1. 引言
近些年来,由于材料技术的发展和突破,也间接带动了材料加工行业的发展,金属板料的折弯技术作为材料成型的基本方法之一,具有使用广泛,生产成本低等特点,广泛应用于各行各业,因此对于金属材料的折弯成型的研究对板料的成型有着重要意义 [1] 。折弯成型是一个复杂的物理过程,这是由折弯材料和成型技术决定的,它包括几何非线性、边界条件的非线性和材料非线性等问题。对于传统的折弯成型,只能初步计算折弯的模型,然后经过大量的试折来保证折弯的精度以保持工件的质量。但是近些年来,随着计算机技术的进步和发展,有限元被大量的应用到材料加工行业 [2] ,它可以更好地模拟材料的成型过程并且极大地减少了材料所带来的成本消耗,每进行一次模拟就相当于在实际加工条件下的一次尝试,它缩短了产品的开发,在材料加工成型方面变的越来越重要。
刘雨生、宋健 [3] 等在V形折弯中通过对中厚板135˚折弯过程进行数值模拟,分析了板料在成形过程中的等效应力应变及其中性层内移现象,测得了应变中性层与几何中间层之间的距离变化;李静 [4] 等通过ABAQUS有限元仿真软件对复合板弯曲成形过程进行仿真模拟,对比分析了不锈钢、铝合金、不锈钢层状金属复合板和单层金属板的弯曲性能,并采用双线性内聚力模型对界面分层损伤进行了研究,得出430不锈钢板承受应力最大,其次为304不锈钢板,3003铝合金板承受应力最小;胡丽华 [5] 等利用ANSYS/LS-DYNA有限元平台对板料的弯曲成形过程进行了模拟,研究了不同弯曲半径对板料成形质量的影响,然后通过LS-PREPOST得到了应力和应变的曲线图;柳建安等 [6] 对板料塑性弯曲时的应力应变状态、变形区的应力和应变数值、最大弯矩及其分布规律进行分析,推导出了V形件自由弯曲时的应力和最大弯矩的计算公式;Graf和Hosford [7] 研究了应变路径对铝合金2008-T4和6111-T4的FLD的影响,得到在不同预应变条件下的成形极限发生不同的显著变化;方刚 [8] 等利用DEFORM有限元软件对不锈钢板料(AISI304)的冲裁工艺进行模拟,材料断裂破坏采用一般破坏准则,分析了冲裁过程中裂纹生成、扩展以及材料断裂分离的过程,冲裁力的变化等。
2. 板料折弯的弹塑性变化
板料的折弯过程是一个弹性变形和塑性变形的叠加过程,它的变形过程可以用如下图1表示,在载荷加载的开始阶段变形较小的时候应变也比较小,可以看到只存在弹性变形,所以弹性模量E为常量,变形呈现出线性变化。然而,当应力超过材料的屈服应力的时候,此时板料的变形就是弹性和塑性变形的叠加状态,所以应力状态从线性变成了非线性状态。最后在载荷卸载后,可以看到弹性应变消失,而塑性变形依然存在。在材料进行单向拉伸的试验中,得到的应力和应变数据一般都称为名义应力和名义应变,然而在进行有限元分析的时候,这些名义应力应变不能进行直接使用,而需要进行一定的转化,有限元中需要的是真实的应力应变来定义出材料的应力应变曲线,名义应力应变到真实应力应变的转化可以通过如下公式进行:
上式中
为真实的应力,
为真实的应变,
为名义应力,
为名义应变。
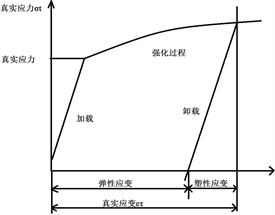
Figure 1. Elastic deformation of the material
图1. 材料的弹性变形
3. 有限元模型的关键技术
通常用于材料成型分析的有限元软件由ABAQUS和ANASYS,它们的适用条件也不同,其中,ANASYS软件常用于线性分析 [9] ,对于非线性问题更好的是选用ABAQUS软件。在材料加工成型时,通常有线性和非线性问题的存在,所以本次的板料折弯就采用ABAQUS有限元来模拟完成,在处理板料折弯回弹模拟的时候一般有两种方式,折弯回弹过程的模拟一般可以采用两种方法,即有模法与无模法.有模法是指在板料折弯成形结束后,控制上模反向运动直至接触消失,这种方法的计算时间较长;无模法是指在板料折弯成形结束后,去除模具并代之以接触反力,直至接触反力减小到零为止 [9] 。由于有模和无模方法对实验模拟的结果并无影响,并且考虑到计算时间的问题,本次实验采用无模法进行模拟实验。
本次使用ABAQUS/Explicit显示求解器来计算板料的折弯成型问题,这是由于ABAQUS的显示算法不存在收敛性等问题,而且计算过程中也不需要构造刚度矩阵,但是在板料的回弹过程中由于非线性等问题,为了更好的模拟回弹所以选择ABAQUS/Standard隐式算法来求解,这样通过显示算法和隐式算法相结合就可以更好的进行回弹模拟 [10] 。
4. 板料的选取和模型的建立
4.1. 材料的选取
此次实验的研究对象为板料,所以对于模具即凸模和凹模定义为刚体,并且也不划分网格,只对板料进行网格划分处理,所使用的材料为304不锈钢,它的材料属性如下表1所示。
4.2. 模型的建立
4.2.1. ABAQUS模型
ABAQUS有限元模型如下图2所示,其中上下部分分别为凸模和凹模,且分别定义为刚体,中间为板料。
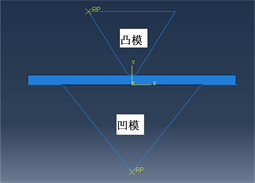
Figure 2. ABAQUS finite element model
图2. ABAQUS有限元模型
4.2.2. 板料的网格划分(图3)
4.2.3. 接触的设置(图4)
4.2.4. 板料折弯处理过程
在进行模拟过程中存在数据的传递,在考虑到在回弹的过程中需要以第一个过程的结束为起始状态,所以直接利用abaqus的重启动来进行第二个状态的模拟 [11] [12] [13] 。
5. 折弯过程中应力变化
5.1. 板料的应力变化
如下图5所示,上模具的进深依次增加,为板料折弯变形的几个不同阶段应力变化云图。从这几个阶段来看,随着板料折弯深度的增加,折弯角度逐渐减小,板料的变形增加。其中,应力最大的地方位于板料的上下两侧,而板料的应力沿边缘向内呈现减小的趋势。与此同时,从板料的中心往板料的左右两侧板料的应力也呈现减小的趋势。当板料完全成型时应力达到最大,且最大应力位于板料上下边缘为648.6 MPa。上模下压量越大,板料的应力沿左右两边有往回收缩的趋势。
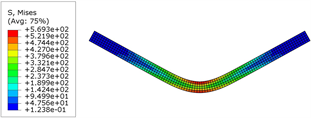
(a) (b)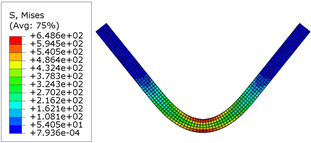
(c) (d)
Figure 5. Stress variations inside the sheet within different stages of bending. (a) Degree of deformation 25%; (b) Degree of deformation 50%; (c) Degree of deformation 75%; (d) Degree of deformation 100%
图5. 折弯不同阶段内板料内部的应力变化。(a) 变形程度25%;(b) 变形程度50%;(c) 变形程度75%;(d) 变形程度100%
如图6所示为分别取板料的上中心边缘、下中心边缘和板料中心的三个点,图7为不同时刻所对应的点的应力变化曲线,可以看出,板料中心上下边缘的应力变化最为剧烈,最高可达到647 Mpa,而板料靠近中心位置的应力不到边缘的一半。图8为不同时刻板料的等效应变变化曲线,节点node 1和node 3及基本上呈现出重合的趋势,板料上下表面受力相同,由此可知,板料的变形程度与板料上下边缘所所受的应力相关。
在刚开始下压的时候由于板料弹性的作用,导致板料上下表面的应力变化最快曲线陡然上升,随着折弯的进行,塑性变形开始出现,从应力曲线变化上可以看出板料应力变化趋于稳定。
5.2. 折弯过程中上模的受力变化
在整个折弯过程中上模在y方向上的受力如下图9所示,可以看到刚开始的上模受力增加的最快,有部分阶段呈现出线性变化,在0.25 s到0.4秒之间上模的受力极不稳定且有减小的趋势,这是因为随着折弯的进行塑性变形开始加剧,有部分弹性转化成塑性,使得弹性力减少,最大受力出位于板料的成型的最终阶段。
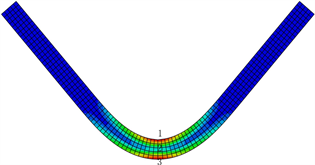
Figure 6. Selected positions of three points on the top, middle and bottom of the sheet
图6. 板料上中下三个点的选取位置
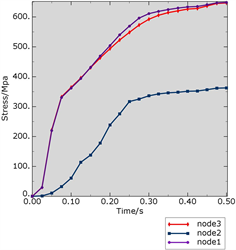
Figure 7. Stress variations at the top, middle and bottom edges of the middle part of the sheet
图7. 板料中间部分的上中下边缘的应力变化
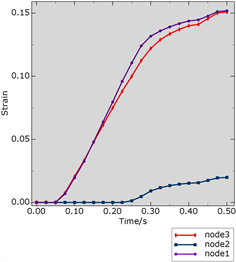
Figure 8. Strain variations at the top, middle and bottom edges of the middle part of the sheet
图8. 板料中间部分的上中下边缘的应变变化
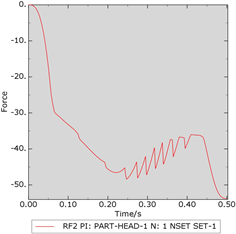
Figure 9. Variation of the force on the upper mold
图9. 上模受力变化
6. 板料回弹时的应力变化
载荷卸载后板料回弹后的应力云图如下图10所示,可以看出回弹过后板料中的应力整体上减小,同时最大应力位置发生了转移,最大应力出现在了板料的中部,与回弹前相比正好相反。图11为图6对应三个点的应力变化曲线图,可以看出上下边缘的即1点和3点的应力急剧下降,下降的曲线在刚开始和时间呈现出线性关系,而最后又有一个轻微的上升。中间点2完全呈现了一个线性的下降,变化缓慢。
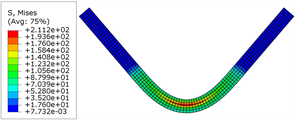
Figure 10. Stress state of the plate after spring back
图10. 板料回弹后的应力状态
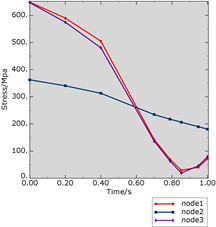
Figure 11. Stress variation at corresponding points during rebound process
图11. 回弹过程中对应点的应力变化图
7. 板料折弯过程中等效塑性应变
下图为板料折弯过程中等效塑性的变化状态,如图12所示,等效塑性变化趋势基本上和板料折弯成形中应力的变化趋势一样,都是随着折弯程度的加深而增大,直到完全成形,板料的塑性变形达到最大,最大的塑性应变达到0.1519。图12等效塑性云图应变云图也可看出随着折弯程度的加深它的塑性变形区域也在增加,它的塑性变形集中在板料和上模的接触部分,其中板料的上表面为压应变,下表面因为受拉力的作用而产生拉应变。从曲线图13可以看出在前几秒板料的中心节点node 2的塑性变形一直为0,而上下表面node 1和node 2的应变一直在增加,这表明塑性变形区域最先出现在靠近板料上表面和下表面的区域而中心区域后出现,并且上下表面的变化趋势相同。
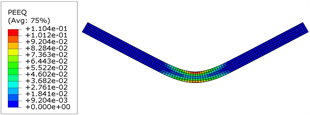
(a) (b)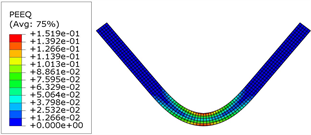
(c) (d)
Figure 12. State change of equivalent plastic strain of sheet material during bending process. (a) 25% distortion; (b) 50% distortion; (c) 75% distortion; (d) 100% distortion
图12. 折弯过程中板料等效塑性应变的状态变化。(a) 变形程度25%;(b) 变形程度50%;(c) 变形程度75%;(d) 变形程度100%
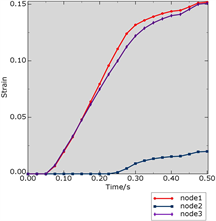
Figure 13. Equivalent plasticity change curves at 3 nodes during the bending and forming process
图13. 折弯成型过程中3个节点的等效塑性变化曲线图
对比图10和图14可以看出,回弹后板料的应力主要集中在板料的中心部位,靠近中性层的部位,而塑性变形却依然集中在板料的上表面和下表面部位。
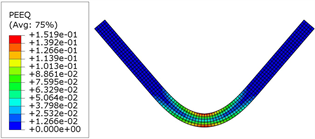
Figure 14. Equivalent plastic change state of plate material after rebound
图14. 回弹后板料的等效塑性变化状态
8. 不同上模对折弯的影响
如图15所示为不同上模圆角半径下在不同下压深度下得到的折弯回弹角变化的变化,可以看出在同一下压量条件下,上模圆角半径越大回弹角反而越小,这是由于在开始折弯的阶段,凸模的两端并未与板料接触,板料两端主要受到凹模的支反力,而折弯变形主要取决于上模与板料的接触部位。在上模折弯加深的过程中板料的两侧逐渐与上模的两边开始接触,由于上模圆角半径越大板料与上模接触的面积就越大,这样导致板料发生的塑性变形就越多,所以它的回弹角就越小,如图16为凸模不同圆角半径下板料折弯回弹后的受力情况。
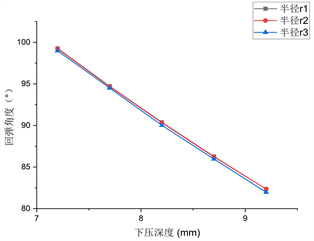
Figure 15. The rebound angle of sheet metal bending under different pressure pressures
图15. 不同下压量下板料折弯的回弹角度
9. 结论
1) 从ABAQUS分析来看,304板料折弯的过程中应力主要集中在板料的上下边缘靠近折弯的部位,板料上下表面的应力的大小变化趋势基本上是一致的,靠近板料中心的部位应力最小。在折弯板料上的载荷卸载的时候,最大应力又最终从板料的上下表面集中到板料中心的折弯角处,并且应力大大减少,减少了60%左右。
(a)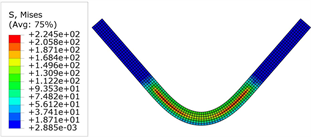
(b) (c)
Figure 16. Stress contour diagram of sheet metal after rebound under different fillet radii when the punch pressure is 9.2 mm. (a) The radius of the punch fillet is 1 mm; (b) The radius of the punch fillet is 2 mm; (c) The radius of the punch fillet is 3 mm
图16. 凸模下压量在9.2 mm时不同圆角半径下板料回弹后的应力云图。(a) 凸模圆角半径为1 mm;(b) 凸模圆角半径为2 mm;(c) 凸模圆角半径为3 mm
2) 载荷卸载后,板料回弹过程中应力呈现出一个按比例减少的趋势,并且上表面和下表面部位减小的最快,基本上减小到了0。对于等效塑性应变,也是增大的,但是可以看到板料中心的节点node 2在刚开始的几秒应变基本不变为0,随后又有一个微量的变化,证明折弯过程是一个从弹性变形到塑性叠加变形的过程。
3) 在板料折弯的过程中,上模受力先是增大而后又因为塑性的作用有一个小的波动,并且整体的受力呈现一个增大的趋势,在最后上模受力达到最大。
在折弯过程中上模圆角半径越大,塑性变形就越大,板料折弯后回弹的角度越小。