1. 引言
在含铝复合推进剂的燃烧过程中,铝熔点相对燃烧室温度低,颗粒在推进剂燃烧表面处熔化、聚集,从而形成更大尺寸的团聚物 [1] 。这些团聚物一部分沿着发动机壳体流动,一部分被燃气吹入高度旋转的气流中。其中大部分尺寸较小的三氧化二铝颗粒会随着燃气排出喷管,较大的三氧化二铝颗粒与发动机壁撞击,粘结在壁面形成熔渣。另一方面,潜入式喷管背壁区域随着燃面的推移逐渐形成一个空腔。该空腔区域存在复杂的回流区,进入背壁区域的颗粒在回流的作用下滞留,颗粒浓度在增大,从而背壁区域的颗粒碰撞聚合的概率也在大大增加,使得区域内颗粒的尺寸较大,颗粒的随流性下降,因此发生沉积的概率也随之提高 [2] [3] ,颗粒沉积形成的熔渣会影响发动机的稳定性 [4] [5] 。
固体火箭发动机燃气中颗粒对喷管的沉积是非常复杂的问题,张旭 [6] 分析了颗粒尺寸对沉积的影响,计算分析了八组不同的颗粒直径的颗粒捕获率,研究发现1 μm和5 μm的颗粒发生沉积的概率很小,当颗粒直径大于40 μm时。沉积概率会显著增大。刘涵元 [7] 采用DPM与VOF耦合的方法,模拟了颗粒进入流场到与壁面发生撞击产生液膜这一过程,实现了颗粒从离散相转化成连续相的过程。他将耦合的方法用于模拟不同喷管背壁区域的颗粒沉积,发现台阶型的喷管背壁相较于直线型的喷管背壁沉积量更小。秦少东 [8] 采用张胜敏 [9] 测试的丁羟三组元推进剂的颗粒尺寸分布,选取了6个时刻对分段式固体火箭发动机沉积进行计算,分析限燃层高度对颗粒沉积的影响。研究发现,颗粒运动在受到限燃层的扰动后运动开始混乱,增加了沉积的概率,并且沉积率随着限燃层高度增加而增大。张勇 [10] 用simple算法计算气相,DPM方法追踪颗粒,分析了颗粒相与气体速度比以及颗粒分布对沉积规律的影响。研究发现颗粒粒径增大会导致沉积量增加,颗粒相注入速度增大会导致颗粒捕获率下降。
研究Al2O3凝相颗粒的沉积规律,有利于合理设计喷管背壁型面和潜入深度等,对提高发动机性能有重要意义。本文选用颗粒沉积统计方法,针对潜入式喷管发动机进行了颗粒沉积两相流数值模拟,分析了不同颗粒直径、颗粒初速度与颗粒浓度对颗粒沉积的影响。
2. 物理模型和计算方法
2.1. 几何模型
本论文在武利敏 [11] 建立的固体火箭发动机几何模型的基础上进行两相流计算,燃烧室总长为1.45 m。针对不同时刻的燃面进行简化计算,选取发动机工作的0 s、1.74 s、3.47 s、5.17 s、6.93 s和8.72 s六个时刻进行分析。其中0 s、1.74 s和3.47 s代表药柱前翼正在消失,后翼还未消失;5.17 s和6.93 s代表药柱前后翼都在消失;8.72 s代表药柱前后翼完全消失。在每个时刻内药柱中心燃面退移10 mm,二维轴对称几何模型和燃面位置如图1所示,图1中粗实线代表发动机燃面,细实线代表发动机外壳。

Figure 1. Engine combustion surface schematic diagram
图1. 发动机燃面示意图
本计算选用典型的AP/HTPB含铝复合推进剂,推进剂密度为1826.4 kg/m3,参照Cai W [12] 燃气组分和质量分数。本文在计算中假设燃烧产物中的所有颗粒全是Al2O3,Al2O3颗粒以燃气速度的0.4倍垂直于推进剂燃面进入流场。发动机六个典型时刻的发动机工况和两相参数,如表1所示。气相和颗粒入口温度均为3300 K,燃面喷射的Al2O3颗粒质量流量为总颗粒质量流量的35%。
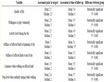
Table 1. Engine operating conditions and two-phase parameters
表1. 发动机工况和两相参数
2.2. 计算方法
本文对气相流场采用pimple算法,对其采用预测—校正策略,通过迭代的方式将速度和压力的计算解耦。湍流模型采用SSTk-ω模型,选用pimple算法求解气相流场,时间项采用欧拉离散,对流项采用高斯迎风格式离散,扩散项采用高斯理论线性插值,并带有正交修正。颗粒轨道模型跟踪计算颗粒轨迹。
2.3. 颗粒沉积统计方法
本文选用Bai和Gosman [13] 的基于韦伯数的颗粒碰撞壁面模型。液滴撞击产生的冲击压力、斜向液滴撞击膜表面产生的切向动量传递以及膜表面的气体剪切力。在边界层框架下,建立了壁膜流动的质量、动量和能量的一般输运方程。
连续方程:
(1)
式中,
——局部膜厚,
——液膜x方向的速度,
——液膜y方向的速度,
,
是气体速度矢量,
是界面速度矢量,n是界面的单位外法向量;
是撞击液滴产生的净质量通量。
动量方程:
(2)
(3)
式中,
,
是液滴切向动量损失产生的动量源,
表示液滴和气体冲击压力与毛细压力之和,后者可近似为
。
3. 计算结果分析
3.1. 颗粒冲刷模拟与数据统计
根据相关试验研究,对含潜入式喷管的固体火箭发动机,机械侵蚀主要发生在喷管附近,因此本文研究的颗粒冲刷区域如图2所示,CD是喷管收敛段,DE是喷管扩张段。
图3是发动机各区域沉积速率随时间变化图。背壁区域沉积速率在5.17 s前都比较小,5.17 s后沉积速率快速增加。凸缘段沉积速率先减小后增大,在6.93 s后又减小。喷管收敛段沉积速率在6.93 s前不断增大,在6.93 s后显著减小。凸缘段沉积速率主要与药柱中后段喷射的颗粒有关,3.47 s前药柱后翼还未开始消耗,由于气流漩涡强度在增大,颗粒在气流漩涡中心运动,与凸缘段撞击的颗粒在减小,因此沉积速率下降。3.47 s后药柱后翼开始消失,药柱中段喷射的颗粒增多,在燃气作用下与喷管收敛段发生撞击的颗粒数也在增多,沉积速率增大。随着燃面的退移和气流漩涡尺寸的增大,与喷管收敛段撞击的颗粒数越来越多,在8.72 s时气流漩涡强度达到了最大,进入背壁区域的颗粒数最多,因此喷管收敛段和凸缘段沉积速率都有所下降。
表2统计了发动机各时间段的颗粒沉积速率和沉积量,颗粒沉积量等于颗粒沉积速率与持续时间的乘积,本模拟计算得到0 s~10.51 s时间段内Al2O3颗粒沉积量1.554 kg,颗粒喷射量86.36 kg,沉积率是1.8%。与本文发动机几何外形和推进剂均相似的SRMU发动机,试验测量Al2O3沉积率是1.9%。与试验相比,本计算得到的沉积占比数据与试验数据吻合较好,误差在可接受范围内。
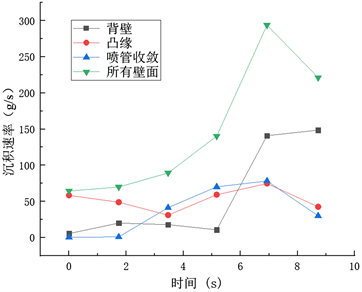
Figure 3. The deposition rate of each region varies over time
图3. 各区域沉积速率随时间变化
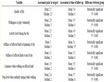
Table 2. Particle deposition statistics
表2. 颗粒沉积统计
3.2. 粒径分布对颗粒沉积的影响
发动机不同时刻燃烧室各区域颗粒沉积量有显著差异,在8.72 s发动机背壁区域沉积速率最大。因此以8.72 s时刻对应燃面为研究对象,通过设置单一尺寸颗粒和多尺寸颗粒进行计算分析,且假设在燃烧室内运动过程中颗粒直径不发生改变。本研究粒径分布采用Rosin-Rammler分布,依据铝质量分数是17%的推进剂颗粒收集实验结果 [9] ,在本文计算中设置Al2O3颗粒平均直径是10 μm,最小直径是5 μm,最大直径是100 μm。
3.2.1. 单一尺寸颗粒对颗粒沉积的影响
图4是不同直径的颗粒沉积形成的液膜厚度云图。当颗粒小于10 μm时,颗粒随流性好,进入背壁区域内的颗粒在气流漩涡中心运动,与背壁面发生撞击的颗粒少,与凸缘处和喷管收敛段发生撞击颗粒较多,因此颗粒主要在凸缘段和喷管收敛段沉积。当颗粒大于20 μm时,随流性差,进入背壁区域气流漩涡的颗粒在气流漩涡的影响下容易与背壁面发生撞击,因此颗粒在背壁区域液膜厚度大。
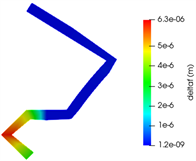
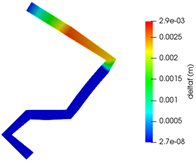
(a) 10 μm(b) 20 μm (c) 40 μm
Figure 4. Cloud map of liquid film thickness with different diameters
图4. 不同直径的液膜厚度云图
图5是发动机各区域不同直径的颗粒沉积速率变化图。直径小于10 μm的颗粒在背壁区域沉积率小,凸缘段和喷管收敛段沉积率大。直径大于20 μm的颗粒在背壁区域沉积率显著增大,且随着颗粒直径增大背壁区域沉积率减小,在喷管收敛段和凸缘段沉积率小,且随着颗粒直径增大这两段沉积率减小。这主要是因为当颗粒小于10 μm时,背壁区域内的颗粒随流性强,在气流漩涡中心运动,凸缘段和喷管收敛段颗粒多,因此背壁区域颗粒沉积率小,凸缘段和喷管收敛段沉积率大。当颗粒大于20 μm时,颗粒随流性差,背壁区域内的颗粒容易撞击壁面发生沉积,但是由于颗粒直径增大后,颗粒靠近轴线运动,大多数颗粒从轴线流出喷管,背壁区域内部的颗粒数减小,因此当颗粒大于20 μm时,主要在背壁面发生沉积,且沉积率随着颗粒直径增大而减小。
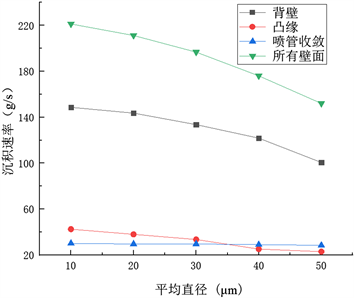
Figure 5. Deposition rate of particles with different average diameters
图5. 不同平均直径的颗粒沉积速率
3.2.2. 多尺寸颗粒对颗粒沉积的影响
图6是不同平均直径的颗粒沉积形成的液膜厚度云图。当颗粒平均直径是10 μm时,液膜厚度最大是8.4e−04 m,当颗粒平均直径是50 μm时,液膜厚度最大是9.6e−05 m。显然,背壁区域液膜厚度随着颗粒平均直径增大而减小,凸缘段和喷管收敛段相对于背壁区域液膜厚度一直很小。
(a) 10 μm(b) 20 μm (c) 40 μm
Figure 6. Cloud map of particle liquid film thickness with different average diameters
图6. 不同平均直径的颗粒液膜厚度云图
图7是发动机各区域不同平均直径的颗粒沉积速率图。随着颗粒平均直径增大,背壁区域和凸缘段颗粒沉积速率明显下降,喷管收敛段颗粒沉积率一直维持在很低的水平。以上结果表明:颗粒平均直径增大后,颗粒随流性差,进入发动机背壁区域的颗粒减少,在发动机轴线附近颗粒多。因此颗粒平均直径增大后,背壁和凸缘的颗粒少,沉积速率下降。背壁面沉积占所有壁面沉积比例最大,因此背壁区域是颗粒沉积的主要部位。

Figure 7. Deposition rate of particles with different average diameters
图7. 不同平均直径的颗粒沉积速率
3.3. 颗粒初速度对颗粒沉积的影响
图8是不同初速度的颗粒沉积形成的液膜厚度云图。不同初速度的颗粒都主要在背壁区域沉积形成液膜,凸缘段和喷管收敛段液膜厚度很小。在背壁区域液膜的最大液膜厚度几乎相同,最小液膜厚度有所不同,但整体液膜厚度随颗粒初速度变化不明显。
图9是发动机各区域不同初速度的颗粒沉积速率。随着颗粒初速度增大,背壁面沉积速率略有下降,凸缘段和喷管收敛段沉积速率略有增加,但是所有壁面沉积速率基本没有变化。这主要是因为当颗粒初速度增加后,进入背壁区域的颗粒数略有减少,与凸缘段和喷管收敛段撞击的颗粒略有增加,但是总的来说,颗粒初速度的增加对沉积区域附近的颗粒曳力增加不明显,颗粒在燃烧室的运动轨迹主要还是受燃气影响。因此当颗粒初速度增加后,对沉积速率影响不大。
(a) 4.76 m/s(b) 5.95 m/s (c) 10.71 m/s
Figure 8. Cloud maps of particle liquid film thickness at different initial velocities
图8. 不同初速度的颗粒液膜厚度云图
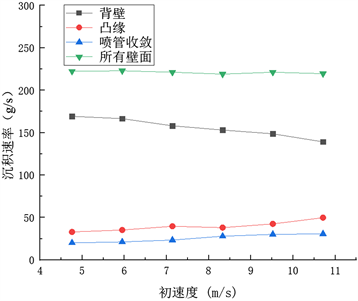
Figure 9. Deposition rate at different initial velocities
图9. 不同初速度的颗粒沉积速率
3.4. 颗粒质量流量对颗粒沉积的影响
图10是不同颗粒质量流量沉积形成的液膜厚度云图。如图所示,颗粒主要在背壁区域沉积产生液膜,凸缘段和喷管收敛段液膜厚度都很小。随着颗粒质量流量增加,背壁面最大液膜厚度显著增加,当颗粒质量流量达到3.2736 kg/s时,液膜最大厚度在10−3 m以上。
图11是发动机各区域不同颗粒质量流量的颗粒沉积速率图。随着颗粒质量流量增加,发动机各区域沉积速率都增大。其中,背壁区域较凸缘段和喷管收敛段沉积速率增长更快,凸缘段和喷管收敛段颗粒沉积速率增长速率基本相同。当颗粒质量流量增加后,进入背壁区域的颗粒比例也略有增加,在喷管收敛段和凸缘段发生沉积的颗粒比例减小。
(a) 1.6368 kg/s (b) 2.1824 kg/s (d) 3.2736 kg/s
Figure 10. Cloud map of liquid film thickness formed by particle deposition with different particle mass flow rates
图10. 不同颗粒质量流量的颗粒沉积形成的液膜厚度云图
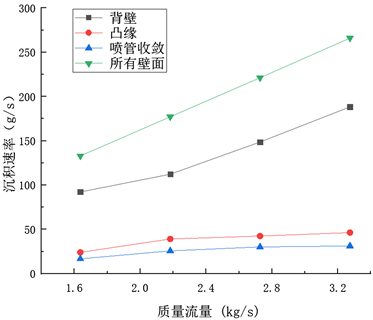
Figure 11. Deposition rate of different particle mass flow rates
图11. 不同颗粒质量流量的沉积速率
4. 总结
本论文分析了颗粒直径、颗粒初速度与颗粒浓度对含潜入式喷管的固体火箭发动机颗粒沉积的影响,主要结论如下:
1) 颗粒是单一尺寸粒径分布,当颗粒直径小于10 μm时,颗粒随流性强,在背壁区域的大多数颗粒在气流漩涡中心运动,凸缘段和喷管收敛段颗粒多,因此背壁区域颗粒沉积速率小,凸缘段和喷管收敛段沉积速率大;如果颗粒是多尺寸分布,颗粒平均直径增大后,进入发动机背壁区域的颗粒减少,背壁面和凸缘段沉积速率下降,大多数颗粒从中心轴线附近流出燃烧室。
2) 颗粒初速度增加后,背壁面沉积速率略有下降,凸缘段和喷管收敛段沉积速率略有增加,但是所有壁面沉积速率总和基本没有变化。
3) 当颗粒质量流量增加后,发动机各区域沉积速率都增大。其中,背壁区域较凸缘段和喷管收敛段沉积速率增长更快,凸缘段和喷管收敛段颗粒沉积速率增长速率基本相同。