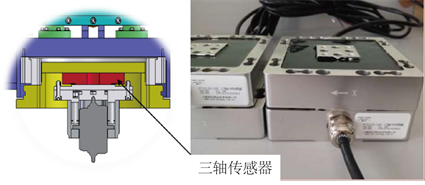
Figure 2. Triaxial force transducer installed over the disc cutter
图2. 安装在盘形滚刀上方的三轴传感器
2.3. 岩盘安装
试验岩样取自福州地铁4号线一期工程现场,为中风化花岗岩,饱和状态岩石单轴抗压强度35.374~90.63 MPa,平均值58.90 MPa,天然状态岩石单轴抗压强度41.630~103.24 MPa,平均值70.66 MPa。考虑到现场无法直接取出直径3.2 m的岩样,采用对圆柱体岩样按照预先设计的分块尺寸切割出单元试块后逐次拼装填充至岩盘模具中的方式制作岩盘,如图3所示。采用高强度水泥砂浆灌浆填充拼装后岩样之间的缝隙,养护至达到强度90 MPa的要求,以保障各分块间的有力胶结。
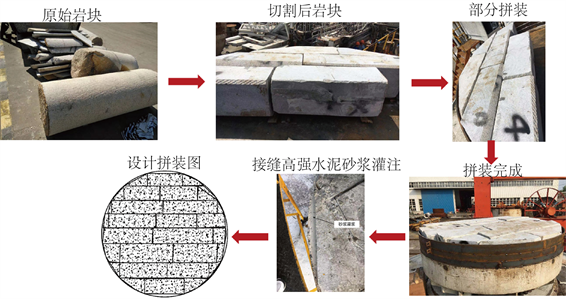
Figure 3. Installation process of the rock sample
图3. 岩盘拼装过程
2.4. 试验工况
采用了19 mm刃宽的标准滚刀,以10 cm和13 cm作为刀间距,考察岩盘转速、贯入度和切割半径对滚刀力以及破岩效果的影响。岩盘转速取0.4、0.8和1.2转/分钟,贯入度取1、2、3和4 mm,切割半径以水平千斤顶行程表示,切割半径从660 mm变化至1260 mm。详细的试验工况如表1所示。
试验机采用下方岩盘转动、上方滚刀固定的方式实现相对回转切割,切割试验过程如图4所示。在试验进行过程中,同步采用工业吸尘器对岩片和岩渣进行清理,在每一工况试验结束后,对岩盘进行整体清理,保证岩盘的整洁,不影响后续切割进行。
(a) 岩块、岩渣同步清理
(b) 岩盘整体清理
Figure 4. Photos of cutting process
图4. 试验切割过程照片
3. 试验结果分析
3.1. 破岩平均力分析
不同贯入度下的切割工况,三向力均在切割2圈之后开始逐渐降低,并在若干圈后稳定在一近似相同的较低值,故可知前两圈为主要破岩过程。因此,本试验针对贯入度为1、2、3和4 mm工况下,均取前2圈范围三向力的平均值作为破岩平均力。在保持转速为0.8 rev/min的情况下,10 cm刀间距,不同工况下破岩三向力演化如图5所示。总体而言,随着贯入度的增加,滚刀所受三向力显著上升。除个别切割半径工况外,滚刀的三向力都呈现先上升后下降的非线性趋势,在3 mm贯入度时达到峰值。但切割系数随贯入度的变化并不显著,略微呈现随贯入度增大而下降的趋势,总体维持在24%左右。
图6为滚刀三向力及切割系数随切割转速增大的变化情况。相比贯入度对三向力的影响,切割转速的改变对滚刀三向力的影响并不明显,不同切割转速下滚刀三向力及切割系数都较为接近,均在某一数值上下波动。
(a) 滚动力 (b) 侧向力
(c) 法向力(d) 切割系数
Figure 5. Variation of three directional cutting forces and cutting coefficient with increasing penetration (revolution speed = 0.8 rev/min, spacing = 10 cm)
图5. 滚刀三向力及切割系数随贯入度增大的变化情况(转速 = 0.8 rev/min,刀间距 = 10 cm)
(a) 滚动力 (b) 侧向力
(c) 法向力(d) 切割系数
Figure 6. Variation of three directional cutting forces and cutting coefficient with increasing revolution speed
图6. 滚刀三向力及切割系数随切割转速增大的变化情况
图7为转速0.8 rev/min,刀间距10 cm下三向力随切割半径的变化情况。由图可知,切向力和法向力随切割半径的变化规律不明显,呈现一定的波动,但侧向力随切割半径的减小而逐渐增大,且切割系数也随切割半径的增大而增大,大致变化范围在0.15~0.26之间。试验中并未出现Pan等 [6] [7] 所提出的临界切割半径的现象,这可能是因为本项研究中考虑的切割半径较大,已经超出了临界切割半径的范围。
(a) 滚动力 (b) 侧向力
(c) 法向力 (d) 切割系数
Figure 7. Variation of three directional cutting forces and cutting coefficient with cutting radius (revolution speed = 0.8 rev/min, spacing = 10 cm)
图7. 滚刀三向力及切割系数随切割半径的变化情况(转速 = 0.8 rev/min,刀间距 = 10 cm)
3.2. 破岩比能分析
转速1.2 rev/min,刀间距10 cm下单圈破岩所做功随贯入度和切割半径的变化情况如图8所示。由图可知,单圈破岩所做功随着贯入度的增加呈非线性增加趋势,且总体随着切割半径的增大而增大。这是因为切槽体积随着贯入度及切割半径的增加而增大,单圈所破岩的量也随之增大。为了进一步分析贯入度和切割半径对于破岩效率的影响,计算破岩比能:
(1)
其中,Fr为滚刀滚动力,lr为滚刀行进长度,V为对应的破岩体积。每个工况完成后收集岩片和岩渣,对其进行称重,然后根据岩样的天然重度即可计算出破岩岩渣体积。如图9所示,不同切割半径工况的破岩比能基本呈现随贯入度增大先减小而后增大的趋势,并在3 mm的贯入度处达到最小值(即最优贯入度)。
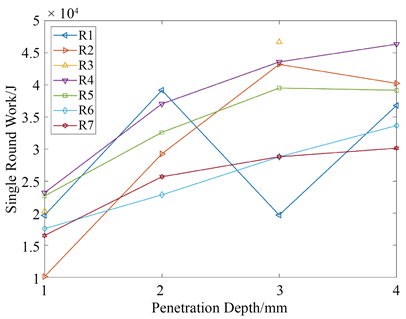
Figure 8. Variation of work per round with penetration depth (revolution speed = 1.2 rev/min, spacing = 10 cm)
图8. 单圈破岩所做功随贯入度变化情况((转速 = 1.2 rev/min,刀间距 = 10 cm)
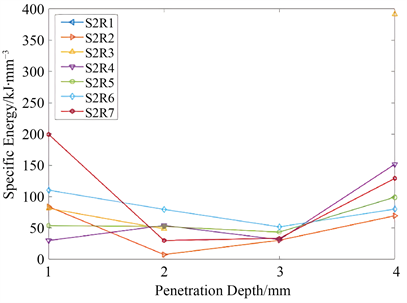
Figure 9. Variation of specific energy with increasing penetration depth (revolution speed = 0.8 rev/min, spacing = 10 cm)
图9. 滚刀破岩比能随贯入度增大的变化情况(转速 = 0.8 rev/min,刀间距 = 10 cm)
4. 结论
利用自主研发的可重构大型滚刀回转切割破岩平台对福州市轨道交通4号线一期工程中滚刀破岩性能开展了大型回转切割试验研究。系统研究了包括贯入度、转速、切割半径等施工参数对滚刀破岩效果的影响,主要结论如下:
(1) 滚刀三向力(法向力、滚动力和侧向力)随着切割圈数的增大而呈现波动下降并最终保持波动平稳的规律。
(2) 贯入度是滚刀破岩的最关键影响因素。滚刀平均法向力与滚动力均随贯入度的增大而近似线性增大,但在达到某一贯入度后呈现出非线性增大的趋势;法向力与滚动力随切割半径的增加没有明显的变化规律,但切割系数随着切割半径的增加而减小,侧向力受切割半径的影响较大,呈现出随切割半径减小而明显增大的现象。在1.2 rev/min以内切割转速对滚刀破岩没有明显影响,据此可建议现场适当增加转速来提高推进效率。
(3) 滚刀破岩比能随贯入度的增大呈现先减小后增大的趋势,存在一临界贯入度使得破岩比能最低,对于本试验所用岩样19 mm刃宽滚刀10 cm刀间距下最优贯入度为3 mm。
致谢
特别感谢同济大学硕士研究生唐苗原在数据处理过程中给予的帮助。
基金项目
上海市青年科技启明星21QB1401800。