1. 引言
保护火灾中人身和财产安全是人们关心的大事,无论在建筑、电力、车辆、航天、船舶、地铁、军工等领域,对设施的安全性以及可靠性的要求逐渐提高,因此消防重点部门必须要求使用具有优异的阻燃耐火性能的制品,其中有机硅橡胶材料较为适合,但是普通橡胶在火中一般都会被完全烧毁,所以需要采取新技术对其性能进行增强从而达到阻燃自熄的目的,以往的技术是添加含卤素阻燃剂,例如十溴二苯醚[1] 等,虽然效果很好,但是燃烧时放出大量有毒和腐蚀性气体并伴随有大量的烟雾已被国内外环保法规禁用。而目前的技术主要采用无卤低烟阻燃橡胶[2] ,主要有硅橡胶乙丙橡胶和乙烯乙酸乙烯酯橡胶等,这些橡胶在火中燃烧具有难燃性和自熄性,能在火灾中起一定作用,可是持续高温燃烧后烧余物没有机械强度变成灰烬,不能保持制品的完整性,会造成更危险的二次灾害例如电缆的护套和绝缘烧毁后造成短路。
已研究过的可陶瓷化的聚合物有许多种,包括热塑性塑料、热固性塑料和弹性体,其中最成功的是陶瓷化硅橡胶。近几年,我国研究者在推介陶瓷化硅橡胶[3] -[5] 的同时,进行了一些探索[6] 已在一些领域开始应用陶瓷化硅橡胶。已经商品化的陶瓷化硅橡胶主要有深圳市沃尔核材股份有限公司[7] -[9] 其以树脂共聚物为基材,通过在硅橡胶中添加二氧化硅、硅油、偶联剂所得混合物即为陶瓷化硅橡胶,混合后经过高温捏合、混炼、硫化等加工后制备出陶瓷化硅橡胶热缩套管。芜湖航天特种电缆厂[10] 发明了一种应用与电缆的陶瓷化硅橡胶,以硅橡胶和天然橡胶的混合物为基体,改性硅藻土为填料制得阻燃、低烟、环保、耐候性好、成本低的电缆料。
目前主要使用的方法有多种,如碳纤维增强,硅酸盐填料以及其他阻燃剂,互溶剂,结构助剂等[11] [12] ,其中云母粉是硅橡胶复合材料中最受欢迎的阻燃填料之一,尤其是在电线、电缆应用方面。研究发现通过以下几种方式提高了硅橡胶的热稳定性[13] -[15] :1) 云母表面对硅橡胶大分子链的吸附阻碍了链段的运动抑制了分子链的重排和链转移反应,导致了残炭量的增加;2) 云母片层和陶瓷化层的屏蔽效应降低了质量传输率(例如,由于聚合物熔体粘度的增加降低了可燃物向气相的扩散)。
本研究以甲基乙烯基苯基硅橡胶为基体,以云母粉为成瓷填料,气相二氧化硅为补强填料,制备硅橡胶/云母/氧化硅系复合材料,硫化后的硅橡胶在低温下各项性能保持良好,当逐步升温时,材料内部发生陶瓷化转变,形成坚硬的陶瓷体,从而降低了质量的进一步损失并阻止了热量的扩散。
2. 实验
2.1. 实验原料
硅橡胶混炼胶(PVMQ,上海中骏化工有限公司);云母粉(mica,国药集团化学试剂有限公司);气相二氧化硅(SiO2,国药集团化学试剂有限公司);2,5-二甲基-2,5-双(叔丁基过氧基)己烷(DBPH,上海中骏化工有限公司)。
2.2. 材料制备
本实验以甲基乙烯基苯基硅橡胶(PVMQ,型号为110-1,乙烯基含量为0.2%,分子量50~60万)为基体,绢云母粉末和气相二氧化硅为补强填料制备硅橡胶/云母/氧化硅系可瓷化复合材料。取试样总重50 g,根据配方(表1,以硅橡胶的质量份数为100计)准确称取各组分原料。采用直接共混法将云母填料和低熔点玻璃结构控制剂在研钵中研磨混合均匀,然后添加到甲基乙烯基苯基硅橡胶基体中进行混炼,最后加入硫化剂使混合均匀。而后在80 × 80 × 40 mm3的模具中成型,于165℃保温10 min进行一段硫化,形成云母/硅橡胶弹性体,随后在200℃进行二段硫化4 h。
再取四块大小相同硅橡胶复合材料3试样,在马弗炉中分别在400℃、600℃、800℃、1000℃煅烧5 min。冷却到室温,根据测试要求制样。
2.3. 表征与测试
2.3.1. DSC-TG测试
通过差示扫描量热一热重联用分析技术,采用德国耐驰NETZSCH STA449C/3/G型综合热分析仪,在空气氛围下,将试样以10℃/min的升温速率从室温升温至1000℃,分析硅橡胶/云母/氧化硅系在升温过程中质量发生的变化。
2.3.2. XRD测试
研究采用Bruker公司生产的D8 ADVANCE型x射线衍射仪对烧蚀的样品进行物相分析。测试条件为:扫描范围为10˚~80˚,角度步长0.002,扫描速率1˚/min,X射线为Cu-Ka线,电压40 kV,电流400 mA。
2.3.3. IR测试
采用Thermo Nicolet公司的Nexus傅立叶变换红外光谱分析仪,仪器的测试波数范围,中红外光区为4000~400 cm−1,快速扫描为1次/秒,最高分辨率为0.019 cm−1,红外变温为(室温−400℃)。样品的结构及骨架采用KBr支撑片,改性粉体与KBr质量比为1:300,在400~4000 cm−1记录样品的振动红外吸收峰。
3. 结果与讨论
3.1. 硅橡胶复合材料热性能分析
普通苯基硅橡胶最高只能在约250℃正常使用,超过一定温度范围其内部结构会发生变化,主链Si-O-Si键断裂产生SiO2并伴随有小分子热解产物(主要有CO、H2O等)的产生,使其体积收缩,失重明显而无法正常使用。本实验通过添加云母粉和气相二氧化硅制备硅橡胶/云母/氧化硅复合材料,随着温度的升高,能够在高温时发生有机–无机陶瓷化转变,形成高温陶瓷保护层阻碍热量的进入与质量的进一步损失。本实验主要以起始分解温度(失重为5 wt%所对应的温度,T5)、分解峰值温度(最大分解速率所对应的温度,Tmax)、高温残留率来表征硅橡胶/云母/氧化硅系复合材料的热性能。图1、图2分别为不同添加量的云母粉改性硅橡胶的TG图和DSC图。从中分析出热性能参数如表2所示。
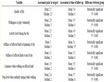
Table 1. Formula of silicone/mica/silicone rubber
表1. 硅橡胶/云母/氧化硅系复合材料配方
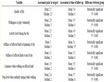
Table 2. Thermal parameters of pure PVMQ and PVMQ/mica/silicone rubber
表2. 不同云母添加量的硅橡胶/云母/氧化硅系复合材料的热重参数

Figure 1. TG analysis of pure PVMQ and PVMQ/mica/ silicone rubber with different amounts of mica
图1. 不同云母添加量的硅橡胶/云母/氧化硅系复合材料TG图

Figure 2. DSC analysis of pure PVMQ and PVMQ/mica/silicone rubber with different amounts of mica
图2. 不同云母添加量的硅橡胶/云母/氧化硅系复合材料DSC图
随着云母粉添加量从0份增加到40份,硅橡胶复合材料的初始分解温度均在400℃左右,无明显变化。而分解峰值温度均低于纯硅橡胶,但随着云母粉含量的增加,呈逐渐上升趋势。而1000℃时的残留量比纯硅橡胶有明显增加,且在云母添加量为40份时达到最大值66.21wt%。从中可以看出,随着云母在苯基硅橡胶复合材料中含量的增加,当云母粉添加到一定量后,云母对其热稳定性略有下降,影响不大。这可能是由于云母具有片层结构能阻隔材料在燃烧下气体和热量的传输,并通过对硅橡胶大分子链的吸附交联等作用,限制链段运动,从而提高硅橡胶的热稳定性。但当添加过多的云母粉时,硅橡胶复合材料的残留量会降低,这可能是由于云母粉中含有钾、钠及其它杂质金属离子(钙、镁等)。当复合材料中含有过多的碱金属离子时,在高温下会加剧催化硅橡胶的热分解。
3.2. 硅橡胶复合材料陶瓷化机理分析
将在0℃、400℃、600℃、800℃以及1000℃所制备的材料分别进行红外测试,从而分析随着温度变化基体硅橡胶的结构变化,结果如图所示,1080~1020 cm−1处的“W”型的峰是Si-O-Si的特征吸收峰,在温度升高时,主链Si-O-Si键发生断裂,很有可能生成了SiO2;位于2964 cm−1处的信号峰是Si-CH3上甲基的伸展振动吸收峰,1256 cm−1和777 cm−1处的信号峰是Si-CH3上甲基的弯曲振动吸收峰,可以发现随着温度的升高Si-CH3的信号峰逐渐减弱,在1000℃时几乎消失,表明此时Si-C键断裂;位于1620 cm−1处的是CH=CH2上C=C伸展振动吸收峰,2980 cm−1处为苯基上C-H键的伸展振动峰,位于1414 cm−1和702 cm−1两处的信号峰说明Si-C6H5结构的存在。如图3所示。
与此同时,对不同温度煅烧下的复合材料进行XRD分析,测试结果如图所示,将40份添加量的云母粉加入硅橡胶中后,从图中可以发现,随着温度的升高,材料的衍射峰开始出现且越来越尖锐,在400℃时出现无定型二氧化硅衍射峰,当温度达到600℃并逐渐升高的过程中,出现了α-SiO2衍射峰,并随温度升高而更加明显。如图4所示。
综合分析发现,在400℃时,材料内部结构无较大变化,质量以及体积保持率都比较完整,而在400~600℃区间内,462℃时材料失重率最大,这可能是由于侧链乙烯基的断裂以及少量无定型二氧化硅的生成所致;当温度升高到600℃时,主链Si-O-Si键的峰值有所减弱,并且在XRD图中可以观察到少量的α-SiO2衍射峰,这可能由在400℃时出现的少量无定型二氧化硅转化而来,并且主链的断裂导致整体失重,因此材料表观可见部分脱落并伴随有一定的体积收缩;最后在1000℃时,红外图谱中几乎观察不到苯基的存在,并且Si-O-Si键也十分微弱,与此同时可以看见十分尖锐的α-SiO2的衍射峰,材料较600℃时力学性能有一定增强,可以猜测在800~1000℃范围内,侧链上的Si-C6H5键断裂,大部分的无定型二氧化硅也转换成了α-SiO2。
高温烧蚀下有机硅基体发生降解,降解产物(主要是SiO2)与添加的云母粉会发生共熔共晶反应,从而形成新的固相和/或液相。随着烧蚀温度的升高和时间的延长,液相组分逐渐扩散渗到粉末颗粒间起到桥连作用。冷却固化后,材料被烧结成坚硬的陶瓷体。
4. 结论
1) 随着云母添加量的增加,所得复合材料在1000℃时的残留量首先明显增加,当添加量为40份时达到最大约为66.21%,当添加量继续增加时残留量有略微下降。针对于云母添加量为40份的产品,在约460℃时有一次明显失重,随后无较大变化。
2) 云母添加量为40份的复合材料,462℃时材料失重率最大,600℃时Si-O-Si键的峰值有所减弱,出现少量的α-SiO2衍射峰,1000℃时出现尖锐的α-SiO2的衍射峰,侧链上的Si-C6H5键断裂,大部分的无定型二氧化硅也转换成了α-SiO2。

Figure 3. FTIR analysis of PVMQ/mica40/silicone rubber at different temperature
图3. 硅橡胶/云母/氧化硅系复合材料在不同温度下烧蚀后的红外图谱

Figure 4. XRD analysis of PVMQ/mica40/silicone rubber at different temperature
图4. 硅橡胶/云母/氧化硅系复合材料在不同温度下烧蚀后的X射线衍射图
3) 在600℃以后,硅橡胶主链开始断裂,高温下降解产物SiO2与填料发生共融共晶反应,保持材料的黏结性使不易脱落。
本文通过TG-DSC、FTIR以及XRD等技术,对硅橡胶/云母/氧化硅系的陶瓷化机理进行简单分析与阐述,在不同温度下的链节断裂和无机填料的结构与晶形变化,猜测其可能发生的陶瓷化转变过程。当云母添加量为40份时,1000℃时的残留量为66.21%,从600℃发生陶瓷化转变,Si-O-Si键断裂并出现少量α-SiO2,随着温度升高,产生越来越多的SiO2,在云母粉边缘处形成起桥接作用的共熔混合物,冷却后形成α-SiO2陶瓷化产物,结果发现发生陶瓷化的硅橡胶具有优异的隔热阻燃效果,有望应用于电线电缆,航空航天,医疗设备等多种耐高温条件中,同时可以通过添加其它填料如玻璃料、阻燃剂,结构控制剂以及其他制备助剂等,尽可能降低成本的同时改善其陶瓷化过程,从而提高其烧蚀条件下的机械性能,耐热性能等,更好的将其投入实际应用之中。

NOTES
*通讯作者。