1. 引言
盘式制动器是汽车中常见的制动系统之一,用于实现车辆的减速和停车 [1] 。在制动器的设计和开发过程中,模态分析是一种重要的工程工具 [2] ,可以评估制动器结构的振动特性和固有频率。通过模态分析,可以了解制动器在振动条件下的振动模态,从而揭示潜在的振动问题,优化设计,改善系统的动态性能,减少噪音和振动。
为了设计高的性能盘式制动器,高德峰 [3] 采用接触摩擦模型,选取紧急制动工况对制动器的盘、片的热力耦合特性进行仿真与试验分析,为此类研究提供参考;潘公宇 [4] 为了寻找降低抖动的方案,构造出动力学模型,提出了一种对制动卡钳结构和制动块背板结构改进的有效方案;张军 [5] 通过优化制动盘安装连接方式,有效的降低了汽车制动NVH性能;周云泽 [6] 通过软件分析和台架试验对盘式制动器进行复特征值分析和自由模态分析,探讨出系统部件自由模态与摩擦耦合模态的关系;袁琼 [7] 使用三种不同制动模式下的热–机耦合行为进行分析,对制动器不同工况下制动情况研究有较大指导意义。这些研究对制动器不同工况不同尺寸进行了试验分析,为制动器的改进提供了参考,本文主要对某轿车盘式制动器进行约束模态仿真,对其频率和振型进行分析。首先通过建立制动器的有限元模型,然后应用ANSYS软件进行约束模态分析,通过逐渐增加模态阶数,分析了制动器主要零件的固有频率随模态阶数的变化情况,同时对各个零件的固有频率进行比较分析,以评估各个部件之间的共振情况。
2. 结构与材料
本文以某汽车盘式制动器为对象,利用solidworks建立盘式制动器各零部件三维物理模型,包括制动盘、摩擦片、卡钳、支架、转向节等,其结构如图1所示;使用workbench模态分析时定义材料的密度、泊松比和弹性模量,如表1所示。
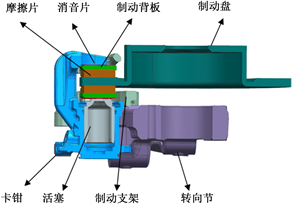
Figure 1. Structure diagram of disc brake
图1. 盘式制动器结构图
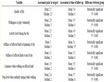
Table 1. Materials of components of disc brake
表1. 盘式制动器部分零部件材料参数
3. 结果与分析
3.1. 前处理
3.1.1. 材料属性
打开Ansys workbench,打开modal模块,将表1中各零部件参数输入workbench工程数据库中,并导入相应的模型中。
3.1.2. 网格划分
双击Model,打开Mechanical界面,然后右击Mesh,将单元尺寸设置成3 mm,单击Generate Mesh,结果如图2所示。其中制动盘生成243,014个节点和153,243个单元,得有限元模型图,如图2(a)所示;摩擦片生成17,077个节点和7902个单元,如图2(b)所示;卡钳生成185,716个节点和109,235个单元,如图2(c)所示;支架生成64,929个节点和36,348个单元,如图2(d)所示;盘式制动器总成生成1,654,307个节点和1,104,617个单元,如图2(e)所示。
31.3. 边界条件
该盘式制动器绕Y轴转动:
1) 根据制动盘的实际安装,对轮毂安装面施加X、Z方向约束;对与摩擦片接触的摩擦面同样施加X、Z方向约束;对制动盘螺纹孔进行全约束。
2) 根据摩擦片的安装情况,将摩擦片与制动背板看成一个整体,对与制动盘接触的摩擦面和卡钳接触的制动背板面施加X、Z方向约束,对四个端面进行全约束;
3) 钳体与支架的螺栓连接处,由于钳体可相对支架做轴向滑动,所以6个自由度中,沿轴向的移动是自由的,即其余5个自由度被约束。
4) 根据实际工况,支架与转向节连接的2个螺栓孔处,其6个自由度全被约束。
3.2. 后处理
由于高阶模态分析容易引起一定的误差,而且高阶模态难以被激励,因此本文提取前6阶的固有频率和振型进行分析。
3.2.1. 制动盘模态分析
求解得到的制动盘模态振型如图3所示。
根据得到的模态振型图和演示动画,制动盘第一阶模态频率为2582.2 Hz,与摩擦片接触的摩擦面振型较大,表现为中心孔固定,盘体轴向运动;第二阶模态频率为4656.3 Hz和第三阶模态频率4696.9 Hz的振型相似,振型分布对称,说明制动盘两侧相对于中心线对折运动;第四阶和第五阶模态频率为8104.5 Hz和8118.8 Hz,表现为两组对折运动;第六阶模态频率为8366.4 Hz,轮毂轴向运动。前六阶模态振型图最大应变都集中在制动盘边缘,故边缘处易产生噪音。
3.2.2. 摩擦盘模态分析
求解得到的摩擦片模态振型如图4所示。
根据得到的模态振型图和演示动画,摩擦片第一阶模态频率为10,660 Hz,表现为制动背板固定,摩擦片中加向轴向挤压产生变形;第二阶和第三阶模态频率分别为17,218 Hz和24,566 Hz,左右存在应变,表现为摩擦片两端弯曲运动;第四阶模态频率为24,693 Hz,摩擦片振型发生弯曲,摩擦片四个角落处应力较大,表现为摩擦片发生对折运动;第五阶和第六阶模态频率分别为30,367 Hz和36,722 Hz,上下存在应变,表现为摩擦片两端弯曲运动;前六阶模态振型图显示,该摩擦片表面总体变形轻微,但四周边缘变化大,易产生振动噪音。对于摩擦片变形轻微可能是由于其采用具有较高弹性模量和刚度的材料,对受到的载荷有很好的抵抗能力,从而在受力时变形较小;而且在设计时,通常会选择足够的厚度,以增加其刚度和稳定性,从而减小变形;在仿真时摩擦片是根据其实际安装情况施加约束,这种约束条件可能会出现偏差从而限制摩擦片的自由变形和振动,使其相对固定,造成四周变形变化大,总体变形小。
3.2.3. 卡钳模态分析
求解得到的卡钳模态振型如图5所示。
根据得到的模态振型图和演示动画,在螺栓位置固定情况下,卡钳第一阶模态频率可忽略不计,表现为沿轴向移动;第二阶模态频率为247.86 Hz,表现为后端钳体处大幅度上下摆动;第三阶模态频率为1085.4 Hz,表现为后端钳体大幅度左右摆动;第四阶模态频率为247.86 Hz,表现绕轴向转动;第五阶模态频率为2551.1 Hz,表现为前端活塞处上下摆动;第六阶模态频率为4111.8 Hz;表现为前端活塞处沿轴向摆动,后端钳体处对折运动。前六阶模态振型图最大应变都集中在活塞和钳体处,易产生噪音。
3.2.4. 支架模态分析
求解得到的支架模态振型如图6所示。
根据得到的模态振型图和演示动画,在下端螺栓孔固定情况下,支架的第一阶模态频率为1012.6 Hz,变现为上端支架绕两螺栓孔上下转动;第二阶和第三阶模态频率分别为1153.6 Hz和1232.1 Hz,表现为上端两支架交错绕螺栓孔上下运动;第四阶模态频率为1333.6 Hz,表现为上端两支架同步上下运动;第五阶模态频率为1619.3 Hz,支架表现为左右发生对折运动;第六阶模态频率为1842.5 Hz,支架表现为绕螺栓孔同步左右摆动。前六阶模态振型图最大应变都集中在支架上端处,易产生噪音。
3.3. 仿真结果对比分析
将通过workbench模态分析得到的各部件前六阶频率如表2所示。
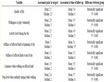
Table 2. Modal frequencies of the primary components of the brake system up to the sixth order
表2. 制动器主要部件前六阶模态频率(Hz)
通过对制动器主要部件进行约束模态分析得知,随着模态阶数的增加,制动器主要零件的固有频率呈递增趋势。从第一阶模态开始,各部件的固有频率存在显著差异,这表明制动盘和摩擦片的模型设计和材料选择较为合理。如果零件的频率接近,易发生共振现象,为避免共振,可通过调整模型尺寸和更换材料的方式改变零件的固有频率。
其中摩擦片通常使用复合材料或金属,高弹性模量的材料会导致较高的模态频率,因为它们更难弯曲或扭转,而且摩擦片通常是相对薄且平坦的结构,其几何形状有助于产生较高的模态频率,相对于其尺寸,因此摩擦片的主要振动模态通常呈现较高的频率。制动卡钳通常具有复杂的几何形状,包括多个弯曲和曲线部分。这种几何形状会导致卡钳的主要振动模态呈现较低的频率,因为它们具有较大的挠度;卡钳一般由金属材料(如铝合金或铸铁)制成,这些材料的弹性模量相对较低,较低的弹性模量意味着较低的刚度,这有助于产生较低的模态频率,因为材料更容易弯曲或扭转。
4. 结论
本研究使用ANSYS软件进行了某轿车盘式制动器的模态仿真分析,可有以下作用:
(1) 结构优化设计:约束模态分析可以用于评估和优化结构系统的振动特性,例如汽车、飞机和建筑等。通过分析不同约束条件下的固有振动频率和模态,可以发现结构中的薄弱部位和共振问题,从而指导设计中的改进措施,提高结构的稳定性和性能。
(2) 预测振动响应:约束模态分析可以帮助预测结构系统在实际使用过程中的振动响应。通过了解不同约束条件下的模态形态和振动频率,可以更好地预测结构在受到外界激励时的响应情况,为结构的可靠性评估和振动控制提供依据。
(3) 避免共振问题:约束模态分析可以帮助设计人员避免共振问题的发生。在约束模态分析中,通过比较不同组件的固有频率,可以确定是否存在共振现象,从而指导材料选择、组件设计和结构调整,以避免共振引起的损坏和不稳定性。
这些分析结果可以为盘式制动器的设计改进和优化提供参考,以提升性能和安全性。未来的研究可以进一步扩展到其他类型的制动器或进行结构动态响应的分析,以进一步完善制动器的设计和性能评估。