1. 引言
相当数量的部件和结构失效是由疲劳载荷引起的 [1] 。疲劳失效是构件和结构在寿命设计阶段应考虑的重要因素之一。在实际工况中,疲劳破坏往往发生在由缺陷引起的应力集中较强的部位,因此如何获取金属内部缺陷信息,建立缺陷与疲劳寿命关系模型的分析已成为人们关注的疲劳寿命问题预测。近些年,大量学者进行了关于铝合金缺陷特征对疲劳损伤的影响研究。ROMANO [2] 等通过实验发现铝合金的最大内部缺陷是疲劳失效的源头;FEDOR [3] 等指出缺陷尺寸并不是决定疲劳失效的唯一因素,即使表面缺陷的尺寸为内部缺陷的五分之一,材料也会产生疲劳失效;宋哲 [4] 等基于X射线成像设备发现铝合金的内部孔隙率随着疲劳拉伸周次的增大而增大,当达到40,076周次时,材料由于孔隙率急剧增加,有效承载面积不断减小导致疲劳断裂。同时,缺陷的形貌越复杂,缺陷边缘的尖端会产生更显著的应力集中。铝合金的疲劳寿命与缺陷的特征参数(体积、位置、形状等)有直接联系。
传统研究中,为寻找细观缺陷变量与铝合金力学性能之间的联系,研究人员都进行了大量的疲劳实验,导致人工和经济成本过高。近些年,机器学习算法在材料领域广泛应用 [5] ,机器学习和人工智能利用概率和统计方法,在实验数据的基础上从过去的经验中学习,以预测更准确的结果。
本文利用缺陷的特征参数作为支持向量机模型的输入参数,预测铝合金材料的疲劳寿命。首先,采用计算机CT扫描技术对不同加载阶段的疲劳试样进行扫描。采用缺陷分布分类方法对Avizo可视化处理的疲劳试件缺陷信息进行分级简化。该方法不仅考虑了微缺陷的大小,还考虑了形状和位置。最后,引入支持向量机算法,利用缺陷形状、尺寸和位置等因素预测疲劳寿命。
2. 缺陷特征数据的获取
2.1. 试件制备
本研究中,试件材料选择6061-T6铝合金。根据美国试验材料学会ASTM E8/E8M-15a标准制备试件,试件的主要化学成分表如表1所示,试件的具体形状及尺寸如图1所示。
2.2. 缺陷信息获取
为获取不同损伤阶段的试件,使用MTS Landmark电液伺服动态测试系统(如图2所示)对铝合金材料试件进行阶段性的疲劳拉伸实验。本次试验将试件从开始加载到疲劳失效设置了5个循环周次(20,000次,40,000次,60,000次,80,000次和100,000次),最终获得不同疲劳损伤阶段的铝合金试件缺陷信息,实验的相关参数见表2。
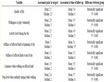
Table 1. Composition of 6061-T6 aluminum alloy
表1. 6061-T6铝合金的成分
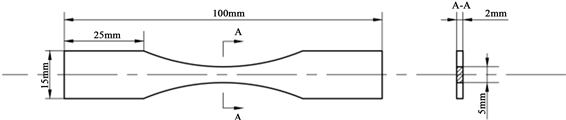
Figure 1. Dimensional of experimental specimen
图1. 实验试件的尺寸图
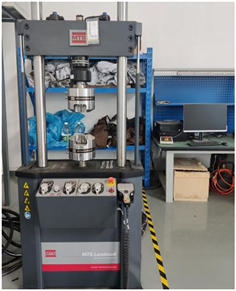
Figure 2. MTS Landmark Electro-hydraulic servo dynamic test system
图2. MTS Landmark电液伺服动态测试系统
然后采用Pheonixv系列的X-CT设备(如图3所示)对疲劳拉伸过后的铝合金试件进行CT扫描,获取到试件扫描区域的TIF图。在X-CT扫描时,X射线会对铝合金试件进行360度扫描,拍摄1600张图片,将拍摄到的图片导入到Visual studio软件中处理,得到TIF切片图像。最后,将TIF图片导入到AVIZO软件进行三维重构,TIF图像的处理流程如图4所示,三维重构的缺陷图像结果如图5所示。
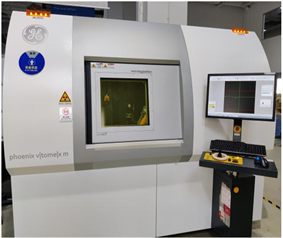
Figure 3. Pheonixv X-ray computed tomography system
图3. Pheonixv X射线计算机断层扫描系统
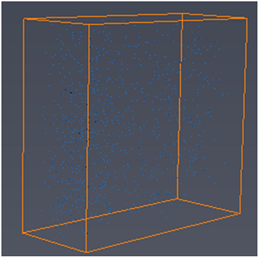
Figure 5. 3D reconstruction of defects
图5. 缺陷的三维重构图
3. 缺陷简化
通过Avizo获取试样的缺陷信息,包括缺陷体积、缺陷表面积和缺陷坐标。由于试件中缺陷较多且形状不规则,对后续建模和分析非常不利,因此有必要建立一个简化的缺陷模型,以便在准确评估实质性损伤的基础上进行建模和分析。首先,缺陷的形状需要简化。本文将缺陷形状简化为旋转椭球,旋转椭球是由一个椭圆围绕它的短轴旋转180度所形成的几何形状。利用Avizo软件得到的缺陷信息可以计算简化后旋转椭球的半长轴a和半长轴b,计算公式如下:
(1)
(2)
旋转椭球的形状可用扁率
表示:
(3)
此外,椭球缺陷的半长轴与应力方向之间的夹角
对疲劳寿命也有一定影响。考虑到材料内部实际缺陷分布的随机性,对每个缺陷赋予一个随机角度(0˚~90˚),模拟缺陷的真实状态,如图6所示。
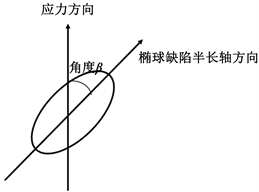
Figure 6. The Angle between the ellipsoidal defect and the stress direction
图6. 椭球缺陷与应力方向的夹角
最后将缺陷信息(体积、表面积、位置)分为表面缺陷、近表面缺陷和内部缺陷。当缺陷体积V和缺陷中心到材料表面的最短距离d满足
[6] 时定义为表面缺陷,当缺陷的表面积S和缺陷中心到材料表面的最短距离d满足
[7] 时定义为内部缺陷,不满足上述关系的均定义为近表面缺陷。不同循环周次的缺陷的变化趋势如图7所示。在加载的初始阶段,内部缺陷会急剧增加;在加载中期,内部的小缺陷相互合并形成较大的缺陷,它们由内部缺陷转变为近表面缺陷。因此,近表面缺陷在这一阶段生长迅速,内部缺陷的数量开始减少。在加载后期,由于体积的增大,一些近表面缺陷变成了表面缺陷,因此这一阶段表面缺陷数量开始迅速增加,而近表面缺陷数量开始减少。
在加载的前期和中期,表面缺陷、近表面缺陷和内部缺陷的总体积都随着加载次数的增加而增加。在后期,内部缺陷中的一些缺陷相互融合形成体积较大而成为次表面缺陷,近表面缺陷中的大体积缺陷由于同样的原因成为表面缺陷,因此后期内部缺陷的总体积会迅速减少,而表面和近表面缺陷的总体积会迅速增加,如图8所示。在加载过程中,各区域缺陷特征信息的变化既不同又相关,证实了缺陷分区预测疲劳寿命的必要性和可行性,因此选取不同位置的缺陷数量和体积作为疲劳寿命预测模型的主要参数。
(a) 表面
(b) 近表面
(c) 内部
Figure 7. Number of defects at different loading stages
图7. 不同加载阶段的缺陷数量
(a) 表面
(b) 近表面
(c) 内部
Figure 8. Defect volume at different loading stages
图8. 不同加载阶段的缺陷体积
4. 疲劳寿命预测模型的建立
4.1. ABAQUS仿真
利用ABAQUS仿真软件对试件的缺陷进行了仿真。试件模型参照CT扫描中试件中心面积,设定为长、宽、高分别为5 mm、2 mm、6 mm的区域,分别对应坐标轴的Y、X、Z轴。将缺陷信息(位置、形状、体积)导入ABAQus软件,生成等效损伤模型。固定模型的一端,在另一端施加应力p,通过仿真得到最大应力点的值
,如图9所示。损伤模型的应力集中系数k可由式(4)得出。不同疲劳周次对应的应力集中系数如图10所示。因此应力集中系数可以作为表征疲劳寿命的参量。
(4)
4.2. 支持向量机(SVR)回归模型
支持向量机(SVR)属于有监督类型的机器学习算法,它可对未知的数据样本有极强的预测能力,对于数据样本点(x, y),传统的回归模型通常直接输出f(x)与真实输出y之间的差别来计算损失,当且仅当f(x)与y完全相同时,误差才为零。SVR假设我们能容忍f(x)与y之间最多有ε的偏差,即仅当f(x)与y之间的差别绝对值大于ε时才计算损失,这相当于以f(x)为中心构建一个宽度为2ε的间隔带,若样本落入此间隔带,则认为是预测正确的,如图11所示。
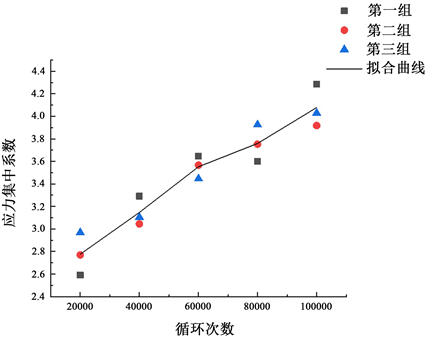
Figure 10. Stress concentration factors of damage models in different fatigue stages
图10. 不同疲劳阶段损伤模型的应力集中系数
SVR回归模型的建立可分为四个步骤,分别是数据预处理(归一化处理)、计算最优初始参数、模型的训练、模型检验,本文采用数据归一化方法对缺陷数据预处理,具体公式为
(5)
式中,max 为缺陷数据样本内的最大值;min为缺陷数据样本内的最小值;x为原始数据;
为预处理后的数据。
SVR算法的数学表达式为
(6)
式中,ω,b,
来自超平面表达式
;y是样本点的值;C为正则化常数;
为损失函数。
在考虑特征映射的情况下,需要引入一个核函数将输入样本映射到另一个高维空间,并使其线性可分。本文采用RBF核函数构建SVR回归模型,其表达式如下:
(7)
本文使用网格搜索算法(Grid Search)选取模型的最优表达式,Grid Search是一种调优方法,在参数列表中进行循环搜索,对每种参数组合进行训练,找到最优的参数。参数 C,g的范围如式(8)和式(9)所示,一共可以得到41 × 41对组合,最佳参数的结果如表3所示。
(8)
(9)
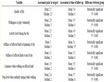
Table 3. Results of parameter selection for SVR model
表3. SVR模型的参数选取结果
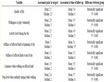
Table 4. Results of R2 for different models
表4. 不同划分方式的R2的结果
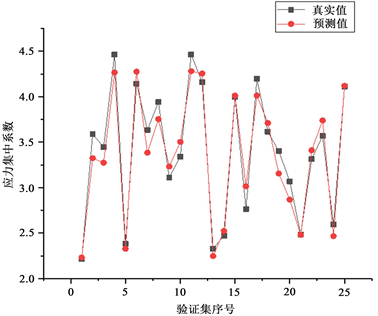
Figure 12. The actual value and predicted value of the test set
图12. 测试集的真实值与预测值
在确定了相关参数后,就可以对SVR预测模型进行训练,将输入输出参数的数据集按照70:30、80:20和90:10的比例随机分为训练数据集和测试数据集。在训练数据集上应用SVR机器学习模型并在测试数据集上对每个训练过的模型进行测试,计算R2决定系数。R2的计算公式如(10)所示。不同模型的R2的结果如表4所示,因此本文采用80:20划分方式训练数据。训练结果如图12所示,根据计算,模型的均方误差mse为0.142,结果表明该SVR预测模型具有较好的预测表现。
(10)
5. 结语
本文首先通过ABAQUS仿真分析,得出了疲劳循环周次与应力集中系数呈线性关系,因此应力集中系数可以作为疲劳寿命的表征参数,借助支持向量回归算法(SVR)建立了不同缺陷特征信息的应力集中系数的预测模型。结果表明,SVR模型能够准确铝合金材料的应力集中系数。