1. 引言
涡旋压缩机是一种新型高效容积式压缩机,因其结构简单、体积小、容积效率高、噪音低等优点,目前广泛应用于空调、交通运输、电动汽车等领域里 [1] [2]。
苏亚锋 [3] 等通过动平衡理论对涡旋压缩机传动系统进行动平衡设计计算,实现了传动系统的结构优化。邱海飞 [4] 建立传动系统等效力学模型和动平衡方程,借助有限元建模程序,确定了平衡块更加合理的质心位置。赵嫚 [5] 等应用Ansys Workbench有限元分析软件对传动系统进行模态分析,得到传动系统前六阶模态的固有频率和对应振型。张亢 [6] 等压涡旋缩机传动系统进行力学和多体动力学仿真分析,优化了偏心轮结构参数。
本文通过UG软件对涡旋压缩机传动系统结构进行三维建模;为了实现传动系统动平衡设计,通过机械平衡原理在动涡盘底板处减少质量实现一次平衡,通过力学分析在传动系统中添加平衡块来实现二次平衡;通过Ansys Workbench有限元分析软件对平衡后的传动系统进行模态分析,得到传动系统前六阶模态的固有频率和对应振型以及临界转速。验证了该传动系统结构设计的可行性。
2. 材料与方法
本文研究的是涡旋压缩机的传动系统,传动系统是涡旋压缩机的重要组成部分,它影响着压缩机的可靠性、寿命、效率、噪声等各个方面,传动系统由动涡盘组件(动涡盘、动涡盘轴承)、主轴承、副轴承、曲轴、转子、偏心摆套和上、下平衡块组成。各部件材料属性如表1所示。
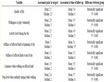
Table 1. Material properties of each component
表1. 各部件材料属性
对于涡旋压缩机传动系统的模态分析,本文提供的研究方法如下:
1) 通过UG软件对涡旋压缩机传动系统结构进行三维建模;
2) 通过计算对涡旋压缩机传动系统结构进行动平衡设计;
3) 通过Ansys Workbench有限元分析软件对涡旋压缩机传动系统进行模态分析,可以提取前六阶的固有频率和对应振型图,能够看出传动系统的薄弱环节;借助坎贝尔图可以知道临界转速,以便于更好的避免共振。
3. 基于UG的涡旋压缩机传动系统几何模型
在涡旋压缩机传动系统中,曲轴的结构是阶梯偏心,在曲轴上安装有动涡盘组件(动涡盘、动涡盘轴承)、主轴承、副轴承、转子、偏心摆套和上下平衡块,在UG软件中分别建立这些零部件的三维模型,在根据实际的运动关系进行装配,组装的传动系统三维模型如图1所示。
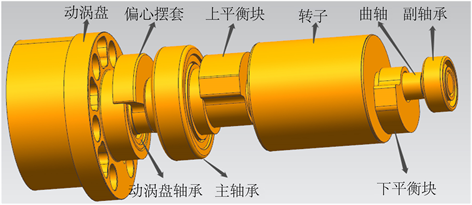
Figure 1. The 3D moder of transmission system of scroll compressor
图1. 涡旋压缩机传动系统三维模型
将这些零部件装配完成之后,还需要用UG软件对装配的模型进行干涉检查,可以检查各零件之间的位置是否装配合理,提高了设计和建模的准确性。
4. 传动系统动平衡设计
涡旋压缩机传动系统的动平衡在涡旋压缩机制造中占有重要的地位,严格的进行动平衡设计可以降低涡旋压缩机的振动和提高涡旋压缩机的安全性、寿命和效率。动平衡设计一般要分为两步:一次平衡和二次平衡。
4.1. 一次平衡
由于动涡盘的设计相对复杂,其质心一般不在动涡盘的基圆中心轴线上,所以需要在动涡盘底板处的一定位置上增加或减少一定的质量,这两种方法分别叫做增加质量法和减少质量法,这样就可以将动涡盘的质心移到基圆中心轴线上,从而实现涡旋压缩机传动系统的一次平衡 [7]。
根据机械平衡原理来平衡动涡盘的偏心质量,将动涡盘简化为如图2所示的模型。
图1中
为动涡盘的偏心质量,
为偏心质量的质心到动涡盘基圆中心的距离,
为增加质量法的平衡质量,
为增加质量法的平衡质量的回转半径,
为减少质量法的平衡质量,
为减少质量法的平衡质量的回转半径。要使动涡盘平衡,根据机械平衡原理可知:
(1)
平衡质量的相位角
为:
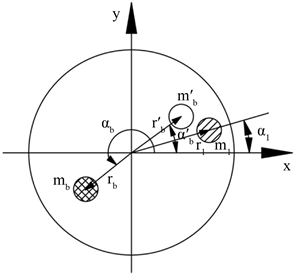
Figure 2. Simplified mechanical model of orbit scroll
图2. 动涡盘简化力学模型
(2)
上述为增加质量法,但是在工程实际应用中增加质量可能会增加部件之间运动的干涉性,为了防止这种情况发生,可以在
的反方向减少一定的质量使动涡盘达到一次平衡,只需要满足
即可。图中
,通过计算可求出在
、
处挖掉一个半径为2 mm、深度为4.2 mm的小圆柱体即可达到一次平衡。对于动涡盘考虑到强量化设计以及防止运动部件之间发生干涉,一般采用减少质量法对动涡盘进行平衡设计,平衡后的动涡盘如图3所示。
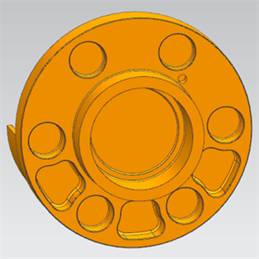
Figure 3. Model of orbit scroll after balancing
图3. 平衡后的动涡盘模型
4.2. 二次平衡
由于动涡盘通过动涡盘轴承偏心布置于曲轴的圆柱销上,因而动涡盘在旋转过程中产生的旋转惯性力必将传递到曲轴上,增加了主轴承和副轴承的负荷,引起压缩机的振动。为了使传动系统动平衡,可以在曲轴特定的位置上布置平衡块,由于结构设计的限制,传动系统偏心部件的旋转惯性力不可能作用在一条直线上,若采用一个平衡块的话,曲轴的惯性力矩得不到平衡,因此至少采用两个平衡块,且这两块平衡块布置角度相差180˚。本文采用两块平衡块来平衡传动系统的旋转惯性力和其力矩,从而实现传动系统的二次平衡。传动系统动平衡受力模型如图4所示。
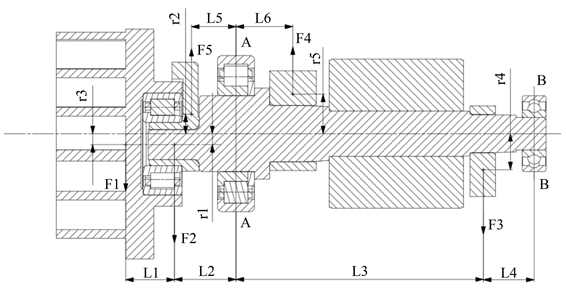
Figure 4. Dynamic balance force model of transmission system
图4. 传动系统动平衡受力模型
根据图4受力分析并通过主轴承中心面A-A和副轴承中心面B-B列出传动系统动平衡方程:
旋转惯性力的平衡:
(3)
力矩的平衡:
A-A面:
(4)
B-B面:
(5)
(6)
式中:F1——动涡盘组件旋转惯性力;
r3——动涡盘组件质心到曲轴中心线的距离;
——曲轴旋转角速度;
m1——动涡盘质量;
m2——动涡盘轴承质量;
(7)
式中:F2——偏心圆柱销旋转惯性力;
r1——偏心圆柱销质心到曲轴中心线的距离;
m3——偏心圆柱销质量;
(8)
式中:F3——下平衡块旋转惯性力;
r4——下平衡块质心到曲轴中心线的距离;
m4——下平衡块质量;
(9)
式中:F4——上平衡块旋转惯性力;
r5——上平衡块质心到曲轴中心线的距离;
m5——上平衡块质量;
(10)
式中:F5——偏心摆套旋转惯性力;
r2——偏心摆套质心到曲轴中心线的距离;
m6——偏心摆套质量;
其他字母含义:
L1——动涡盘组件质心到主轴承中心面A-A的距离;
L2——偏心圆柱销质心到主轴承中心面A-A的距离;
L3——下平衡块质心到主轴承中心面A-A的距离;
L4——下平衡块质心到副轴承中心面B-B的距离;
L5——偏心摆套质心到主轴承中心面A-A的距离;
L6——上平衡块质心到主轴承中心面A-A的距离;
带入相关数据可得:
(11)
(12)
(13)
联立方程并将相关参数代入上述方程中可以求得上平衡块的质量m5为170.17 g和距离L6为26.22 mm、下平衡块的质量m4为99.71 g和距离L4为23.44 mm,通过计算即可达到二次平衡。
通过对动涡盘的一次平衡和传动系统整体的二次平衡,为涡旋压缩机的动平衡提供了理论依据。
5. 模态分析
5.1. 固有频率与模态振型
在模态分析之前需要对传动系统进行简化处理,将动涡盘组件和上、下平衡块简化为集中质量添加在曲轴上,采用bearing约束命令模拟轴承 [8]。涡旋压缩机传动系统简化模型如图5所示。传动系统进行模态分析后可以得到模态振型,从模态振型可以明显看出传动系统对应的固有频率下的振动响应,即变形趋势,变形较大的位置是传动系统的薄弱部分,进行结构优化时应着重对薄弱环节优化。由于模态分析通常只考虑低阶模态频率的固有频率,高阶频率对传动系统影响小,故提取前六阶的传动系统的扩展模态,其频率和对应振型如图6所示。
从图6传动系统前六阶固有频率和相应的振型图可以看出:一阶模态是刚体模态,其固有频率是0 Hz,传动系统没有变形;二阶模态的固有频率是69.524 Hz,在此频率下产生弯曲振动,变形较大的位置出现在副轴承支撑处;三阶模态的固有频率是160.11 Hz,在此频率下产生弯曲振动,变形较大的位置出现在偏心圆柱销处;四阶模态的固有频率是261 Hz,在此频率下产生弯曲振动,变形较大的位置出现在
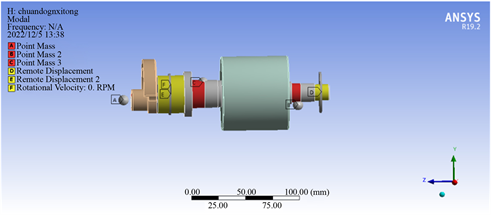
Figure 5. Simplified model of transmission system of scroll compressor
图5. 涡旋压缩机传动系统简化模型
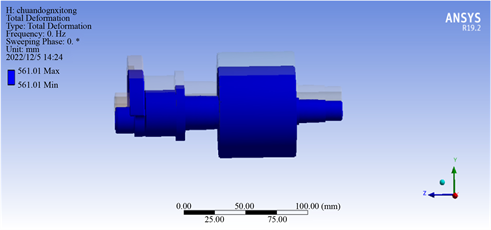
(a)
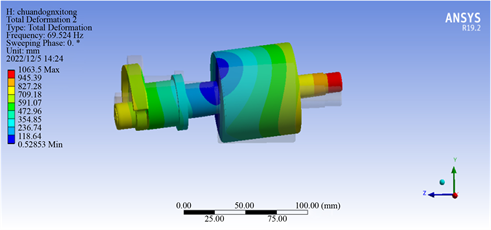
(b)
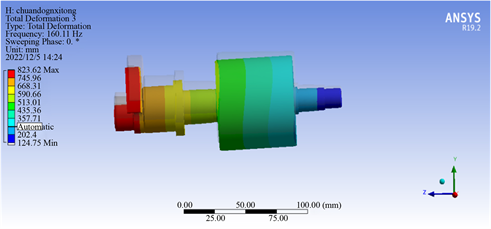
(c)
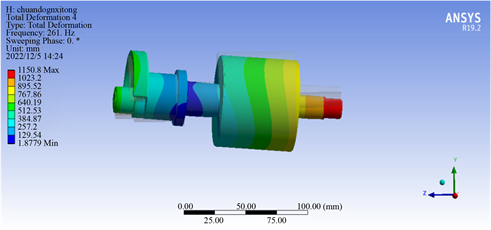
(d)
(e)
(f)
Figure 6. Diagram of the first six natural frequencies and vibration modes of the transmission system. (a) 1-order vibrationmode; (b) 2-order vibrationmode; (c) 3-order vibrationmode; (d) 4-order vibrationmode; (e) 5-order vibrationmode; (f) 6-order vibrationmode
图6. 传动系统前六阶固有频率与振型图。(a) 1阶振型;(b) 2阶振型;(c) 3阶振型;(d) 4阶振型;(e) 5阶振型;(f) 6阶振型
副轴承支撑处;五阶模态的固有频率是2014.4 Hz,变形较大的位置出现在转子处;六阶模态的固有频率是2313.9 Hz,在此频率下产生扭转振动和弯曲振动的复合模态,变形较大的位置出现在副轴承支撑处。另外模态分析中由于传动系统各个节点的位移结果是归一化的,即所有节点相对于某一节点的相对运动,所以仿真提取的模态振型的位移值是没有意义的,查看振型云图时主要观察结构的振型。
通过振型云图可以明显的看出传动系统的薄弱环节,所以在对传动系统结构设计和改进时,应充分考虑这些薄弱部分,通过修改结构可以避免传动系统产生共振。
5.2. 坎贝尔图
借助坎贝尔图可视化与转速有关的频率变化,判断传动系统在各阶模态的稳定性和涡动方向,识别传动系统工作转速中的临界转速,以便于传动系统更好的避免共振。
坎贝尔图是传动系统三维模型的二维表达,传动系统的坎贝尔图如图7所示,其横坐标表示转速(rpm),纵坐标表示固有频率(Hz),图中从原点出发的斜线表示涡动线,其他斜线表示各阶模态转速与固有频率的关系,涡动线与其他斜线的相交点用红色三角形标记,与红色三角形相对应的转速是传动系统的临界转速。
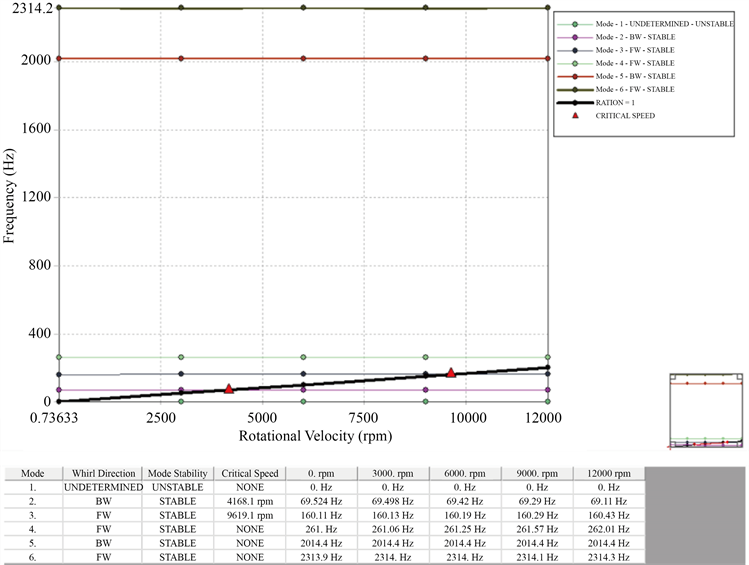
Figure 7. Campbell diagram of the transmission system
图7. 传动系统的坎贝尔图
从图7中看出有两个红色三角形,表示该传动系统有两个临界转速,临界转速分别为4168.1 rpm、9619.1 rpm。在看坎贝尔图中,每阶模态均标记FW (正向涡动)、BW (反向涡动)或Undetermined (待定)的旋转方向。由于临界转速只取决于正向涡动参数,所以该传动系统真正的临界转速是9619.1 rpm。要使传动系统正常工作不产生共振,就必须要求传动系统的工作转速避开临界转速有足够的安全裕度 [9],一般要求传动系统的工作转速小于0.75倍的临界转速。该传动系统的工作转速为0~6000 rpm,0.75倍的临界转速为7214.325 rpm,所以该传动系统不会发生振动,结构设计合理。
6. 结论
本文对传动系统进行动平衡设计和模态分析,得到如下结论:
1) 传动系统动平衡设计需要进行一次平衡和二次平衡。一次平衡就是将动涡盘质心移到中心轴线上,通过在动涡盘底板
、
处挖掉一个半径为2 mm、深度为4.2 mm的小圆柱体即可实现一次平衡;二次平衡就是通过添加平衡块平衡偏心部件的旋转惯性力和其力矩,通过计算可以求得上平衡块的质量m5为170.17 g和距离L6为26.22 mm、下平衡块的质量m4为99.71 g和距离L4为23.44 mm,即可实现二次平衡。为涡旋压缩机动平衡设计提供了理论依据。
2) 通过模态分析即可得到传动系统前六阶固有频率和振型图,通过振型云图可以看出传动系统的薄弱环节,在进行结构设计和改进时,应充分考虑这些薄弱部分,避免传动系统产生共振。为涡旋压缩机的传动系统结构设计提供了理论依据。
3) 通过坎贝尔图可以得到该传动系统的临界转速为9619.1 rpm,由于工作转速小于0.75倍的临界转速,所以该传动系统的结构设计是符合要求的。