1. 汽车排气系统
汽车在行驶的过程中,在加速和减速的情况下会产生不同程度的载荷,当挂钩的刚度过低就会发生位移和断裂;当汽车处于启动和行挂挡时发动机由于空转会产生怠速现象,引起共振从而影响悬挂胶的寿命。所以,测试、分析和优化汽车零件在极端条件下的受力情况以及减小汽车的行驶噪音是必不可少的工作 [1]。
CAE (Computer Aided Engineering)通过对排气系统进行NVH性能分析,可以有效并快速地确定问题所在并进行优化。对排气系统的分析要首先验证其结构强度;再通过模态分析检验排气系统是否会在怠速情况下发生共振。
1.1. 排气系统的组成
排气系统大致按温度可以分为热端和冷端。其中,热端的由于主要其催化总成的作用,所以在汽车的日常行驶中热端的温度通常在500℃~600℃;冷端的作用主要是消除噪音和排出废气,所以冷端尾管处温度通常在200℃~300℃。
1.2. 排气系统的构建及简化
使用CATIA对排气系统模型进行构建。网格构建使用HyperMesh软件。为了提高计算精度,需要对排气系统的部分零件进行简化处理。在排气系统热端使用RB3模拟质心,再用MASS单元来替代热端催化器的质量;对螺孔进行WASHER以确保连接的准确性。用RB2刚性单元来模拟发动机与三元催化器、排气系统吊耳之间的刚性连接。用SHELL单元来连接冷端箱体、端盖和箱体上筋板。用CBUSH单元来模拟挂钩与挂钩之间的悬挂胶连接。由于安装于发动机排气岐管和消声器之间排气管上的排气波纹管有一定的质量并且自身拥有自由度,所以使用1D-MASSES来模拟波纹管的质量 [2]。网格单元尺寸为5 mm,其中网格单元总数为53663。
使用SH409L铝合金作为排气系统主副消声器、尾管等部件的材料。单元格式为SHELL壳单元,箱体厚度和排气管道厚度定义为1.2 mm,左右端盖厚度1.5 mm。Q235用作法兰和挂钩的材料,单元格式为SOLID实体单元 [3] (见表1)。挂钩与挂钩之间使用悬挂胶进行连接,其Z向刚度10 N/mm,X向刚度3 N/mm。波纹管刚度参数值由供应商提供,质量为0.6 kg;轴向刚度为15 N/mm;径向刚度为1.2 N/mm。
在对模型划分好的区域进行网格构建后,进行网格质量检测。使用OptiStruct对已形成网格的零件进行求解分析,可以模拟汽车在行驶过程排气系统的状态。
2. 排气系统的静力分析
由于排气系统的固定是依靠螺栓之间的吊耳进行固定的,所以有必要对排气系统进行1G和4G条件下的静力分析以确保排气系统的受力在允许的范围内。需要对位于排气系统的四个挂钩进行测试,使其在1G静载工况下其性能满足各挂钩最大支反力 ≤ 50 N;最大位移 ≤ 5 mm;在4G冲击载荷下性能满足挂钩焊缝应力 < 150 Mpa;管壳焊缝应力 < 100 Mpa要求。
排气系统上一共3个挂钩,如图1分布:
2.1. 排气系统的连接
第一挂钩和第二挂钩使用CBUSH来模拟挂钩、悬挂胶、螺栓之间的连接。螺栓和卡扣之间使用一圈RB2模拟刚性连接;卡扣和箱体之间使用SHELL方式进行连接。
第三挂钩使用CBUSH来模拟挂钩、悬挂胶、管道之间的连接;挂钩和管道之间采用RB2来模拟刚性连接。
2.2. 工况测试
在对该模型进行4G下的工况测试时,发现第一挂钩处的焊缝应力为163.454 Mpa (见图2),大于规定值150 Mpa。故对改处的挂钩进行优化。
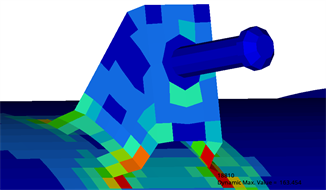
Figure 2. Weld stress of the first hook
图2. 第一挂钩焊缝应力
2.3. 优化方案
根据剪切应力公式:
A为焊缝横截面积,增大横截面积可减小剪切应力,故把卡扣和箱体之间的点焊变为全焊(见图3和图4)。
2.4. 1G工况下的分析
排气系统的热端和冷端通过法兰进行刚性连接,同时法兰也通过悬挂胶承连接车体;箱体上的两个卡扣和螺栓、排气管道上的螺栓也通过悬挂胶和车体进行固定。对其进行预载力分析以确保挂钩在该位置不会发生断裂。
优化后的排气系统的应力分析如下图所示,其中第一挂钩的支反力为38.474 N;第二挂钩的支反力为31.950 N,两个挂钩的支反力分布较为均匀。其中,由于第三挂钩距冷端距离较远,其支反力只有16.633 N。三个挂钩的支反力都小于规定的50 N,故符合要求(见图5)。
对此排气系统的位移进行分析。第一挂钩的位移为3.867 mm,第二挂钩的位移为3.191 mm,第三挂钩的位移为1.609 mm (见图6)。系统的最大位移4.074 mm位于箱体前端盖出,均小于规定值的5 mm (见图7)。
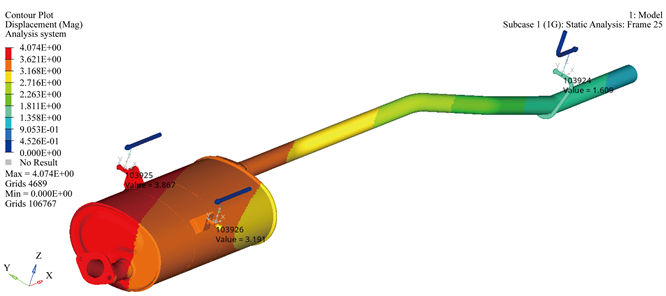
Figure 6. Cloud diagram of hook displacement
图6. 挂钩位移云图
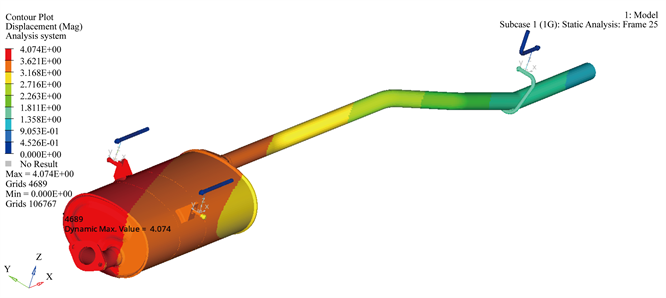
Figure 7. Cloud diagram of system displacement
图7. 系统位移云图
故该系统的1G静力分析符合安全要求。
1G静力分析主要分析系统在静置情况下挂钩各的受力和位移,防止系统失衡。该系统最大支反力在第一挂钩处为38.474 N;最大位移4.074 mm位于箱体前端盖出。故此系统在静置情况无失衡。
2.5. 4G工况下的分析
传统的化油器式发动机有五大基本工况,分别是:怠速、小负荷、中等负荷、大负荷(全负荷),加速工况。由于加速和减速工况会造成冲击载荷,此时如果挂钩由于刚度系数较低在冲击载荷下产生过大的位移甚至断裂,将会造成严重的安全事故。其中4G静力分析主要研究排气系统在发动机在垂向颠簸路段下的一个极限工况,等效为测试其在Z向加速度最大的工况 [4]。
对该模型进行4G静力分析分析:第一挂钩所受的应力为99.933 Mpa (见图8),相较优化前减少了63.521 Mpa,小于极限应力150 Mpa,符合要求。第二挂钩的应力大小为85.088 Mpa (见图9);第三挂钩的应力为22.368 Mpa (见图10)。均小于极限应力150 Mpa,符合要求。
管壳焊缝应力如下云图所示,其中第一处焊缝的最大应力为1.075 Mpa;第二处焊缝的最大应力为10.683 Mpa;第三处焊缝的最大应力为1.610 Mpa;第四处焊缝的最大应力为5.403 Mpa。均小于规定值100 Mpa。
其中,各焊缝所对应各自应力见图11。
4G静力分析主要验证系统在冲击载荷下挂钩的应力和管壳焊缝应力,即当汽车在颠簸路面行驶时受到的载荷会数倍于重力载荷。该系统在4G静力分析下,最大挂钩应力为第一挂钩99.933 Mpa;焊缝的最大应力在第四处焊缝为5.403 Mpa。均在安全范围内。
3. 排气系统的模态分析
在对模型1G、4G进行静力分析后,该模型的结构强度符合要求。由于汽车发动机在启动、行车挂挡时会发生怠速的现象,此时发动机会因为空转而发生严重抖动,导致损坏发动机部件。模态分析主要验证该模型在怠速频率之内没有Z向弯曲模态。
由于排气系统中的动力总成和悬置所具有的动态特性会影响车辆的NVH性能,所以要对其进行优化。首先通过动力总成质心坐标确定质心位置,输入质量、确定惯性矩阵;再确立左、右、后悬置的坐标以及各个方向的刚度值。简化后的动力总成和悬置如图12所示 [5]。
3.1. 模态分析的基本理论
一个多自由度系统的运动微分方程为:
由于该模型系统中的阻尼对模态分析的影响很小,所以在进行模态分析时不考虑阻尼对模型的影响,则使用无阻尼自由振动方程:
3.2. 排气系统的模态分析
由于该排气系统为4缸4冲程发动机,其怠速频率为750 ± 50 r/min,最大转速6000 r/min,通过发动机激励频率计算公式:
其中:f为激励频率,n为发动机转速,s为气缸数,S为发动机冲程数。计算可知怠速时的频率为23.33~26.67 Hz,主要观察这个频率内是否会出现Z向弯曲模态。
通过数据可知,系统约束模态在怠速频率23.33~26.67 Hz附近的模态有7、8两个模态,其中第7模态为一阶Y向弯曲模态;第8模态为二阶X向扭转模态。两个模态均未出现Z向弯曲模态,即在汽车发动机低转速时均不会发生共振 [6] (见表2)。
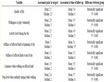
Table 2. Modal distribution of exhaust system at each order within 0~200 Hz
表2. 排气系统在0~200 Hz内各阶模态分布表
4. 结论
使用CATIA建模和HyperMseh构建网格,对某排气系统进行了1G、4G的静力分析和约束模态分析。经过改进和分析均使其满足需求。
1G、4G的静力分析主要论证系统的整体强度。1G静力分析中,一二挂钩的受力较为均匀,第三挂钩由于距离较远所以受力较小,可以通过改变位置使其受力均匀;在4G分析中,对应力过大以及仍要减小其应力的焊缝,可以通过增加焊接、增加壁厚的方式提高焊缝强度。
在模态的分析中,该模型在怠速频率内没有Z向弯曲模态,所以不会产生共振破坏排气系统结构。但由于汽车在行驶过程中会由于路面颠簸而产生振动,并且振动会通过排气系统的挂钩而传递到车内,从而影响整车的NVH性能。所以后续可以通过研究该系统的挂钩动刚度来调整挂钩位置,并对改进后的模型进行静力分析和模态分析来提高整车的性能。
基金项目
柳州市科技计划项目《智能化农牧物流车辆关键技术研究与新产品开发》(2021AAA0115)。
参考文献
NOTES
*第一作者。
#通讯作者。