摘要: 齿轮箱体作为齿轮箱的基础零部件,为其内部的齿轮提供了结构支持与保护等作用,需要保证其自身的稳定性与可靠性。利用SolidWorks建立齿轮箱体三维模型,将模型导入ANYSYS Workbench中对箱体进行静力学分析以及模态分析。静力学分析结果表明齿轮箱的最大应力为25.191 Mpa,位于齿轮箱输入轴于输出轴的孔中;最小应力为2.2864e−2 Mpa,位于齿轮箱的顶部。模态分析得出,齿轮箱体的各阶固有频率和振型,随着阶数的增大,其变形量变化的数值较小,为齿轮箱体的结构优化设计提出进一步的理论依据。
Abstract:
As the basic component of a gearbox, the gearbox provides structural support and protection for the internal gears, and it is necessary to ensure its own stability and reliability. Build a 3D model of the gear box using SolidWorks, and import the model into ANSYS Workbench to perform static and modal analysis on the box. The static analysis results show that the maximum stress of the gearbox is 25.191 Mpa, located in the hole between the input shaft and the output shaft of the gearbox; The minimum stress is 2.2864e−2 Mpa, located at the top of the gearbox. Modal analysis reveals the natural frequencies and modes of each order of the gear box. As the order increases, the numerical changes in deformation are relatively small, providing further theoretical basis for the structural optimization design of the gear box.
1. 引言
齿轮箱,作为机械装备传动系统中的关键部件,其性能直接影响着整个机械装备的运行状况。因此,对齿轮箱的安全性和可靠性要求也愈发严格。一旦出现故障,可能会引发连锁反应,导致生产线中断,造成巨大的经济损失在这样的背景下 [1] [2] 。它主要负责转换运动方向和传递功率,具有结构紧凑、传动平稳、效率高且承载能力强等特点。因此,齿轮箱被广泛应用于各种复杂机械装备中,如风力发电机、直升机、重型卡车和家用轿车等 [3] [4] [5] 。在这些复杂的工作环境中,闭式齿轮因其独特的性能优势而得到广泛应用,而齿轮箱箱体则为闭式齿轮提供了必要的保护,确保了齿轮工作环境的稳定性。
齿轮箱箱体不仅延长了齿轮的使用寿命,降低了故障率,还起到了支撑和减震的重要作用。它的性能直接影响着齿轮箱的传动效率和使用寿命。因此,对齿轮箱箱体进行深入研究和分析具有重要意义。本文利用SolidWorks三维软件建立了齿轮箱的结构模型,并导入ANSYS软件进行静力学分析和模态分析,以全面评估齿轮箱的稳定性。这些分析结果为实际齿轮箱结构的设计优化提供了重要参考,有助于进一步提升齿轮箱的性能和可靠性。
2. 齿轮箱体结构模型的建立
选用市面常见的齿轮箱为设计原型,利用SolidWorks三维建模软件建立三维模型。此模型长为130 mm,宽为100 mm,高度为100 mm,轴孔的直径为24 mm。建立好的齿轮箱模型如上图1。
2.1. 静力学分析
结构静力学分析是一种精细化的方法,它通过对结构进行网格划分来精确计算其内部的应力分布。这种分析方式可以深入直观的了解材料的疲劳性能、预估使用寿命提供了重要的依据。静力结构分析专注于评估结构在特定静力载荷作用下的响应情况,其中,位移、应力和应变等关键参数是关注焦点。
将齿轮箱箱体的设计与结构静力学分析紧密结合,可以让产品在设计初期便及时发现并解决潜在的问题,从而避免在后续的制造或使用过程中遭遇重大困扰。这种方法不仅有助于提升产品的整体质量和可靠性,更能够在很大程度上节省生产成本和时间,实现更高效、更优化的产品设计 [6] [7] 。
2.2. 材料设置和网格划分
完成建模后(如图1),将齿轮箱导入ANSYS Workbench中,然后设置箱体的材料属性。整个齿轮箱选用的材料是Q460。屈服强度为460 MPa,杨氏模量为2e+05 MPa,泊松比为0.247。齿轮箱材料选定完成后,使用ANSYS Workbench软件自带自动生成网格的功能,在网格尺寸设定选项中,选择中等,细化网格,得到齿轮箱箱体总共69,635个单元,105,725个节点。对已生成的网格按照Elemental Quality网格质量评判标准,网格的平均质量达标,符合齿轮箱箱体静态应力以及模态分析网格划分标准。
2.3. 施加约束和载荷
实际工况中,减速器是通过螺栓固定在设备上,需要在齿轮箱的4个引脚处设置固定约束。减速器除了受到其自身的载荷还另外施加1000 N的力于轴孔的内壁。
2.4. 结果后处理:
从图1中可以看出,齿轮箱的最大应力为25.191 Mpa,位于齿轮箱输入轴于输出轴的孔中;最小应力为0.022864 Mpa,位于齿轮箱的顶部。从图2 (等效应变图)中,可以得知,变形最大处也位于齿轮箱输入轴孔与输出轴孔壁,变形量为1.2596 × 10−4 mm。其余位置的受力情况较为理想,变形量不大。

Figure 2. Stress distribution diagram of gearbox
图2. 齿轮箱应力分布图
3. 模态分析
通过对齿轮箱的模态分析 [8] [9] [10] [11] ,可以得到在设备工作时,齿轮箱自身发生的形变,从而得知此齿轮箱本身的工作强度范围。观察图3~图5,即齿轮箱在1、2、3阶模态时,齿轮箱的震动频率都为0 HZ。从图3可以得知,此时的齿轮箱最大变形发生在齿轮箱背面,最大变形量为2.7418 mm。图4中,最大变形量为2.7418 mm,最大变形量处发生了变化,但是依旧出现在齿轮箱顶角处,变形趋势大致沿着一条平行线向上变小。如图5,最大变形量为2.8088 mm,最大变形量处依旧出现在了齿轮箱的顶角处,变形趋势也没有发生改变,只是此时输入轴孔的变形量变大。如图6,频率为2.5943e−004 HZ,变形量最大为2.4739 mm.此时箱体的最大变形处出现在其顶角处,且各个顶角都已一定的变形。由图7可知,频率为3.1839e−004 HZ,最大变形量2.3067 mm,最小变形量为0.58104 mm。最大变形量出现在箱体顶角处。如图8,振动频率为3.4889e−004 HZ,最大变形量为2.5479 mm,最小变形量为0.69255 mm。出现在箱体的顶边处。从上述数据可以看出,齿轮箱在这6阶模态分析中,变形量的数值变化并不大(2.8088 mm < 5 mm),只是随着阶数的增大,顶角的变形量变大,且变形区域增大,因此该齿轮箱符合强度要求。
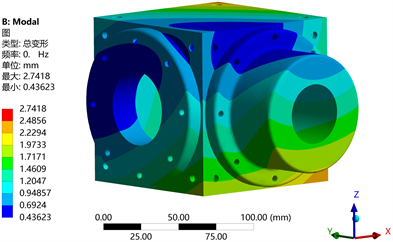
Figure 3. First-order deformation diagram
图3. 一阶变形图

Figure 4. Second-order deformation diagram
图4. 二阶变形图

Figure 5. Third-order deformation diagram
图5. 三阶变形图

Figure 6. Fourth-order deformation diagram
图6. 四阶变形图

Figure 7. Fifth-order deformation diagram
图7. 五阶变形图

Figure 8. Sixth-order deformation diagram
图8. 六阶变形图
4. 结论
通过ANSYS Workbench软件对齿轮箱箱体结构进行静力学分析和模态分析,得到以下结果:
(1) 通过静力学分析,当齿轮箱处于工作状态时,最大变形量为1.2596 × 10−4 mm,变形量较小,符合实际工作需求,齿轮箱受到的最大应力为25.191 Mpa,齿轮箱的结构设计表现出良好的稳定性和承载能力。各部件之间的连接和支撑结构能够有效地传递和分散负载,避免了局部应力集中的问题。
(2) 通过模态分析获得了齿轮箱在不同频率下的振动特性。齿轮箱在这6阶模态分析中,固有频率的范围在0到3.4889e−004 HZ之,其中,齿轮箱在五阶频率时变形量较小,当固有频率为三阶时,最大变星岭到达最大,此时的变形量为2.8088 mm。但总体而言,变形量在可接受范围内,因此满足设计要求。
综上所述,齿轮箱在静态和动态性能方面都表现出了较高的可靠性。通过本次分析,不仅验证了齿轮箱设计的合理性,还为后续的优化和改进提供了重要依据,在未来的实际应用中,齿轮箱将能够稳定运行,为设备的正常运行提供可靠保障。