1. 引言
随着汽车工业的不断发展,人们开始关注驾驶和乘坐时的个人舒适感,离合器膜片弹簧的强度直接影响离合系统的稳定性,严重会导致车辆故障停运 [1] 。膜片弹簧是一个单一的薄金属片,当压力施加到它上时,它会压缩;当压力移除时,膜片弹簧就会恢复到原来的形状。膜片弹簧的中心部分被切成许多部分,作为分离指。当离合器装配体与发动机一起旋转时,这些重量被离心力抛向外,导致轴承压向压力板 [2] 。在离合期间,推力球轴承被分离轴承向前移动。弹簧在支点环上转动,其外缘远离飞轮,膜片弹簧将压盘从从动盘上拉离,从而实现离合器分离 [3] 。因此对膜片弹簧结构的结构优化和有限元分析有助于提升汽车稳定性和乘车者舒适性。
李剑英等 [4] 研究了膜片弹簧离合器的静力学、模态、瞬时动力学和疲劳分析,结果表明其结构设计的安全性可靠,各零部件的动力学特性与预期要求相符,且通过疲劳分析结果为结构设计提供了优化思路。刘培等 [5] 通过膜片弹簧端口形貌观察、化学成分分析、硬度检测等,得到膜片弹簧断裂的主要原因是离合器盖的分离行程超出设计要求,改进这一指标可解决离合器的使用性能问题。金博宇等 [6] 为了解决工程中膜片弹簧离合器快速设计要求,提出了一套基于设计流程知识和参数化模型知识的设计技术,降低了实际生产中膜片弹簧的设计使用难度。Purohit等 [7] 对离合器系统进行冲击锤测试,分别确定了离合器零部件的振型和固有频率。Patil等 [8] 基于ANSYS进行了网格收敛研究,通过定义单元数与分析精度的关系,构建离散化函数,从而得到膜片弹簧更加精确的应力分析结果。
本文利用ANSYS软件基于实际参数下设计的膜片弹簧模型,对其进行静应力和模态分析,并通过冲制加强筋优化其结构,改善其分离指数并提高结构强度,为后续离合器零部件结构改进提供研究思路。
2. 膜片弹簧仿真模型建立
2.1. 膜片弹簧结构设计
根据某型车辆的实际参数,该车为单片干式膜片弹簧摩擦离合器,具有结构性能稳定、设计成熟和应用广泛等优点,且干式离合器得到传递扭矩更大。离合器是手动挡汽车重要变速装置,膜片弹簧离合器位于发动机飞轮上,主要包括离合器盖总成、从动盘总成和分离轴承总成等部分。膜片弹簧属于离合器盖总成的一部分,与离合器盖、压盘等零件相接触。膜片弹簧在结构上是碟簧状,具有一定锥度,在锥面上分布着多个分离指。膜片弹簧结构的具体尺寸参数如表1所示。
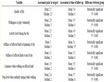
Table 1. Dimensional parameters of diaphragm spring
表1. 膜片弹簧尺寸参数
膜片弹簧的弹性和刚度需要得到保证,选用的材料的塑性变形能力和抗冲击能力足够好,本设计所选膜片弹簧材料为60Si2MnA,材料特性如表2所示。
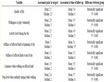
Table 2. Material characteristics of diaphragm spring
表2.膜片弹簧材料特性
根据上述膜片弹簧的结构尺寸参数和材料特性,在SolidWorks软件绘制膜片弹簧的三维模型,如图1所示。图1(a)是膜片弹簧正视图,可以清晰看出其结构组成,包括碟簧内外径、分离指位置和个数;图1(b)的侧视图可以观察到膜片弹簧锥角。
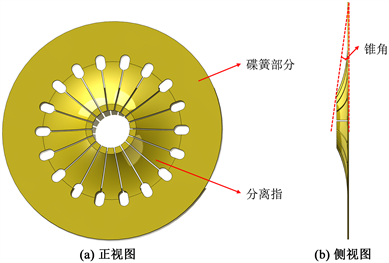
Figure 1. Structure model of diaphragm spring
图1. 膜片弹簧结构模型
2.2. 膜片弹簧仿真模型建立
在膜片弹簧离合器中,零部件的形状和应力情况各不相同,而膜片弹簧的受力发生伸缩,基于其工作原理进行网格划分、边界设置和加载。
本文将SolidWorks软件建立的膜片弹簧三维模型导入ANSYS中,根据表2的材料参数定义膜片弹簧的材料类型、弹性模量、泊松比等,再对其进行网格划分,结果如图2所示。为保证计算精度和准确性,同时减少计算量,对膜片弹簧网格划分时进行局部加密 [9] 。
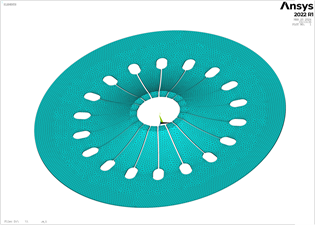
Figure 2. Schematic diagram of grid division
图2. 网格划分示意图
膜片弹簧在工作状态时处于结合状态,将与支撑环接触处设置为零位移约束,与压盘接触的大端处设置作用力。根据相关研究表明,作用力的加载范围设定为2000~7000 N,车辆膜片弹簧的一般最大受力不超过6000 N,所以设定的研究范围稳定可靠。
2.3. 膜片弹簧结构优化
在对膜片弹簧的结构应力和位移分析后,结果显示在分离指根部所受应力最大。为改善膜片弹簧的结构和提升强度,在膜片弹簧的表面冲制加强筋 [10] ,如图3所示。加强筋冲制位置位于分离指之间,其底端与膜片弹簧小端平齐,基本尺寸为长15 mm,宽6 mm,深3 mm。
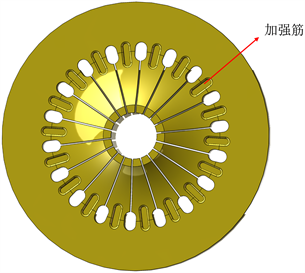
Figure 3. Model of diaphragm spring with punched reinforcements
图3.冲制加强筋后的膜片弹簧模型
膜片弹簧的分离指在离合器分离过程中会发生弹性变形,分离行程会影响离合器的响应时长,在冲制加强筋后,可以提升分离指刚度,减小分离行程,从而提高膜片弹簧的强度和性能。
3. 仿真结果分析
表3为膜片弹簧的最大变形量和应力值随加载的仿真结果,在加载力不断变大的过程中,位移量和应力值也随之增大,当最大加载力为7000 N时,膜片弹簧最大应力为869.428 MPa,远低于材料的强度要求。
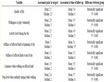
Table 3. Deflection and maximum stress values of diaphragm springs under different loading forces
表3.不同加载力下膜片弹簧的变形量和最大应力值
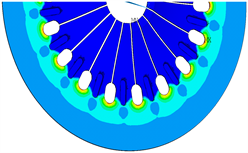
Figure 4. Local enlargement of diaphragm spring deformation
图4.膜片弹簧变形局部放大图
从图4的仿真结果可以看到,最大应力值所在的地方一般是分离指与支撑圈接触的部位,这里受到压盘的压紧力,压力值的大小影响膜片弹簧的工作安全性,所以要重点研究。
3.1. 膜片弹簧静应力仿真分析
当膜片弹簧处于接合状态时,一般认为压盘与膜片弹簧接触处的作用力低于6000 N;图5为不同加载力下最大应力仿真分析图。结果表明,在施加7000 N的力时,其最大应力为869.428 MPa,没有超过材料的屈服强度1372 MPa,本设计的结构安全性能比较好。
3.2. 膜片弹簧的模态分析
将膜片弹簧三维模型导入ANSYS进行模态分析,仿真结果如表4所示。
一般膜片弹簧离合器所配合使用的曲轴达到最大转速时的频率为110 HZ,通过表4的分析可知,前6阶弹簧处于刚性状态,频率始终为0,在第7至10阶膜片弹簧在弹性模态的频率值都比110 HZ大,所以不会产生共振,说明本设计的膜片弹簧满足模态分析的要求。如图6所示,分别为膜片弹簧第7、8、9、10阶模态图,模态分析不仅可以保证离合装置的安全性和稳定性,还对膜片弹簧的优化设计有指导意义。
3.3. 冲制加强筋后膜片弹簧静应力分析
将SolidWorks软件建立的冲制加强筋后的膜片弹簧结构优化模型导入ANSYS中,定义材料参数和划分网格后,定义2000 N~7000 N的加载力,最大应力值仿真结果如图7所示。
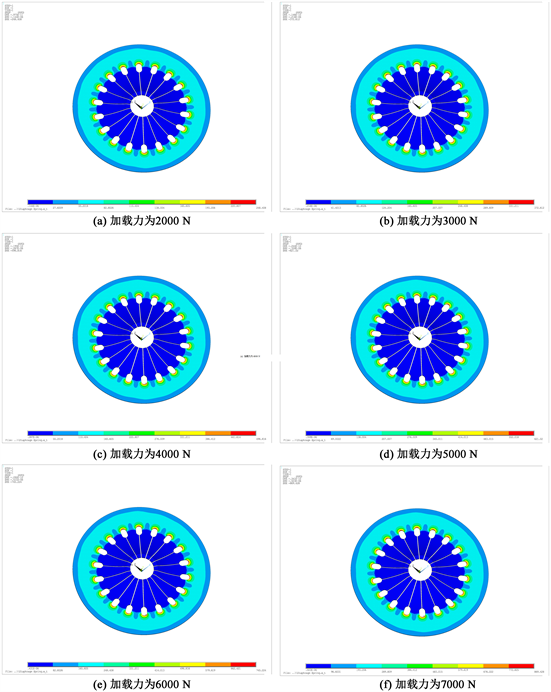
Figure 5. Maximum stress analysis with different loading force
图5. 不同加载力最大应力分析图
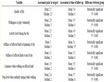
Table 4. 1st~10th order frequency values of diaphragm spring
表4. 膜片弹簧1~10阶频率值
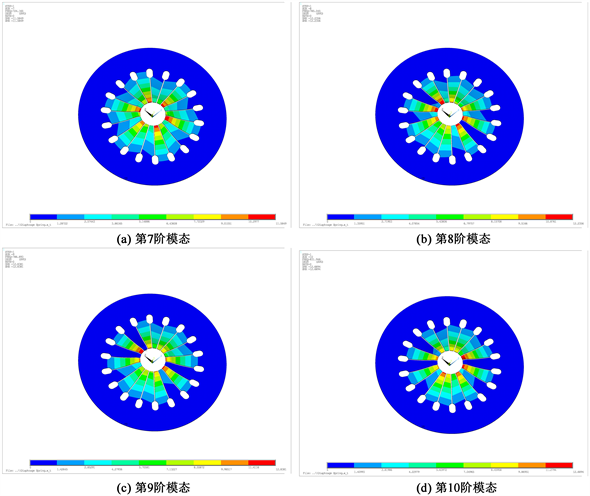
Figure 6. Modal diagram of diaphragm spring
图6. 膜片弹簧模态图
通过图7可以看出,对冲制加强筋后的膜片弹簧加载力为2000~7000 N时,最大应力值为842.887 MPa,没有超过屈服极限,结构优化后也满足材料强度要求。膜片弹簧在冲制加强筋后,提高了驾驶过程中膜片弹簧分离指的刚度,有效改善了其分离性能。
3.4. 结构优化前后最大应力值的对比
将加强筋冲制前后膜片弹簧的最大应力仿真结果绘制对比图,如图8所示,通过两组仿真数据的对比,膜片弹簧新结构的最大应力变小,结构更加稳定。
通过图8的结果对比,可以发现随着加载力的不断增大,冲制后的结构对于最大应力值的影响越来越明显。在加载力为2000 N时,最大应力值由248.408 MPa降低至210.772 MPa,降幅为25.666 MPa;在加载力为7000 N时,最大应力值由869.428 MPa降低至842.887 MPa,说明冲制加强筋对膜片弹簧结构强度有显著改善。
4. 结论
本文以膜片弹簧为研究对象,根据车辆参数建立了离合器膜片弹簧三维模型,分析了膜片弹簧在工作过程中不同加载力时的最大变形量和应力值,进行了模态分析;根据分离指变形和最大应力位置,在膜片弹簧分离指根部冲制加强筋,结果如下:
(1) 将膜片弹簧模型导入ANSYS软件,分析在加载力分别为2000~7000 N时膜片弹簧最大应力值仿真结果,随着加载力的增大,膜片弹簧最大应力值变大,但远低于材料的屈服强度;
(2) 模态分析结果表明,膜片弹簧在1到6阶为刚性模态,7到12阶的固有频率都大于发动机的参
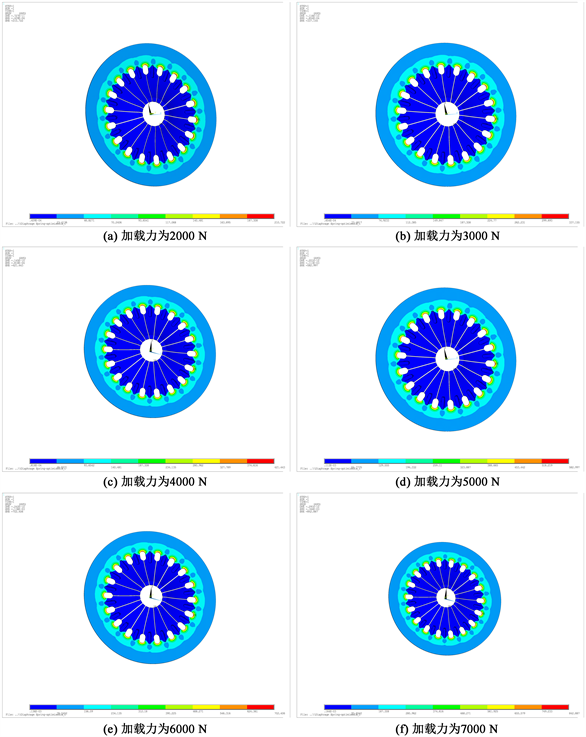
Figure 7. Maximum stress results for different loading forces
图7. 不同加载力的最大应力结果图
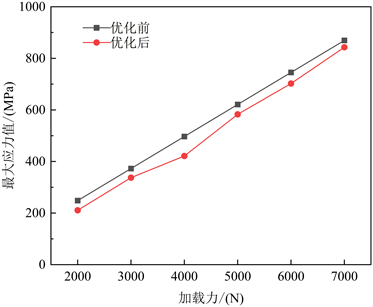
Figure 8. Comparison of maximum stress values before and after reinforcement punching
图8.两种膜片弹簧最大应力值对比图
考值,因此不会发生共振;
(3) 对比加强筋冲制前后膜片弹簧的最大应力值仿真结果,加强筋对最大应力值的减小效果显著,验证了结构优化后对膜片弹簧强度的改善作用。