1. 前言
压延铜箔由于耐弯折性能好,被广泛应用于挠性印刷电路板,但是其表面粗糙度低,导致铜箔与PI膜结合能力差 [1],为提高压延铜箔与薄膜基体的结合力,需要对光箔进行表面粗化处理。粗化是采用电镀方法在铜箔表面生成铜或铜合金镀层,提高压延铜箔真实表面积的一种表面处理工艺,其效果的好坏会影响到后续的防扩散阻挡层处理和防氧化层处理 [2] [3];粗化处理目的是细化铜瘤大小,得到分布均匀、结合牢固的球状铜颗粒。
本文通过概括分析电解液、添加剂、电沉积参数、搅拌强度和脉冲电流等对粗化层结晶形态、表面粗糙度、抗剥离强度和掉粉等特性的影响,分析压延铜箔表面粗化技术的发展,探究铜箔表面粗化的精准高效控制途径。
2. 压延铜箔表面粗化的工艺过程
粗化是将待粗化的铜箔与电源负极相连,不溶性的导体(不锈钢或钛基体表面涂覆贵金属)与电源正极相连,以酸性CuSO4溶液为粗化液,接通电源后控制适当的工艺条件,使铜在阴极铜箔上沉积。压延铜箔表面粗化的工艺流程见图1。
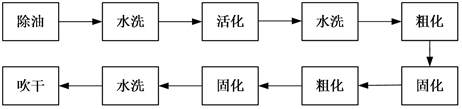
Figure 1. Process flow of surface roughening treatment of rolled copper foil
图1. 压延铜箔表面粗化处理的工艺流程
2.1. 除油
压延铜箔是经抛光的轧辊轧制而成,轧制过程中需要轧制油对轧辊冷却润滑,轧制油在铜箔表面形成一层有机膜,有机膜影响后续表面处理时金属粒子在铜箔表面沉积的均匀性 [4],因此,在粗化之前需要除去表面残油。
常用的除油方法有:有机溶剂除油、电解除油、超声波除油和化学除油等。工业生产一般使用电解除油,将铜箔浸入碱性电解液中,电解时阴极会析出大量气体,这些气泡将油膜撕裂,使油膜脱离铜箔,同时气泡对溶液起搅拌作用,加速了铜箔表面油污的脱除速度。
2.2. 酸洗
酸洗使压延铜箔表面活化 [5],同时除去其表面的氧化物和除油残留物 [6]。酸洗液一般采用质量分数为15%的H2SO4溶液。
2.3. 粗化工序
粗化处理包含两个工序:粗化工序和固化工序,采用酸性硫酸铜体系,至少经过两次粗化“烧焦镀”和两次固化“包裹镀”处理。
粗化工序采用低铜高酸的低温溶液,在高电流密度条件下,铜箔表面沉积一层瘤状铜颗粒,为后续固化过程沉积铜颗粒提供生长点 [7]。
2.4. 固化工序
固化工序采用高铜低酸、温度较高的溶液,固化电流密度较低,在粗化工序生成的瘤状颗粒间沉积一层致密、细小的铜颗粒,增大铜箔的比表面积,降低表面粗糙度,提高铜箔剥离强度 [8] [9]。
3. 粗化层特性的影响因素
3.1. 电解液
3.1.1. Cu2+浓度
CuSO4作为粗化液的主盐,是溶液中Cu2+的来源。Cu2+浓度影响粗化层的生长方向;Cu2+浓度增大,阴极极化作用降低,使晶核形成速度变慢、晶粒长大速度变快,导致铜晶粒粗大 [10]、形状不规则。
胡旭日等 [11] 观察不同Cu2+浓度下粗化层的SEM图(见图2)发现,Cu2+浓度在15 g/L~30 g/L时,粗化层基本是横向生长,Cu2+浓度为40 g/L时,粗化层在纵向上有较大生长,导致“铜芽”较高,容易掉粉。余德超等 [12] 研究了Cu2+浓度对剥离强度的影响,发现粗化液中Cu2+浓度在20 g/L左右时剥离强度最高。
(1)
(2)
(3)
(4)
Figure 2. Scanning electron microscope images of roughened layer under different Cu2+ concentration [11] (´2000). (1) 15 g/L Cu2 +, (2) 20 g/L Cu2 +, (3) 30 g/L Cu2 +, (4) 40 g/L Cu2 +
图2. 不同Cu2+浓度下粗化层的SEM图 [11] (´2000)。(1) 15 g/L Cu2+,(2) 20 g/L Cu2+,(3) 30 g/L Cu2+,(4) 40 g/L Cu2+
3.1.2. H2SO4含量
H2SO4在粗化处理中的作用:1) 防止铜离子水解 [1];2) 增强溶液的导电性;3) H2SO4含量影响酸铜比,粗化层的均匀程度取决于酸铜比 [12]。
胡旭日等 [13] 测试分析了H2SO4含量对剥离强度和表面铜粉的影响,H2SO4含量由80 g/L增加到120 g/L,剥离强度增大,H2SO4含量由120 g/L增加到160 g/L,剥离强度基本保持不变;H2SO4含量由80 g/L增加到120 g/L,铜箔表面掉粉减少;因此粗化液中H2SO4含量应控制在120 g/L左右。若粗化液中硫酸含量过高,阴极析氢严重,导致结晶颗粒呈树枝状 [13]。
3.2. 添加剂
粗化液中的添加剂有金属离子添加剂和有机添加剂,添加金属离子通过金属离子和铜离子共沉积,能改变铜颗粒结晶形态,增加剥离强度、减少掉粉。目前,国内外学者研究的粗化液添加剂有Ni2+、Mo6+、Na+、W6+、Sn2+和聚乙二醇400。
3.2.1. Ni2+
Chang-Yong Lee等 [14] 采用CuSO4和NiSO4溶液对18 μm压延铜箔表面进行瘤化电镀处理,对低电流密度下生成的沉积层进行EDS、XPS分析,得知沉积颗粒含有Cu2O;当增大电流密度时,镍粒子沉积到铜箔表面,铜箔的剥离强度提高,是由于沉积层中含镍时铜箔与粘合剂之间的粘结力大。
胡旭日等 [13] 以80~160 g/L H2SO4、5~20 g/L Cu2+、0.5~20 mg/L明胶混合溶液为粗化液,加入不同量的NiSO4,研究了Ni2+对掉粉的影响,发现Ni2+的加入可以减少表面铜粉,原因是Ni2+和Cu2+共沉积抑制了发达树枝状晶的生成,当Ni2+含量为0.5 g/L和1.0 g/L时,基板表面基本无铜粉。
3.2.2. Mo6+
冯绍彬等 [15] 以微分电容值表征铜箔粗化后的表面粗糙度,分析(NH4)2MoO4对铜箔表面粗糙度的影响,结果表明,添加(NH4)2MoO4可以提高粗化层的微分电容,增大铜箔表面粗糙度;添加(NH4)2MoO4还可以提高结合强度,但其作用机理不明确。
3.2.3. Na+、W6+、Sn2+
唐云志等 [16] 向粗化液中加入Na2WO4和SnSO4复合添加剂,同时加入适量锡粒来防止Sn2+被氧化,发现当加入0.07~0.15 g/L Na2WO4和0.7~1.5 g/L SnSO4时,粗化效果明显。图3为粗化液中加入TiSO4所得粗化层的扫描电镜图 [18],图4为粗化液中加入不同量Na2WO4所得粗化层的扫描电镜图 [17],表1为不同浓度的TiSO4和Na2WO4下测得的铜箔表面粗糙度 [17],添加TiSO4使铜晶粒以树枝状生长,加入Na2WO4可以得到球状铜颗粒,且随着Na2WO4含量增加铜颗粒尺寸减小,这是因为Na+能降低铜形核的过电位,提高成核数 [18];添加TiSO4和Na2WO4均可提高铜箔表面粗糙度。
3.2.4. 有机添加剂
吴婷等 [19] 采用10 g/L CuSO4、10 g/L NiSO4和10 ppm聚乙二醇400的混合溶液对10 μm压延铜箔进行一次粗化处理,粗化液温度25℃,粗化液PH用酒石酸调节为2,得到的粗化层颗粒尺寸约0.1 μm,粗糙度Rz ≤ 0.8 μm,抗剥离强度P.S. ≥ 0.8 N/mm,在保证抗剥离强度的同时实现了低粗糙度。
(1)
(2)
Figure 3. Scanning electron microscope images of roughened layer under different TiSO4 concentration [17] (´8000). (1) 0.0 g/L TiSO4, (2) 0.3 g/L TiSO4
图3. 不同TiSO4浓度下粗化层的扫描电镜图 [17] (´8000)。(1) 0.0 g/L TiSO4,(2) 0.3 g/L TiSO4
(1)
(2)
(3)
Figure 4. Scanning electron microscope images of roughened layer under different Na2WO4 concentration [17] (´8000). (1) 0.03 g/L Na2WO4, (2) 0.06 g/L Na2WO4, (3) 0.09 g/L Na2WO4
图4. 不同Na2WO4浓度下粗化层的扫描电镜图 [17] (´8000)。(1) 0.03 g/L Na2WO4,(2) 0.06 g/L Na2WO4,(3) 0.09 g/L Na2WO4
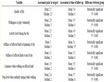
Table 1. Surface roughness of copper foil [17]
表1. 铜箔表面粗糙度Ra [17]
3.3. 电沉积参数
3.3.1. 电流密度
增大电流密度可以增强阴极极化作用,细化铜晶粒 [20];电流密度过大会形成树枝状晶,树枝状晶过于发达将导致铜颗粒脱落产生铜粉 [21];升高电流密度会使镀层织构发生变化。
徐树民等 [22] 在高电流密度下沉积的铜颗粒细小,低电流密度下沉积的铜颗粒粗大。吴婷等 [23] 研究了电流密度对铜箔剥离强度和表面粗糙度的影响,电流密度由25 A/dm2升高到55 A/dm2,铜箔剥离强度提高,Rz增大。胡旭日等 [13] 研究了电流密度对掉粉的影响,发现电流密度超过35 A/dm2时,铜箔表面掉粉严重。硫酸盐体系中铜镀层的择优取向是低电流密度下的(110)晶面和高电流密度下的(111)晶面 [24],且高电流密度下铜颗粒呈六棱锥形,这可能是电流密度升高时铜粉脱落的原因 [8]。
3.3.2. 温度
温度对粗化层特性的影响主要体现在控制阴极极化和离子迁移上 [8]。溶液温度升高会加快阴极反应速度和离子扩散速度,降低阴极极化作用,使铜晶粒变大;溶液温度较低时,Cu2+扩散慢,使镀层均匀性差,且影响生产效率。
图5为不同溶液温度下所得粗化层的扫描电镜图 [25],21℃时镀层覆盖不完全,存在大沟壑,铜晶粒小;25℃时,镀层表面沟壑变小,铜晶粒增大;30℃时铜晶粒大且大小较为均匀,沟壑减少。不同温度下铜箔的剥离强度和掉粉情况见表2 [11],温度升高剥离强度先升高后降低,温度过高时,铜箔表面会有铜粉脱落。
(1)
(2)
(3)
Figure 5. Scanning electron microscope images of the roughened layer at different solution temperatures [25]. (1) 21˚C, (2) 25˚C, (3) 30˚C
图5. 不同溶液温度下所得粗化层的扫描电镜图 [25]。(1) 21℃,(2) 25℃,(3) 30℃
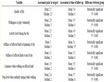
Table 2. Effect of temperature on peel strength and “dropping powder” [11]
表2. 温度对剥离强度和“掉粉”情况的影响 [11]
3.3.3. 时间
粗化时间过短,镀层不能将基体完全覆盖;粗化时间过长,铜晶粒过大,镀层过厚,会影响铜箔的电性能 [12] [14]。
4. 其它条件
1) 搅拌强度:电解液的搅拌强度会影响镀层质量,在粗化过程中引入超声波,利用超声空化作用加强搅拌,消除溶液的局部浓度不均匀,可以提高铜的沉积速率、细化晶粒 [26]。
徐火平等 [27] 在不锈钢表面电镀铜过程中引入超声波后,铜晶粒细化。邓庚凤等 [28] 采用磁力搅拌和超声波搅拌制备超薄电解铜箔,发现采用超声波搅拌得到的铜箔表面颗粒更均匀、细小。Martins等 [29] 采用磁力搅拌和超声波搅拌对铁基体表面铜沉积层的特性进行研究,结果表明,采用超声波搅拌得到的铜沉积层与铁基体之间的粘结力高;图6为采用磁力搅拌和超声波搅拌所得铜沉积层的扫描电镜图 [29],在磁力搅拌下铜镀层颗粒呈球状,在超声波搅拌下铜镀层颗粒形状不规则。
2) 脉冲电流:采用脉冲电流镀铜可以达到较好的深镀能力 [30],得到均匀致密的镀层 [31]。Pena等 [32] 在不锈钢表面镀铜,研究了直流电和脉冲电流对铜镀层性能的影响,发现脉冲电流有利于新晶核生成,可以减小晶粒尺寸。乔瑞华等 [33] 采用100 Hz、1000 Hz的脉冲频率在铁表面电沉积铜,发现在100 Hz的脉冲频率下得到的铜沉积层颗粒尺寸小。采用直流电在钼基体上沉积的铜颗粒呈树枝状,在脉冲电流下钼基体上沉积的铜颗粒呈球状 [34]。
5. 总结与发展趋势
综上所述,Cu2+浓度过高,导致粗化层晶粒形状不规则、剥离强度低、掉粉严重,Cu2+浓度过低,镀层覆盖不完整;H2SO4含量过高,粗化层晶粒呈树枝状,H2SO4含量过低,剥离强度低、掉粉严重;金属离子添加剂可以改变粗化层颗粒形态,提高剥离强度,减少掉粉;电流密度过低,铜颗粒粗大、剥离强度低,电流密度过高,加剧铜箔表面掉粉;温度过低,镀层不均匀,温度过高,掉粉严重;搅拌强度影响沉积层颗粒形状;脉冲电流可以细化晶粒,使沉积层颗粒呈球状。改善提高压延铜箔的表面粗化特性,以下三个方面是技术研发的发展趋势:
(1)
(2)
Figure 6. Scanning electron microscope images of copper coating obtained under different stirring methods [29]. (1) Magnetic stirring, (2) Ultrasonic stirring
图6. 不同搅拌方式下所得铜镀层的的扫描电镜图 [29]。(1) 磁力搅拌,(2) 超声波搅拌
1) 压延铜箔粗化工艺向减少粗化处理次数甚至只进行一次粗化处理方向发展。2) 在粗化液中加入合金离子,实现铜离子和合金离子共沉积,以提高压延铜箔的耐蚀性、耐热性和抗氧化性,延长终端产品的使用寿命。3) 为实现信号传输的高频化和高速化,电子产品要求压延铜箔在保持高剥离强度的同时,具备更低轮廓。因此,制备超低轮廓压延铜箔即减小粗化处理后铜箔表面粗糙度成为粗化处理的发展方向。
基金名称
国家重点研发计划项目(2016YFB0301300);山东省重大科技创新工程项目(2019TSLH0101)。
NOTES
*通讯作者。