1. 引言
航空发动机被形象地描述为飞机的心脏,它的性能和技术水平直接反映了一个国家的工业水平。因此,航空发动机被广泛认为是现代工业的重要支柱。为了提高航空发动机的推力和燃烧效率,则必须提高内部燃烧环境的温度 [1] ,但是目前航空发动机热端部件所用材料的使用温度已经接近极限,意味着金属耐高温性能想要进一步的提高是非常困难的,尤其是发动机火焰筒在工作的时候处于高温高压的环境下,需长时间抵御燃气的灼烧、腐蚀作用,工作环境十分恶劣,致使火焰筒的寿命比起其他发动机零件要短得多 [2] 。因此,开发热障涂层(TBC)新技术作为航空发动机热端部件上的保护结构在如今看来已成大势所趋。
热障涂层(TBC, Thermal Barrier Coating)的概念最早由美国宇航局利维斯研究中心在20世纪50年代提出,旨在提高燃气涡轮叶片和火箭发动机零部件的耐高温和抗腐蚀性能。随后,在60年代,美国宇航局率先将这一技术成功应用于X-15火箭飞机的燃烧室和喷气管上,取得了显著效果 [3] ,如图1所示。经过一段时间的探索,在20世纪80年代初,美国取得了重大突破,为全球热障涂层技术打下坚实的基础。
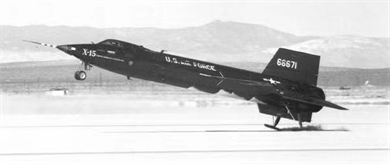
Figure 1. X-15 hypersonic rocket aircraft
图1. X-15超高声速火箭飞机
航空发动机热端部件主要包括涡轮叶片、燃烧室火焰筒、涡轮盘、导向叶片、尾喷管等与高温燃气直接接触的发动机零部件,占航空发动机总重量的40%~60%,航空发动机的主要性能几乎取决于这些热端零部件的性能,所以热障涂层技术作为提高这些零部件性能的关键技术,已经得到了广泛应用,图2所示为涂覆了热障涂层的发动机热端件。热障涂层保护结构可以明显提高发动机所能承受的温度,进一步减少燃料的消耗,提高发动机效率,延长热端部件使用寿命,确保发动机安全及可靠运行,是航空发动机热端部件不可缺少的一种保护结构。本文分别从热障涂层系统结构及材料和热障涂层失效机理两个方面来介绍热障涂层体系及现如今的研究发展状况。
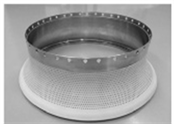
Figure 2. Engine hot end pieces coated with thermal barrier coating [4] [5]
图2. 涂覆了热障涂层的发动机热端件 [4] [5]
2. 热障涂层系统结构及材料
2.1. 热障涂层(TBC)结构阐述
在过去数十年里,热障涂层(TBC)技术得到了很好的发展,结构体系方面发展出双层、多层、梯度等结构形式 [6] ,图3为不同结构的热障涂层简化图。在航空发动机上,常采用双层热障涂层保护结构,是由金属粘结层和高耐热、隔热性好的陶瓷表层组成。这种层合型金属陶瓷复合涂层结构可以有效降低热端部件的工作温度,提高其抗高温、耐腐蚀和抗磨损能力 [7] 。
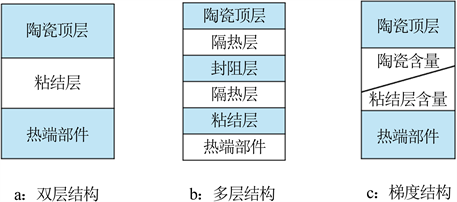
Figure 3. Simplified diagram of thermal barrier coatings with different structures [8]
图3. 不同结构的热障涂层简化图 [8]
在航空发动机热端部件上,常采用等离子喷涂(PS)和电子束物理气相沉积(EB-PVD)这两种先进的技术方法来制备热障涂层保护结构。这些热障涂层通常由耐高温材料组成,以提供对发动机部件的保护,并提高其性能和寿命。目前世界上等离子喷涂技术已相对成熟,可根据设备形式的不同进行细分,如低压等离子喷涂、真空等离子喷涂等。相较于PS工艺,EB-PVD技术具有明显优势,如延长热循环寿命、提高涂层表面光洁度、控制涂层结构更加简便、增强抗氧化和抗热腐蚀性能,并提高涂层结合力等。
热障涂层保护结构主要包括四个部分,具体介绍见表1:
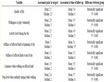
Table 1. Overview of thermal barrier coating protection structures [7]
表1. 热障涂层保护结构概述 [7]
下面两张图片示意了热障涂层微观结构及工作原理,图4为微观下的热障涂层结构,图5为应用于叶片的热障涂层工作原理示意图。
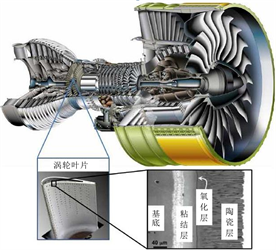
Figure 4. Thermal barrier coating structure in microscopic view [9]
图4. 微观下的热障涂层结构 [9]
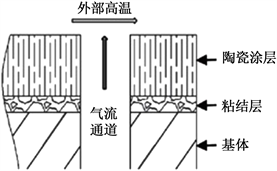
Figure 5. Schematic diagram of the working principle of thermal barrier coatings applied to blades [10]
图5. 应用于叶片的热障涂层工作原理示意图 [10]
2.2. 热障涂层(TBC)——金属粘结层
粘结层一般选取高温合金MCrAlY或高温合金Pt-Al制备,该结构不仅可以减少因材料热膨胀系数不匹配而产生的应力影响,同时其表面易生成Al2O3,而Al2O3正是保护性氧化膜TGO的主要成分,使基体合金的抗氧化性能得到提升,在陶瓷涂层和基体材料之间起了至关重要的作用。
此外,粘结层还起到提高涂层与热端件间物理相容性的基材的作用,充当涂层与热端件之间良好的介质。粘结层的组成对其在热循环过程中形成的热氧化膜性质以及与基体的结合和剥离行为等方面具有至关重要的影响。在热循环中,粘结层应不形成脆性相,同时,能与金属基体形成良好的界面,以减少在零件使用过程中基体和粘结层性能的降低 [3] 。
2.2.1. MCrAlY合金粘结层材料
自上世纪70年代以来,MCrAlY已被广泛应用于航空发动机叶片上的抗氧化防护涂层或者用作热障涂层(TBC)的粘结层 [11] - [17] 。MCrAlY材料具有优异的抗氧化性能和耐热强度,能够有效地保护叶片表面免受高温气流和气体中的氧化物侵蚀。同时,MCrAlY材料的热膨胀系数与基体金属相匹配,有助于降低保护涂层与基体之间的残余应力,提高保护涂层的附着性和稳定性。由于其卓越的性能和可靠性,MCrAlY涂层已经成为航空发动机热端部件首选的合金粘结层材料。这种涂层具有出色的抗氧化、抗热腐蚀和粘附性能,能够有效保护基材并延长部件的使用寿命。在航空航天工业中,MCrAlY涂层已经得到广泛应用,为发动机零部件提供了可靠的保护和性能提升。
M主要有Fe、Ni、Co以及Ni和Co共掺等几种选择;Co可提高界面结合性;Cr含量通常大于20%,含量占比较高,这是因为加入的Cr元素能够促进致密Al2O3层的快速形成,同时提升抗热腐蚀性能;Al元素在工作过程中会与环境中的O2发生反应,并生成一层具有抗氧化能力的Al2O3层;稀土元素Y则在其中起到钉扎氧化物的作用,改善界面结合性,减缓氧化层生成速度,提高粘结层的抗氧化性能 [18] 。在低于1050℃的环境中,MCrAlY涂层表现出优异的抗氧化性能,但在高于1100℃的工作环境下,涂层表面会形成大量以Al2O3为主的热生长氧化层(TGO)。由于TGO层与基体之间存在较大的热膨胀差异,层间会受到较大的压应力累积,同时在TGO-BC (粘结层)界面产生促使涂层界面分离的面外拉应力,导致粘结层界面的变形加速氧化层的断裂 [19] 。图6所示为热障涂层TGO服役后附近区域截面SEM图。
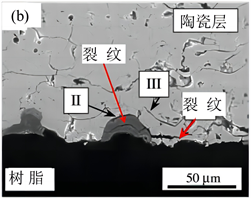
Figure 6. SEM image of cross-section in the vicinity of the thermal barrier coated TGO after service [9]
图6. 热障涂层TGO服役后附近区域截面SEM图 [9]
为了满足更高的使用要求,提升MCrAlY涂层的性能,相关科研工作者对其进行了大量的研究,Andrea等 [20] 通过EB-PVD法分别制备了添加了Hf和Zr的NiCrAlY涂层,研究发现,TBC沉积后TGO的结构和厚度也取决于掺杂含量。稀土元素含量越高,纯Al2O3 TGO和7 YSZ之间的稀土氧化物层越厚、越连续。稀土氧化物开始形成为局部岛屿,当稀土元素含量较低时,并随着掺杂水平的上升而增加数量和大小,当掺杂水平达到0.3 at.% Hf和1.0 at.% Zr时,稀土氧化物层变得连续。与参考物相比,整个TGO厚度(Al2O3 + 稀土氧化物)随着更高的稀土元素含量呈现增加趋势(图7中的圆点虚线),两种RE元素的情况类似,如图8所示。在1100℃的循环测试中,改进过的MCrAlY涂层表现出了明显的寿命延长。Hf的掺杂量在0.15~0.6 at.%时,实现了超过3000次的循环。在0.3 at.%的Zr掺杂量下涂层有着较高的寿命(约2800次),但随着掺杂量的增加,尖晶石的生成量增多,寿命反而会降低,如图7所示。Meng等 [21] 对MCrAlY涂层的表面进行了表面预聚集(SPA)处理。在SPA处理过程中,沉积的氧化铝薄膜在表面形成了大量的平均粒径为200 nm和1 μm的α-Al2O3颗粒。这些α-Al2O3颗粒分别使LPPS和APS涂层的抗氧化性能提高了3倍和8倍。
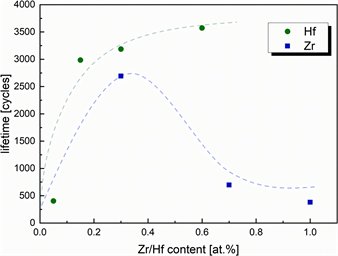
Figure 7. Cycle life versus doping content (at.%) [20]
图7. 循环寿命与掺杂含量(at.%)的关系 [20]
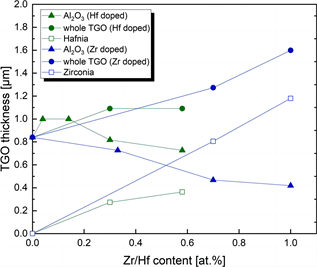
Figure 8. Variation curve of TGO thickness with doping element content [20]
图8. TGO厚度随掺杂元素含量的变化曲线 [20]
目前,改善MCrAlY涂层的微观结构特性和高温氧化行为的方法主要包括各种改性工艺和添加活性元素或其氧化物等。改性工艺涵盖了纳米结晶、SPA (熔喷氧化)、活性元素合金化、ODS改性 [22] 、火花等离子烧结(SPS)、激光处理以及多层或梯度涂层开发等。然而,这些改性工艺大多会增加加工成本,同时部分工艺可能会引起涂层的内部氧化倾向增加、附着力降低以及结构偏移等问题。因此,实现对MCrAlY涂层进行大规模改性并标准化规划仍然具有一定复杂性 [18] 。
2.2.2. Pt-Al合金粘结层材料
另一种用于制备粘结层的材料是Pt-Al,常用于镍基高温合金基体表面。制备方法一般有化学气相沉积法 [23] 或电镀Pt+渗铝法 [24] 这两种方法。Pt-Al粘结层具有优异的高温抗氧化和机械性能,能够提高合金基体的耐热性和抗腐蚀性,因此在航空发动机等高温工作环境下被广泛应用。通过选择合适的制备方法和工艺参数,可以实现Pt-Al粘结层的精密控制和优化,为高温合金的性能提升和部件寿命延长提供重要支持。
在制备过程中,由于Ni的扩散作用,在基体附近形成β-(Ni,Pt)Al相,Pt使涂层与基体之间的元素扩散减少,增强涂层组织的稳定性,使涂层长期保持较高的Al浓度,形成一层稳定的α-Al2O3保护膜,使循环氧化寿命显著延长。该金属粘结层的另一显著优点是具有极佳的高温断裂韧性,粘结层内部的动态再结晶在使用温度超过750℃时,会明显提高涂层的断裂韧性,从而有助于提高涂层的应变容限。但形成大颗粒的β-(Ni,Pt)Al,会导致基体高温合金的抗蠕变性能降低10%~40%。这说明在设计Pt-Al涂层时,需要权衡涂层结构之间的关系,才能使应用效果达到最佳 [24] [25] 。
现如今最常用的粘结层体系是MCrAlY和Pt-Al,这两种体系都具有出色的抗氧化能力。相比于MCrAlY,Pt-Al更适合用于温度更高且对基体力学性能要求较低的叶片。除了以上两种高温合金,其他的高温合金也非常具有应用价值,例如NiAl中含有较高的铝元素,在1200℃及以上的高温下能够形成稳定、平整的保护性氧化膜,因此被认为是未来新一代高温合金叶片的候选粘结层材料之一。
综合来看,不同的金属粘结层材料在涂层领域各有优劣,需要根据具体的使用情况选择适合自己的材质。MCrAlY涂层具有优异的氧化和热腐蚀抗性,适用于要求高循环寿命和抗蠕变性能的场合 [3] 。而Pt-Al合金具有很好的高温断裂韧性和氧化寿命延长效果,适用于要求高温下涂层稳定性和良好的断裂性能的场合 [3] 。在选择金属粘结层材料时,需要考虑到涂层的性能要求、使用条件、成本等因素,综合权衡各种因素才能选择到最适合的材料。此外,改性合金的研究和应用也为提高涂层性能提供了新的方向,可以通过改变合金成分和工艺来优化涂层的性能,提高其在高温环境下的稳定性和耐受性。因此,在实际工程中,需要根据具体情况灵活运用不同的金属粘结层材料,以满足不同的使用需求,最大限度地发挥涂层的保护效果,确保所涂层材料的高效稳定运行。
2.3. 热障涂层(TBC)——陶瓷面层
热障涂层保护结构中的陶瓷面层,主要功能是减少热量传导,并具有抗高温氧化和耐热腐蚀的特性。这种涂层材料通常具有较高的熔点、较低的密度、低导热率和高热发射率,并与基材的热膨胀系数相匹配。常用6%~8%氧化钇(Y2O3)部分稳定氧化锆(ZrO2)来制备。
为了改善YSZ的热物理性能,研究人员正在尝试通过单一或共混添加稀土氧化物和其他氧化物来提高其性能。
2.3.1. 单元素掺杂改性YSZ涂层陶瓷材料
稀土氧化物R2O3 (其中R为La至Lu、Sc、Gd等)改性YSZ (氧化钇部分稳定的氧化锆)是目前研究较多的一种改性方法。其中,Sc3+是一种常用的稀土改性元素 [26] [27] ,其离子半径与Zr4+相近,有助于提高YSZ的结构稳定性和性能。Leoni M等人 [26] 的研究表明,在YSZ中加入适量的Sc2O3可以显著提高其在高温下的相稳定性。具体实验结果显示,含有6.57% Sc2O3、1.00% Y2O3和氧化锆的材料在1400摄氏度热处理100小时后,再在1480摄氏度下处理24小时,仍然保持了96.7%的亚稳态四方相结构 [26] ,图9为1600摄氏度下烧结24小时的掺杂改性YSZ材料的相分析。这表明Sc2O3的加入可以有效增强YSZ的相稳定性,延长其在高温下的使用寿命,并提高其耐高温氧化和腐蚀性能。因此,稀土氧化物R2O3改性YSZ是一种有潜力的改性方法,可以通过调节稀土氧化物的种类和含量,优化和改进YSZ的结构和性能,为陶瓷材料在高温环境下的应用提供更好的保护和稳定性。

Figure 9. Phase analysis results of doped modified YSZ materials sintered at 1600 degrees Celsius for 24 hours [28]
图9. 1600摄氏度下烧结24小时的掺杂改性YSZ材料相分析结果 [28]
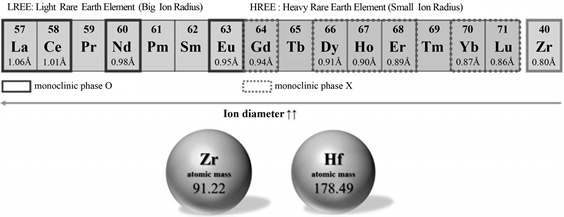
Figure 10. (a) Relationship between radius size and monoclinic phase formation for additive rare earth ions; (b) Atomic mass difference between Zr and Hf [28]
图10. (a) 添加剂稀土离子的半径大小与单斜相形成之间的关系;(b) Zr和Hf的原子质量差 [28]
掺杂元素会对YSZ涂层的热物理性质产生显著影响。当掺杂元素的离子半径与Zr4+有较大差异时,会造成晶格畸变,从而使YSZ涂层的导热性能烧结性能得到优化,但同时也会使涂层的力学性能减弱。而当掺杂元素的离子半径与Zr4+接近时,YSZ涂层在高温稳定性方面表现出色。此外,当改性元素的离子半径小于Zr4+时,涂层的结合强度也会明显提高 [18] 。Raghavan等 [29] 的研究结果表明,对于各种氧化物,随着阳离子的半径从Sc3+到Y3+的增大,稳定能力会增强。这意味着当阳离子的半径逐渐增大时,氧化物的稳定性也会相应提高。然而,随着阳离子半径从Y3+到La3+的进一步增大,稳定能力则会下降。这说明在一定范围内,阳离子的半径大小对氧化物的稳定性有着显著影响,且存在一个最佳的半径范围,超出此范围可能导致稳定性的降低。因此,在设计和选择改性元素时,需要综合考虑离子半径对YSZ涂层性能的影响。合适的掺杂元素可以优化YSZ涂层的热物理性能,提高其在高温环境下的稳定性和耐久性,同时维持其力学性能。这对于提高涂层的性能和延长其使用寿命具有重要意义。图10所示为添加剂稀土离子的半径大小与单斜相形成之间的关系、Zr和Hf的原子质量差。
2.3.2. 多元素掺杂改性YSZ涂层陶瓷材料
采用多元稀土元素共同掺杂ZrO2,不仅能降低热障涂层的导热性能,还能使材料的相稳定性、抗烧结性等性能得到维持甚至提高,从而对稀土元素单一掺杂所带来的性能劣势进行部分弥补。此外,多元素掺杂也有可能获得高温稳定性较好的亚稳态t相,使YSZ综合性能得到大幅提升,目前该材料已成为当前研究YSZ改性的热点。
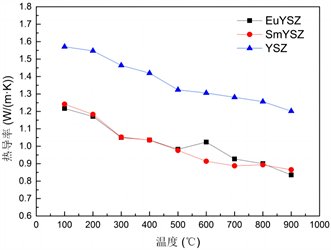
Figure 11. Thermal conductivity of three different ceramic layers of YSZ, EuYSZ, SmYSZ [30]
图11. YSZ、EuYSZ、SmYSZ三种不同的陶瓷层的热导率 [30]
在中国民航大学李尧 [30] 的研究中,利用大气等离子喷涂技术制备了YSZ涂层、EuYSZ涂层和SmYSZ涂层。研究结果表明,在温度升高的情况下,这三种涂料的热导率在100℃至900℃的范围内都会降低。其中,EuYSZ的热导率(1.21657 W/(m∙K)~0.83525 W/(m∙K))明显低于YSZ的(1.57065 W/(m∙K)~1.20141 W/(m∙K)),降幅约30%。SmYSZ的热导率(1.24167 W/(m∙k)~0.86519 W/(m∙k))较YSZ的热导率明显下降,降幅约为28%,如图11所示。W. Fan等 [31] 研究结论表明,在含氧量相同的样品中,如果Sc3+与Zr4+的离子质量差值大于Y3+与Zr4+,不论是理论计算值还是试验测量值,Sc2O3-Y2O3-ZrO2材料热导率均要比6 wt.%~8 wt.% Y2O3-ZrO2低20%~28%。Shen Y等 [32] 结论表明,Ta2O5和Y2O3共同掺杂ZrO2,不仅可以降低材料热导率,还能通过中和晶格内的氧空缺,对TGO的生长起到抑制作用。Wang Y等人的结论表明,通过等离子喷涂在大气中制备的Gd2O3掺杂YSZ涂层,不仅能保证热导率下降,还能提高抗烧结性 [33] [34] 。由此可见,多元稀土元素掺杂ZrO2可以很好地降低热障涂层的导热性能,使YSZ材料具有更好的性能表现。随着科学研究的不断进步,相信多元素掺杂改性YSZ陶瓷材料将在未来被广泛应用于更多领域。通过多元素掺杂优化材料的性能和功能,提高其热稳定性和机械性能,使其适用于更广泛的应用场景,这或许将为材料科学和工程领域带来新的发展机遇和可能性。
3. 热障涂层(TBC)失效机理
飞机发动机叶片在工作环境中受到高温、高压、高速颗粒冲击、环境颗粒侵蚀等多种复合因素影响。此外,隔热涂层体系中存在多个界面,不同外部条件下会导致涂层产生各种应力,最终导致涂层失效。隔热涂层的失效是一种三维断裂现象,可以通过使用二维模型来描述。如图12所示。数值分析和建模对研究隔热涂层(TBC)的可靠性和耐久性方面起着重要作用,特别是有限元模型在探究TBC的隔热性能和断裂破坏机制方面具有高效性 [35] 。例如GuoDun等 [36] 通过有限元法研究了CMAS渗透对使用EB-PVD技术制备的TBC中残余应力和界面裂纹扩展的影响。杜浩等 [37] 通过应用生死单元法和建立双层TGO扩散-氧化生长模型,研究了双层TGO生长对热障涂层界面失效的影响。王士峰等 [38] 利用代表体积单元法构建了NiCoCrAlY/YSZ梯度热障涂层的二维微观有限元模型,分析了梯度层在不同相成分配比下的热物理性能参数,进而将参数推广到三维多层涂层的实体模型中,研究了双层结构涂层和梯度结构涂层在热循环过程中的热力学性能。
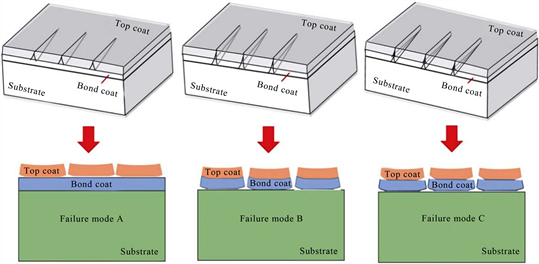
Figure 12. Coating failure mode schematic [35]
图12. 涂层失效模式示意图 [35]
航空发动机热端部件普遍采用热障涂层防护技术以增强其耐高温能力,然而其失效机制是复杂且多变的。主要表现为涂层的破损与剥离,该现象在受控的实验条件下往往与热生长氧化层(TGO)的发展密切相关。然而,在现实运转条件下,燃气中携带的微小杂质如CaO、MgO、Al2O3、SiO2等与涂层发生复杂作用,特别是这些微粒构成的熔融沉积物(CMAS)与Y2O3反应,导致涂层性能降低,从而缩短其使用寿命。此外,高温环境下的气流中携带的微粒冲击涂层,也是导致涂层损伤的重要因素。在此情形下,TGO界面受到的面外力的增加,会促进界面缺陷的形成,并加速涂层的脱落。
随着温度的提高,热障涂层正在面临一个新的挑战,即需要着手解决熔融硅酸盐腐蚀的问题 [39] [40] [41] 。在特定的航空条件下,如高灰尘环境、低飞行高度或海军飞机的低空巡航任务,必须关注由CMAS和硫酸盐沉积引起的涂层失效问题。CMAS对黏结层Y2O3的腐蚀作用,会诱发ZrO2的高温相变,引起涂层体积变化,最终导致涂层的破碎和剥离。此外,CMAS的渗透会导致涂层的逐步消耗,进一步降低其应变容忍度。熔融硫酸盐的沉积对涂层的破坏机制与CMAS相似。郭磊等 [42] 针对Y2O3部分稳定的ZrO2 (YSZ)热障涂层在不同熔融硅酸盐作用下的腐蚀行为对比研究表明,在研究选取的CMAS、CMAS + NaVO3、CMAS + 海盐三种不同的熔体中,CMAS + 海盐熔体是对热障涂层内部渗透能力最强的,在经过1250℃热处理4 h后,可以发现其对热障涂层的渗透深度已经超过400 μm。其原因大概可归结为CMAS自身的性质会因盐类的加入而发生改变,增强了原本熔体对于热障涂层的渗透能力,进而导致涂层内部甚至底部结构失效。天津大学辛会 [43] 的研究指出,CN对于热障涂层来说是一个不可忽视的隐患,当10 wt.%的NaVO3混入,不仅会导致热障涂层熔融温度下降50℃左右,还会使涂层的粘度降低。上海交通大学毋敌 [44] 的研究进一步发现不同YO1.5含量的YSZ材料都存在优先晶界腐蚀,致使8YSZ材料相比于其他材料表现出较差的CMAS腐蚀抗力,在8YSZ材料中CMAS腐蚀速率大约为15 µm/h。
烧结现象在温度高于1373 K时尤为显著,导致陶瓷层内部柱状晶体的形态发生根本性变化,晶体间连接加强,导致整个陶瓷层弹性模量的提升。这种结构变化伴随着柱状晶体簇的体积收缩,形成纵向的裂缝,增强了TGO界面的面外应力,加速了界面缺陷的扩展及涂层的脱落,如图13所示。因此寻找到抗烧结性能良好的材料至关重要,Saruhan等 [45] 对比研究了采用EB-PVD技术制备的LZ涂层的抗烧结能力。研究结果表明,同时在1373 K温度下煅烧100 h的条件下,LZ涂层的比表面积降低了0.86%,而8YSZ涂层降低了0.94%。这意味着LZ涂层在高温条件下能够更好地保持其比表面积,从而具有更好的保护效果。这一结论有助于指导材料科学领域中对涂层材料的选择和设计 [46] 。Lehmann [47] 通过研究发现,稀土离子取代La对热膨胀系数的影响并不完全符合随着原子序数增加而键能降低的规律。举例来说,LaEuZr2O7的热膨胀系数先增后减,其峰值为10.6 × 10−6/K;Nd2Zr2O7的热膨胀系数则先减后增,峰值为9.6 × 10−6/K;而Gd2Zr2O7的热膨胀系数则呈线性增加,峰值为10.4 × 10−6/K。其他离子的取代也会对热膨胀系数产生影响,甚至会导致其形成杂质相,尤其是当取代量较低时会不利于P-结构的稳定。这表明稀土离子取代对热膨胀系数的影响具有一定的复杂性,需要进行深入研究以更好地理解这种影响。
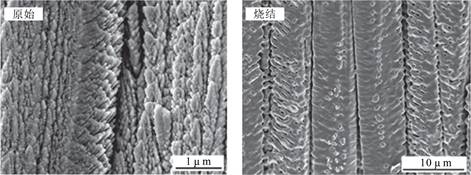
Figure 13. Comparison of feather shape before and after sintering of EB-PVD ceramic layer [48]
图13. EB-PVD陶瓷层烧结前后羽毛形状对比图 [48]
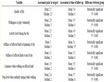
Table 2. Two types of FOD [49]
表2. FOD的两种类型 [49]
颗粒冲击损伤通常发生在高压涡轮叶片的前缘,尤其是当颗粒直径超过100微米时,其破坏力尤为显著。颗粒的撞击不仅会侵蚀涂层,也会加剧涂层的剥落,对发动机性能构成严重威胁。在材料损伤体系中,颗粒冲击诱发的失效现象多样,涵盖微粒腐蚀、塑性变形损害及异物撞击(FOD)等模式。尤其是FOD,它涉及中速大质量颗粒或高速微粒对涂层的冲击破坏,阈值为塑性损害,并可能伴随高应变冲击过程中诱生的横向及剪切型裂纹,正如图14的展示。在所有冲击损害类型中,FOD的破坏性最为突出。Wellman等 [49] 通过冲蚀实验进一步研究了这种模式,并总结出了两种不同类型的FOD,见表2,图15为EB-PVD涂层冲蚀模式的SEM图。
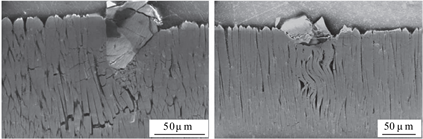
Figure 14. Example of FOD destruction by TBC [50]
图14. TBC的FOD破坏示例 [50]
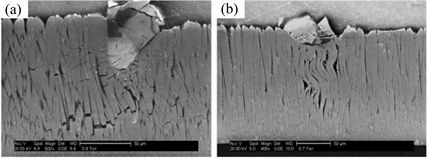
Figure 15. SEM images of EB-PVD coating erosion patterns [51] : (a) Room temperature; (b) 800˚C
图15. EB-PVD涂层冲蚀模式的SEM图 [51] :(a) 常温;(b) 800℃
在热障涂层的失效机制研究中,热生长氧化层(TGO)的形成被认为是决定涂层寿命的核心因素 [52] 。此外,烧结现象、循环加速热冲击(CAMS)以及颗粒冲击,共同制约涂层的实际应用环境及其寿命 [52] 。失效机制研究通过对各种失效机理的模型进行深入分析,可以揭示热障涂层在实际使用条件下出现问题的根本原因,从而指导工程师们改进涂层设计和制备工艺,延长涂层的使用寿命。例如,对TGO的形成机制可以建立各种数学模型,考虑不同的氧化反应动力学、温度梯度和材料性质等因素,以预测TGO的厚度和生长速率。对烧结现象的研究可以建立热力学和相变模型,探讨涂层在高温下的结构演变和稳定性。颗粒冲击引起的涂层剥落和裂纹形成可以通过有限元分析等方法进行模拟,评估涂层的损伤程度和寿命。
因此,深入分析各种失效机制的模型研究在热障涂层技术领域具有重要意义,可以推动该领域的进一步发展和应用。失效机制机理研究结果不仅有助于深化对涂层失效机制的理解,也为设计和优化热障涂层提供了重要的理论指导和实践参考。
4. 结论
随着航空工业的不断进步,航空发动机需要持续提升性能,涉及轻量化、推重比和长时间服役等方面的要求。这将对保护热端部件的技术提出更高要求。热障涂层作为关键技术之一,需要进行各方面的研究以满足这些新需求。未来,我们应该重视TBC材料方面的研究,探索新型优良材料的研发,同时建立涂层失效理论和模型。这将有助于提高热障涂层的性能和可靠性,以应对航空发动机性能提升的挑战,推动航空工业的进步和发展。以下两个方面是对TBC技术的展望。
在材料研究方面,金属粘结层和陶瓷面层的研究将会成为热点,在目前看来热障涂层的研究主要集中在MCrAl合金、Pt-Al合金、单元素掺杂改性YSZ涂层陶瓷材料、多元素掺杂改性YSZ涂层陶瓷材料的掺杂改性,对改性后的材料进行处理,以及对相关结构的调整。但是随着航空发动机领域的快速发展,现如今的金属粘结层材料和陶瓷面层性能逐渐逼近极限,所以开发新的粘结层材料体系和陶瓷面层体系势在必行,以满足航空发动机热端部件需求。
在失效分析方面,由于热障涂层应用过程中,不同类型的失效现象常常发生,因此深入研究这些失效机理对于改进涂层设计和确立涂层性能评价标准具有重要意义。而在计算机仿真技术快速发展的背景下,数值分析和有限元模拟等方法在研究热障涂层(TBC)失效方面扮演着关键角色,有助于揭示失效的原因和评估涂层的性能表现。
综上所述,在未来,我们应该重视TBC材料方面的研究,探索新型优良材料的研发,同时建立涂层失效理论和模型,帮助我们深入洞察TBC系统中涂层失效的机制和模式,为开发更耐高温、可靠性更强的材料提供重要指导,从而推动航空发动机等高温部件的性能和寿命提升。