1. 引言
世界各国普遍认识到:为了避免全球极端天气带来的威胁,人类需要关掉持续排放温室气体的“水龙头”,并在本世纪末实现将每年向全球大气排放510 × 108吨CO2当量的温室气体“净零”排放 [1] 。迫于现实环境的压力和政府的号召下,可持续发展成为当今社会的必由之路 [2] [3] 。太阳能热发电技术的发展大大减少了对于化石能源的依赖,已被很多国家和地区开发利用。但在利用太阳能的过程中存在间歇性、不能稳定持续地供应热量,储能技术是解决这一问题的有效方式 [4] 。在显热储存技术中,熔盐体系具有良好的应用,特别是多元混合熔盐,具有高温蒸气压低,且价格便宜的特点。研发具有熔点低、腐蚀性低、稳定性好、温度范围广和价格低廉等优点的熔盐体系,仍是优化太阳能光热发电技术的重要途径 [5] [6] 。潜热储存技术是基于材料的相变过程,拥有相变温度趋向于定温、能量密度较高的特点。热化学储能技术可分为几种不同的体系,例如金属氢化物体系 [7] 、氧化还原体系 [8] 、有机物热化学体系 [9] 、碳酸盐体系 [10] 和氨基体系 [11] 等 [12] [13] 。与潜热和显热两种储能方法相比较,热化学储能技术(Thermochemical energy storage, TCES)具有储能密度高,可以长时间储存热量,并且热量损失小,满足远距离运输要求等优点 [14] [15] [16] [17] 。
Ca(OH)2/CaO是一种较为成熟的TCES体系,其工作温度一般在623.15~723.15 K之间。在吸热过程中,热量通过传热流体(Heat transfer fluid,HTF)从太阳能发电塔传递到TCES反应器,触发Ca(OH)2吸热分解成CaO和水 [18] ,如式(1)正向反应所示。在放热过程中,CaO与水的反应产生的热量,由HTF输送到电站,供发电机组使用。蒸汽作为反应物,由蒸汽发生器产生,通过压缩机输送到反应床中与CaO发生反应 [19] [20] [21] [22] [23] ,如式(1)逆向反应所示。
(1)
在对于反应过程的研究中,Yan等 [24] 研究了在脱水过程中,脱水温度对于放热过程的影响。为了把CaO重新变回Ca(OH)2,体系温度需要达到900℃,但在该过程中反应物会产生烧结现象,内部的多孔结构会遭到破坏,不利于水蒸气的吸附。因此,Yan等提出了一种解决方法,即在进行一个高温的储/放热反应循环后,再进行一个低温的反应循环,从而使反应物重新恢复多孔结构。Dai等 [25] 研究了Ca(OH)2/CaO体系的热化学储能反应器在20次循环中的储/放热特性。研究发现,在放热过程中,当温度达到510℃时,总吸热量开始缓慢地增加,在50到180分钟时间段内,吸热量快速增长,达到1318 kJ/kg。在研究翅片对于反应器传热性能的影响时,通常使用数值模拟的方法。Wang等 [26] 将圆柱形板翅片和半圆柱型板翅片安装在板式反应器的热载流体通道内。在多孔率0.5的条件下,水解反应时间减少了33%,水合反应时间没有明显变化。在多孔率0.8的条件下,脱水反应没有明显变化,但在水合反应中,由于热载流体和反应床层的温差变大,反应时间减少了20%。
本文中,采用数值模拟方法,着重研究反应器内部载热流体通道内翅片排布对Ca(OH)2/CaO体系储/放热过程的影响。探讨了翅片结构对储能系统的水解反应、水合反应过程的影响和热流密度与压降的影响,为促进Ca(OH)2/CaO体系在热化学储能系统中的发展提供理论指导和借鉴。
2. 反应器几何建模
本文的反应器几何模型以Wang等 [27] 的研究作为基础,具体结构如图1~3所示。对两种翅片结构形式的反应器进行COMSOL建模。在第一种反应器中(交错式翅片反应器),翅片交错、垂直地分布于热载流体流道两侧,第一个翅片位于沿流动方向距离入口位置5 mm处,同侧翅片间距20 mm,与对向翅片的水平间距为10 mm。反应器上下两侧为反应床层,其中载入Ca(OH)2/CaO颗粒。在储热过程中,空气通入热载流体通道,热量通过金属壁面传入反应床层。反应床内的CaO/Ca(OH)2颗粒与通入的水蒸气接触,Ca(OH)2受热分解为CaO和H2O,热量以化学能的形式被存储在反应生成物中。在放热过程中,热载流体通道和反应床层同样分别通入空气和水蒸气,CaO能够水合成Ca(OH)2,并在过程中释放热量,同时将热量传递给中间流道的热载流体 [27] 。在第二种结构的反应器中(并列式翅片反应器),翅片沿流道中轴线对称垂直分布,第一组翅片位于距入口5 mm处,同侧翅片间距20 mm,布置十组翅片。两种结构形式的反应器的反应过程相同。由于反应器沿中轴线对称,且考虑到在竖直方向上,流体流动的方向是相同的,因此本文中将反应器由三维结构简化为二维结构。几何模型参数如表1所示。
在网格划分中,在COMSOL软件内部将网格设置为“流体动力学网格”,网格尺寸分布设置为“较细化”,最小网格单元大小为2.2 × 10−4 m。在热载流体的圆柱形翅片一侧,定义30层湍流边界层网格,边界拉伸因子设为1.1;在反应物一侧的金属壁面设立10层传热边界层网格,边界拉伸因子设为1.1。模型网格如图4所示。
在仿真模拟中,采用k-ε湍流模型处理热载流体在流体通道内的湍流流动,采用固体与流体的传热模块模拟整个反应器的传热情况,采用达西定律模块模拟水蒸气流过Ca(OH)2/CaO颗粒的流动情况。边界条件基于环境温度设置(293.15 K, 1 atm)。模型当中所采用的假设如下:(1) 把多孔床层看作是连续介质,反应床的孔隙率在脱水/水合过程中看作是常数;(2) 将有效导热系数看作常数;(3) 固体反应物的密度随着反应物转化率的改变而改变;(4) 在常压下的比热随着温度的变化而改变;(5) 在不同的温度和压力下,热载体的流动处于二维稳态流动。表2为仿真模拟的边界/初始条件 [28] 。
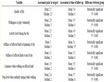
Table 1. Geometric parameters of the reactor
表1. 反应器的几何参数
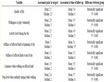
Table 2. Setting of boundary conditions
表2. 边界条件的设置
3. 翅片结构对水解反应过程的影响
3.1. 水解过程中床层温度和转化率分析
如图5所示,脱水过程 [29] [30] 中多孔反应床层的平均温度与反应物的转化率可划分为三个阶段。在第一阶段,整个系统的初始温度设为723.15 K,水解过程中热载流体为热源,在流道入口处温度为863.15 K,反应床内反应物平均温度被热载流体加热。当多孔反应床内的温度超过反应的平衡温度时,激发了吸热的水解过程。在第二阶段,随着水解过程的发展,反应床温度提升的速率放缓了。在第三阶段,水解反应进入末期,反应速率开始减缓,因为反应的吸热量渐渐减少,到最后反应床温度趋于平稳,与热载流体温度重合。各阶段的反应时间和对应的温度情况如表3和表4所示。
从图中能够发现,反应器翅片结构的改变对整体的温度上升趋势没有改变。在第一阶段,由于交错式翅片、并列式翅片反应器的传热性能更好,反应床层整体更早达到平衡温度,因此反应更快开始,且第一阶段结束时的温度要比板式反应器低25 K左右。板式反应器反应时间为240 min,交错式翅片反应器与并列式翅片反应器反应时间为180 min,减少了大约27%。

Figure 5. Changes in average bed temperature (T) and average conversion rate (X) over time in plate, staggered, and parallel fin reactors (hydrolysis process: ε = 0.5, μ = 25 m/s)
图5. 板式、交错式翅片、并列式翅片反应器内反应床层平均温度(T)和平均转化率(X)随时间的变化(水解过程:ε = 0.5,μ = 25 m/s)
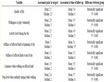
Table 3. Reaction time and corresponding temperature for the first and second stages
表3. 第一、二阶段的反应时间和对应的温度
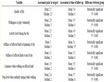
Table 4. Reaction time and corresponding temperature for the second and third stages
表4. 第二、三阶段的反应时间和对应的温度
3.2. 反应床层内不同位置处水解过程的考察
为了详细考察翅片结构对反应器换热情况的影响,研究反应器内各区域的换热效果,在反应床内部设置了六个域点探针,探针的坐标如表5内所示,其位置见图2。其中,P1、P3和P5为沿轴向流动方向不同位置处的点,P1和P2为相同轴同方向但不同径向位置上的点。
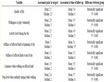
Table 5. Specific positions of probes in the reaction bed
表5. 反应床内探针的具体位置情况

Figure 6. Changes in temperature (T) and conversion rate (X) over time at monitoring points P1 and P2 in plate and symmetrical fin reactors (hydrolysis process: ε = 0.5, μ = 25 m/s)
图6. 在板式、对称式翅片反应器中监测点P1、P2的温度(T)和转化率(X)随时间的变化(水解过程:ε = 0.5,μ = 25 m/s)
如图6所示,转化率曲线表明,在增设翅片结构后,近壁面处的反应进行的更快(P1)。从监测点P1和P2所获得的数据来看,当转化率达到1时,P1和P2点耗时分别减少了39%和36.8%;而达到50%的转化率的时间,两者分别减少了51.7%和52.5%,因此促进反应发生的程度在反应的前期更加明显。尽管翅片结构对于P2点在反应前半段的提升更加显著,但以整个反应过程来看,P1点的强化效果更好,这是因为反应床内反应物导热性较差,靠近壁面处位置的温度更高。
图6显示了在第二阶段,增设翅片后多孔床层的平均温度更低,这是因为反应被激发得更加迅速,而水解反应为吸热反应,反应一发生,多孔床层内的温度就降低了,但在不同区域温度的变化趋势没有改变。考察不同翅片结构下探针位置处的温度随时间曲线中不同阶段转变点(M)的变化情况,M点表明由热载流体传递给反应物的热量与反应物吸收的热量相接近,反应开始进入了第二阶段。与板式换热器相比,在P1和P2位置处,对称式翅片反应器曲线的M点所对应的温度分别降低了大约30 K和40 K。除此之外,增设翅片后,M点的出现时间提早了10 min左右。以上的变化都表示,翅片结构对于水解反应有促进作用,反应能更早地进入第二阶段。
图7与图8显示了沿流动方向上不同位置的温度和转化率随反应时间转变的情况。由图可知,板式

Figure 7. Changes in temperature (T) and conversion rate (X) at monitoring points P1, P3, and P5 near the wall of a symmetrical finned reactor over time (hydrolysis process: ε = 0.5, μ = 25 m/s)
图7. 对称式翅片反应器近壁面监测点P1、P3、P5位置温度(T)与转化率(X)随时间的变化(水解过程:ε = 0.5,μ = 25 m/s)

Figure 8. Changes in temperature (T) and conversion rate (X) at monitoring points P1, P3, and P5 near the wall of the plate reactor over time (hydrolysis process: ε = 0.5, μ = 25 m/s)
图8. 板式反应器近壁面监测点P1、P3、P5位置温度(T)与转化率(X)随时间的变化(水解过程:ε = 0.5,μ = 25 m/s)
与对称式翅片反应器内部各区域变化趋势基本相同。其中,距离入口处越远,温度曲线的转变点M对应的温度越低。反应过程是由入口向出口进行的,具有循序渐进的特点,但板式反应器在距离入口处较远区域,反应几乎同一时间完成。在对称式翅片反应器内,在P1、P3和P5点处,完成反应时间分别约为110 min、130 min和135 min。在板式反应器内,水解反应从出口处开始,向入口处循序渐进,但在反应器入口段到反应器中端转化率的程度基本相同。在P5位置处,反应完成时间为160 min,在P1和P3位置处,反应完成时间为210 min。导致这种现象的原因是反应平衡温度随着反应床层内的压力下降而下降,因此反应器距离出口近的地方平衡温度低。反应初期反应速率随着反应床温度的升高而提升。由图9可知,P5位置点的温度上升的较快,且平衡温度较低,综合这两方面原因,板式反应器水解过程从出口处开始。而在对称式翅片反应器中,P3相比P1、P5位置点的温度上升速率较小,且在反应阶段P1 > P3 > P5,因此反应呈现出反应器两端转化率变化较快的性质。图9、图10、图11和图12为两种结构反应器水解过程不同时段转化率与速度云图,可以更加直观地看出水解反应床内,轴向与径向上反应趋势的变化。

Figure 9. Conversion rate cloud map of reactants in the reaction bed of a symmetrical finned reactor at 40, 80, and 120 minutes (hydrolysis process: ε = 0.5, μ = 25 m/s)
图9. 对称式翅片反应器反应床层反应物40、80、120 min时的转化率云图(水解过程:ε = 0.5,μ = 25 m/s)

Figure 10. Temperature cloud map of reactants in the reaction bed of a symmetrical finned reactor at 40, 80, and 120 minutes (hydrolysis process: ε = 0.5, μ = 25 m/s)
图10. 对称式翅片反应器反应床层反应物40、80、120min时的温度云图(水解过程:ε = 0.5,μ = 25 m/s)

Figure 11. Conversion rate cloud map of reactants at 40, 80, and 120 minutes in the plate reactor bed (hydrolysis process: ε = 0.5, μ = 25 m/s)
图11. 板式反应器反应床层反应物40、80、120 min时的转化率云图(水解过程:ε = 0.5,μ = 25 m/s)
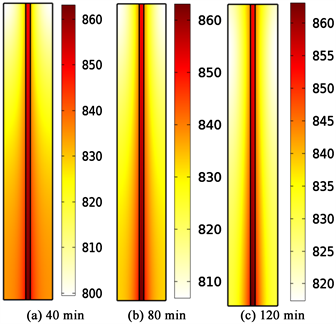
Figure 12. Temperature cloud map of reactants at 40, 80, and 120 minutes in the reaction bed of a plate reactor (hydrolysis process: ε = 0.5, μ = 25 m/s)
图12. 板式反应器反应床层反应物40、80、120 min时的温度云图(水解过程:ε = 0.5,μ = 25 m/s)
4. 翅片结构对水合反应过程的影响
4.1. 水合过程中床层温度和转化率的分析
如图13所示,CaO/Ca(OH)2体系的水合反应 [31] [32] 也能被划分为三个阶段。在第一阶段,系统的初始温度与热载流体在入口处的温度为623.15 K,这个温度低于反应的平衡温度,因此反应床层的温度上升很快,水合反应也就被激发了。在第二阶段,随着热载流体同反应床间发生换热,反应温度达到了顶峰并缓慢的下降。在第三阶段,随着反应的进行,放热反应最终停止了。反应物的转化率达到1,反应床层温度逐渐下降,最后与热载流体的温度相同。
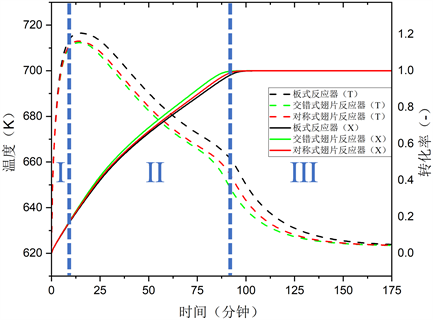
Figure 13. Changes in average temperature (T) and average conversion rate (X) of reactants over time in plate, staggered, and parallel fin reactors (hydration process: ε = 0.5, μ = 25 m/s)
图13.板式、交错式翅片、并列式翅片反应器内反应物平均温度(T)和平均转化率(X)随时间的变化(水合过程:ε = 0.5,μ = 25 m/s)
如图13所示,在水合反应过程中,通过改变翅片结构,从而增强对流换热的方法对水合反应进程具有微弱的影响效果。但是,相较于板式反应器,交错式翅片反应器与对称式翅片反应器内多孔床层的温度更低。该现象的主要原因是:在水合过程中,热源是反应床而非热载流体,尽管热载流体与金属壁面间的对流换热性能被增强,但反应床内的固相反应物导热系数很低,由反应床层向金属壁面的导热过程较慢,以至于增强对流换热造成的影响不明显,但是反应床的平均温度降低,反应期间的热量损失减少。由图13的数据可知,交错式翅片反应器的性能最好,与板式反应器相比,反应器的反应时间减少了7%。
4.2. 反应床层内不同位置处水合过程的考察
如图14所示,在水合过程中,流道内的翅片结构对于相同轴向不同径向位置下,不同区域的反应状况影响较小,三种反应器结构所呈现的反应趋势相同,温度和转化程度的变化随时间的变化和分布是相似的。在相同轴向位置,靠近壁面位置处的温度率先下降,这主要是因为壁面作为金属材料具有很强的导热性,可以将近壁面处的热量快速转移给热载流体。在远壁面处,反应物本身不断散发热量,且固相反应物的导热性较差,热量难以被转移而积聚,因此反应温度更高。
在轴向方向上,因为气体从入口处迅速充满整个热载体通道,因此水合过程首先在入口处进行。当空气持续被泵运送至反应器内,如图15与图16所示,水合反应过程从入口处向出口处推进,板式反应器与对称式翅片反应器各区域的反应过程趋势基本一致。不同探针位置所能达到的峰值温度与入口距离有关,位置距离入口处越远,峰值温度越低。更细致地观察可以发现,当化学反应从进口处向出口地推动过程中,转化率曲线在第二阶段的斜率降低,说明在该阶段的反应速率在缓缓下降。图17与图18是水合过程不同时间段的转化率与温度云图,可以更加直观地看出水合反应床内轴向与径向上反应趋势的变化。

Figure 14. Changes in temperature (T) and conversion rate (X) at monitoring points P1 and P2 in plate and staggered fin reactors over time (hydration process: ε = 0.5, μ = 25 m/s)
图14. 在板式、交错式翅片反应器中监测点P1、P2位置处的温度(T)和转化率(X)随时间的转变(水合过程:ε = 0.5,μ = 25 m/s)

Figure 15. Changes in temperature (T) and conversion rate (X) over time at monitoring points P1, P3, and P5 near the wall of the staggered finned reactor (hydration process: ε = 0.5, μ = 25 m/s)
图15. 交错式翅片反应器近壁面监测点P1、P3、P5位置处的温度(T)与转化率(X)随时间的变化(水合过程:ε = 0.5,μ = 25 m/s)
通过以上分析,可以得出在同一径向上,在近壁面处的水合过程先于反应床层内部的水合过程,但反应的速率相近。在轴向方向上,反应沿热载流体流动方向不断推进,且反应速率的大小呈现递减的趋势。

Figure 16. Changes in temperature (T) and conversion rate (X) over time at monitoring points P1, P3, and P5 near the wall of the plate reactor (hydration process: ε = 0.5, μ = 25 m/s)
图16. 板式反应器近壁面监测点P1、P3、P5位置处的温度(T)与转化率(X)随时间的变化(水合过程:ε = 0.5,μ = 25 m/s)

Figure 17. Conversion rate cloud map of reactants in the reaction bed of a plate reactor at 20, 40, and 60 minutes (hydration process: ε = 0.5, μ = 25m/s)
图17. 板式反应器反应床层反应物20、40、60 min时的转化率云图(水合过程:ε = 0.5,μ = 25 m/s)
5. 热流密度与压降
温度曲线和转化率曲线改变的根本原因是传热性能的优化,与此同时,增设翅片之后流道内的压降也会产生变化。如图19和表4所示,在三种结构的反应器中,金属壁面的平均热流密度与产生的压降不同。在水解反应中,与反应历程相对应,热流密度的变化也呈现为三个阶段。在第一阶段,热量通过壁面传递至反应床层并对多孔床层加热,并且随着热载流体与金属壁面间温差的减小,热流密度在短时间内迅速下降。接着,在第二阶段,多孔床层内反应物开始发生吸热水解反应,多孔床层平均温度上升的

Figure 18. Velocity cloud map of reactants in the reaction bed of a plate reactor at 20, 40, and 60 minutes (hydration process: ε = 0.5, μ = 25 m/s)
图18. 板式反应器反应床层反应物20、40、60 min时的速度云图(水合过程:ε = 0.5,μ = 25 m/s)

Figure 19. Average heat flux density (Q) of metal wall surfaces in three reactors (hydrolysis process: ε = 0.5)
图19. 三种反应器中金属壁面的平均热流密度(Q) (水解过程:ε = 0.5)
速率减缓。这也解释了在此阶段,热流密度下降的速率相较于第一阶段下降了许多。最终,在第三阶段中,随着反应不断进行并趋近于完成,反应床内温度趋近于热载流体温度,热流密度也趋近于0。在热流密度曲线中,三种结构的反应器初始热流密度基本相同,但在第一阶段,板式反应器热流密度下降幅度最大,交错与对称式翅片反应器基本相同。在第二阶段,板式反应器热流密度曲线相较于另外两者下降趋势相对平缓,热流密度趋向于0耗时更长,表明板式反应器相较于设有翅片的反应器,反应时间更长。
增设翅片后,反应器金属壁面处热流密度的变化依旧保持着相同的规律,但当热载流体流经带有翅片的通道时,半圆柱型翅片对于空气有扰动作用,使通道内的空气运动轨迹发生改变。图20为热载流体在通道内的流线图,颜色的不同代表了热载流体具有不同的速度。由图可知,空气流经半圆柱型翅片后,在翅片后方速度下降至约5 m/s左右,在此处形成涡流。在主流区域,由于通道被翅片占据,流通通道变窄,而空气为恒定质量流动,因此在主流区域流速增加。由速度云图可知,板式反应器的热流载体通道速度边界层较厚,而设有翅片的反应器的通道速度边界层较薄,这是因为翅片结构形成的扰动,破坏了原有的速度边界,这也是翅片结构能强化换热性能的主要原因。
翅片结构除了对空气流动产生影响之外,同时对于通道内的压降产生影响。表6列出了热载流体通道入口处的压力变化。可以看出,交错式和对称式翅片反应器的压降比板式反应器更大,这是因为翅片结构阻碍了空气流动,并且形成涡流。对称式翅片反应器比起交错式翅片反应器产生的压降还要大450 Pa左右。入口处压力的增加需要耗费更多的机械功,增加了泵的负担和反应器运行的成本。

Figure 20. Flowline diagram of the thermal carrier fluid channel after 300 minutes of hydrolysis reaction (hydrolysis process: ε = 0.5, μ = 25 m/s)
图20. 水解反应经过300分钟后热载流体通道的流线图(水解过程:ε = 0.5,μ = 25 m/s)
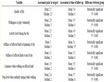
Table 6. Pressure at the inlet of the thermal fluid channel (hydrolysis process: ε = 0.5, μ = 25 m/s)
表6. 热载流体通道入口处压力(水解过程:ε = 0.5,μ = 25 m/s)
热载流体的速度能够影响流体产生的压降与热载流体和金属壁面间的对流换热能力,即较高的流速就会引起压降的增加和对流换热系数的增大。当流体在管道或通道中流动时,由于流体的内摩擦和与壁面的摩擦,会产生压力损失,即压降。流体的速度越快,流体分子间的相互作用以及流体与壁面间的碰撞就越频繁,从而产生的内摩擦力就越大,导致压降增加。图21表示了水解过程中,在进口空气流速分别为25 m/s、30 m/s和35 m/s时,交错式翅片反应器内反应物平均转化率随时间的变化。从图中可知,随着流速的增加,换热性能的提升有限,而流体在进口处的压力急剧上升。因此,为了换热性能有限的提升而使热载流体流速过高是没有必要的,这样做会额外产生压降,进而需要增加泵的机械功,从而提高反应器整体运行的成本。

Figure 21. Changes in conversion rate over time at inlet flow rates of 25 m/s, 30 m/s, and 35 m/s in a staggered finned reactor (hydrolysis process: ε = 0.5)
图21. 交错式翅片反应器在入口处流速25 m/s、30 m/s和35 m/s时转化率随时间的变化(水解过程:ε = 0.5)
6. 结论
热化学储能是实现太阳能光热发电长期稳定使用的有效方法,其中,热化学储能反应器是实现热量存储和释放的核心装置。本文采用数值模拟方法,着重研究反应器内部载热流体通道内翅片排布对CaO/Ca(OH)2体系储/放热过程的影响。通过仿真实验与分析得到如下结论:在反应床孔隙率为0.5的条件下,水解过程中,对称式翅片反应器与交错式翅片反应器减少反应时间27%。板式反应器反应从出口处向入口处延伸,而设有翅片结构的反应器反应从入口与出口处向内部延伸。水合过程中,对称式翅片与交错式翅片结构的强化性能相较于水解过程提升较小。增加热载流体流速会产生负面的效果。两种翅片结构热载流体流经后都会产生额外的压降,对称式翅片结构比交错式翅片结构产生的压降还要高450 Pa,而提高流速完成反应的时间是相近的,但增加流速会提高反应器整体的运行成本,因此提高流速是不可取的。
符号说明
L——反应器长度,mm;
P——无水蒸气热通量,J/s;
P1,P2,P3,P4,P5,P6——探针位置;
PD——水解过程水蒸气出口压力,Pa;
PH——水合过程水蒸气进口压力,Pa;
Q——平均热流密度,W/m2;
q——绝热边界,mm;
r——翅片半径,mm;
T——反应层平均温度,K;
Tbed——反应床温度,K;
THTF——传热流体温度,K;
Tin/D——热载流体水解过程的进口温度,K;
Tin/H——热载流体水合过程的进口温度,K;
Wb——反应床宽度,mm;
Wc——流道宽度,mm;
X——平均转化率;
y——无滑移边界,mm;
ΔH——反应的焓值,KJ/mol;
µ——热载流体进口处初速度,m/s;
ε——孔隙率。
NOTES
*通讯作者。