1. 引言
在特种车辆如矿山车辆、沙漠车辆和军用装甲车辆的内燃机上,广泛使用由旋风分离器和油浴过滤器组成的双级重型空气滤清器 [1] 。由于工作环境含尘量或含砂量大,这类空气滤清器的使用寿命很短,一般在10 h~30 h。提高空气滤清器的使用寿命最有效的方法之一是提高预滤器即旋风分离器的分离效率。旋风分离器的核心部件就是旋流管,这样,提高部件的整体效率就归结到提高旋流管单管的效率上来,单管的阻力降低和效率提升则意味着整个旋风分离粗滤器的阻力降低和效率提升,带来空气滤清器系统的阻力降低和效率提升,空气滤清器的容尘能力升高 [2] 。
随着现代重型车辆对进气系统模块化和小型化的需求越来越高,高效紧凑的旋流管技术研究已成为制约高效低阻空气滤清器研究发展的瓶颈。经过多年的发展,国内旋流管的设计水平已经有了长足进步,但研究开发的路线依然处在“仿制 + 试验 + 改进”这一老路线,缺乏对旋流管设计理论的图片与工程应用经验。特别是在一些新型的旋流管如直通翅片式旋流管的设计开发过程中,存在如下几个问题:1) 缺乏对旋流管的工作原理、结构设计以及试验数据的有效整合,没有形成系统完整的直通翅片式旋流管理论计算方法;2) 理论计算方法复杂,设计人员从旋流管的参数设计到性能计算存在着理论计算方法工程化这一难题;3) 如何将理论计算结论、试验结果与旋流管的几何参数及其工况的关系对应起来,始终没有措施。
旋流管的结构参数如进气口尺寸、排气管尺寸、筒体直径、锥体长度及灰斗的尺寸直接影响分离效率。本文从直通翅片式旋流管的工作原理、设计理论出发,构造流场数学模型,整理台架试验和实车测试数据,与理论模型相结合,形成了直通翅片式旋流管的经验设计算法,并应用Visual Studio2015工作环境,对直通翅片式旋流管开发流程进行程序化,形成设计软件,应用软件算法研究了旋流管设计参数对其阻力、效率等性能的影响规律,确定相关参数的最佳取值范围,实现对直通复合旋流管性能的准确计算,达到提升预滤器综合性能的目标。
2. 数学模型的建立
2.1. 直通翅片式旋流管的结构与工作原理
基于某重点预研项目对空气滤清器一级滤清器的技术要求,结合国家合作项目中引进的相关技术,中国北方车辆研究所过滤技术团队开发出一种直通翅片式旋流管,该型旋流管是一种高效旋流管,该管技术先进,具有单管处理风量大,滤清效率高,且在全工作流量范围内能够保持较高的过滤效率的三个显著优点。
该型旋流管主要由旋流管叶片、旋流管中间椎管和旋流管风筒组成。其分解结构见图1。旋流管叶片通过中间锥孔套在旋流管中间椎管上,二者有被旋流管风筒包裹,三者为同轴关系。

Figure 1. Component diagram of straight finned cyclone tube
图1. 直通翅片式旋流管元件图
直通翅片式旋流管的工作机理是利用旋风和格栅复合过滤原理,较传统直通式旋流管相比,应用旋流管中间椎管的格栅取代了原来的出气中心管,含尘空气有旋流管的顶端进入直通翅片式旋流管,首先在旋流管叶片的作用下产生旋流,在旋流的过程中,较大直径即质量较大的粉尘颗粒在旋转气流的作用下径向向外运动并与旋流管风筒内部碰撞,坠落到风筒底部,在旋转流的作用下通过旋流管风筒的切向排尘口排出管外,含尘量较少的空气继续绕旋流管轴心旋转,与旋流管中间椎管的格栅作用,格栅为锥形结构,且开口大小由上到下逐渐减小,这正与灰尘颗粒由上到下逐渐减小相对应,这样,惯性分离后剩余的粉尘颗粒大部分又会被锥形格栅滤除,附着在锥形格栅的外表面,当灰尘附着到一定程度,达到格栅表面粘合能力的极限时,会从格栅表面脱落,形成较大尺寸的灰尘粘结块,这种大质量的粉尘块又会进入到惯性分离的作用范围,被旋转气流从排尘口排出。这样反复作用,透过格栅通过旋流管的气流得到了过滤,且过滤后的干净空气中含尘量低。直通翅片式旋流管工作原理见图2。
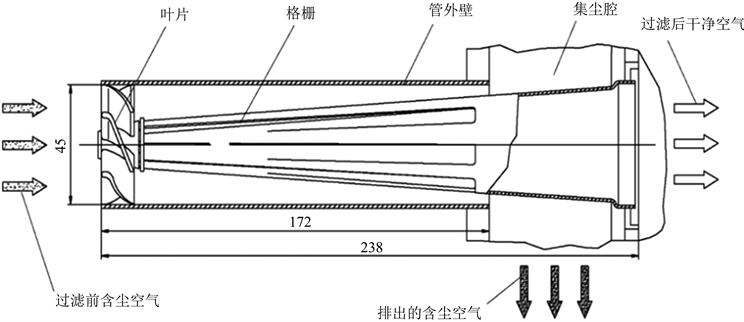
Figure 2. Schematic diagram of filtration process of straight-through finned cyclone tube
图2. 直通翅片式旋流管过滤过程原理图
2.2. 直通翅片式旋流管压降模型
一般来说,旋流管的压降可以分为三个部分:进口损失、分离空间损失、排气管内的损失。如果导流叶片的形状符合空气动力学的条件,进口损失一般较小;旋流管本体中的能量损失比较高,其主要原因在于分离空间限制旋流强度:壁面的摩擦损失越大导致旋流强度越弱。但这部分壁面损失在总压降中并不起支配作用。在直流式和逆流式切向入口的两种旋流管中,升气管中的能量损失所占的比例是最大的。这种损失可能比其他两种损失高一个数量级。
整个旋流管的压降正比于或者非常近似地正比于体积流量的平方,这与所有具有湍流流动的工艺设备中的情况相同。根据CFD和试验检验模型,对于一个光滑器壁的旋流管分离器在第入口浓度下的压降,使用简单的经验公式是足够的。
计算直通翅片式旋流管的性能特性,必须明确直通复合时旋流管的几何要素,确定旋流管的结构参数,经过三维构造分解,直通翅片式旋流管的结构参数如图3所示:
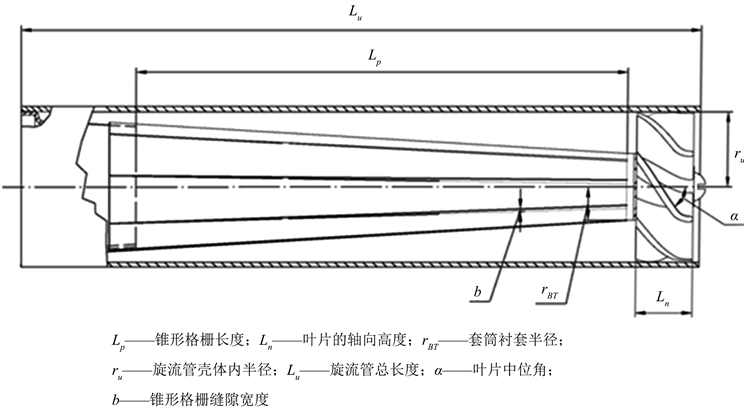
Figure 3. Structural parameter diagram of straight finned cyclone tube
图3. 直通翅片式旋流管结构参数图
根据阐述的旋流管压力降理论基础研究,将直通翅片式旋流管简化为具有筒形壳体的简单旋流管内部流体结构,
阻力计算公式为(1)
(1)
式中:
——旋流管流体阻力;
——旋流管流体阻力系数;
——旋流管入口速度;
——空气密度。
其中,根据直通翅片式旋流管的结构特征,公式中的关键参数—旋流管阻力系数
可以由经验公式(2)确定:
(2)
式中:
——套筒衬套相对半径,
;
——格栅缝隙的相对宽度;
,
;
——叶片中位角;
(3)
——抽尘系数;
——抽尘比例系数,%。
2.3. 直通翅片式旋流管的效率计算数学模型
应用《旋风分离器–原理、设计和工程应用》中关于直通式旋流管的理论总效率计算方法,可以得到直通翅片式旋流管的总效率推导流程 [3] :
A. 按照颗粒粒径分布将试验粉尘划分为N个粒度级的质量组分,每个质量组分之和构成了全部颗粒质量;
B. 用每个质量百分数乘以该组分平均粒径下的捕集效率(分级效率),这个捕集效率是从分级效率计算而得的。
C. 所有N个粒度级组分的总和就是得到总效率。其数学表达式为公式(5):
(4)
式中:
——尺寸为
的颗粒在旋流管内通过效率;
——尺寸为
的颗粒质量百分数。
的颗粒质量百分数函数为公式(5):
(5)
在此基础上,利于斯托克斯公式进行颗粒分级效率计算,具体的计算步骤为:
(6)
式中,
——用于直径为
的颗粒的斯托克斯数,斯托克斯数(Stokesnumber)是一个无量纲数,是颗粒松弛时间和流体特征时间的比,它描述了悬浮在流体中颗粒的行为。这里是颗粒的迟豫时间,是远离障碍物时流体的速度,是障碍物的特征尺寸。斯托克斯数可以简单理解为如下公式:
式中,
——颗粒的放松时间;
——液体通过障碍物时的流速;
——是障碍物的特征量。
当
时,当流线绕过障碍物时,颗粒会依然按直线行驶,直至撞上障碍物。
当
时,颗粒会紧紧随着流线行驶。
斯托克斯数的物理意义是表征着颗粒惯性作用和扩散作用的比值,它的值越小,颗粒惯性越小,越容易跟随流体运动,其扩散作用就越明显;反之,值越大,颗粒惯性越大,颗粒运动的跟随性越不明显。
——旋流管通道内完全分离出的颗粒的最小尺寸,采用δnp标记,与该颗粒尺寸相符的斯托克斯数
称为斯托克斯数极限值。随后,
和
分别由经验公式(7)和(8)求出。
(7)
(8)
与斯托克斯数的极限值相对应的颗粒的尺寸
,按照公式(9)可以确定
(9)
式中,
——通过管流量,
;
——特性速度;
(10)
——结构参数,
;
——旋流管净化空气的质量流量;
——叶片特征系数,
,对于7叶片套筒。
——叶片中位角;
——套筒衬套相对半径,
;
——旋流管等效计算长度,针对直通翅片式旋流管特殊结构,将各影响效率的参数如锥形格栅部分长度Lp,叶片轴向高度Ln和格栅缝隙宽度b进行影响效率的权重分配,结合试验数据确定参数可以由公式(11)确定。
(11)
式中,
——锥形格栅相对长度;
当
时,A = 0.042;
——锥形格栅内缝隙宽度的相对平均值;
——叶片的轴向高度。
以上公式及系数适用的旋流管直径范围为15~90 mm,在该范围内旋流管结构参数优选范围经过推到计算可以初步确定为如下:
3. 直通翅片式旋流管计算程序的构建
基于建立的直通翅片式旋流管数学模型,可以开展直通翅片式旋流管的设计与优化工作。为了使直通翅片式旋流管数学设计算法准确、高效的应用在旋流管的研发过程中,特别是需要将旋流管的几何特性参数,工况和性能计算结果对应起来,并完成各种参数需求下性能结果的快速计算、查询与筛选,对直通翅片式旋流管性能数学计算模型进行了程序化实现。该程序在Windows系统下进行开发,利用通用化数据库开发工具采用Visual Basic6.0语言,计算数据库与试验结果数据库采用Access2010数据库软件进行管理。
3.1. 数学模型程序化设计流程图与计算程序
计算模型程序化工作的第一步是明确计算流程,这也是软件编制的首要工作。经过整理,阻力与效率计算流程分别如图4所示:

Figure 4. Flow chart for calculation of resistance efficiency of straight finned cyclone tube
图4. 直通翅片式旋流管阻力效率计算流程图
主窗体是用户程序操作过程中第一步接触的部分,是软件表象最重要的部分之一,是用户进行人机交互的核心功能区所在,用户可以通过主窗体调用系统相关的全部功能模块,快速实现本系统中所嵌入的各种功能模块。
3.2. 直通翅片式旋流管数学计算模型程序化计算模块
直通翅片式旋流管设计过程数学计算模型程序化的核心是计算模块,其形成过程是将数学模型的几个关键参数输入确定,并将理论公式计算过程进行程序化,形成内部计算内核,嵌套进入软件内部。
计算模块界面简单明了,主要分两大部分,左侧为直通翅片式旋流管关键参数输入,右侧上方为形象的参数说明,通过点击“计算”按钮,右侧下方就可以得到将关键参数带入内核计算程序得到的计算结果并显示出来,结果具有初步筛选功能,对于用户计算得到的有效计算结果,用户可点击“保存数据”按钮,如果计算结果超出合理设计范围,结果不可保存,计算结果及对应的几何参数以及流量工况将被写入数据库,方便用户对历史数据的查询、对比。
软件通过数据库对数据进行管理,并具备查询功能。用户通过程序的计算内核得到了一组有效数据,是由直通翅片式旋流管关键几何参数与管的性能特征量(如旋流管过滤效率、旋流管流体阻力等)组成的,数据被存入数据库中,查询窗体中,用户可以通过8~10单选条件,以及三项复合式选择按钮根据需求进行任意组合设置选择条件,用户可查询前期的计算结果,并将符合同一条件的计算结果列表,用户根据使用要求和布置特点进行结果优选。
4. 直通翅片式旋流管关键参数对旋流管性能影响分析与试验验证
利用直通翅片式旋流管设计特性计算数学模型进行计算,在保持其余参数为定值的条件下,分别得到了直通翅片式旋流管不同的内部结构参数对旋流管性能的影响曲线。几种不同的内部参数分别为旋流管格栅缝隙宽度相对值b、叶片中位角
、套筒衬套半径相对值
以及锥形格栅相对长度
。经过分析,得到几种直通翅片式旋流管关键参数对旋流管压力降的影响曲线如图5所示,对效率的影响曲线如图6所示。
通过以上影响几何特性参数影响性能关系曲线,可以分析得到,在设计旋流管时,对于确定的空间目标值(旋流管长度
和旋流管内径
)和性能目标值(旋流管压力降
和过滤效率
),可以按照曲线结合经验与旋流管加工工艺对其结构参数(锥形格栅相对长度
、锥形格栅内缝隙宽度的相对平均值
、叶片的轴向高度
和叶片中位角
)在优选范围内权衡取值。
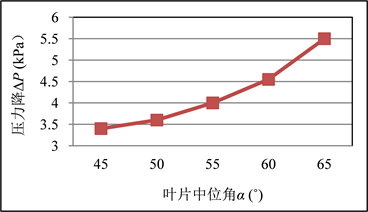
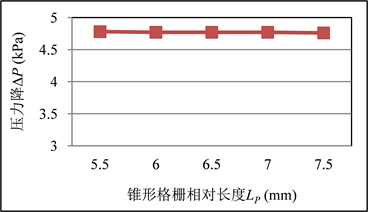
Figure 5. Curve chart of influence of structural parameters on resistance of cyclone tube
图5. 结构参数影响旋流管阻力曲线图
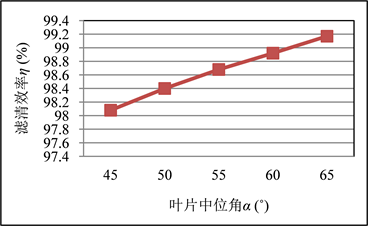

Figure 6. Curve chart of effect of structural parameters on cyclone tube efficiency
图6. 结构参数影响旋流管效率曲线图
为了验证直通翅片式旋流管数学计算模型及程序化软件的有效性,将在旋流管单管性能试验台进行的单管流量–压力降试验的试验值与直通翅片式旋流管设计软件在关键几何参数相同条件下的计算值进行对比,单管流量–压力降对比曲线见图7,同理,应用同一组旋流管几何特征参数加工而成的两个直通翅片式旋流管,应用同一种粉尘在单管性能试验台上进行过滤效率试验,与计算模型程序化软件计算值对比见表1。

Figure 7. Comparison curve of resistance between calculated value and experimental value of swirling tube with different parameters
图7. 不同参数旋流管软件计算值与试验值阻力对比曲线
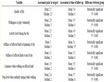
Table 1. Comparison data table of calculated and experimental efficiency values for two types of samples
表1. 两种样品效率计算值与试验值对比数据表
分析图7和表1可以得出,虽然试验件在加工过程中难以避免因受加工环境工艺水平的影响与理论计算值存在着个体差异,但压力降和过滤效率计算结果与试验结果的曲线趋势是一致的,误差在可接受范围内,特别是滤清效率,误差均小于1%,从而可以说明,直通翅片式旋流管的数学特性计算模型是正确且有指导意义的,依据模型可以科学的开展旋流管的设计与优化工作,特别是将数学模型程序化为一种计算直通翅片式旋流管的专用软件后,使得计算过程更加快捷准确,这一计算模块在旋流管设计领域具有重要的应用价值。
5. 结论
旋风分离器单管设计数学模型的推理与提出,并将数学模型的内核算法通过添加人机交互界面、数据计算模块和查询模块等功能进行程序化后,逐步将旋流管的研制过程由原来的“仿制 + 试验 + 改进”转变为“设计 + 试验”,固化了新的旋流管的研制流程、进一步缩短了一级滤清器的开发周期、节约了设计与优化改进过程的直接成本,算法程序化解决了设计人员从旋流管的参数设计到性能计算存在着理论计算方法工程化这一难题,并提供了参数选取空间与影响曲线,提升了元件开发效率、准确地预测旋流管的性能结果、有效指导旋流管设计。通过加工样件在旋流管单管试验台上进行了压力降和效率试验,并与计算结果进行了对比分析,证明了数学模型的正确性和软件的有效性。